Winding along the edges of steep slopes deep in the eastern forests of British Columbia, a stretch of Highway 1 offers stunning vistas for commuters and visitors as they traverse Kicking Horse Canyon. But the 70-plus-year-old two-lane highway also has been susceptible to rockfalls, avalanches and traffic accidents involving both humans and wildlife.
Three phases of work since the mid-2000s have transformed 21 kilometers of narrow, winding two-lane canyon highway into a modern four-lane, 100 km/h standard. But construction of the fourth and final phase to complete the most difficult remaining 4.8 km entailed years of planning and extensive redesign due to complicated geology. The project team also needed to keep local towns connected—as well as the rest of Canada.
“The Trans-Canada Highway is an artery,” says Michael Gash, construction manager with Kicking Horse Canyon Constructors (KHCC). “If it gets shut down, there is a huge economic impact. Everything lands in Vancouver and funnels through the highway throughout the rest of the country.” Roughly 30% of the 12,000 daily vehicles are commercial, he adds.
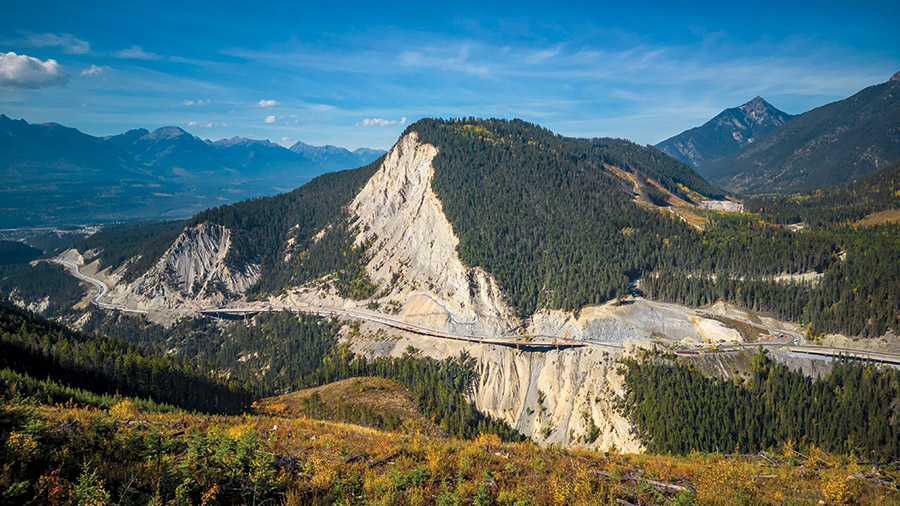
Photo courtesy of KHCC
KHCC, a design-build joint venture of Aecon, Parsons and Emil Anderson, won the $331-million contract in 2020 to realign and upgrade the remaining section of Trans-Canada Highway 1 to four lanes from two, eliminating 13 hairpin curves. Crews are building four bridges, nine viaducts and seven mechanically stabilized earthwalls; conducting major cuts and excavations; relocating utilities; and mitigating rockfalls and avalanches. Even harsh winters have not stopped the fast-track project, which is on schedule for completion this winter.
Those 4.8 km constitute just a fraction of British Columbia’s overall plan to make Highway 1 four lanes between Kamloops and the Alberta border. Since 2001, 68 km have been completed, including the first three phases of Kicking Horse Canyon.
The original stretch of Highway 1 through the canyon, with sharp curves and falling debris, has traditionally seen twice the provincial average of highway incidents, according to the province website. As recently as last year, a motorist was killed when a boulder hit her car, in a tragedy unrelated to the construction that aims to alleviate that very risk.
Phase 4, encompassing the most rugged terrain of the entire alignment, had to wait until sufficient funding. “It was clearly the most complex part” of the program, says Gash. The Canadian government pitched in $162 million for the project, with British Columbia funding the rest.
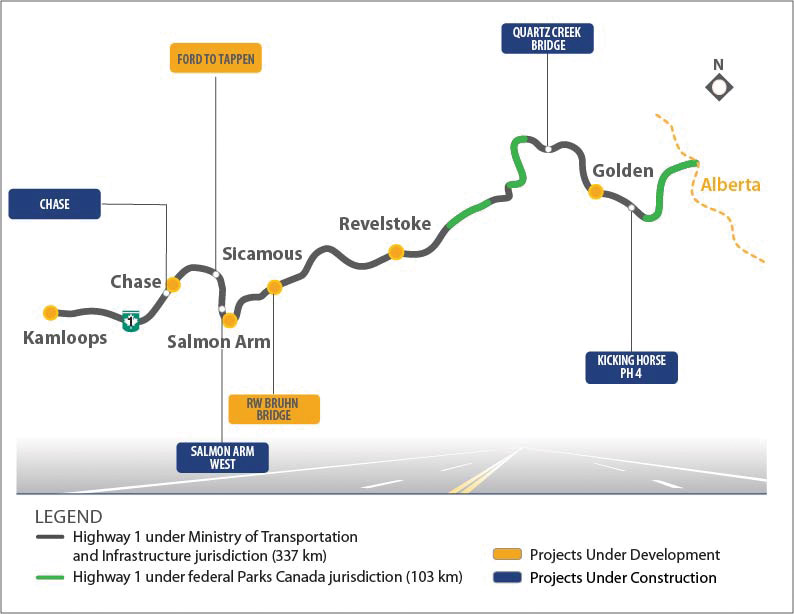
Map courtesy of BC Transportation Investment Co.
