ENR's 2024 Top 400 Contractors: Firms Feel Pinch for Profitability
May 22, 2024
ENR's 2024 Top 400 Contractors: Firms Feel Pinch for Profitability
May 22, 2024Emery Sapp, in a joint venture with Ames, is working on the $570-million US69 project in Kansas—the state's first-ever express lanes project, the firm says.
Photo courtesy of Emery Sapp & Sons
Related Links:
ENR 2024 Top 400 Contractor Rankings
2024 Top 400 Contractors | Full PDF
(Subscription Required)
When the Federal Reserve hiked interest rates 11 times last year in a bid to control rampant economic inflation, many Top 400 Contractors said they felt those policy changes in the form of project delays, rescopes or outright cancellations. Now, with construction costs at a prolonged high, firms say preconstruction has helped some would-be paused projects stay viable. But in a construction market where demand for resources far outpaces supply, firms say preconstruction has its limits against inflation.
“We believe the economy overall is more robust than the fed anticipated, and we don’t expect significant interest rate reductions this year,” says Anthony Johnson, Clayco executive vice president and president of the contractor’s Industrial Business Unit. The firm is ranked No. 23 on this year’s list.
For a second consecutive year, Top 400 revenue has increased by a double-digit percentage, rising 13.9% to $556.9 billion, from $488.98 billion last year. Median firm revenue is also up 10.9%, to $629.5 million, and of the 375 firms that filed this year and last, 77.3% reported an increase in general contracting revenue, slightly down from 78.9% on last year’s survey.
Yet behind the numbers, firms say there is a tidal shift among owners as they prioritize projects in sectors that will yield larger return on investment with lower short-term risks.
“Interest rate increases have made it challenging for some clients to obtain construction loans,” says Primus Builders Chief Financial Officer Matthew Hott. Although this has not reduced the No. 278-ranked contractor’s backlog, Hott says the delays can affect project starts, “which can move financial activities from one year to the next in some cases,” he adds.
Although the inflation rates are still higher than the Fed’s target average, some contractors are finding cost increases to be “a more manageable and predictable challenge than it was a couple of years ago,” says Clayco’s Johnson. For other contractors, the ability to manage such a challenge depends on the contractor’s ability to adjust already strained labor resources.
Shifting Sectors
As owners shift their attention to opportunities in lower risk sectors, Top 400 revenue numbers illustrate how contractors are following the demand.
From 2022 to 2023, revenue increased in all ENR-tracked sectors, except hazardous waste, which was down 9.7%. The largest growth was seen in manufacturing (up 74.8%), petroleum (up 46.7%), sewer/waste (up 38.8%) and water supply (up 28.6%). The manufacturing market in particular grew exponentially, with total general contracting revenue up 201% from 2021 and 2023. In 2021, 115 Top 400 firms had at least some manufacturing revenue. In 2023, that number increased to 142.
“The manufacturing sector continues to grow, due in no small part to the resurgence of Federal investment in the onshoring and reshoring of advanced manufacturing,” says Deron Brown, president and COO of PCL Construction’s U.S. Operations. “From pharmaceuticals to microchips, almost every sector of manufacturing is growing, creating significant opportunity in the coming years for contractors with the skillset to build new facilities.”
Industrywide, Top 400 contractors say projects funded by the Bipartisan Infrastructure Law (IIJA), CHIPS and the Science Act and Inflation Reduction Act (IRA) are also creating more opportunities.
“In energy for example, government initiatives like the IRA have driven a significant increase in our early phase solutions,” says Ken Gilmartin, CEO of Wood PLC, which is ranked No. 323. “Equally in oil and gas, we have seen significant growth in 2023 as the energy security agenda has increased globally.”
Brown says PCL, which is ranked No. 10, has also seen opportunity growth in water and wastewater infrastructure projects as municipalities comply with new federal standards for the allowable amount of per-and polyfluoroalkyl substances (PFAS) in drinking water.
“As water reuse continues to grow, we’ve seen an increase in investment in advanced water filtration facilities,” says Brown, adding that the firm is in the preconstruction phase of a direct-to-potable facility, which will recycle toilet and shower water into safe drinking water.
