Last summer, Paul Schwer, a green mechanical engineer, met with Portland, Ore., Mayor Ted Wheeler to talk about a subject dear to him—resilient structures for the earthquake-prone city. Those who don’t know Schwer, president of PAE Consulting Engineers Inc., might question why a mechanical engineer would be asking a mayor for a city grant program to make new office buildings as quake-resistant as hospitals.
The answer involves Schwer’s pet project—a 58,000-sq-ft speculative office building that started construction on April 1 in Portland’s Skidmore/Old Town historic district. The five-story PAE Living Building, named after its prime tenant, is on course to be the first—and the largest—privately developed office building to be fully certified under the rigorous Living Building Challenge sustainability program of the International Living Future Institute (ILFI). And if it opens as expected in September 2021, it also will be one of very few developer buildings designed to survive a magnitude-7.5 quake with barely a scratch.
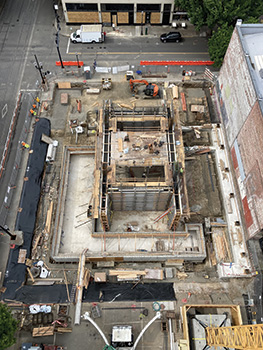
A resilient PAE building is attractive to Schwer because it would allow immediate reoccupancy after a quake, which would minimize business interruption. And as a prospective tenant, the mechanical-electrical-plumbing (MEP) engineer wanted seismic resilience. But both Schwer and PAE also had another reason—they have equity in the building. And to further the break with tradition, ZGF Architects and contractor Walsh Construction Co./OR also have stakes in the project.
Though drawn to the idea, Schwer says Wheeler turned down the request for grants for better seismic performance—mostly because the city coffers were dry.
Undaunted, Schwer pitched a wilder idea. After a major quake, PAE would vacate its three floors for six months so the city could move into the fully functional building and set up an emergency operations center. For the privilege, all the city had to do was pay the landlord an annual rent of $0.50 per sq ft. “I thought of this before COVID-19, when I didn’t even know whether we could work remotely,” says PAE’s Schwer.
Again, Wheeler was intrigued but not swayed. Consequently, the PAE building team found another way to pay the $135,000 premium to stiffen the structure.
Ordinary office buildings are required to have an 8-in. seismic joint—an air space between the exterior wall and the property line so that swaying neighbors do not collide in a quake. But the stiffer PAE building would only sway as much as 4 in. at the roof. That allowed a 4-in. joint along the two affected sides of the building. That in turn facilitated a larger floor plate, which increased leasable space—enough to cover the premium.
Seismic resilience isn’t the PAE building’s only rare feature with a premium. The $40.2-million building also will contain the first commercial installation in the Americas of a system that turns nutrient-rich urine into agriculture-grade fertilizer. “We are taking the pee out of PAE,” says Kathy Berg, a ZGF principal.
If successful, the nutrient recovery system could serve as a model for liquid waste treatment in terminals, sports facilities, amusement parks and more—relieving strain on wastewater treatments plants, says Harold Leverenz, co-founder, with Russell Adams, of Advanced Environmental Methods LLC (AEM), which developed the system, called AmmPhotek.
“We are decentralizing fertilizer production. How game-changing is this?” asks Pete Munoz, practice lead for Biohabitats, the PAE building’s water infrastructure engineer and the person who suggested the system.
Living Buildings Cost More
Exotic systems, such as rooftop solar and onsite water and wastewater treatment, may make Living Buildings independent, but they also make them 20% to 25% more expensive. The PAE building is expected to cost $435 per sq ft. That compares to about $314 per sq ft for an ordinary building, says Ed Sloop, Walsh’s chief estimator-project manager.
The premium for rainwater-to-potable water, composting, graywater and nutrient recovery alone is $1.25 million of a $25.2-million hard cost. And though public utility bills are low or nonexistent, there are costs associated with maintaining the systems.
“A building like this is great for everybody, for it is showing people possibilities.”
– Terry Whitehill, Portland’s Building Official
During design, the pro forma ruled. Finding ways to pay for the exotic systems was a near-constant exercise for the investors, which also include developer Gerding Edlen, landowner Downtown Development Group (DDG) and office broker Apex Real Estate Partners. “There is no question a Living Building is harder to pencil,” says Jill Sherman, a Gerding Edlen partner. “We had some difficult conversations.”
To relieve some budget stress, Gerding Edlen found a parcel of land owned by DDG and offered it equity in the venture instead of cash for the land.
PAE, Apex and ZGF also waived fees in return for equity—a risky proposition because, until the permit was issued, there was no guarantee the project would go forward. Walsh waived compensation for 27 months of preconstruction consulting, starting in January 2018.
And like the others on the team committed to making better buildings, the contractor also invested directly in the enterprise. “This project has a lot more inherent risk because it has not been done a thousand times,” says Sloop.