Steeped in Challenges
North America map by Getty Images/ Danica Jovanov
The site crosses a series of unstable slopes, and the rough concept given to the design-build team had a conventional solution of stabilization pipe piles installed in front of retaining walls to support the highway. But after extensive geotechnical exploration, engineers realized that such piles would need to be of large diameters and installed with very tight spacing, often with rock anchors restraining the pile top. These would be costly and time-consuming to install, and would require extensive, complex temporary access and stabilization for equipment.
“When we started, we had four or five bridges in preliminary design,” says Gash. “The majority of the project was going to be a lot of walls and graded road, and downslope retaining walls. Now half the project is on bridges and viaducts.” The four bridges have varying span lengths ranging from 30-70 m and are typically over deep gullies of up to 65 m deep. The viaducts have consistent, repeating short spans of approximately 23 m, and are generally less than 5 m above existing ground.
Under the original concept, piles would sometimes be within a meter and half of each other, and downslope from the new alignment, notes James Williams, principal with BASIS Engineering Ltd., one of the two geotechnical subs. The team worked with the province to upgrade—literally—the overall design. “With the viaducts concept, we could move the piles upslope a bit—away from treacherous locations and into easier-to-access areas. It also allowed us to place piles 24 m apart, reducing piling requirements substantially. The design philosophy is that instead of resisting the soil loading with elements, we allow soil to move around the piles.”
Jason Jardine, a design lead with KHCC, says the most fundamental change was to the roadway alignment. “There was a lot of back and forth about a narrow corridor, a railway below us and really a lot of tradeoffs that had to be done to meet the 100-km design speed,” he says. “What ultimately came out was a general pushing of the alignment out away from the mountain and lowering the profile.”
Konlee Dobbins, also a design lead, adds that this affected the bridge locations. “We moved each bridge where it touches down [so that] the substructures and abutments would be in better soil conditions. Access was a huge factor on this project. We were trying to find [good] access points to have working platforms and then be able to span over deep valleys and be able to construct those temporary trestles to slide girders into place.”
The new structures had to be either protected in place from rockfalls or “in some cases we dug out a bit more than initially planned just to provide safe paths for 300-year avalanche events,” Dobbins adds.
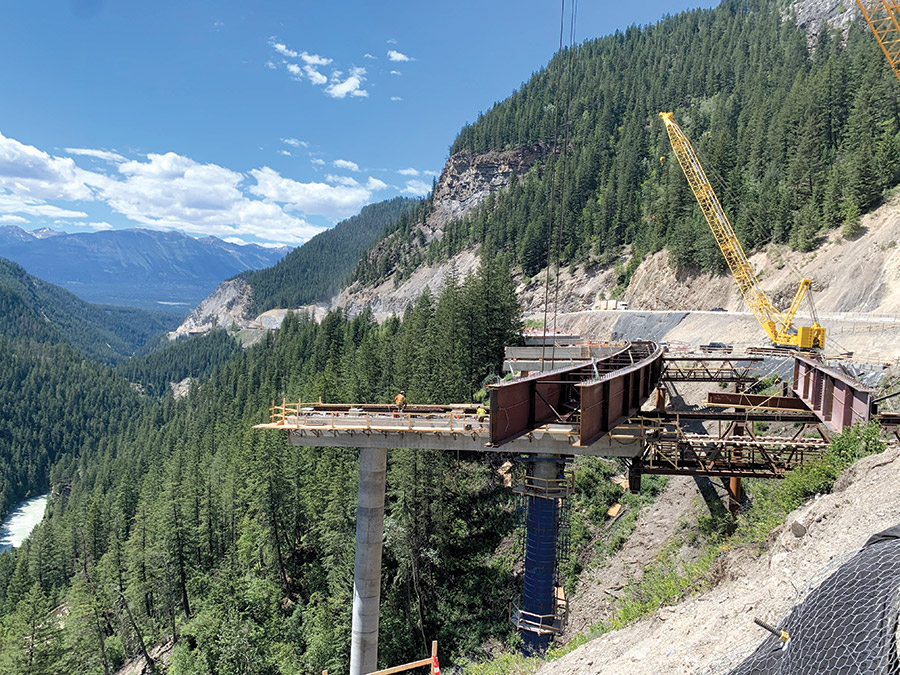
The team had to constantly readjust locations of piers and equipment due to unpredictable geology.