In addition to bridge replacement, reconstruction and rehabilitation, S&B USA Chief Commercial Officer Haggai Dror says the contractor is entering new markets such as rail infrastructure and climate resiliency solutions. “These trends are fueled by initiatives like the IIJA and the IRA, and we’re strategically aligning ourselves to seize these opportunities,” he says.
Profitability Pressures
With an abundance of projects in some sectors, Top 400 contractors say other sectors are slowing because they need more owner buy-in to justify the risks.
In the multifamily residential building sector, Wieland CEO Edward Lorenz says the firm has seen many deals delayed or scrapped entirely due to higher interest rates. “These customers must rethink their ROI goals, or raise rents, and rents are already at all-time highs,” he says. The firm is ranked No. 318 this year.
At Dallas, Texas-based MYCON, interest rates hikes have reshaped the sector makeup of its project portfolio as owners shift to sectors that will yield more returns in the short term.
“We are seeing slightly less industrial, but retail is not being weighed down by the current interest rates, and the demand is rapidly growing,” says Chip Myers, partner and vice president at the No. 234-ranked general contractor. “This shift is pushing us towards certain sectors to keep up with the demand.”
He adds, “As we look across the breadth of our markets, we see growing opportunities in energy transition with hydrogen and carbon capture as the industry seeks to diversify.”
Of 314 contractors that reported their profitability status, 97.5% said they made a profit domestically, while 97.1% saw international profits. The median domestic profit margin is 4%, up from 3.2% last year.
But behind the numbers, Top 400 contractors see ongoing pressure to keep projects profitable.
On recent jobs, Clancy & Theys President Baker Glasgow says the firm, ranked at No. 120, faced numerous challenges to manage shifting project schedules, supply chain disruptions and meet labor demands.
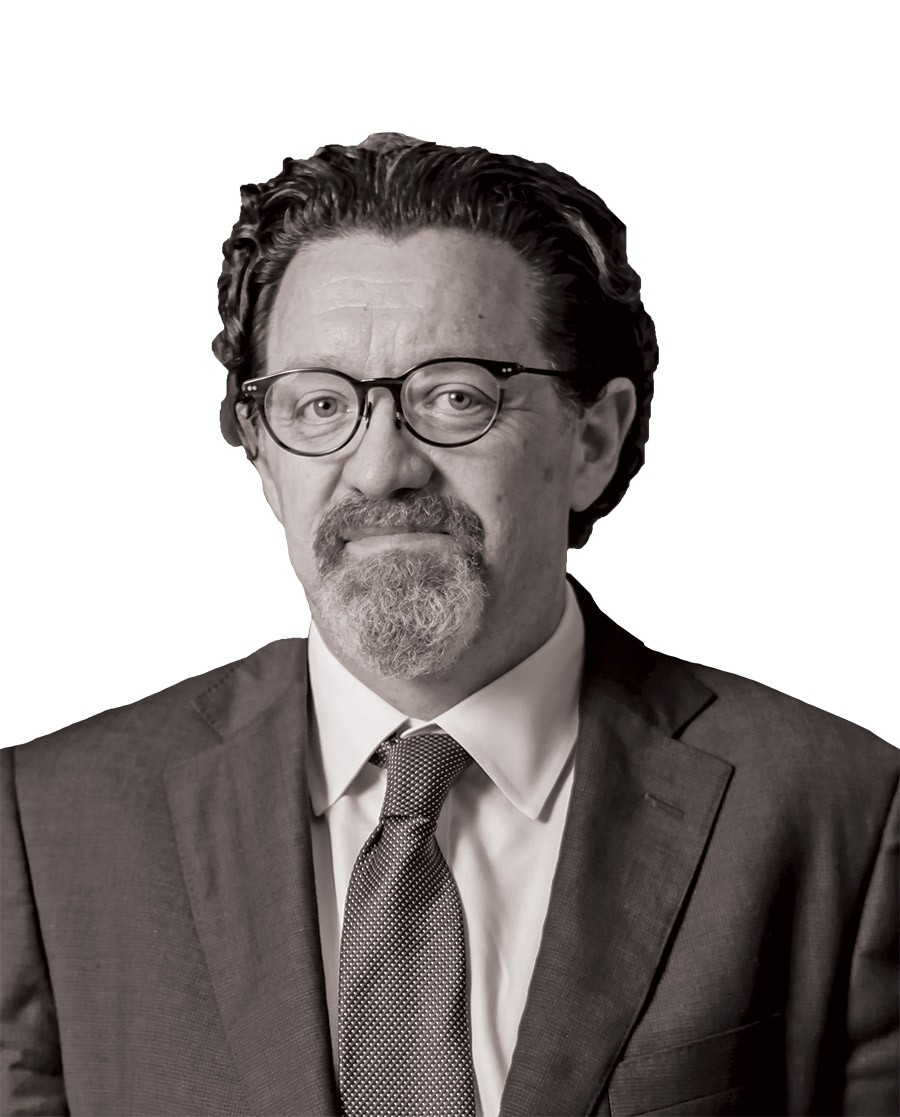
“We see growing opportunities in energy transition with hydrogen and carbon capture as the industry seeks to diversify.”
