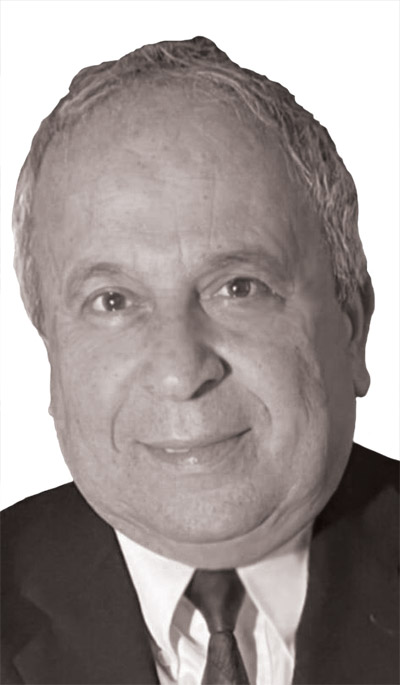
Mehdi Rastakhiz
During design and constructibility review, plans and specs are checked mostly for what is there. But during construction the impact of everything that is not there, or is present when it shouldn’t be, is magnified. I was trained to find what was absent and what was wrongly included early in my career. I remember when I first started plan checking, my mentor told me to take my designer hat off and to look for things that
are not there rather than just verifying the correctness of what the plans indicate. No matter how good you are, when you finally see what is missing, you become humbler—especially since the issues raised by what’s omitted or wrongly included can be very costly.
I once reviewed construction drawings on a 70-ft-deep sewer junction structure. As shown in the plans, the structure met all the city’s standards and sewer design guidelines. What was missing was how to provide access to the junction structure once an adjacent project was constructed.
The junction structure included steps for the operation crew to access the bottom of the pipe—an example of something that appears to be right but should not have been there. Deep sewers require confined space entry safety measures and personal protective equipment, and anyone entering must use a tripod and harness, not steps. Providing steps may suggest that someone should use them for access when they should not, and also increases the costs. Plus, the steps themselves may corrode over the years due to exposure to hydrogen sulfide gas.
There is more to consider. In designing some water and wastewater facilities, I found that design and constructibility teams need to consider having clear elbow room for the operating crew to work on or remove equipment. While the crew is involved in reviewing plans, operators are much more hands-on—and may not be able to detect these problems by looking at the plans. Even experienced engineers and reviewers can easily miss what is not there when looking at the plans.
There are other examples of information that may go missing in action. Once, our specifications provided information about fiber optic cables that we were installing around the city, so our consulting engineer prepared a design with the number of strands, color codes, type, storage and staging. He also had detailed instructions for the inspector and installer. But because what we specified could not be purchased off the shelf and there was no bid item for it, there was no indication about who would supply the cable and pay for it. A change order had to be written to correct that omission.
Realistically, many agencies are facing scheduling and budgetary issues. Although plans and specs go through several review stages in most agencies, and often an independent constructibility review, there’s never enough time or budget to do it right. Having perfect plans and specs becomes almost impossible, especially on complex projects. So the last step, constructibility review, which sometimes overlaps with value engineering, is the most critical.
Once issues arise during construction or operation, plenty of experts express their opinions about what went wrong. The best expert is the one who foresees them before they become issues in a constructibility review.
For more complex projects involving hydrogeology, structural issues, corrosion, instrumentation or other specialties, it is best to have an expert who knows his or her craft to take a quick look, at the minimum, to avoid fundamental mistakes. That ensures there are no discrepancies between different disciplines and specs and that the project can be built safely and efficiently.
Technological Change
The rapid pace of technological advancement also affects constructibility reviews. Better products may be available for a project that was specified seven to 10 years in the past. There’s also a generation gap between younger engineers and contractors and those more experienced and close to retirement. The older generation has experience that the younger one lacks.
On any project, doing the vital detective work and perceiving what’s not shown, and what should not be there at all, can prevent a lot of trouble and expense. That’s what I’ve learned over many years and many projects.
Mehdi Rastakhiz, deputy construction manager for the city of San Diego’s Pure Water CM team, has supervised the city plan checking section and acted as project manager and construction manager on many private and public sector projects. He can be reached at 858-776-0340.