Photo courtesy of KHCC
Moving Targets
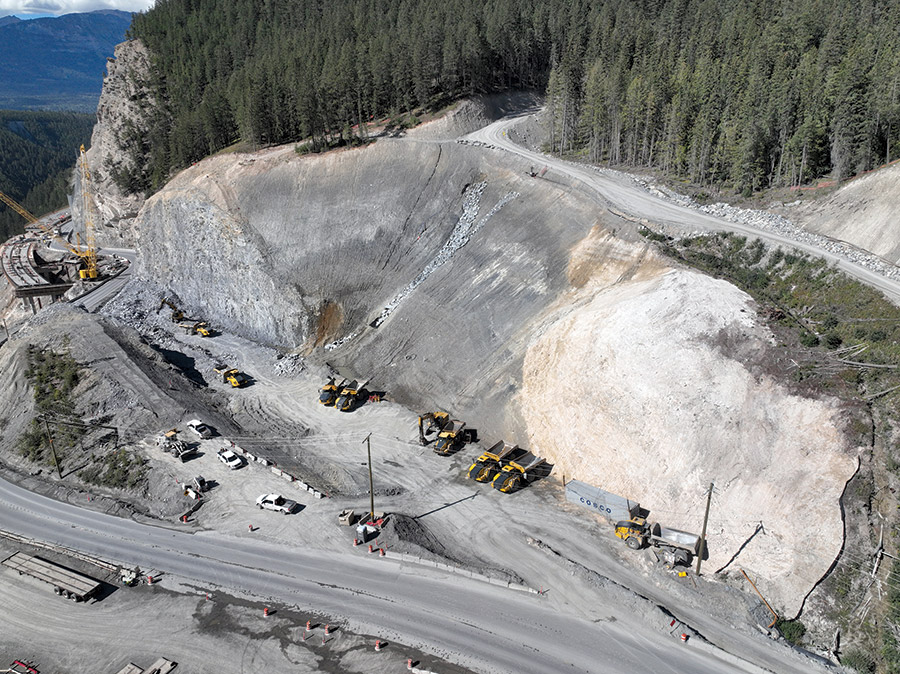
Photo courtesy of KHCC
Foundation construction had to start in early April of 2021, just five months after commencement of design, due to the design-build nature of the job. A major geotechnical investigation during November and December 2020 found unexpected conditions, including unstable slopes and varying depths of bedrock. It resulted in a detailed design that was different even from KHCC’s submitted plan during bidding.
“In our area, complicated glacial lacustrine soils were problematic,” says Williams, referring to the eastern third of the alignment. “Most of the site was colluvium overburden atop stable rock. The critical path involved getting piles installed early on. Supporting the temporary works was a big challenge during the spring melt in February and March. Everything was unstable and we constantly had to check designs of working platforms and crane pads and assess safety of locations daily as conditions changed.”
Bedrock depths were so variable that often crews couldn’t be absolutely sure how deep to drive piles until they actually did it. “You can’t drill a hole at every pile location,” says Paul Wilson, partner with Thurber Engineering Ltd., the other geotechnical sub. “We had to basically allow for contingency. [We had to] guess at the range of rock depth at every pile.” Concrete-filled steel piles had diameters as large as 1.22 m.
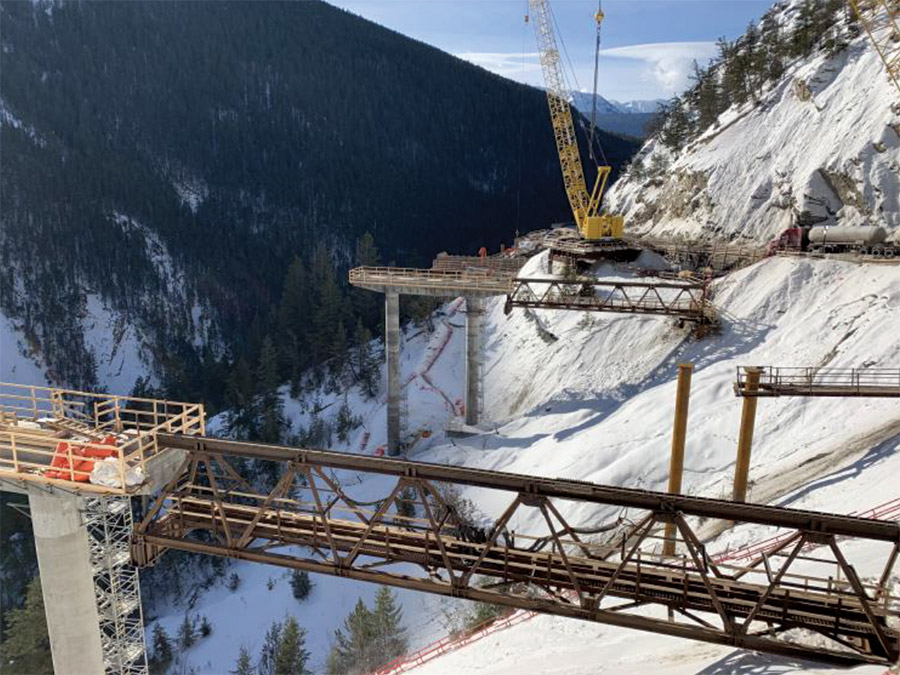
The placement of everything from temporary works to crane pads to permanent structures had to be tweaked according to changing soil conditions.
