How often did John R. Hillman, founder and president of Chicago-based HC Bridge Co., LLC, think about giving up on getting the industry to accept his hybrid bridge beam of concrete and steel with fiber-reinforced polymer materials? “Only about once a week,” he laughs.
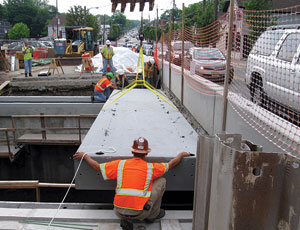
Hillman invented the beam design in 1996 after wondering what would happen if he combined concrete and steel with a composite material. Exposure to FRPs in graduate school at Virginia Tech and the experience of working with renowned bridge designer Jean Muller inspired him to marry the “age-old technology” of the arch structure with modern-day materials. “It became a mild obsession,” he says.
Riding the train to his daily job as an engineer at Teng & Associates, Chicago, Hillman did what engineers do—scribble down calculations. The result: a glass-fiber-reinforced shell, self-consolidating concrete for compression reinforcement, and high-strength continuous steel fibers for tension reinforcement. His first chance to prove the technology came in 2002, when Lehigh University engineering professor Dennis Mertz urged him to apply for a research grant from the Federal Railroad Administration and the state departments of transportation through the Transportation Research Board’s National Cooperative Highway Research Program.
“The hybrid composite beam is unquestionably unique,” says Neil Hawks, TRB staff representative. “Although the beam conforms to the principles of structural engineering, its ingenious combination of complex and commonplace materials yields a structural member that is lightweight and less bulky than its reinforced-concrete equivalent. With our current concerns about renewing our rail and highway bridges while minimizing disruption, these properties are in high demand.”
With the grant, Hillman successfully tested a 30-ft-long, 17-ft-wide span comprising eight beams in Pueblo, Colo., in 2008. It supported a full-size locomotive pulling 26 heavy-axle-load coal cars. “The hybrid composite beam will be the best solution for the many situations where stronger but shallower and lighter beams are needed,” notes Hawks.

Bridge engineer created a hybrid of conventional materials and composites that can create long-lasting, noncorrosive bridges that carry heavy loads.
The beam is catching on. The second application was the $2-million, 57-ft-long High Road Bridge in Lockport Township, Ill. This year, the New Jersey Dept. of Transportation used federal research funds to apply the beams on a $1.34-million replacement of state Rte. 23 Peckman’s Brook Bridge in Cedar Grove. Coming next is the Knickerbocker Bridge in Boothbay, Maine, an eight-span, 540-ft-long, $6-million replacement structure.
“It’s a labor of love to keep moving with this,” says Hillman of developing his patented technology. “Every time I did a major test, part of me hoped for a failure so I could move on. Then it would succeed, so I couldn’t stop.” Moreover, his colleagues at Teng gave him moral and engineering support. “Colleagues who I deem smarter than I—they told me it’s a great idea. So I couldn’t walk away from it,” he says.