A different prefabrication and modular construction sector came out of the pandemic. Ambitious startups such as Skender Manufacturing and Katerra folded in the last few years, while one major health care designer lamented an industrywide pullback that saw many of the suppliers they work with cut back on custom, by-project fabrication to standardize on products like headwalls and bathroom pods.
Prefabrication consultant Amy Marks, formerly Autodesk’s industry transformation executive and advisor to the Singapore Building & Construction Authority for its prefab initiative, says prefab is in a better place today, even if ambitious startups aren’t leading the way anymore.
“If you asked me if today, are there 600 MEP subcontractors that are doing more fabrication now than last year? The answer would probably be yes,“ she said. “It’s going to be dependent upon the volume of work they’re putting out in totality.”
Marks, also widely known as the “queen of prefab,” cautions that the success of manufacturers that produce prefab modular interiors shouldn’t be seen as a reflection of the health of prefab construction overall.
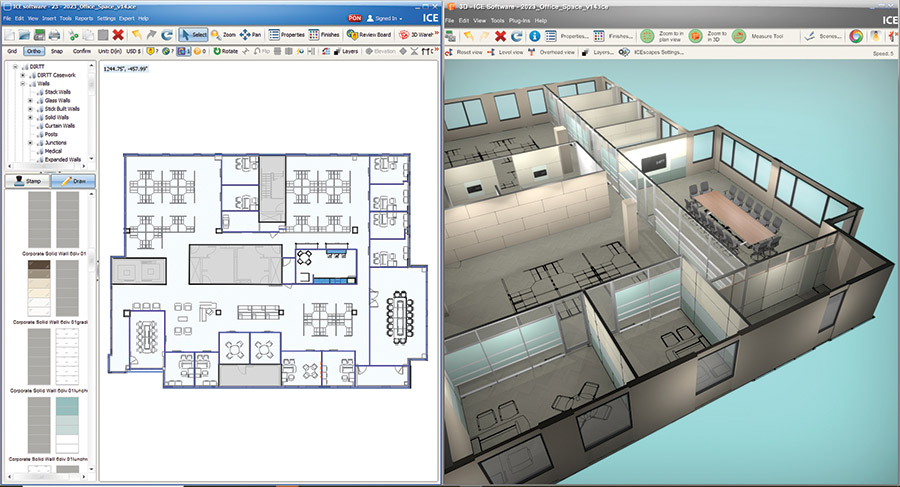
DIRTT’s software converts 2D CAD to 3D BIM, and can also do VR for clients to try out their spaces before they’re built.
Image courtesy DIRTT
Prefabricated interiors manufacturer DIRTT Environmental Solutions replaced its board of directors in May 2022 and has since released new versions of its design-to-fabrication software and VR/AR experiences for owners to virtually walk through their spaces. Former Gensler Managing Principal Ken Sanders is the chair of the new board, and with new CEO Benjamin Urban, they’ve pushed the company toward flexible and adaptable systems such as unitized meeting rooms for offices and patient rooms for health care settings. Assignment and co-ownership agreements with wall and ceiling product manufacturer Armstrong World Industries Inc. helped drive DIRTT’s revenue growth in 2023.
“We all excel at one piece of [construction prefabrication], right?” Urban says. “We have no interest in doing building frames or envelopes such as structural steel prefab. That’s not who we are. We do [interiors] really well. And the reality is we’re already in this prefabrication space, doing some part of a whole project.”
Urban says there is also an element “handicapping us from being able to do what a Katerra was trying to do, or do what we could all do if we went in together speaking the same language.”
Construction technologists are still trying to unlock the efficiencies of manufacturing and prefabrication while dealing with supply chains and the unique difficulties that go into creating a kit of parts that can form unitized assemblies and serve as functional building systems. No small feat in an industry where so many tasks are left to different trades to complete.
“The second piece of procurement is around materials and equipment,” said Sidharth Haksar, head of construction strategy and industry partnerships at Autodesk. “In the U.S. alone, over $300 billion is spent on materials. That whole process is done on the phone, faxes, emails. How can you digitize that aspect?”
DIRTT’s Urban thinks there’s potential for greater collaboration within prefab. “There’s no distrust amongst us prefab manufacturers,” he said. “We’ve just all been focused on trying to drive our own narrative rather than solving it together.”
Post a comment to this article
Report Abusive Comment