Photos courtesy of KHCC
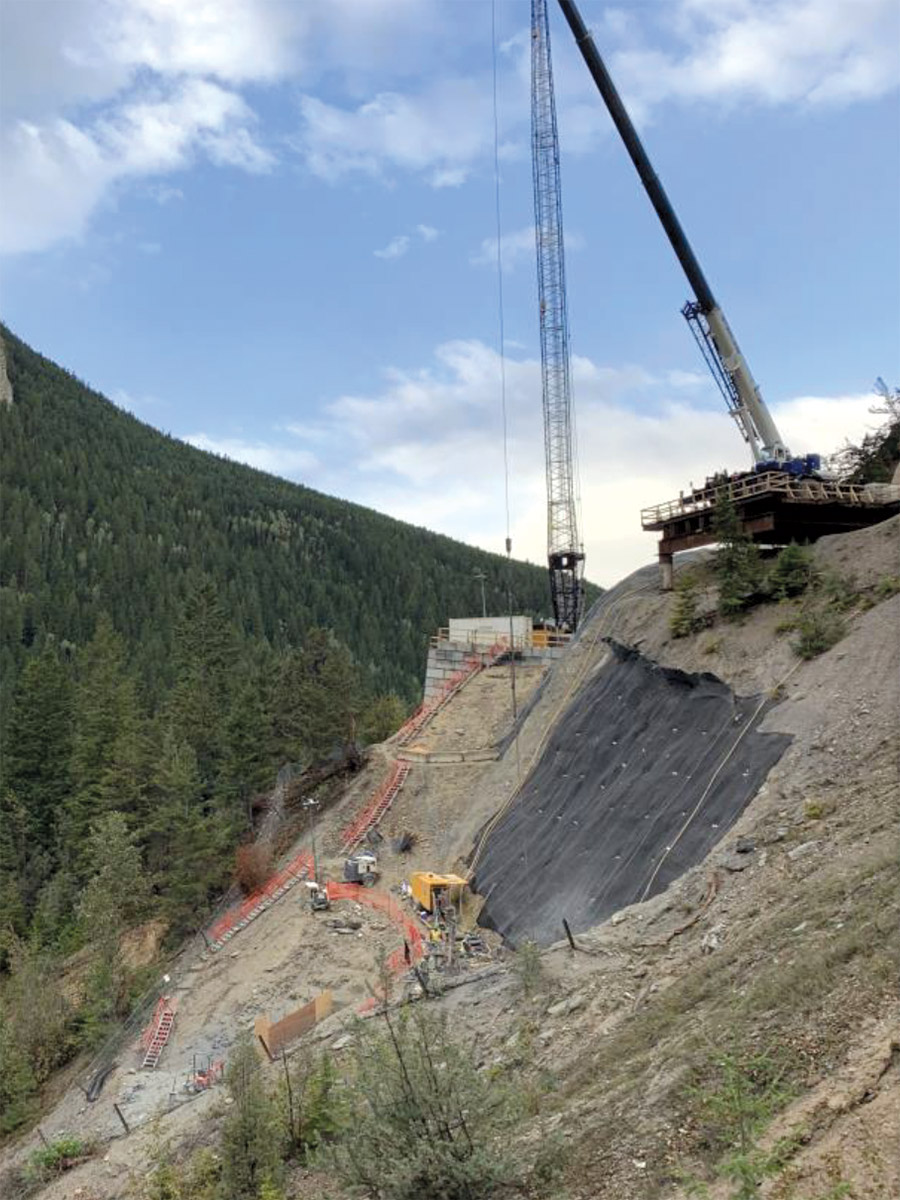
The 600+ piles range from 7 to 65 m long, adds Nikki Turner, KHCC foundations manager. Crews operated five rigs with up to eight shifts day and night at peak. For bridge pier locations that were particularly difficult to access, crews installed a total of 144 micropiles. Spider excavators supported by winch cables “get to places no conventional excavator can get to or where we couldn’t build an access road.”
