Facing inflation, material shortages, skilled labor shortages, fuel escalation, bidding uncertainties and the onset of project labor agreements (PLAs) and a possible recession, subcontractors in the three-state region of Arizona, Nevada and New Mexico continue to fight on many fronts for pre-pandemic normalcy.
“Our members did very well in 2021. Our industry was deemed essential and everyone continued to work,” says Jim Garcia, executive director of the Associated Contractors of New Mexico. “None of our 119 members left the group.”
Related Link:
ENR Southwest 2022 Top Specialty Contractors
But conditions are “bad now,” he adds. “We’re coming off fuel-escalation negotiations and entering full-scale materials shortages in things like steel, bridge supplies and finish materials. In addition, Buy America measures are in the long term good, but this is not a good time to implement them, so we support a waiver.”
Additionally, PLAs are challenging companies to remain competitive in quality while raising the price of public works projects 14% to 16%. “It couldn’t be a worse time to introduce PLAs. It takes out the smaller prime contractors, mandates expensive compliance controls and increases the price of the projects to the consumers,” he says.
Because of inflation, continuing issues with labor and materials delays, Garcia notes, “It’s going to be a bumpy road [ahead].”
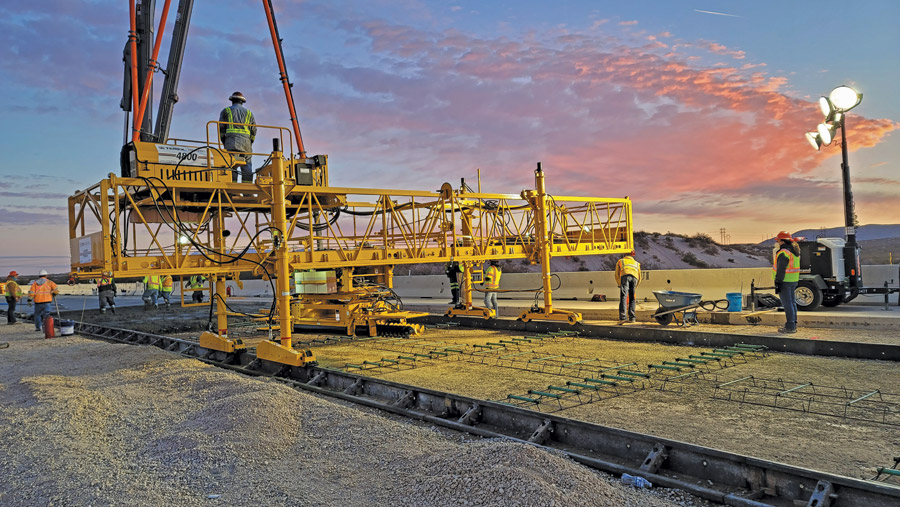
Crews with contractor AUI Inc. at work on a paving project in Anthony, N.M.
Photo by Jonathan Wasson
Coming Off a Good Year
In 2021, Arizona specialty contractors did “quite well, all things considered. Arizona has continued to grow, and many of the skilled-trades companies in our membership have an impressive backlog of work built up,” says Josh Umar, executive director of the American Subcontractors Association (ASA) of Arizona, with 215 members, mostly in the Phoenix area.
From 2021 through today, single-family and multifamily have been very strong as well as warehousing and industrial tech/microchip, electric vehicle, health care and heavy civil, including the Broadway Curve I-10 megacontract in Phoenix, Umar says.
The market is “positive. However, we do predict some slowdowns in both the housing market and new non-tenant-improvement office construction,” Umar says. “We expect that the Arizona market will remain strong and buoy us a bit in comparison with other parts of the U.S. because of remaining high demand in several sectors and a population that is rapidly growing.”
Jennifer Roberts, president of A-1 Masonry in Las Vegas, says that the past year has been one of the company’s strongest. Working only in Nevada, the company reported revenue of $8 million in 2021, up 14% from $7 million in 2020. “Some projects were placed on hold or delayed during COVID. We adjusted, came back strong with accelerated schedules,” she says. “We continue to see strong demand but expect some softening with the slowdown in housing locally.”
In Reno, Craig Madole, CEO of the Nevada Chapter AGC, says that in 2021, most specialty contractors were busy and able to choose which projects to bid “to ensure they were a good fit for the job. But inflation, raising fuel prices and supply chain shortages impacted their profitability and ability to make schedules.” The chapter serves 300 members north of Tonopah.
But now, many subcontractors are still seeing project delays that are “not necessarily due to their own performance and maintaining schedules to deliver the work they are under contract for,” he adds. “They are still struggling with high fuel prices and lack of materials availability.”
