Jack Wilson admits it: He welcomes the rising price of asphalt. It’s not a concrete bias—he is a 40-year contracting veteran who worked impartially with both asphalt and concrete. But now that asphalt milling and repaving is more expensive, he believes the time has finally come for his asphalt overlay invention to gain a wide audience.
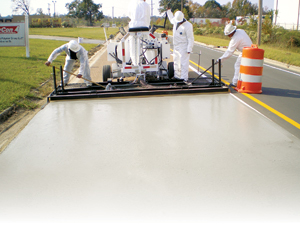
Wilson, president and chief executive officer of PolyCon Manufacturing, Madison, Miss., first developed his product, dubbed “E-Krete,” twelve years ago. The ⅛-in.-thick overlay is a light-colored, reflective, water-based polymer composite with cement and aggregate. It acts like a slurry when applied to asphalt pavement, filling in cracks and creating a nonbituminous seal that may preserve the existing road for up to 20 years with minimal maintenance.
“Years ago I was pouring post-tensioned slabs,” he recalls. “I used a thin coat of polymer cement, but it wouldn’t stay bonded to asphalt.” Typical asphalt binders deteriorate as the asphalt absorbs water. Wilson hired a chemist and spent the next year searching for the perfect blend. The result, he believes, could save road agencies millions of dollars in main tenance costs and carbon footprints.
James Kopf, former chief engineer for the Mississippi Dept. of Transportation, agreed to give the material a test. Ten years later, the pavement on three small bridges is as good as ever, he says. “It’s a radical approach to maintaining asphalt,” says Kopf, who now is vice president of PolyCon. “It arrests oxidation. It can bend, yet it’s high-strength; it won’t shatter.”
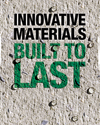
In 1998, the U.S. Army Corps of Engineers agreed to test E-Krete in the lab and at seven military naval and air stations. The subsequent report stated: “Overall, the E-Krete product would appear to be an excellent alternative to conventional coal tar fuel-resistant sealer.”
Reid Daws, operations manager for Tupelo Mississippi Regional Airport, agreed to try E-Krete nine years ago on a damaged taxiway. “We did a test patch and liked what we saw,” he says, so much that the airport won federal approval to use it on the entire length of the 6,500ft-long taxiway.
The E-Krete today “looks almost as good as when we put it down,” he adds. “There are some reflection cracks, and we will always have those. But no spalling. We still haven’t milled the taxiway.” Without it, “we would’ve done two mill-and-overlays on it by now.”
Rod Woullard, a member of the Forrest County Board of Supervisors in Mississippi, saw the Corps of Engineers report. “We tried it on three roads about two years ago,” he says. “It’s disappointing that asphalt is not lasting as long as it used to. You can’t put it down and not worry about it any more.” But the E-Krete application alleviates that problem. “If you have a good base, it works great,” Woullard says. “It’s costly, but the cost of asphalt has made it competitive. One mile of asphalt costs $110,000 to $115,000. Doing this costs less than $85,000.”
Placement is simple, requiring one truck, specialized equipment costing about $30,000, a crew of five and ideally temperatures between 50°F-100°F, says Wilson. Woullard concurs: “We got the equipment, and in two weeks my two guys could operate it better than Jack’s [Polycon] guys.”
The National Center For Asphalt Technology at Auburn University just completed an initial test that found favorable comparisons of E-Krete’s friction and surface durability under heavy loads with hot-mix asphalt. Nam Tran, one of the Auburn researchers, says the second three-year phase, to begin later this year, will study changes in durability over time.