The recipe for success in the construction industry has a very long list of ingredients, but for McCarthy Building Cos. California, none of those is more important than relationships. With 40 years of relationship building in California, McCarthy says approximately 85% of its regional projects come from repeat customers.
According to Mike Myers, president of McCarthy’s southern Pacific region, the firm’s high rate of return business can be summed up in a word: “certainty.”
“There’s a lot of great contractors in California,” says Myers, a 22-year McCarthy veteran. “But I think the reason we get repeat work is that [our clients] trust we’re going to deliver on our promises. They know what they get when they hire us, and they know what to expect.”
The proof of the company’s approach can be seen in the bottom line. McCarthy’s California regional revenue of $2.3 billion in 2022 was a third more than in 2021.
In recognition of the company’s recent achievements, ENR has named McCarthy California Contractor of the Year. ENR editors recognized the company’s innovation in the areas of virtual design and construction, its integration of the latest technology with preconstruction services and its utilization of prefabrication and modular construction on projects.
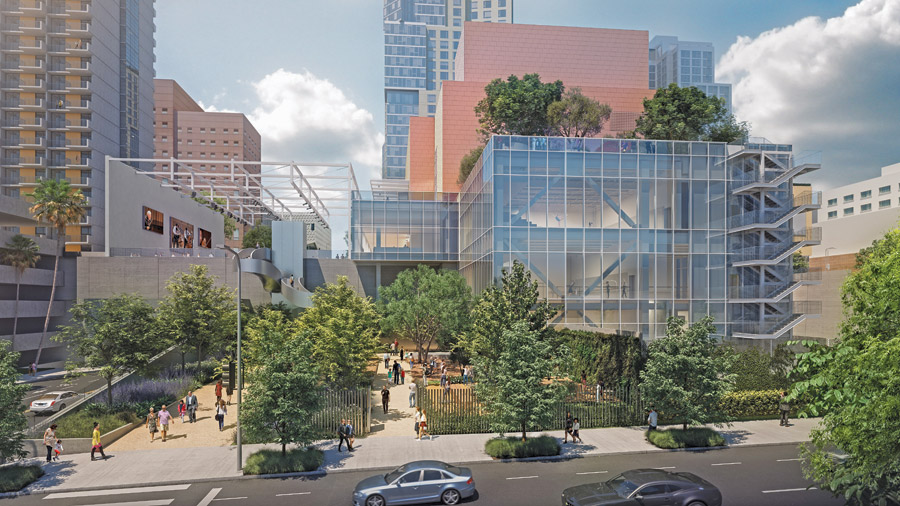
The 100,000-sq-ft campus expansion to the Colburn School in downtown Los Angeles was designed by Frank Gehry.
Rendering courtesy Gehry Partners LLP.
Regional Reliability
The firm’s California operations boast a large portfolio, with a strong presence in the health care, commercial and education markets. Company leaders say their ability to diversify across various markets and their reliance on technology to enhance productivity were part of a recipe to meet the needs of a fast-growing region.
“[In California] you’ve got a healthy market and a diverse marketplace to be in,” says Shaun Sleeth, president of the northern Pacific region. “There’s been a robust need for the types of buildings we build.”
“If one market is falling down, we are able to flex into a different market space that is on the rise.”
— Shaun Sleeth, Northern Pacific Region President, McCarthy
Some of the McCarthy’s recent projects include Loma Linda Medical Center’s Campus Transformation project—ENR California’s 2002 Best Project in the health care category—Skechers’ Corporate Headquarters in Manhattan Beach and two student housing projects for California State University in Los Angeles and Long Beach.
McCarthy has myriad projects in development, including marquee undertakings like UC Davis Health Center’s $3.7-billion state-of-the-art California Tower in Sacramento; the $300-million, 14-acre expansion of Gilead Science’s pharmaceutical manufacturing facility in Oceanside; construction of the Frank Gehry designed Colburn Center, a 100,000-sq-ft campus expansion of the renowned Colburn School in downtown Los Angeles; and the renovation of the architecturally significant Gregory Bateson Building in Sacramento.
“Our diversity within the market space has helped a lot,” says Sleeth, a 19-year McCarthy veteran. “If one market is falling down, we are able to flex into a different market space that is on the rise.”
