First Aqueduct Tunnels Rehabilitation Project
San Diego
Best Project
Submitted by: Michels Corp.
Owner: San Diego County Water Authority
Lead Design Firm: Stantec
General Contractor: Michels Trenchless Inc.
When inspections discovered groundwater infiltration in three 72-in. aqueduct tunnels owned by the San Diego County Water Authority, a complex rehabilitation project became necessary. Those tunnels—Lilac Tunnel (500 ft), Red Mountain Tunnel (3,100 ft), and Oat Hills Tunnel (3,600 ft)—were originally built in 1947.
Addressing this infiltration was crucial to avoid affecting water quality and structural integrity of the pipes. As there were no viable alternatives to provide treated water to customers, the authority determined the aqueduct could only be shut down for repairs during three 10-day periods (240 hours) in the winter months. With these constraints, traditional rehabilitation methods for tunnels of this size were not feasible.
Instead, the team used geopolymer lining and FRP sliplining, minimizing waste, excavation and the project’s carbon footprint. The team also designed and fabricated a system to efficiently transfer material from the surface-level mixing station to the down-tunnel spraying assembly. This solution was crucial for the project, given the constrained storage space above ground and the even more limited space within the aqueduct tunnels.
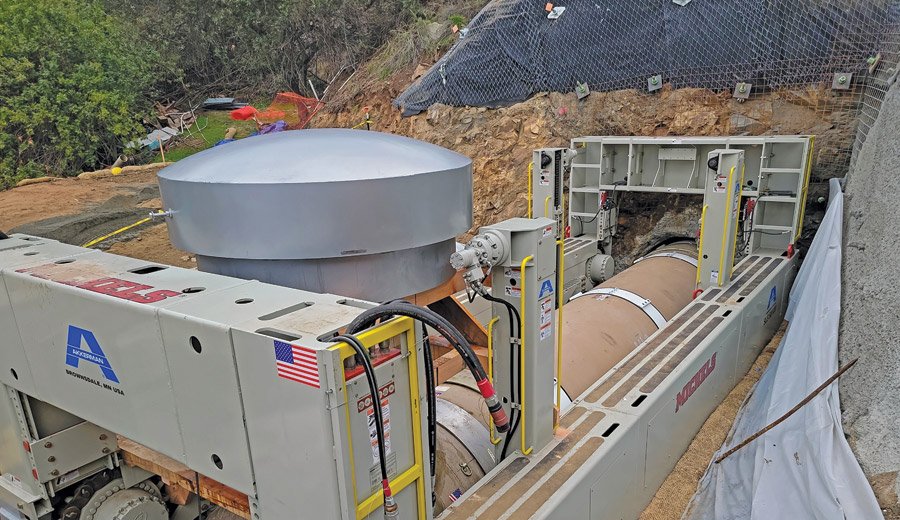
Photo courtesy Michels Trenchless
Geopolymer lining offered technical advantages such as extending the lifespan of each tunnel by more than 75 years, creating a watertight seal without needing to bond to the substrate and improving structural integrity by withstanding external pressures up to 90 ft. The installation process for geopolymer lining also minimized the downtime duration. After sealing and preparing the tunnels, the team installed more than 1 million lb of geopolymer liner over approximately 3,600 ft during the final two shutdown periods.
For the more deteriorated Oat Hill Tunnel, crews installed a 63-in. FRP sliplining. This approach provided a cost-effective solution due to FRP’s inherent corrosion resistance, lower material cost, faster installation and ability to meet performance standards without the need for concrete repair.
The project team set a new installation record for the longest and fastest large diameter (63 in.) FRP sliplining, having installed 3,600 linear ft in just seven days in May 2022.
Post a comment to this article
Report Abusive Comment