The core group covered about half the total equity for the project. Outside equity came into play only after the city issued the permit.
Jason F. McLennan, ENR’s 2016 Award of Excellence Winner for creating the Living Building Challenge, calls the core group’s up-front investment “development bravery.”
Throughout planning and design, there were many ideas that saved features, similar to the one for the structure. Still, triple-glazed windows, automatic external shades and skylights got the axe. “Wearing two hats changed our perspective about design decisions,” says ZGF’s Berg.
“We are enormously happy about the PAE building. I’m only unhappy we don’t have 100,000 Living office buildings.”
– Denis Hayes, President, Bullitt Foundation, First Organizer, Earth Day>
The process was strenuous. “It seemed we had many brushes with death,” associated with the budget, Schwer says.
Perhaps, but for Living Building certification, the team needed less handholding than previous teams that took the challenge, says Kathleen Smith, ILFI’s Living Buildings vice president.
One reason is that PAE and ZGF are Living Building design veterans, for partial and/or full certification. PAE first got its feet wet on a Living Building when it engineered Seattle’s 52,000-sq-ft Bullitt Center—the first and largest speculative Living office building.
The PAE building is cut from the cloth of the six-story Bullitt, but surpasses its sustainability and resilience. That is fine with Denis Hayes, president of the Bullitt Foundation, which developed Bullitt to prove the feasibility of a spec Living office building to dubious developers.
“We are enormously happy about the PAE building,” says Hayes, who organized the first Earth Day. “I’m only unhappy we don’t have 100,000 Living office buildings.”
The PAE team applied lessons from Bullitt, which houses PAE’s Seattle office. For instance, moisture problems with the foam-flush composting toilets prompted PAE to select a vacuum-flush toilet system. And in a role reversal of sorts, Bullitt is switching to vacuum-flush toilets, based on PAE’s investigation.
“There is no question a Living Building is harder to pencil. We had some difficult conversations.”
– Jill Sherman, Partner, Gerding Edlen
McLennan is thrilled with the Portland project, especially the wastewater system and the more historic-looking architecture, required because of the landmark district. “We need Living Buildings of all styles and shapes,” says McLennan, ILFI’s founder, past chair and founder of McLennan Design.
The historic district is designated as an economic Opportunity Zone, which allows investors to defer capital gains for about a decade. But the location complicated the Living Building requirement for renewable power generation.
The PAE building did not have enough roof space for the total kW required for its solar PV array. But landmark rules meant no overhangs or any solar arrays could be visible from the street. Fortunately, in 2018, the Living Building Challenge added an exception for offsite renewable power, to encourage Living Buildings in dense urban areas where power needs cannot be met onsite.
As a result, and to fill its equity obligation for certification, PAE’s core group is helping pay for a 195.4-kW PV system on the Renaissance Commons affordable housing project, several miles away, which is opening soon. That left a 132.6-kW array on the PAE roof.
Risk Reducers
There were several risk reducers. The Energy Trust of Oregon and Oregon Dept. of Energy are providing substantial incentives for sustainable developments. “The city also helped with leeway on system development charges if we can prove our system has lower demand on the municipal systems,” says Schwer.
And PAE’s pre-lease of the upper three of four office floors, and a strong market for office space in Portland helped. The core group doesn’t expect that to change much, even with COVID-19 uncertainty.
“It seemed we had many brushes with death,” associated with the budget.
– Paul Schwer, President, PAE Consulting Engineers
The project is Portland’s first Living Building. City permits took nearly nine months, three months longer than projected. Sloop estimates a permit for a standard 58,000-sq-ft building would take four to six months.
One reason is the number of appeals. One involved the elimination of a required green roof, mostly because roof rainwater will be diverted to a 71,000-gallon cistern and never flow into city sewers.
The city is allowing composting because there is a backup connection to sewers. “A building like this is great for everybody, for it is showing people possibilities,” says Terry Whitehill, the city’s building official.
As soon as the city permit was issued on April 1, the developer got its bank loan, at a low rate of 2.82%. The investment rate of return is expected to be in the range of 8% to 10% for a 10-year investment, before counting the beneficial tax impact of the Opportunity Zone.
“Now that we have proven the concept is commercially viable and, we believe, replicable under the right circumstances, we hope Living Buildings will not need to be funded with the building team at risk,” says Marc C. Brune, a PAE partner.
The team still has a long way to go to cross the Living finish line, which includes a year of proving the performance of the building after it is fully occupied.
“Wearing two hats changed our perspective about design decisions.”
– Kathy Berg, Principal, ZGF Architects
For starters, there are outstanding state permits, including for the rainwater-to-potable water system from the state Dept. of Health and the composting system from the Dept. of Environmental Quality. “We do not yet know what the requirements from DOH will be for the potable rainwater system,” says Brune.
