The worldwide economic downturn places greater demands on the design and construction industries as banks and other lending institutions require enhanced price definition and cost control. Financing will distribute to projects that provide the greatest value for the lowest associated risk. Consequently, little tolerance for waste and inefficiency can be expected in the foreseeable future.
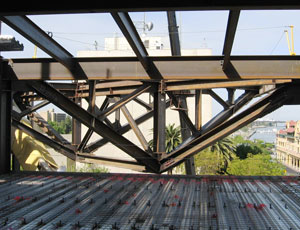
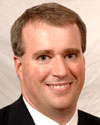
MCMANUS
While productivity in non-farm industries has more than doubled in the U.S. since 1964, labor productivity in the construction industry has actually declined — despite tremendous technological advances. For the structural steel industry, one major culprit is the inefficiency created by poor or incomplete connection design practice. In 1995, William Thornton, then Chief Engineer with Cives Steel Company, lectured at the AISC National Steel Construction Conference outlining many costly shortcomings with steel connection design. Areas of concern included poorly defined load criteria for the design of simple shear, moment, and bracing connections, as well as the use (or abuse) of stiffener and doubler plates in columns. It can easily be argued that nearly all of Thornton’s concerns remain present fourteen years later.
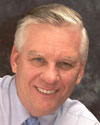
LEWIS
As an illustration, a peer review was recently performed on a group of three similar 180-foot tall stair towers for an industrial project. Connection design work was delegated to the fabricator using bracing forces in terms of a percentage of brace capacity, and gravity beam end reactions in terms of 60% of the total uniform load carrying capacity of the beams. Seismic design provisions and detailing did not apply.
It was determined that the worst-case brace sizes, and thus connection forces, were used throughout the structures, resulting in overdesigned lateral systems. The use of 60% of the total uniform load capacity for the gravity beams resulted in some reactions approximately 650% of those determined from the actual analysis. This placed great limitations on connection type, and any coping of the beams necessitated doubler plates to meet all necessary limit states.
Redesign allowed for significant cost savings and vast simplification of the connection details. Altering the brace types and configurations eliminated 22% of the braces and approximately 170 associated connections. Six hours of engineering time resulted in potential savings of nearly half a million dollars!
Uneconomical or incomplete connection design information is predominantly the result of the outdated design-bid-build business model, which nearly guarantees a lack of communication between the design and construction teams until design is substantially completed. Without fabrication and erection preferences from the construction team, engineers are forced to produce “one size fits all” designs or design criteria. Many structural engineers today typically expend the fewest number of engineering hours possible on each project, both to maximize profitability and out of necessity. Though other criteria may come into play, engineers are evaluated to some extent by fee. Unfortunately, many of the entities hiring engineers have little understanding of the insignificance of the engineering fee when compared to the cost savings associated with a complete and economical structural design. Consequently, the segregation between design and construction eliminates an effective check and balance between design decisions and true cost.
In addition to the negative impact reduced engineering effort has on project economics, the potential development of a dependence on the typical details produced is an inherent concern for engineering firms. As design manuals and codes continue to thicken with each edition, it becomes increasingly difficult, if not impossible, for an individual to be an expert on all structural engineering topics. An increased tendency towards less flexible, typical details, as well as an associated resistance to deviating from those details is understandable. However, the competency to perform, or even review, connection designs that fall outside of a firm’s typical standards is ultimately lessened. Thus, steel connection design appears to slowly be developing into a lost art in consulting engineering.
The steel industry should not tolerate decreased market share simply because of poor structural design. Early fabricator involvement in projects and increased engineering time and fee with feedback from the fabricator are feasible solutions to the problem. Design-build and design-assist construction delivery are just two effective methods of facilitating these solutions. Both have the potential to reduce project costs and add overall project value.
This is a call to arms for the structural engineering community — be the frontrunners in an effort to educate owners, developers, architects, and construction managers. Eliminate those who do not understand or appreciate the value an integrated, quality structural design brings to every project. Those who fail to work towards enhanced value could find themselves among those eliminated.
Post a comment to this article
Report Abusive Comment