In a paper jointly authored by the geotechnical firms, the authors noted: “There are no established design methodologies in geotechnical practice for design of piles embedded in a moving embankment, other than in seismic design for weak liquefied soils.” The methodologies jointly developed by the two firms went through an independent check by Tetratech, and approval from the BC Ministry of Transportation and Infrastructure’s geotechnical engineers and their owner’s engineer WSP/Wood.
Temporary power and communications lines are currently fixed on the downslope side of structures, notes Turner. “When the team started, they were running overhead on the downslope side of the old highway. In the first phase [building the eastbound lanes], they were temporarily buried out of work areas. In the second phase [building the westbound lanes], we flipped the utilities onto brackets on the downslope side of the eastbound lanes.”
Now there are permanent duct banks for utilities to run on upside of structures. Meeting BC Hydro requirements required temporary junction boxes and access, and coordinating the actual switch of the power, adds Turner. “The completion of each utility phase was a critical milestone, which needed to be coordinated well in advance for BC Hydro and Telus to complete their own cable pulls.”
On constant alert for rockfalls and avalanches, the team installed rockfall attenuators above three of the four rock cuts along the alignment. A synthetic aperture radar scans the project from one side of the canyon every 20 minutes to detect displacement, says Jason Adam, KHCC civil manager. “Alerts are received real time via text and with satellite communications so our offsite geotech team has access to the data collected by the radar station. It has successfully alerted us of many tension cracks before they opened up.”
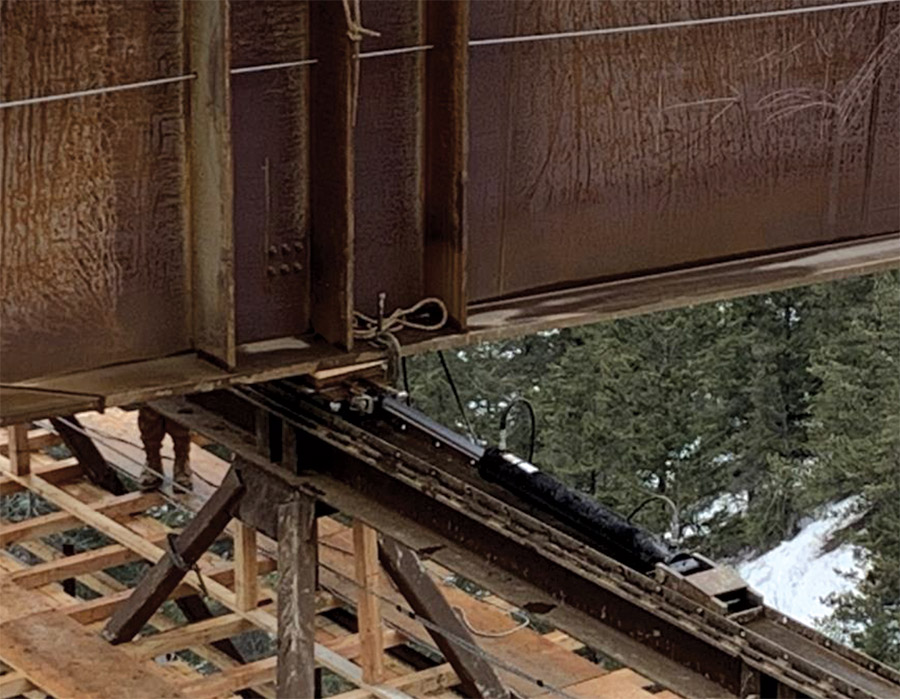
The major steel-girder structures were slid laterally into place in particularly unstable and steep areas.