Meanwhile, Brandon Stephens, operations manager for Rosendin Electric, says that from a work-opportunity perspective, 2021 and 2022 have been “extremely strong. However, the lack of skilled labor in this market makes project pursuit/selection a bit more complex.”
The company reported a drop in year-to-year regional revenue to $278.82 million in 2021 from $381.44 million in 2020, attributable to a few delayed projects. Stephens notes the company’s regional backlog “is still at record levels and we have a number of very large, multiphase projects that started or will start this year.”
Particularly strong are data centers, energy and semiconductor-related projects. These have “immense tailwinds that will drive significant growth in this region for a number of years,” he says. Among these are the $129-million Townsite Solar + Storage in Boulder City, Nev., the first renewable energy facility in the state to use a Tesla battery energy-storage system, Stephens notes.
Commercial Roofers Inc., a roofing and waterproofing contractor in the Las Vegas Valley, has performed well despite reporting a 26% year-to-year reduction in regional revenue to $30.76 million in 2021 from $41.36 million in 2020.
“Within the Nevada market, the construction industry has not really started to slow down yet from what we can see,” says Ashley S. Jager, marketing and business development director. “Our bidding and budgeting activities remain very robust.”
In 2022, Commercial Roofers has received almost three times the number of RFQs/ITBs on new construction projects, compared with January through August 2020.
As with other markets, the roofing industry continues to respond to raw materials shortages, delays, supply chain issues and unprecedented pricing increases for roofing materials, Jager says. “Prices for roofing materials and accessories have risen by an average of 50% in a just over a year, and lead times for materials have increased significantly,” she says. “Despite these challenges, our production and installation work remained extremely high during 2021 and continues currently in 2022, with a significant backlog of work well into 2024.”
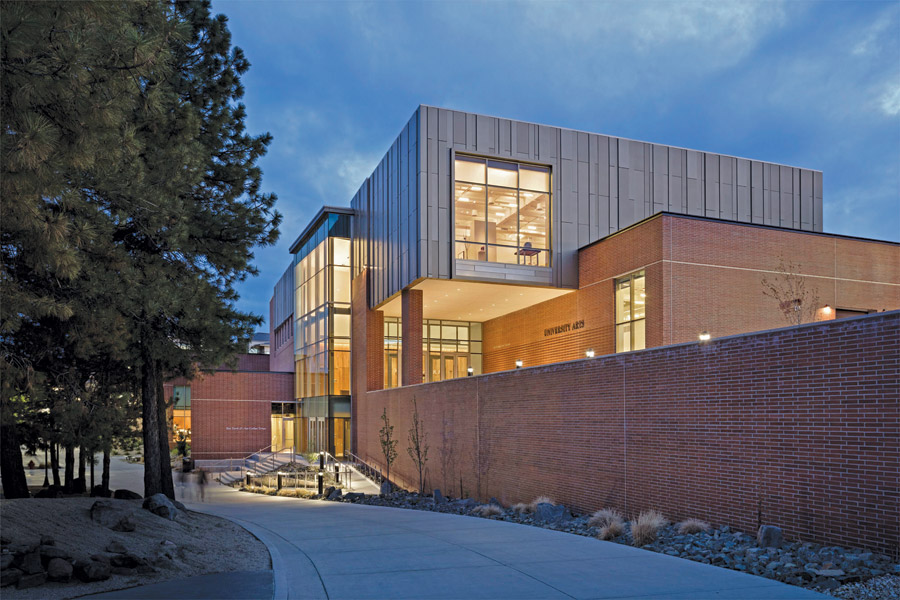
A-1 Masonry & Sandblasting completed the University Arts Building at the University of Nevada at Reno.
Photo courtesy of A-1 Masonry
Staring Down Uncertain Times
Negotiating price increases with general contractors and owners has also been challenging for subcontractors. “With some materials experiencing enormous volatility in pricing, such as PVC pipe, paint, lumber and steel, they were not able to hold their pricing very long and had to work to negotiate new pricing due to materials price changes,” Madole says. “At times, some materials were not available when a signed purchase order had been executed.”
Spectrum Mechanical and Plumbing has thrived regionally, reporting revenue of $43.4 million in 2021, an 83% increase from 2020’s $23.78 million. In response to the challenging market, the Phoenix-based company made a culture-shifting administrative change by promoting and bringing in Dave Mears IV from Nash Plumbing & Mechanical in Florida, says Rebecca James, vice president of communications at HB Global, the parent company of Spectrum and Nash.
