(W)rapper
Los Angeles
BEST PROJECT, OFFICE/RETAIL/MIXED-USE
Submitted by: MATT Construction
Owner: Samitaur Constructs
Lead Design Firm: Eric Owen Moss Architects (EOMA)
General Contractor: MATT Construction
Civil Engineer: Arup
Structural Engineer: Arup
Mechanical Engineer: ACCO Engineered Systems
Electrical Engineer: AJ Kirkwood
Shoring Engineer: John Labib Structural Engineers LLP, dba Labib Funk
Subcontractors: Anning-Johnson Co.; Aztec Fire Protection; Barazani Outdoors Inc.; BLC Surveying Inc.; Bob Holloway Fire Life Safety Consultant LLC; Bomel Construction Co. Inc.; BrightView Landscape Development Inc.; Comet Electric Inc.; Commercial Scaffolding of California Inc.; Cowelco Steel Contractors; Delta Pipeline Inc.; Engel Holdings Inc. dba Cabrillo Hoist; Griffith Co.; HBA Inc.; Joe Picco & Assoc. Inc. dba EJ Enterprises; KONE Inc.; Largo Concrete Inc.; Leko Construction Inc.; Letner Roofing Co.; Malcolm Drilling Co. Inc.; McKeon Door West Inc.; MG Mako Inc.; Mike Zarp Inc.; Muir-Chase Plumbing Co. Inc.; Outdoor Dimensions LLC; Pacific Steel Group; Performance Contracting Inc.; Plas-Tal Manufacturing Co.; Premier Tile & Marble Co.; Reyes Masonry; Roy E. Whitehead Inc.; Shoring Engineers; SME Steel Contractors Inc.; Sound Crete Contractors Inc.; Steel City Glass Inc.; Stumbaugh & Associates Inc.; The MS Rouse Co.; Tractel Inc.; Traffic Management Inc.; United Paving Co.; Vertical Access Inc.; Wiss, Janney, Elstner Associates Inc.
After taking more than two decades to realize, the 235-ft-tall (W)rapper is the latest part of an ongoing 35-year revitalization and adaptive reuse plan for a former industrial and manufacturing zone.
Completed in December 2022 after four years of construction, this 180,000-sq-ft, 17-floor structure is the only commercially available, base-isolated, high-rise office building in the U.S.
Its state-of-the-art structural engineering features a network of curvilinear bands that originate from several geometric center points. Each curving band is wrapped around the largely rectilinear building envelope and folded around each vertical and horizontal corner of the building until it reaches the ground.
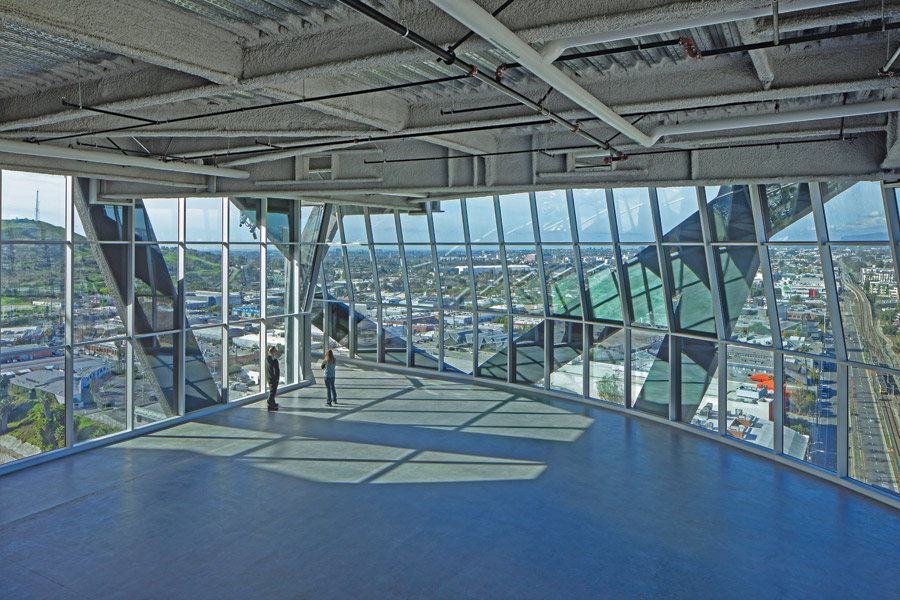
Photo by Tom Bonner
This means “there are no internal columns that would serve as conventional impediments to the use of the floors,” explains Eric Moss, principal at Eric Owen Moss Architects. The building has varying floor-to-floor heights of 13 ft 6 in., 16 ft 6 in. and 24 ft with a mezzanine.