Photos courtesy of KHCC
Slides and Landslides
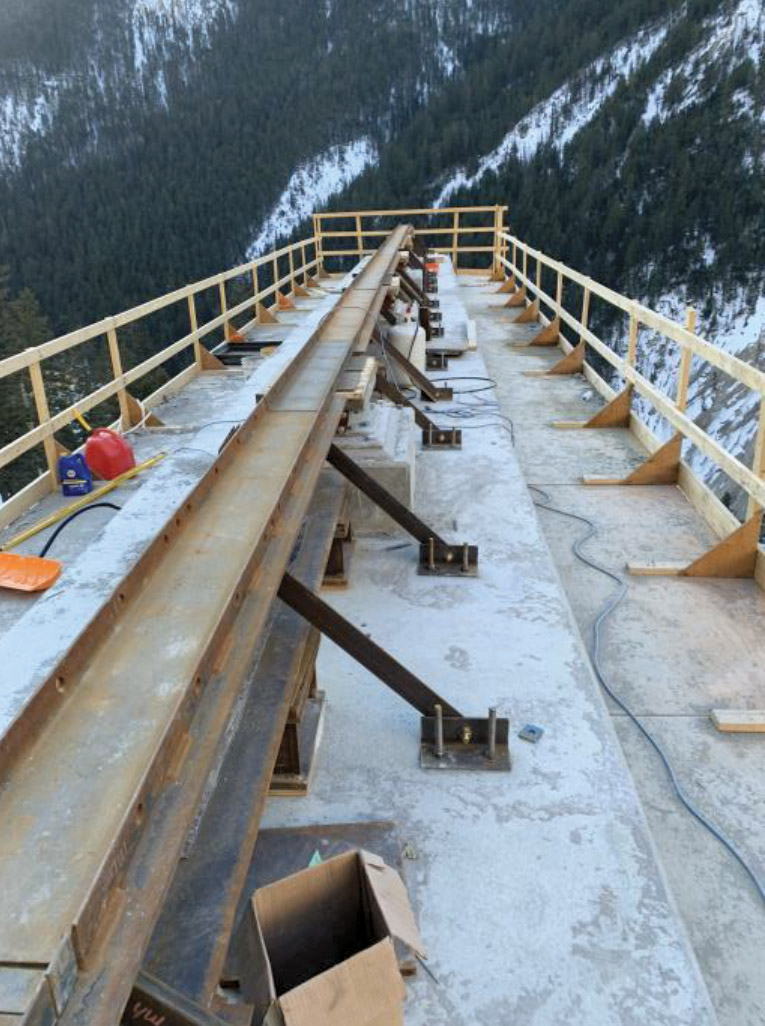
Viaduct piers were designed with precast “sub-caps” and integral cast-in-place diaphragms to eliminate bearings and allow increased tolerances for placing precast caps and stringers. But the size required for pile caps to resist thermal contraction loading and potential avalanche and soil loading would make shipping and lifting the components unfeasible, notes Wilson. Therefore, crews installed a short section of 610-mm-dia pipe into the top of each concrete-filled pipe pile. This made the system more flexible, thereby reducing thermal loads and allowing greater lengths between expansion joints. These short pipe elements, dubbed “drift links,” allowed for smaller voids in the precast caps used for pipe connections and ultimately a more compact precast pile cap.
“We ended up with such long structures,” says Kyle Rhoda, KHCC structures manager. “We had to find a way to build them all within the [tight] timeframe.” For nine viaducts totaling more than 1.8 km, 1,000 precast concrete components were transported from as far as 700 km. In general, piles support precast pile caps, precast box girders and cast-in-place concrete decks, says Rhoda.
