Demands from clients and labor shortages are forcing some contractors into other methods of creating building assemblies, driving new investments in prefabrication and modular construction techniques.
“Owners are demanding more prefabrication—the benefits are fairly well understood,” said Christian Burger, president and founder of Burger Consulting, at the Associated General Contractors of America’s IT Conference in Chicago held August 22.
Burger said that to operate in a prefab environment, “you’re no longer a contractor, you’re behaving like a manufacturer. If you’re not on [an enterprise resource planning system such as] IFS, maybe Acumatica, you don’t have systems to manage manufacturing.”
He noted that contractors are now working within a diverse marketplace, with fabrication facilities and related assets that can be rented out to other users as a side business.
Contractors on the coasts have been investing in their own fabrication shops and making technology investments, creating assemblies off-site since the early 2000s. Pioneers such as DPR Construction are now taking the prefab-first attitude further and standardizing on the cloud-based IT services.
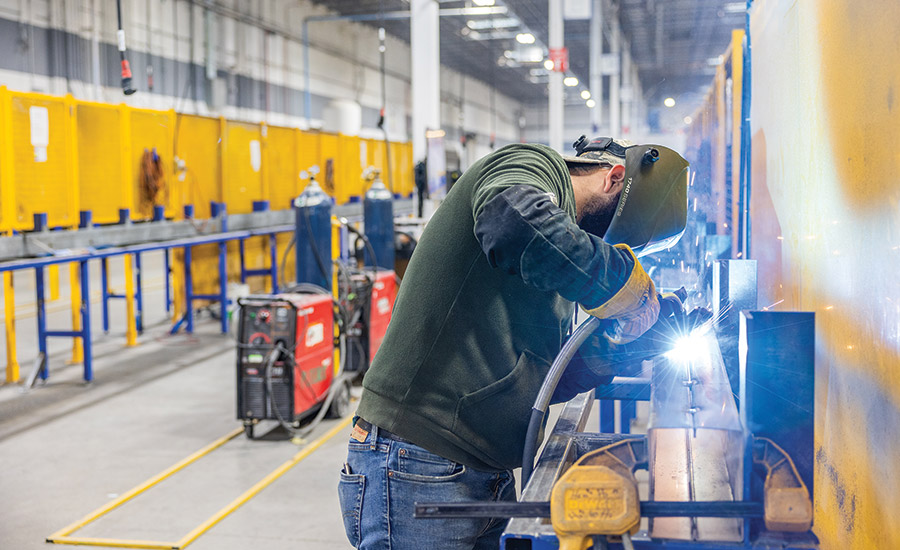
DPR’s Phoenix facility houses subsidiaries Digital Building Components, SurePods and EIG.
Photo courtesy Digital Building Components
“We look at it from the perspective of a project lifecycle,” says Atul Khanzode, technology and innovation leader at the Redwood City, Calif.-based contractor. “What you need during design to produce permits, to produce a set of documents, then shop drawings so that you can produce prefabricated elements or multitrade elements to what the facility managers need for operations and maintenance—these are all different views of data, some visual, some contextual data that’s attached to the visual information in the building information model.”
Khanzode also says that artificial intelligence, in certain use cases, has shown its value to DPR in terms of automating some of the contractor’s prefabrication processes. DPR has several manufacturing facilities and subsidiaries such as Digital Building Components, SurePods and EIG electrical systems. All play roles in procurement and supply for the parent company.
Jim Lynch, senior vice president and general manager of Autodesk Construction Solutions, sees a few key questions contractors ask themselves about these processes. “Do I build my own factory? Can I keep that factory busy enough to justify it? Or do I outsource it?”
“I think doing [prefab] holds great promise, but it’s not without its challenges,” Lynch says. DPR recently standardized on Autodesk’s construction cloud system as its single source of project truth. But while construction companies’ investments in doing their own manufacturing are impressive, we’re still “in the infancy” of prefabrication Lynch adds.
Bill Seery, prefabrication director at Consigli Construction in Boston, has seen both sides of the market having spent 16 years at SurePods, eventually rising to vice president. He joined Consigli to head its prefabrication efforts last year.
“We’re working in some of the really high-cost markets in the country—Boston, New York, etc. So we view prefabrication as beneficial in that manner,” he says.
Seery says Consigli is delivering light-gauge steel assemblies in New Hampshire and Massachusetts. When he was at SurePods, the firm provided bathroom pods for the Prism Apartments in Cambridge, Mass., and other health care projects. Large contractors need to get fabrication facilities to “a certain level of scope and size” for the economies of scale to kick in, but Seery says the benefits are worth it. “If I’m seeing dozens of projects every day, if not hundreds, then you can see the same lesson happening over and over.”
Post a comment to this article
Report Abusive Comment