Inova Mount Vernon Hospital Behavioral Health Unit
Alexandria, Va.
BEST PROJECT
Submitted By: Gilbane Building Co.
Owner: Inova
Lead Design Firm: HKS Inc.
General Contractor: Gilbane Building Co.
Structural Engineer: Cagley and Associates Inc.
MEP Engineer: WSP
Subcontractors: VarcoMac Electrical Construction; Reliant Drywall; Miller Paneling Specialties; BION; Full Service Glass
This 20,000-sq-ft renovation of a 1970s-era building required closely managing surrounding areas to avoid disrupting patients and hospital staff. The project team relied on complex phasing plans and careful coordination to achieve those goals for the new wing, which included architectural, mechanical, plumbing and pneumatics improvements.
The new wing adds 20 inpatient behavioral health beds, increasing the hospital’s capacity by 67%. There are rooms for privacy, TV, laundry, group therapy and a courtroom where patients can meet with their attorneys.
Safety upgrades for the hospital include impact-resistant windows and drywall, anti-barricade doors and anti-ligature fixtures designed to prevent patients from self- harm or suicide. To achieve these safety design features, the team closely reviewed drawings to be sure ligature points were not included.
Because Virginia does not currently have any specifications for behavioral health facilities, the team chose to follow New York State Office of Mental Health standards to be sure the facility meets any standards that may be implemented in the future.
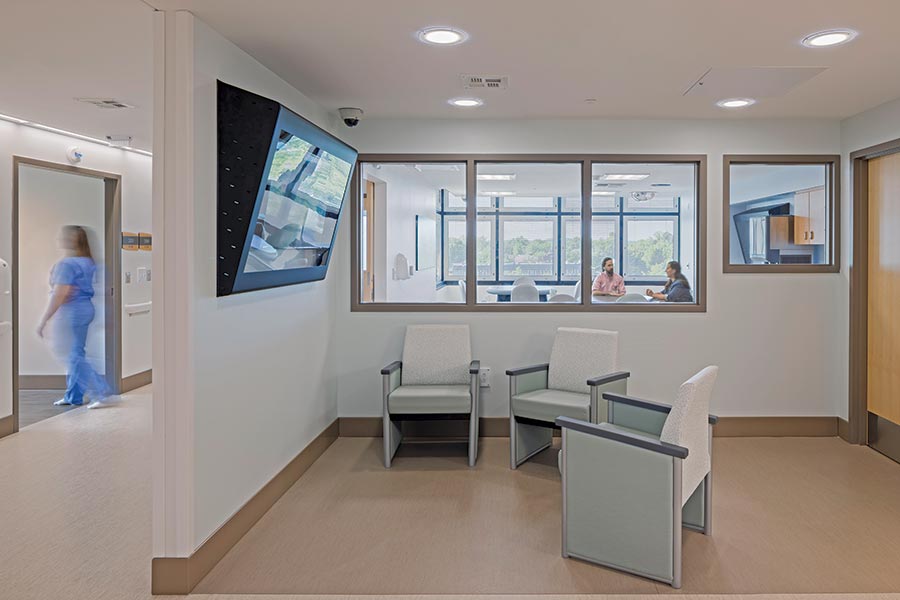
Photo by Evan Thomas, courtesy of Gilbane Building Co.
Another renovation to create a long-term, acute-care unit at the hospital took place on the floor above this project, adding yet more complexity.
This project, completed at budget and on schedule, comes as Northern Virginia has experienced increasing need for behavioral health services. Inova Emergency Departments are caring for nearly 1,200 residents in need of behavioral health services monthly.
Earlier refurbishments and additions to the building created challenges. In one area, the building exterior was left inside when the addition was added. For this area, the team used a Brokk demolition robot one weekend to demolish 60 linear ft of exterior facade inside the space, allowing the operator to accomplish more in less time from a safe distance. That avoided the risk of noisy and possibly dangerous interior demolition work.
For demolition ductwork, trades were restricted from using sawzalls because they create noisy vibration on metal.
Post a comment to this article
Report Abusive Comment