Sixth Street Viaduct
Los Angeles
BEST PROJECT, HIGHWAY/BRIDGE, and EXCELLENCE IN SAFETY AWARD
KEY PLAYERS
Submitted by: HNTB
Owner City of Los Angeles Bureau of Engineering
Lead Designer/Structural Engineer HNTB Corp.
Lead Architect Michael Maltzan Architecture
CM/GC Skanska-Stacy and Witbeck
Erection Engineer COWI
Bearings Earthquake Protection Systems
With 10 pairs of striking—and non-uniform—concrete arches, third-generation triple-pendulum bearings, 27 million lb of falsework and a constrained urban site near a river and 18 railroad tracks, how difficult was it to build the $588-million, 3,060-ft-concrete tied arch Sixth Street Viaduct in Los Angeles?
“On a scale of 1 to 10, it was a 15,” says Michael Aparicio, senior vice president of operations with Skanska Civil USA’s West Coast team. Skanska with Stacy and Witbeck led the construction manager/general contracting team that built the downtown Los Angeles bridge, replacing the original iconic structure featured prominently in movies, videos and television.
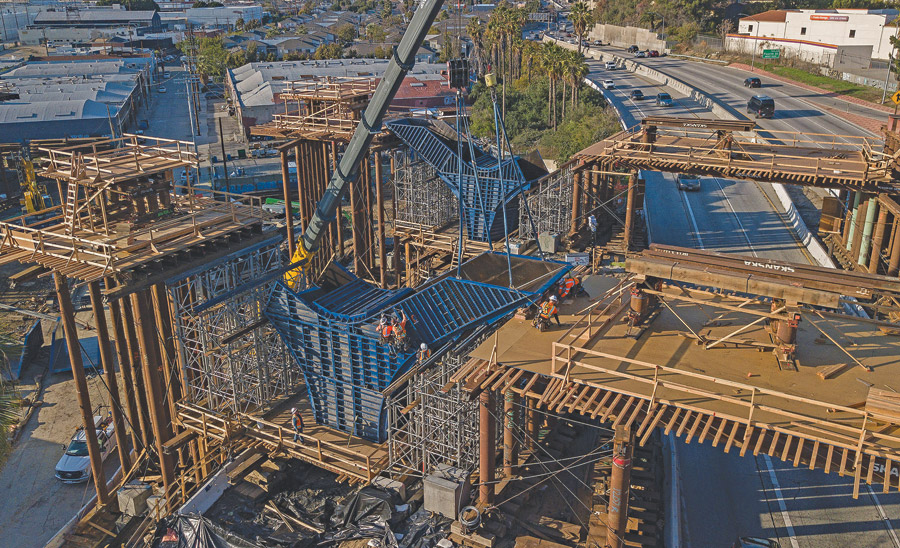
The project included 27 million lb of falsework, both above and below the deck.
Photo courtesy HNTB
The new bridge is already playing a similar role, thanks to the striking concrete arches that when lit at night create the image of a “ribbon of light.” But the unique design created by architect Michael Maltzan working with Poul Ove Jensen and lead designer/structural engineer HNTB “was extraordinarily difficult for engineering and construction,” says Aparicio. “The curvature in the columns coupled with enormous seismic challenges means all the elements required an extreme customized approach.”
Opened to traffic in July 2022, the bridge replaces a historic overpass built in 1932 that was the longest of 14 bridges across the Los Angeles River. The sand in its concrete created an alkali-silica reaction, a “cancer” that caused constant, severe cracking on the 46-ft-wide, four-lane structure just two decades after its completion. That, along with a functionally obsolete design and seismic vulnerability, made it necessary to take it down in 2016. Angelenos took home 1,300 concrete remnants of it as keepsakes.
The city launched a design competition in 2012 for the new bridge, as residents wanted something as iconic as the old one.
