CalPlant Rice Straw-Based MDF Manufacturing Plant
Willows, Calif.
BEST PROJECT, MANUFACTURING
KEY PLAYERS
OWNER: CalPlant I LLC
CONTRACTOR: Industrial Projects Consulting LLC
DESIGN FIRM | STRUCTURAL ENGINEER | CIVIL ENGINEER | MEP: Evergreen Engineering Inc.
The key new construction industry product resulted from a two-decade engineering push that culminated with a green manufacturing facility in Willows, Calif., a small town in the heart of the Sacramento Valley.
Related link: ENR California Best Projects 2021
(Subscription Required)
CalPlant now produces medium-density fiberboard (MDF) in a sustainable practice by turning post-harvest rice straw waste, with no added formaldehyde, into Eureka MDF, a board that matches the performance of traditional wood and can be used to make furniture, cabinetry, doors and moldings.
“We were never going to give up,” says Jerry Uhland, president and CalPlant founder. “I was a rice farmer; my partner—the Boyd family—was in the farming business. We saw there had to be something you could use this rice straw for.”
Getting the project to where it is now—producing 600 truckloads of MDF by September 2021—required decades of engineering work, financing guarantees for the $400-million project and a four-year construction project to build the manufacturing plant, which sits on 276 acres in an area that produces 20% of the country’s rice. CalPlant sources its rice straw from within an average 25-mile radius, providing a local benefit in both jobs and a sustainable way of replenishing local fields.
“This is a farming community, and we have unbelievable support from local agencies and the community at large for this to be built,” Uhland says.
The first steps were engineering and financing. The process for converting the rice straw to MDF isn’t all that dissimilar to that of creating a wood-based product. California law bans the burning of leftover rice stalks after harvest, so flooding the fields and letting rice rot was the only way to prepare a field for future planting. Instead, CalPlant takes the waste rice straw.
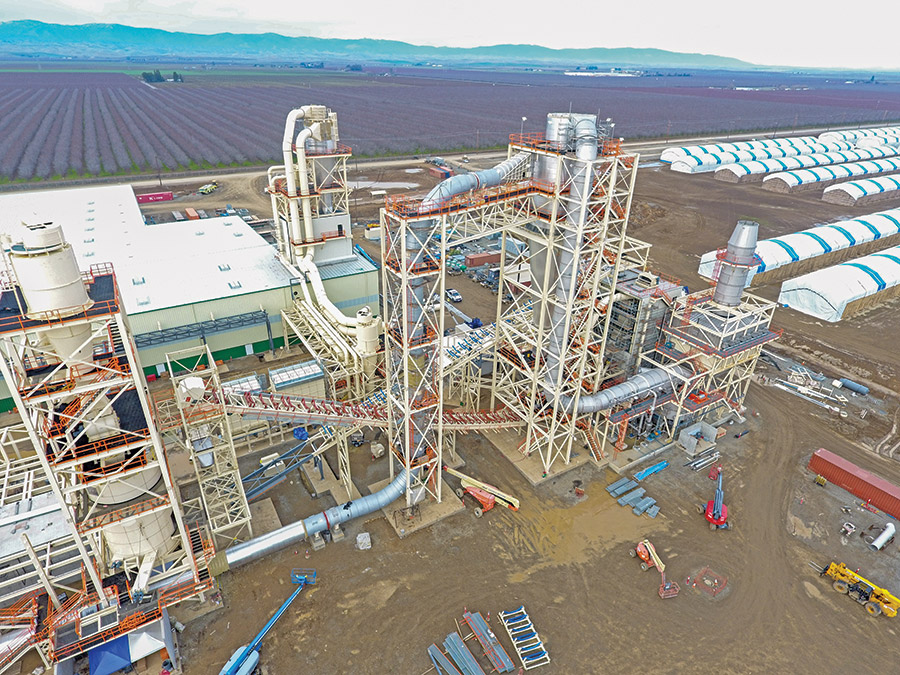
The engineering required a change midway through to reduce the main tower’s height due to FAA regulations. The construction wasn’t dissimilar to that of a traditional MDF plant, but the processes inside the plant required unique engineering.