Spectrum also acquired a local plumbing company, Nash Mechanical—not related to Nash Plumbing & Mechanical—to enhance its offerings and better serve its clients.
The firm is strengthening relationships with its best existing clients and reducing the breadth of offerings and focusing on core competencies of high-rise and multifamily construction. Spectrum has also begun to add work in the health care space, James says.
“It couldn’t be a worse time to introduce PLAs.”
—Jim Garcia, Executive Director, Associated Contractors of New Mexico
“Spectrum has maintained a consistent revenue stream throughout the year by bringing on special projects and securing projects that utilize both the mechanical and plumbing divisions. This has also allowed us to maintain a higher number of craft staffing with consistent employment instead of project-based hiring,” says Mears.
Arizona’s main issue has been unpredictability, says Umar. “Especially with regard to supplies and their prices, things were up in the air and fluctuating constantly. Our members weathered the storm by using the relationships they’ve built over many years in good times and bad.”
They have also adapted via education and collaboration, especially with industry partners and state safety officials at the Arizona Division of Occupational Safety and Health (ADOSH).
ASA is increasingly active in workforce development, partnering with Junior Achievement AZ, Build Your Future AZ and school systems to address long-term labor issues. “We are also offering education sessions to our members to help them learn how to recruit, develop and retain talent,” Umar says. “At least that way they can be armed with best practices and an understanding of what inspires young folks to join the trades.”
A-1 Masonry’s Roberts also stresses education. “I’m excited to see a strong resurgence of trade schools in general and the societal awareness that trades are excellent professions that provide opportunities for advancement, company ownership, if wanted, and a great income.”
She explains that labor remains a struggle but is encouraged by Nevada’s adoption of the Apprenticeship Utilization Act, requiring public works projects to use a percentage of apprentices. “We actively seek out employees who are interested in gaining more knowledge and learning the trade.”
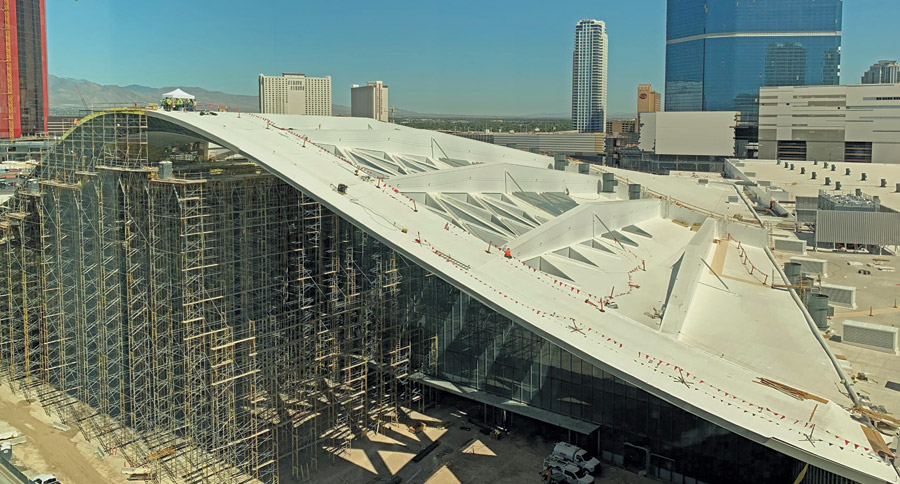
Commercial Roofers built the roof at the Las Vegas Convention Center.
Photo courtesy of Commercial Roofers Inc.
Recession Blues?
The market will likely slow down in northern Nevada during the next year or two, Madole says. But the University of Nevada continues to grow, the state has a successful funding mechanism for school construction and the Regional Transportation Commission also has an excellent funding system, with NDOT planning significant regional projects that will employ many people. “We are hopeful that while the economy may slow down, enough work will be available to prevent another 2008 market collapse,” he says.
“Even in the face of a recession, a guarded optimism remains widespread.”
—Josh Umar, Executive Director, American Subcontractors Association of Arizona
From Phoenix, Dick Roberts, ASA AZ’s president, notes that “the threat of recession has been over our head for the past several months, but our members learned some valuable lessons from the slowdown in 2007 to 2010. And I believe our state leaders have done a great job bringing in industry that is bringing in new workers from across the country, such as the multibillion-dollar [Taiwan Semiconductor Manufacturing Co.] chip factory. This is fueling the growth in residential housing and the infrastructure that goes with it.”
As a result, the metropolitan area expects continued growth. “The ability to keep working, adapt and build momentum on projects has set our members, and the state, up for continued progress even if a slowdown happens,” Umar says. “Even in the face of a recession, a guarded optimism remains widespread.”