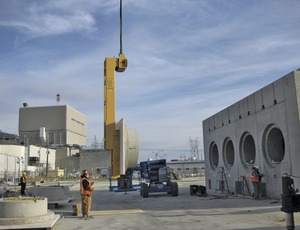

As the 21st century dawned, "nuclear renaissance" was a popular catchphrase. But current trends suggest that renaissance, if it occurs, will be in the market for engineers and contractors providing services to decommission nuclear powerplants and build storage for their spent fuel. In 2000, 104 power reactors were operating in the U.S., and new growth beckoned. In 2013, four of that fleet were retired, and a fifth will close this year. Five new reactors are now in construction, but there are none behind them. And the number of operating power reactors has slipped to 100.
Decommissioning is years in the future, but plant owners are investing now in dry-cask storage for spent fuel. "It's the country's only recession-proof business," says Rod McCullum, director of used-fuel programs at the Nuclear Energy Institute. There are 63 separately licensed facilities for storing spent fuel in the U.S., and many expansions are under way, he says.
The original plan entailed storing spent fuel in deep pools at powerplants until it could be sent for reprocessing. But since 1977, U.S. policy has banned reprocessing to forestall nuclear proliferation. As pools reached capacity, plants built dry-cask systems for long-term temporary storage.
The size of dry-storage facilities constructed in the early 1990s was based on the assumption the Dept. of Energy would begin accepting spent fuel for permanent disposal in 1998, says Wes Jacobs, a nuclear project manager for Black & Veatch. Sites are expanding their dry storage now because that assumption was wrong, he says. Following the 2012 recommendation of a blue-ribbon commission, DOE's goal now is to complete, by 2025, a consolidated interim storage facility to receive fuel from dry storage sites around the country and, by 2048, a permanent spent-fuel geologic repository.
"Right now, we see people expanding existing pads," says Bob Fraser, president of ArevaDZ, a joint venture of Areva, Lynchburg, Va., and Day & Zimmermann, Philadelphia, that engineers and constructs dry storage. The top reason for the market's vitality is the unavailability of the Yucca Mountain deep geologic repository, which was being prepared in Nevada for permanent disposal of spent nuclear fuel, says Fraser. Close behind is plant relicensing, because extending a plant's operating life will lead to continuing production of spent fuel, he says. The Obama administration ordered work terminated on the Yucca Mountain project in 2010 because of huge cost and schedule overruns and intense political opposition in Nevada.
Three companies are the leaders in supplying the dry-cask storage market, but all of them provide concrete- based, multipurpose—that is, storage and transport—systems and sit on a concrete pad, says Juan Subiry, marketing vice president for one of the suppliers, NAC International. NAC's MAGNASTOR was the first licensed ultra-high capacity, multipurpose system on the market currently deployed and still stores more fuel bundles in a canister than other systems with the same footprint, he says.
Areva TN's NUHOMS system uses horizontal storage and offers the highest seismic performance in the U.S., says Jayant Bondre, vice president and chief operating officer.
Holtec International's HI-STORM's basket is made of proprietary neutron-absorbing material, says Pierre Oneid, vice president and chief nuclear officer.
"The reality is, no two plants are the same," says Subiry. "Each technology may have advantages or disadvantages because of the site."
Post a comment to this article
Report Abusive Comment