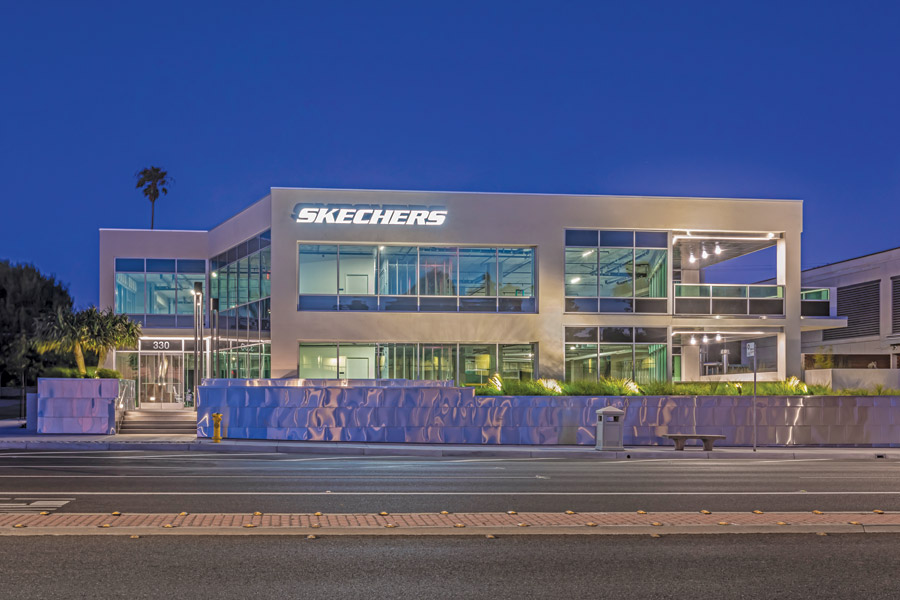
The $150-million Skechers Manhattan Beach campus will be LEED Gold certified.
Photo Courtesy McCarthy Building Cos.
Building California
Flexibility has been a hallmark of McCarthy since its earliest days. Founded in 1864 by Irish immigrant Timothy McCarthy, what started as a lumber business building barns and farmhouses in Ann Arbor, Mich., has grown into one of the largest and most diversified commercial construction firms in the U.S. Its parent company, McCarthy Holdings Inc., is ranked 19th on ENR’s 2023 Top 400 Contractors list with a reported 6,535 employees and $4.4. billion in revenue.
The company opened its first California office in Newport Beach in 1984 and has since grown to include six additional offices within the region: Sacramento, San Francisco, San Diego, San Jose, Los Angeles and Las Vegas. McCarthy’s California region currently has 1,136 full-time employees.
Scripps Health’s Timothy Jacoby has high expectations when working with McCarthy. “Quite simply, they are excellent constructors that excel in the very difficult California hospital construction market,” he says.
The San Diego-area integrated health system has been working with McCarthy for almost 15 years. Its latest project, the $664-million La Jolla Campus Tower II, a 430,000-sq-ft, 200-bed acute care hospital, is scheduled for completion in November 2024.
Jacoby praises McCarthy’s dynamic development of the project’s master plan as well as the firm’s enthusiasm to create the best and most efficient plans to support Scripps Health’s long-term strategic growth. “Having fully engaged, knowledgeable and passionate design and construction partners is invaluable,” says Jacoby.
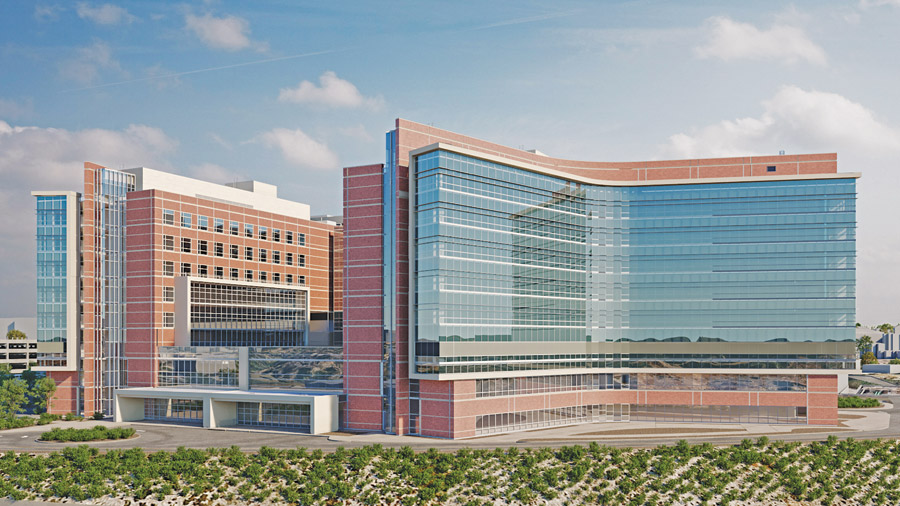
Scripps La Jolla Tower II is a 433,000-sq-ft building that’s part of a complete hospital with 171 beds scheduled to open in 2024.