Photo courtesy Industrial Projects Consulting
The straw bails, weighing on average 1,100 lb each, require the same machines as a wood plant, but with a different steam pressure in the refining process to fully saturate the 3-ft-tall hollow stalks and explode them into fiber bundles in about 15 seconds. From there, the cotton candy-like individual fibers act the same as typical wood-based MDF fibers, leading to the creation of MDF boards that Uhland says have performed in the marketplace on par or better than traditional MDF.
CalPlant says that at the microscopic level, curled rice straw fibers provide Eureka MDF with dimensional stability and strength, and the fiber refining process turns the waste material into an environmentally conscious product. Also, because of the renewable and abundant nature of the rice straw, not only is the product sustainable, it also removes waste straw from the rice fields that would otherwise need to be flooded in the winter, thus conserving water and reducing the methane emissions that rotting rice straw produces.
To help with both the engineering and the financing, German engineering firm Siempelkamp guaranteed lenders the volume and quality of MDF boards while Columbia Forest Products, also an equity partner, guaranteed the sale of the boards at a minimum price for 20 years. And in such a competitive market, the boards have been performing well. “If we can make it faster, they would be buying it faster,” Uhland says.
The first two hurdles of engineering and financing took more than 20 years, but Uhland says “construction was even tougher.”
Early on, the original contractor’s role was greatly diminished, and Industrial Projects Consulting took over as the construction manager on the plant, hiring all contractors and material suppliers to complete the project, all while working hand-in-hand with the owners, Siempelkamp and Oregon-based Evergreen Engineering.
Then came the next major issue: an FFA agreement on height of the plant changed, compelling a 100-ft reduction in the height of the plant’s main tower.
“It required a pretty significant redesign effort midway to reduce the height,” says Larry Persinger, owner of Industrial Projects Consulting. “It was a dramatic redesign that required a pretty herculean effort by Siempelkamp, Evergreen and CalPlant to make that all work.”
Gordon Yutzy, Evergreen Engineering president, says learning about the height changes was quite the surprise. For the fix, they created two shorter structures instead of one taller tower.
Persinger called it “quite a little glitch,” and it had an impact on the construction schedule. “We were scrambling trying to keep the contractors on site busy and productive,” he says. “It was a challenge for all parties.”

German engineering firm Siempelkamp devised the process for converting rice straw to MDF. A steam pressure refining process saturates the 3-ft-tall, hollow stalks and explodes them into fiber bundles in seconds.
Photo courtesy Industrial Projects Consulting
Another major difference in building an MDF plant for rice requires a complete rethinking of raw materials, from the need for ample year-round storage of nearly 300,000 tons of rice straw to handling the six-week influx of trucks bringing in the highly flammable product. A large majority of the site is taken up with storage, leaving just 25 acres for the actual manufacturing plant.
The MDF plant features steel, some sourced locally and some in Europe. This necessitated intense coordination between Evergreen and Siempelkamp. Early on, Evergreen helped the owners understand the raw material needs and then provided structural steel, electrical and mechanical system engineering outside of the main process equipment after Siempelkamp joined the equation.
“We have done refiner systems a number of times, and it is virtually the same equipment, but the inners are different,” Yutzy says. “With a new process there is lots of testing.”
Persinger says that Evergreen also was responsible for ensuring that all the Siempelkamp drawings met U.S. codes and matched up with onsite systems. “The whole design coordination was ongoing and sometimes a difficult part of the project,” he says. “We led the parade on the coordination, but getting the coordination done was a big deal.”
The $20-million hot press built by Siempelkamp is 10 ft wide, 117 ft long and uses more than 1,000 individual parts while operating at 400 degrees Fahrenheit. It produces MDF at a rate of 300 ft per minute. At full capacity, the plant will produce more than 150 million sq ft of MDF annually and use 280,000 tons of rice straw.
Uhland says that with his two-decade-plus perseverance getting CalPlant up and running, he now knows what he needs for a second plant. Persinger was impressed with Uhland every step of the way.
“I’ve been doing this for very nearly 50 years and have never come close to seeing the tenacity this guy has,” he says. “And he is a rice farmer who raised $400 million for this. He was really driven by helping the farming community he came from and then created a very green product. In all the projects we’ve done, we look at this thing and go, ‘this is the best overall, best all-around good project we have ever been involved in.’”
Post a comment to this article
Report Abusive Comment