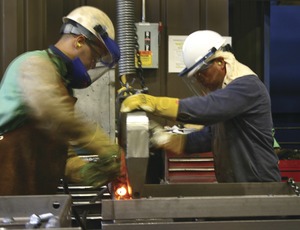
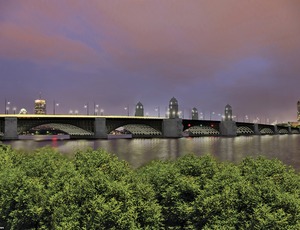
Restoration of the 106-year-old Longfellow Bridge, which spans the Charles River between Boston and Cambridge, evokes Rosie the Riveter's World War II era, when hot metal pins connected structural steel on bridges, skyscrapers and ship hulls.
A joint venture of J.F. White, Skanska and Consigli began work in July 2013 on the $255-million design-build project, scheduled for a November 2016 completion. The goal is to replace structural elements while retaining the aesthetics of the 2,135-ft-long bridge, which has 11 open-spandrel steel-arch spans, plus two steel-girder approach spans at the Cambridge end. With a deck width of 105 ft, it carries trains, vehicles, pedestrians and cyclists.The granite masonry piers support four towers that inspired the nickname "Salt and Pepper" (ENR 6/11/07 p. 16).
From its 45,000-sq-ft facility in Georgetown, Mass., Cianbro Corp. is supplying most of the replacement steel and assembling members with rivets for the exposed areas. TC bolts and hex bolts are used for the rest.
Cianbro tracked down Steve Howell, the owner of Ballard Forge, Seattle, who is heavily involved with riveting and restoration work for small-scale historic preservation, says Bob Small, Cianbro project manager.
"He came out to demonstrate for a week, and our research team dug up old specs to improve our knowledge of tools that became obsolete when the industry began replacing rivets with high- strength bolts in the 1950s," Small says.
"We had a tough time finding a mill willing to produce A502 steel," Small says. But Mokena, Ill.-based Chicago Fasteners found a hot-rolled-steel production facility. The company is cranking out 20,000 units of a stock rivet item that Cianbro purchases in bulk, then presses and forms for the job. Workers heat the rivets to 1,900°F, then place, using tongs, the malleable steel through a hole to form, using a hydraulic press, a rivet head.
Chuck Sabella, resident engineer with the Massachusetts Dept. of Transportation, spent hours poring over engineering plans from the early 1900s. "We can see how they lined holes up—how they made things fit," says Sabella. "You would expect the plans would be more crude, but there is amazing detail all done by hand, including the pile locations."
In the first of six phases, demo work and construction is taking place along the Boston-bound side of the bridge, with one lane carrying vehicles, bike lanes and sidewalks. Trains will continue to run except for occasional weekends, to accommodate rapid construction.
Working in confined spaces, crews are reconstructing the bridge using replica spandrel columns fabricated by Cianbro, while repairing the original steel-arch rib girders. Crews also are performing seismic upgrades with reinforced steel inside the hollow piers.
In the next couple of weeks, crews will be installing spandrel columns, Sabella says. Early completion will win incentive pay of $75,000 per day with a $15-million cap, with equivalent late penalties for each day beyond Nov. 16, 2016.