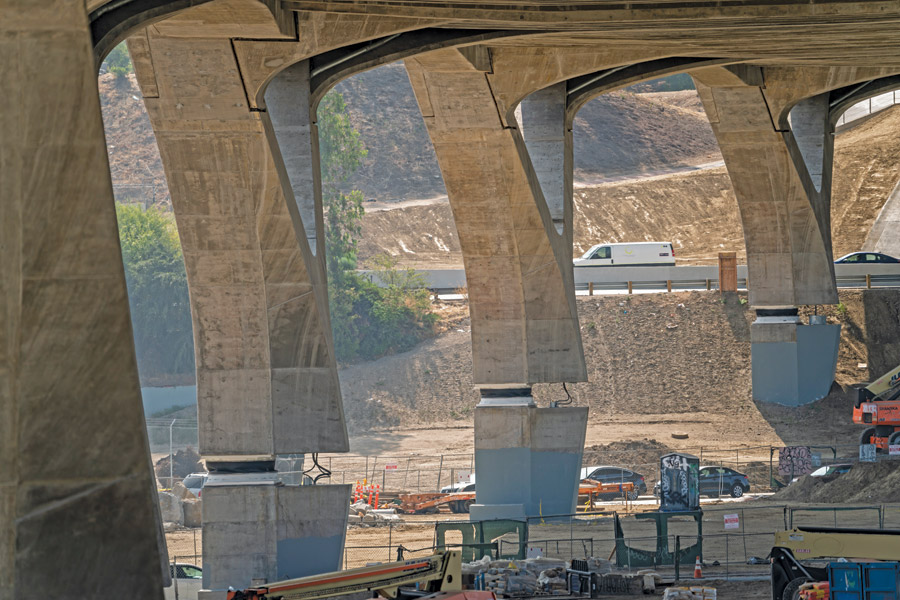
EPS designed third-generation triple-pendulum bearings and a secondary system that engineers believe will allow the bridge to function even after a 1,000-year seismic event.
Photo courtesy HNTB
“Consideration of the community drove the design,” says Michael T. Jones, project manager with HNTB, which won the competition in collaboration with Michael Maltzan Architecture. “We took a holistic approach, turning the whole viaduct into a signature structure—rather than just a crossing over the river—and making it a destination unto its own.”
The team was among six out of nine to be shortlisted and one of three given a stipend for further design. Following a four-month discussion with community members, a city design aesthetics committee chose the team’s design. The group had worked on several concepts containing cable-stayed, extradosed or arch main span with girder type bridges for the approaches but ultimately decided on a concrete viaduct, which provides a continuous structure using the most common and economical building material in California. The team worked with Maltzan and Jensen to conceive the idea of the ribbon arches
Eighteen Y-shaped bents, 90 ft wide and 30 ft tall, flow seamlessly into the arches that are meant to be a tribute to the original steel double-arch viaduct. The new viaduct’s arches cant outward at 9 degrees; the team says the purpose was to provide “framed” views of downtown to the west and the San Gabriel Mountains to the north and east at 300-ft intervals. The tallest pair of arches, at 60 ft, “accents” the LA River, according to the team. The second-tallest pair, at 40 ft, arch about U.S. 101 to the east.
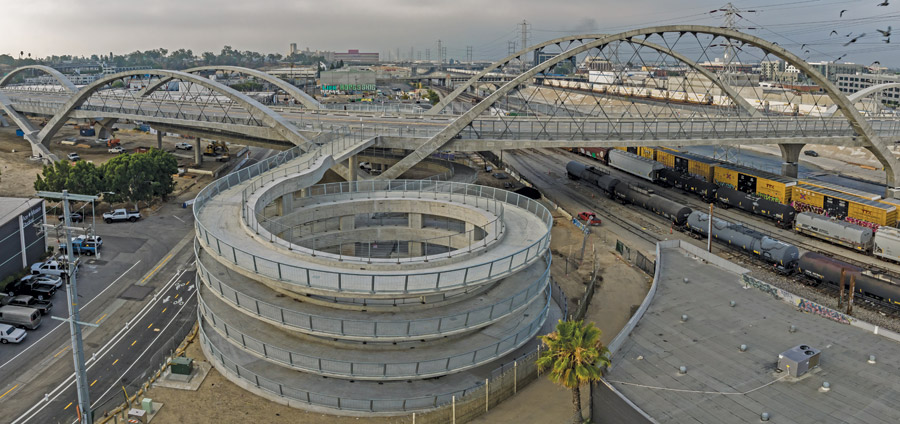
Ramps will connect the bridge to a planned park that the city hopes will revitalize the area.