The steel band structural system supports both gravity and seismic loads atop a base-isolated foundation supported by 20 triple-pendulum friction bearings, or isolators, that can accommodate a 30-in. displacement between site and building during a seismic event.
“In the world of construction, building the (W)rapper was nothing short of a marvel. Its one-of-a-kind complexities pushed the boundaries of what’s been thought to be possible, especially in relation to high-rise office buildings,” says Joe Healy, senior vice president at MATT Construction.
(W)rapper contains no structural concrete either, calling instead for steel plate shear walls, Moss adds.But this design also created some assembly challenges. For one, the tower couldn’t be self-supporting until the structural steel was all erected and welded into place.
To accomplish this, the contractor developed elaborate shoring and de-shoring processes. A series of wide-flange temporary columns surrounded the tower’s perimeter, each one placed strategically just outside where the bands would go, acting as temporary shoring. Each band was then tied off to a temporary column.
Removing the shoring system required dozens of high-capacity hydraulic jacks connected to a central controller, which slowly lifted the entire building from the temporary shoring shims and lowered it to engage the exoskeleton frame. The entire structure now sits on the 20 seismic base isolators.
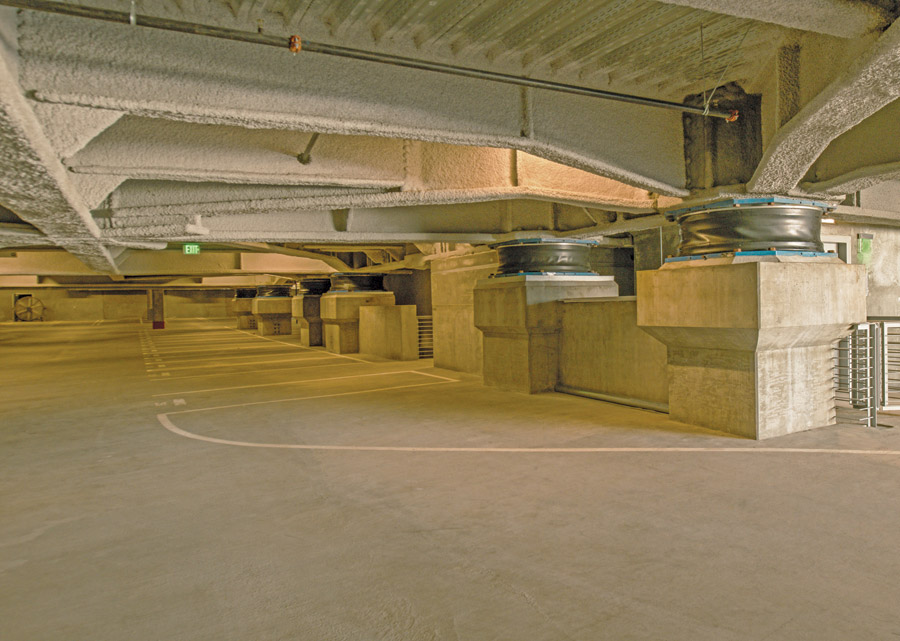
Photo by JenMarie Landing
“When you come into the first level of the garage, the isolators make a kind of exhibition if you are inclined to look at them,” Moss adds.
Each steel band is unique in size, shape and weight, and they were all fabricated in China. All band assemblies required a progressive assembly to ensure proper fit-up during erection. The team imported a massive luffing jib crane from Germany to place the fabricated materials, as the band assemblies weighed up to 60,000 lb. Once an assembly moved into position, temporary erection bolts set the steel in place before final welding. This effort required more than 26,000 worker hours of welding, sometimes continuous and even requiring multiple welders over multiple days.
Beyond its structure, the LEED Silver equivalent building features sustainable features, including a designed life cycle that is five times longer than a typical high-rise, natural site cooling thanks to an orientation that maximizes breezes from the Pacific Ocean and water reuse, with all stormwater collected, filtered and reused for irrigation through cisterns.
Post a comment to this article
Report Abusive Comment