No city permit is required for the fertilizer-from-urine system, says Whitehill.
AmmPhotek’s steam distillation process produces high-ammonia distillate, known as liquid fertilizer, and a powder of magnesium ammonium phosphate, known as powdered fertilizer. AEM tested the system at a wastewater treatment plant at the University of California, Davis.
The PAE fertilizer system reduced the number of composters needed by 20%. It is expected to divert 9,400 gallons of urine per year. The estimated market value of the liquid fertilizer is over $50,000 per year and the 400 lb of powdered fertilizer’s market value is about $1,000 per year.
The PAE team has not yet decided how to use the fertilizer. It might sell it to local nurseries or growers, give it to tenants for their edible plants or give it to the fertilizer system’s operator as compensation.
Currently, only the urinals feed the system. But AEM is working to design urinals for women, because urine is a terrible thing to waste.
“This project has a lot more inherent risk because it has not been done a thousand times.”
– Ed Sloop, chief estimator, Walsh Construction Co./OR
The building’s resilient structure, which is designed to last 500 years, followed the prescriptive code for seismic Risk Category (RC) IV structures rather than RC II, which is the minimum required for office buildings. No special approval was needed, says Anne Monnier, the principal for KPFF Portland Structural.
Though KPFF declined to invest in the project, Monnier still says the job “has not been an easy one to pull off from many angles.”
As designed, the rectilinear hybrid structure consists of a shear wall concrete core to resist lateral loads and a mass timber frame for gravity loads. The frame is made of Forest Stewardship Council-certified wood, which ensures sustainable timber growing and harvesting practices. Though considered more sustainable than steel or concrete, timber costs about $100,000 more than steel and $640,000 more than concrete, says Walsh’s Sloop.
Floors have a 3.5-in.-thick topping slab placed on five-ply cross-laminated timber panels, spanning 15 ft to glue-laminated beams. The slab acts as a diaphragm to connect the wood-floor framing to the shear walls. The beams span 32 ft and are supported on interior glulam columns and perimeter columns.
“We are taking the pee out of PAE.”
– Kathy Berg, Principal, ZGF Architects
The topping slab doubles as a radiant floor for heating and cooling. There are plywood-covered gaps between slab sections for horizontal chases for MEP distribution. “A big part of the design is the integration of the MEP and the structure,” says Monnier.
RC IV frames, required for essential facilities, such as hospitals and fire stations, resist seismic forces that are 50% higher compared to RC II frames. They do this because they are stiffer—mostly accomplished through more reinforcing steel and thicker core walls. The building “really thinks it is a hospital,” says Monnier.
The 115-ft x 95-ft building, 75 ft tall, will take up one quarter of a block. Walsh did 10 estimates to refine hoisting, site logistics, the concrete foundation, excavation plans and more to “find the sweet spot between cost and constructibility,” says Sloop.
Work began April 1 during the height of the COVID-19 pandemic, and though Portland construction continued, Walsh has had to follow CDC guidelines that mandate 6 ft of space between workers. To date that has been simple, with fewer than 12 workers on site.
“We are decentralizing fertilizer production. How game-changing is this?”
– Pete Munoz, Practice Lead, Biohabitats
When safe distances cannot be maintained, workers wear personal protective equipment. There have been no cases of COVID-19 among workers. If there is one, the site must shut down for two weeks.
Work has been challenging, aside from COVID-19 precautions that slow the pace a bit. Unanticipated contaminated soil meant redoing excavation plans to minimize dirt removal and in turn minimize the expense of disposal at an approved dump. “We made as small a footprint in the ground as possible,” says Sloop.
The building has no basement. Instead, it has two foundation levels. The lower level has a 3,100-sq-ft structural concrete mat under the core that sits 5 ft below the first floor. The slab of the 1,600-sq-ft cistern sits 8 ft below the lobby floor. The upper level has continuous perimeter footings and pier footings below column lines. The concrete cistern changed shape four times to get it to fit around the foundations, says Sloop.
“Now that we have proven the concept is commercially viable and, we believe, replicable under the right circumstances, we hope Living Buildings will not need to be funded with the building team at risk.”
– Marc C. Brune, Partner, PAE Consulting Engineers
By summer’s end, Sloop expects crews to top out the core. “We’ll begin flying wood in the fall,” he says.
Though busy with other demands, PAE’s Schwer has not forgotten about structural resilience for Portland’s future office buildings. He’s planning to remake his pitch for grants, ahead of the next budget cycle.
After the PAE building is occupied, Schwer expects to give tours to city officials before re-pitching the virtual rent idea. He will make the point that if a quake shakes things up during the summer months, the building will be able to function for 100 days without using any city utilities. “I haven’t given up on better structural resilience,” Schwer says. “For now, I’m just trying to get the project built.”