Ken Gilmartin, CEO, Wood PLC
There is “too much work out there distressing the trade partners and not allowing them to place adequate resources on projects,” says Glasgow. There’s “also major pressure from owners who have ‘floating’ construction rates that have put their proforma upside down, making it more difficult to get additional general conditions, schedule extensions, etc.”
In an Associated General Contractors of America report on the price of materials and services used in nonresidential construction, chief economist Ken Simonson found that prices for construction inputs have risen faster than contractors’ bids every month in 2024, with an increase of .4% from March to April.
Also, “persistently long lead times for electrical equipment are adding to the cost of many building and infrastructure projects,” says Simonson, with federal policies such as Buy America also poised to “drive up prices for federally aided projects such as highways.”
Even as the country drives toward an energy shift with electric vehicles, Top 400 firms say there is a steep technical learning curve for contractors to get electric infrastructure and manufacturing projects shovel ready, and an even steeper timetable for owners looking for investment returns.
“Automotive suppliers must reconcile government demands for EV products while balancing low consumer demand,” explains Wieland’s Lorenz. “It can create a very (unstable) outlook for our customers.”
Like many Top 400 contractors, “the Inflation Reduction Act and CHIPS Act has resulted in a wave of new projects” for Gray Construction, ranked No. 40, says President and CEO Brian Jones, adding that the firm is seeing “a surge of projects emerge related to electric vehicles, solar panels, and semi-conductors.”
“Most of these projects are mega at scale and have significant impacts on the bottom line,” he says. This includes—as is often with megaprojects—impacts on limited company resources.
To reduce risks and bake more predictability into projects, Jones says the firm has developed a preconstruction phase, including multiple value engineering sessions that are “deliberate,” and a “collaborative” engagement of all project stakeholders to determine best value solutions.
“Building trust in the early stages of a project can be a huge challenge,’ adds Jones. “Understanding our client’s decision-making process is key to our preconstruction strategy. Whether we interact directly with the decision-maker or a committee, we adapt our approach to respect their structure.”
Mixed-Use | By Jonathan Keller
Photo courtesy of Barton Malow
Barton Malow (No. 19) recently topped out Hudson’s Detroit, a 1.5 million-sq-ft, 685-ft high mixed-use development in the city’s downtown. The project is located on the former site of the J.L. Hudson department store, one of the largest U.S. retail stores before its controlled demolition in 1998. The replacement structure will be Detroit’s first skyscraper in 30 years, Barton Malow says. More than 2.7 million worker hours have gone into the project.
Early collaboration can save valuable project scheduling time in the long run by pre-empting potential challenges, solving them before construction starts.
“One significant challenge is assisting owners in achieving their project goals within budgetary constraints,” says Samet Corp. President and COO Rick Davenport. “We’ve implemented a proactive approach by offering our expertise and involvement earlier in the project lifecycle. By engaging with owners from the outset, we can better understand their needs, preferences and budget limitations, allowing us to develop realistic and achievable project plans in partnership.”