Rendering courtesy HGA Architects & Engineers
Enhancing Productivity
For more than a decade, McCarthy has been at the forefront of adopting and implementing leading-edge construction technologies like virtual design to enhance project visualization and coordination. From concept to execution, McCarthy employs building information modeling (BIM) on all of its projects. According to Myers, having a BIM-enabled workforce improves project accuracy, speeds up the construction process and enhances collaboration.
“We do a lot of design-build work, but even when we don’t, we make sure we manage the virtual model,” he says.
Although not a new technology, Myers states that McCarthy’s successful use of BIM is a matter of investment as well as making sure all of a project’s stakeholders have access to the technology.
“We do all the modeling in advance to make sure the details are in the field work,” says Myers. “Then we give our craft workforce and trade partners those same tools and technology to execute in the field. They’re able to pull up the drawing, see it in three dimensions and are able to convert and construct the products.”
McCarthy has also been adept at integrating the latest technology with preconstruction services. Rather than creating its own products, McCarthy has been developing a virtual marketplace for its partners and vendors to have easy access to the vast array of the world’s prefabricated construction products. OFFPRO®, short for offsite products, is an ambitious project in which Myers says McCarthy has been making a heavy investment. “We have tasked ourselves to be the best consumers of prefabricated products,” says Myers in regard to the effort.
Myers thinks of it as “Amazon, but for prefabricated products. We’re creating a tool and a platform that all of our partners can utilize, to search up the most relevant prefabrication product for their design or their project.”
Myers believes OFFPRO® will help McCarthy effectively dovetail prefabrication into preconstruction. “We tie that product into our pre-con services to make sure that we’re bringing all those options forward to our design partners to [help] our clients make good selections early on,” says Myers.
Prioritizing People
For most of its history, McCarthy was a family-owned business. That changed in 2002 when the company became 100% employee owned.
“It’s a very well-balanced ESOP program, says Myers. “We treat our partners like owners. We treat each other like owners, and we all carry our weight.”
According to Myers, no employee owns more than a half-percent of the company.
Sleeth adds that pride in being an employee owner transmits to how the McCarthy team performs in the field. “I think it drives our commitment to our projects, our communities and our clients,” Sleeth says. “Our motivation to live and work in the communities and represent the McCarthy brand is really important to us. I think that resonates with our clients.”
“We don’t just build things. We want to make sure we are actively involved in charities and industry organiza-tions”
—Mike Myers, Southern Pacific Region President McCarthy
Myers and Sleeth both stress that McCarthy’s commitment to the community is integral throughout all of the company’s operations.
“We don’t just build things,” says Myers. “We want to make sure we are actively involved in charities and industry organizations.”
McCarthy takes an active role in supporting the communities where its employees live and work while addressing one of the industry’s primary challenges— how to build and sustain a qualified craft professional workforce.
In an effort to address the issue, McCarthy supports outreach programs like the Santa Clara County Construction Careers Association (S4CA) and Capitol College and Career Academy, a public charter high school in Sacramento that trains students for careers in the construction industry.
“Introducing these young kids to a viable and fulfilling career is important,” says Sleeth. “This is where building our community meets building our industry.”
Other efforts include McCarthy’s Partnership for Women designed to support women within the organization, giving them opportunities to succeed while working at McCarthy.
Myers also notes that McCarthy consistently goes beyond its target of contracting with 25% of its suppliers from diverse communities.
“We have dedicated staff attracting diverse communities into our subcontractor pool, and we keep trying to increase that goal,” Myers says. “We keep pushing the limits to do better.”
Post a comment to this article
Report Abusive Comment