Aside from the nine viaducts, crews built four bridges: the 108-m-long concrete girder Sheep Bridge, the 160-m steel girder Bighorn Bridge, the 134-m steel girder Frenchman’s Bridge and the 110-m steel girder Blackwall Bridge.
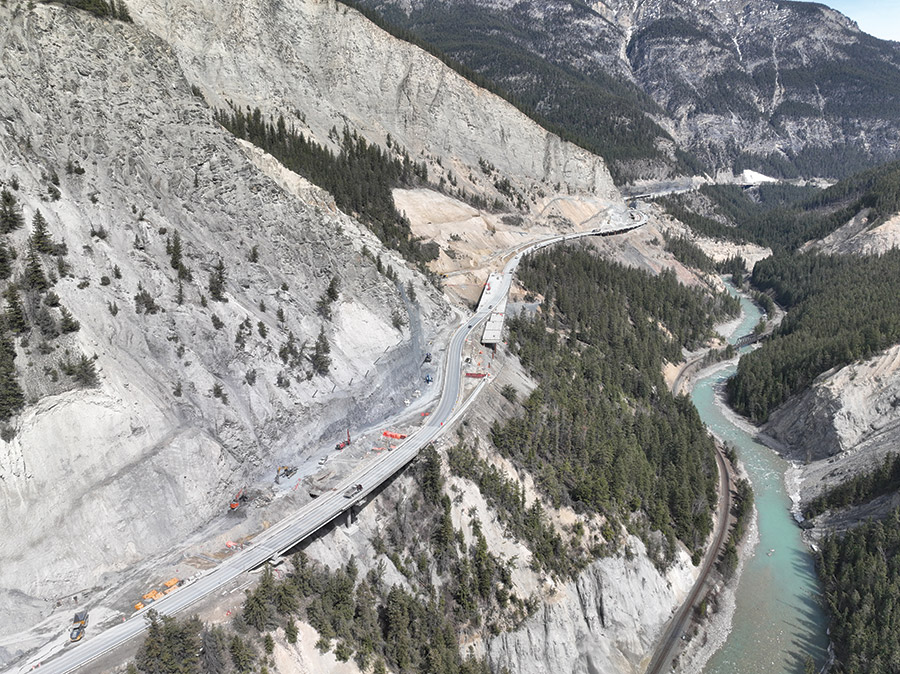
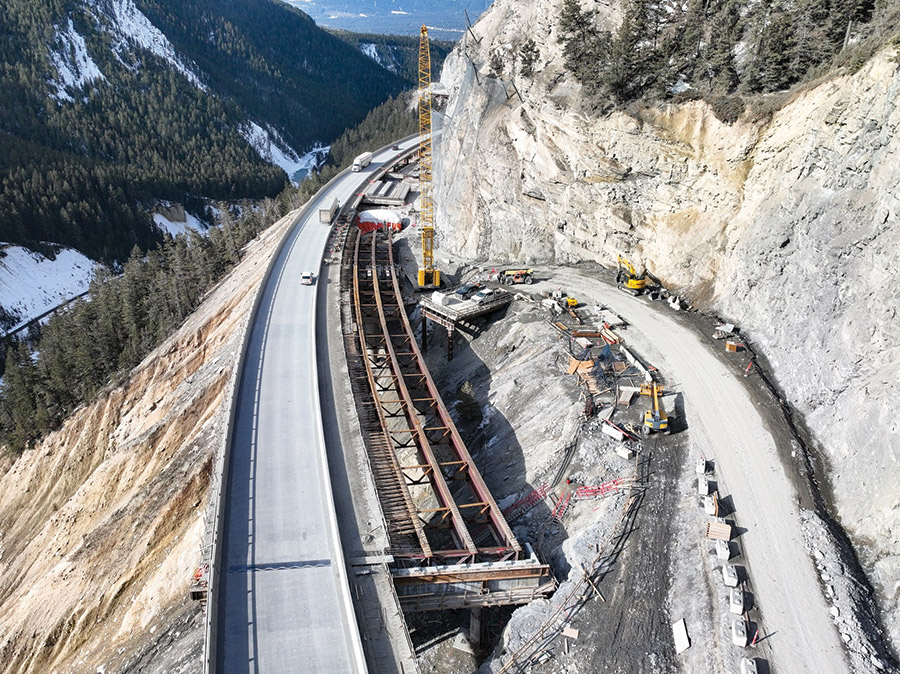
The new four-lane divided highway smooths out the hairpin curves and uneven grade of the original alignment.
Photos courtesy of KHCC
The original concept provided by the ministry was to launch the steel bridge girders longitudinally. The project team decided to launch the girders laterally along the steep terrain. That required temporary trusses and platforms carved into the sides of the mountain in the unstable and varying soil conditions.
Individual girders were assembled into a paired and spliced curved 4-pack. Each 4-pack is hoisted and spliced to previously erected pier girders to make a 70-m span. These picks utilized offset rigging to shift the crane pick points within the pair and align to the geometry of the curved girders. The tandem picks had a total weight of 230,000 lb each. Once the girders were set, crews launched them transversely further out into the canyon, either uphill or downhill, with hydraulic rams.
