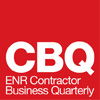
Working in concert with influential construction industry groups, the U.S. Army Corps of Engineers will release at the end of July new guidelines for the use of so-called "single-step design-build" on its projects.
Although the Corps first adopted design-build in the mid-90s, it has steadily increased use of the single-step process on major projects since 2008, despite heavy criticism from contractors and industry groups that fear it could spread to other large owners.
Critics argue that the single-step process defeats the collaborative purpose and creativity of design-build and say that it is expensive and counterproductive. They advocate instead for a two-step system favored by the Design Build Institute of America, Associated General Contractors of America and the American Council of Engineering Cos., among others.
Two-step—or two-phase—design-build first calls for teams to submit a statement of qualifications. Based on that information, the owner develops a short list of three to five teams that submit detailed designs for the project. Single-step combines those phases without short-listing first, often leaving a dozen or more proposers to offer designs. The lack of a short list means that firms spend significant time and resources on competing designs with a much smaller chance of winning the project.
"We do recognize the difficulties of single-step for proposers," says George Lea Jr., the Corps' chief of military engineering construction in Washington, D.C. "Single-step is not our preferred strategy, and it has never reached the same level of use here as two-step, but we believe single-step does save time, and that's important when you have a large volume of projects to get done."
However, Lea admits that the Corps has not collected enough data to clearly document the time savings and insists that the use of more single-step proposals is not about lowering costs for the government. He declined to reveal details of the new guidelines—officially called "Limitations on the Use of One-Step Procedures for Design-Build"—because they had not been fully approved by the Corps' contracting division.
What is clear is that the added expense of single-step competitions—with some firms saying they've spent hundreds of thousands of dollars per year on proposal expenses alone—is keeping many contractors and designers from competing on single-step jobs altogether.
"It would have to be a pretty unique situation before we'd get involved in a single-step process now," says Bob Nartonis, a senior vice president with the Minneapolis office of Mortenson Construction.
Nartonis, who is also the current national chairman of DBIA, says single-step design-build can penalize teams for small mistakes on qualifications statements after they've already spent money on a design. "That's counterproductive," he adds.
Greg Gidez agrees. He's the director of preconstruction services for Hensel Phelps Construction Co., Greeley, Colo., and a past national chairman of DBIA. "We want to be able to compete on a fair basis and provide the best value, but single-step drains the system," Gidez says. "The danger of single-step is when you submit both credentials and a proposal, but you can be disqualified for a small mistake before they even see your design. And that gets expensive."
Nartonis adds that the use of single-step also "stunts the creativity of the best talent in the industry" because most designers and trades can't afford to price their work for several teams at once.
That happens when specialty contractors and designers end up on multiple teams competing for the same project, thus improving their chances to be on a winning team, but also stretching resources, diminishing their value and possibly creating ethical problems.
"In a small market, I may have to bid six different prices for six GCs on the same project," says Jim Dent, preconstruction manager with electrical contractor Weifield Group Contracting LLC, Denver. "That's expensive and renders me useless. A team with an electrical service designed too big for the job is locked in because the non-disclosure agreement says I can't do anything to correct it without hurting the other teams I'm on. All I can do is offer a price to them, and anybody can do that."
However, the Corps' Lea insists that firms can still showcase their skills in a single-step process. "Those who disagree do not represent the industry as a whole," he says. "That's just the perception of a vocal few."
But Dent says that single-step reduces design-build to "a low-bid scenario" and may cost owners more in change orders in the end. "The way the Corps is doing it now is untenable," he adds. "We land work by bringing more value to the table than the next guy. We don't do hard-bids, and this [single-step] is way too close to that."
Design Costs
Some firms are more willing to enter single-step competitions when stipends are offered to the losing teams to help compensate for design costs.
Post a comment to this article
Report Abusive Comment