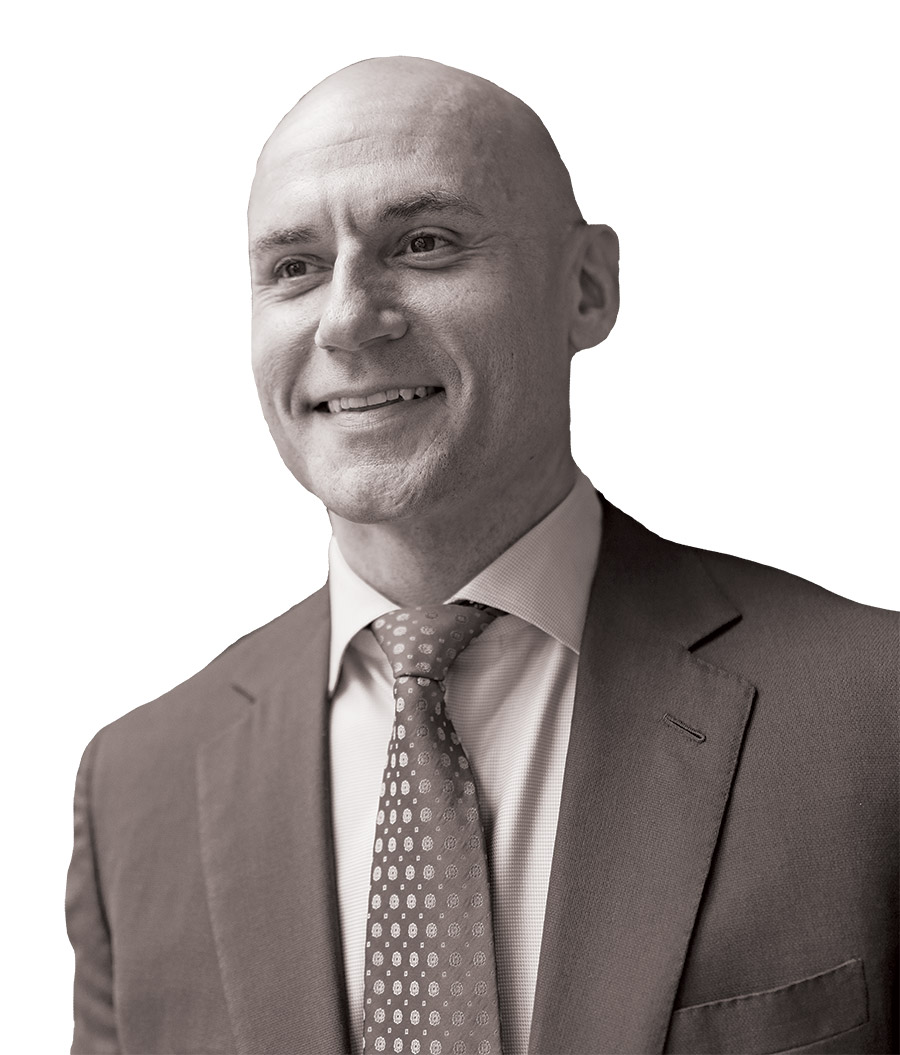
“The Inflation Reduction Act and CHIPS Act resulted in a wave of new projects. … Most of these projects are mega at scale and have significant impacts on the bottom line.”
Brian Jones, President and CEO, Gray Construction
Amid supply chain disruptions, procurement of materials and equipment early in the preconstruction phase can still pose challenges, says Davenport. “To mitigate these challenges, we’ve established strategic partnerships with suppliers and subcontractors, enabling us to secure materials and equipment in advance and minimize delays,” he says.
Turner Construction Executive Vice President Mike Kuntz says the firm is using prefabrication to decrease cost and safety risks on the jobsite. The firm is ranked No. 1.
"On an electric vehicle battery plant, we are building components in manufacturing-like environments and delivering prefabricated sections to the project site," says Kuntz. "It is driving increased construction productivity and the solution removed 80,000 hours from the work site."
He adds, "Across our portfolio of work, offsite construction helps us achieve improved project schedules, reduced cost and budget, improved site safety, and enhanced quality."
At Knutson Construction, Director of Preconstruction Micah Vainikka says a main challenge that the firm has faced in the preconstruction phase is the “increased speed of project development and subsequent need for urgent pricing support.”
Vainikka explains, “We work hard to overcome this challenge by leveraging historical data and relevant software tools to ensure we respond to requests like this quickly and with a high level of confidence in our estimates.” The firm is ranked No. 246.
Digital tools such as 3D models, predictive data analytics and artificial intelligence have also helped increase Knutson’s efficiency in predicting bottlenecks, says Vainikka, but like many Top 400 contractors, they have found that historical cost data can be unreliable in an unpredictable market.