Photo by Core-Visual, courtesy HNTB
At 100 ft wide, the bridge is 40 ft wider than its predecessor. It carries four vehicular lanes and 10-ft-wide bike lanes and up to 14-ft-wide pedestrian walkways on each side, in hopes of encouraging multimodal use and connecting downtown to the East Los Angeles neighborhood of Boyle Heights.
With the increased width, “it wasn’t practical to add cross-bracing between the arch ribs,” says Jones. “Computer simulations were showing that the arch ribs were not responding well to seismic ground motion. Our solution was to add seismic isolation, which was a game changer for the bridge.”
“On a scale of 1 to 10, this was a 15.”
—Michael Aparicio, SVP, Skanska, on the difficulty of building the bridge
Five sets of stairways and two bicycle ramps—one a four-level, 45-ft-tall helical shape—lead down to a planned 12-acre park dubbed PARC for Park, Arts and River Connectivity Improvements Project.
Demolition of the old viaduct and construction of the new viaduct had to be coordinated with freeway closures, railroad operations and rainy season restrictions. While installing 23 pile foundations, crews encountered groundwater and obstructions. The river banks were littered with old debris and cobble.
Crews poured the transverse floor beams with huge edge girders, then post-tensioned them with the falsework still up before building the arches. Skanska deployed a full-time building information modeling group, largely based in Boston, to identify all conflicts between rebar and post-tensioned duct banks in the bridge, says Aparicio. “They reconciled tens of thousands of conflicts. I don’t think this structure would’ve been buildable with this look and engineering 20 years ago,” he says.
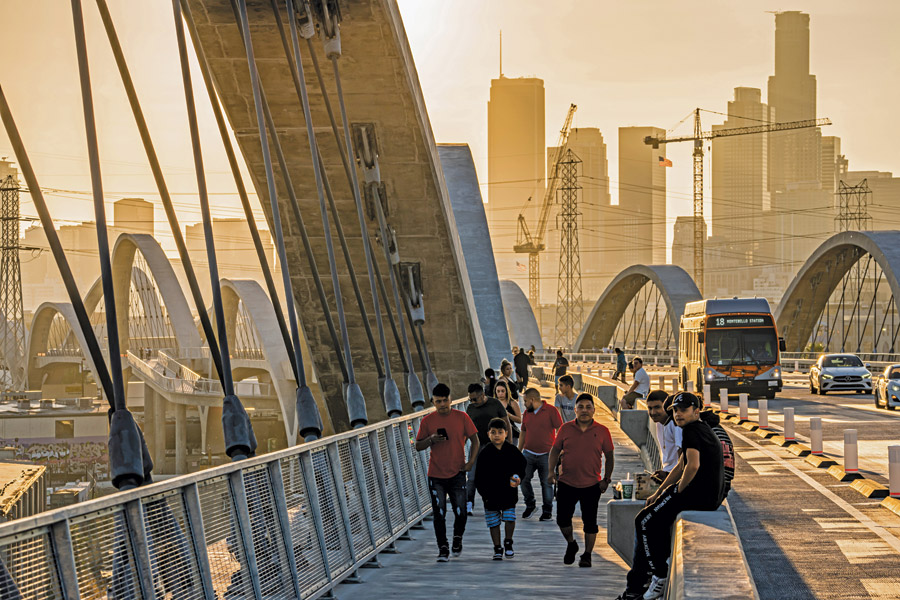
Although many Angelenos wanted a replica of the iconic original bridge, they have flocked to the new one.
Photo courtesy HNTB
Erection engineer COWI designed unique lock-up devices that held the Y bents in place during construction. The devices now serve as shear keys that will accommodate anticipated changes in the alignment of the continuous cast-in-place structure due to creep and shrinkage.
Earthquake Protection Systems developed and patented third-generation triple-pendulum bearings that will rapidly stiffen after an earthquake, allowing for activation of the secondary system in which the bearings would stiffen and the structure would revert to behaving conventionally. The bridge is expected to withstand a 1,000-year return seismic event.
The pandemic delayed completion by two years, but there were no serious injuries on the project.
Post a comment to this article
Report Abusive Comment