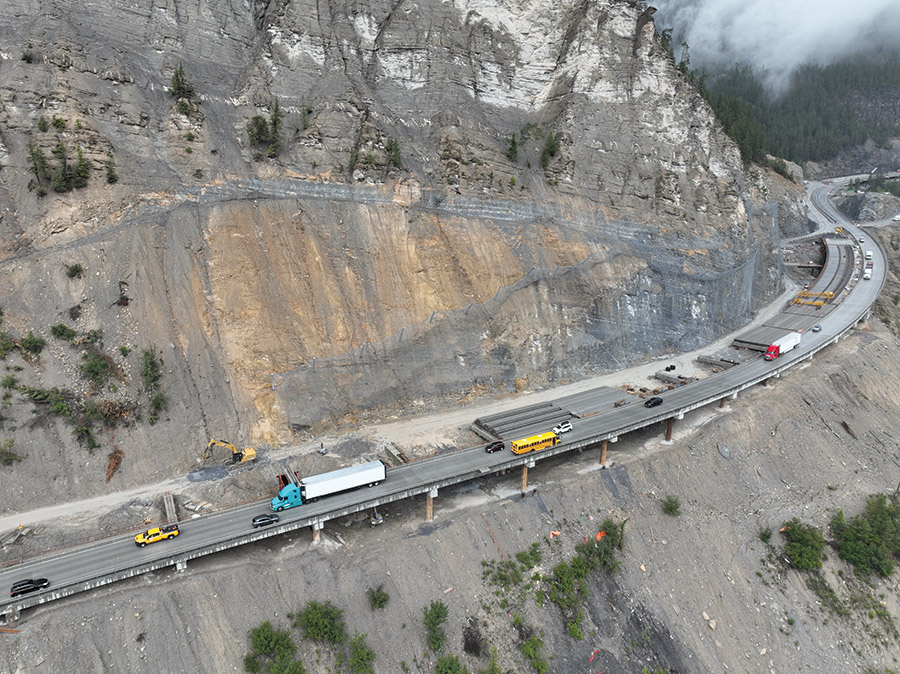
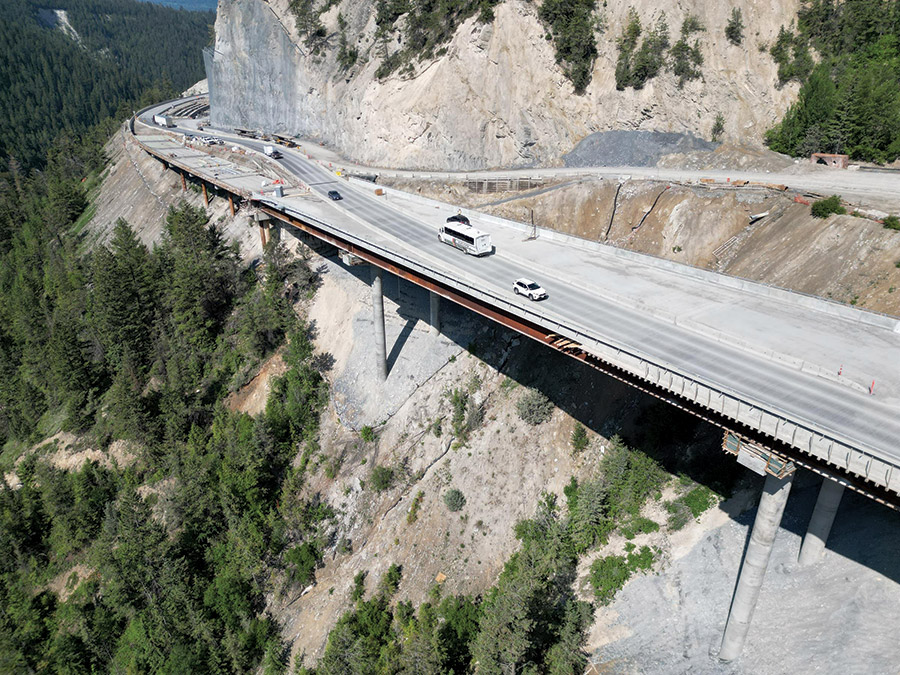
Existing traffic, an active railroad, wildlife and falling debris all had to be accommodated with fencing, ditches, netting and monitoring.
Photos courtesy of KHCC
The work also included four rock cuts as high as 60 m above the existing highway and entailing almost 300 small rock blasts, with almost 100,000 sq m of overburden removal and 320,000 sq m of rock. A total of 1.2 km of rock attenuator post-and-mesh fencing rated at 6,000 kJ protects the site. “The rock cuts were quite challenging—large, steep cut into tricky rock, heavily faulted and folded,” says Wilson.
Debris drops into ditches ranging from 6 m to 20 m in a controlled fashion, says Rhoda. Two of the cuts were in restricted zones with the CP railroad some 1,000 m below. Crews worked constantly with railroad flagmen to ensure no disruptions for 30 daily trains. Acid-generating rock was hauled to a nearby disposal site. “It gets encapsulated and left there forever,” says Khoda. Crews also built 1,203 linear m of mechanically stabilized earthwalls, a 95-m-long cast-in-place wall and two wildlife passages beneath the highway.
Two new eastbound lanes are now carrying vehicles while crews work on completing the westbound lanes, says Chris Koop, KHCC construction project manager. The project is on schedule for completion by early 2024, despite the initial winter bringing one of the highest numbers of avalanches in the region’s history, he adds.
Due to occurrences whether nature- or construction-made, motorists using the highway during construction had to apply for seasonal or day passes and track a website that lists closures, stoppages and single-lane alternating traffic situations. During extended closures, half-hour windows of travel are allowed each day, with a dedicated number for first responders.
The province is committing $548 million over the next three years for continued four-laning of Highway 1 between Kamloops and the Alberta border, with almost 20 km to be upgraded among five projects. But none will be as tricky as the Kicking Horse section—not that many users will know it. “People driving by at 100 kilometers an hour will never realize they’re crossing a bridge or viaduct,” says Adam.
Post a comment to this article
Report Abusive Comment