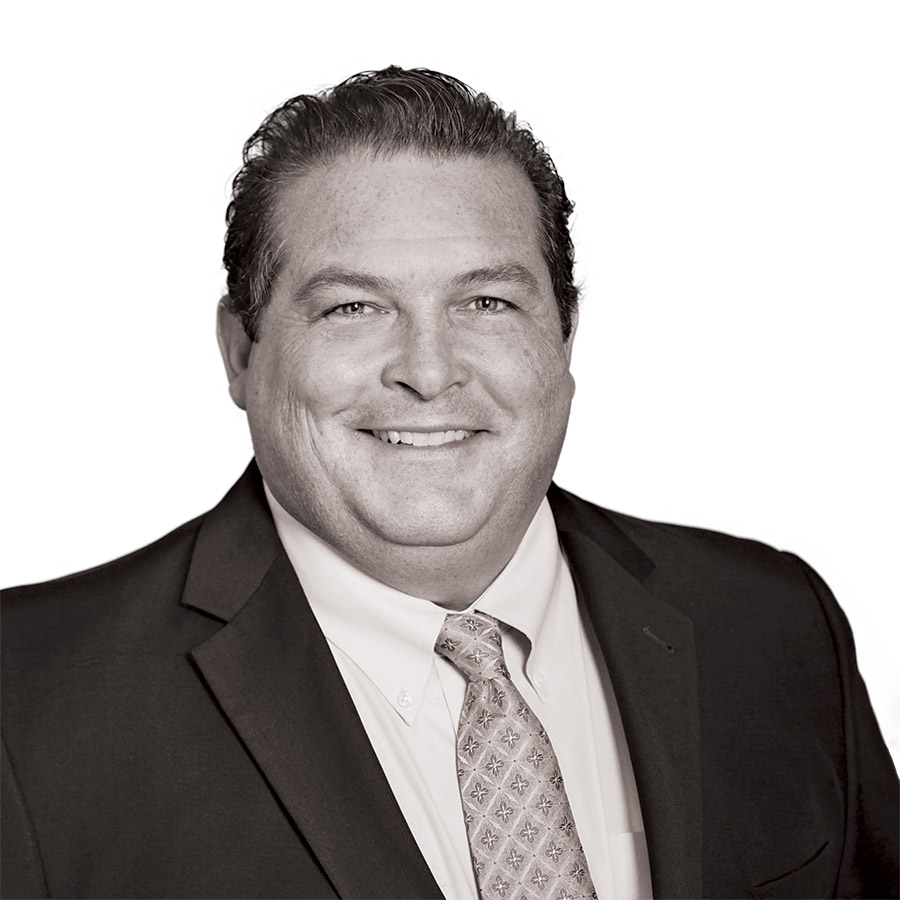
“By engaging with owners from the outset, we can better understand their needs, preferences and budget limitations...”
Rick Davenport, President and COO, Samet Corp.
“Historical costs are somewhat obsolete in this market,” says Doster Construction Co. Executive Vice President Alan Chandler. “You have to dive in and get current feedback to be accurate.”
JE Dunn Chief Strategy and Client Experience Officer Rodd Merchant adds that delayed project starts have also made total construction cost forecasting more difficult.
“Labor pricing and project staffing are more challenging in this environment,” he says. “Beyond just the labor and materials, balancing additional requirements of projects such as sustainability, facility management and social design can add other challenges to the preconstruction phase.”
To address obstacles, Merchant says JE Dunn uses a “target value delivery” management practice throughout the lifecycle of the project to ensure the project’s definition of success is achieved.
“And the cost remains aligned with project scope,” he says. JE Dunn is ranked No. 18.
Top 400 firms have overwhelmingly shared that skilled labor resources continues to be the industry’s most pressing hurdle when it comes to project profitability and delivering projects on time.
Sustainable Cold Storage | By Jonathan Keller
Photo courtesy of Primus Builders
Workers from Primus Builders (No. 278) survey installation of a 1-MW solar array on the roof of a 295,000-sq-ft greenfield cold storage warehouse in Ridgeville, S.C., which will produce 1.5 million kwh of energy. On track to achieve LEED Gold certification, the facility will also feature a 50,000-gal rainwater capture tank to be used as part of an adiabatic cooling system that reduces the water requirement by 50% compared to traditional cooling tower systems, Primus says. Materials have been sourced regionally, and had their Environmental Product Declaration reviewed to make sure no ingredients were on the red list.
Digital Helping Hands
Emery Sapp & Sons co-CEO Tim Paulson says the industry must continue to make labor programs and trade school partnerships a priority. The contractor appears on ENR’s Top 400 list for the first time, at rank No. 119.
“Attracting the talent to meet the craft workforce needs on our infrastructure projects continues to be a challenge,” explains Paulson. “Recruitment, retention and upscaling talent will be our company’s and our industry’s challenge for the next decades.”
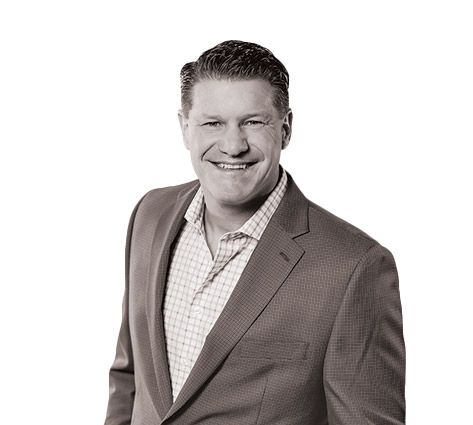
“Recruitment, retention and upscaling talent will be our company’s and our industry’s challenge for the next decades”
Tim Paulson, co-CEO, Emery Sapp & Sons
Swinerton, ranked No. 35, says it is on its way to becoming one of the largest concrete and drywall contractors in the U.S., but CEO David Callis says the company’s biggest obstacle is growing and training its craft employees. “This challenge is not unique to Swinerton, and represents a fantastic opportunity to conduct outreach events in our trade schools and high schools to better inform our youth of the opportunities within the construction industry,” says Callis.
McGough President and CEO Tom McGough Jr. adds, “As construction projects become more sophisticated, the demand for skilled labor increases.”
To address long-term labor pool challenges, McGough says the company is investing in recruiting and talent development programs, including partnerships with trade partners and educational institutions. In the short-term, the No. 115 ranked contractor has made hardware and software investments to give its project teams some digital helping hands.
With a focus on early 4D planning, coordination, prefabrication, quality assurance and project controls, Jeff Dzurik, McGough executive vice president, enterprise construction services says the company’s recent tech investments include drone deployment and Openspace.ai for reality capture, BIM for integrated collaboration, wearable Lidar scanners, mobile augmented reality tablets for overlaying fabrication models and virtual reality headsets for early visualization.
He adds that the company is also “excited about advancements in autonomous reality capture using robots and opportunities to leverage AI across our business operations.”
Kiewit, ranked No. 2, shares that the company has continued to make investments in data infrastructure and data strategy over the past year, including artificial intelligence utilization in the form of a new cloud data platform.
“This platform is the backbone of our automation and data science initiatives and is propelling our AI advancements,” says the firm. “As we’re getting our arms around the value and true business impact of AI, we’re starting to transform industry standards and innovate in ways that we believe will help reshape the future of construction and engineering.”
Presidential Libraries | By Jonathan Keller
Photo by Chad Ziemendorf; courtesy of JE Dunn
JE Dunn (No. 18) is building the 92,000-sq-ft Theodore Roosevelt Presidential Library in Medora, N.D., near the national park named for the 26th president, who lived in the region in the 1880s. Estimated project cost is $333 million, with most privately funded so far. The mass timber library, targeting full Living Building and LEED platinum certifications by its 2026 opening, is set to be net-zero energy, water and waste.
Industry Evolution
Beyond technology, Top 400 contractors say they are reconfiguring operations and adopting new ways of cultivating resources, internally and externally, to keep pace with changing industry demands.
At No. 201-ranked Stacy and Witbeck, President Clayton Gilliland cites success in battling profitability challenges with alternate project delivery, which has helped the firm “by reshaping or reprioritizing the project scope, schedule and budget while keeping project goals intact.”
Over the past year, Primus has invested in improving its business operating system, says Hott. “The highlight of this effort has been standardizing our operating procedures so that when an employee joins our team, they have every tool necessary to succeed starting on Day 1, no matter what their role is,” he says.
Contractor Clayco has expanded purchasing and engineering services through its subsidiary, Consolidated Distribution Co., which leverages international and national purchasing power.
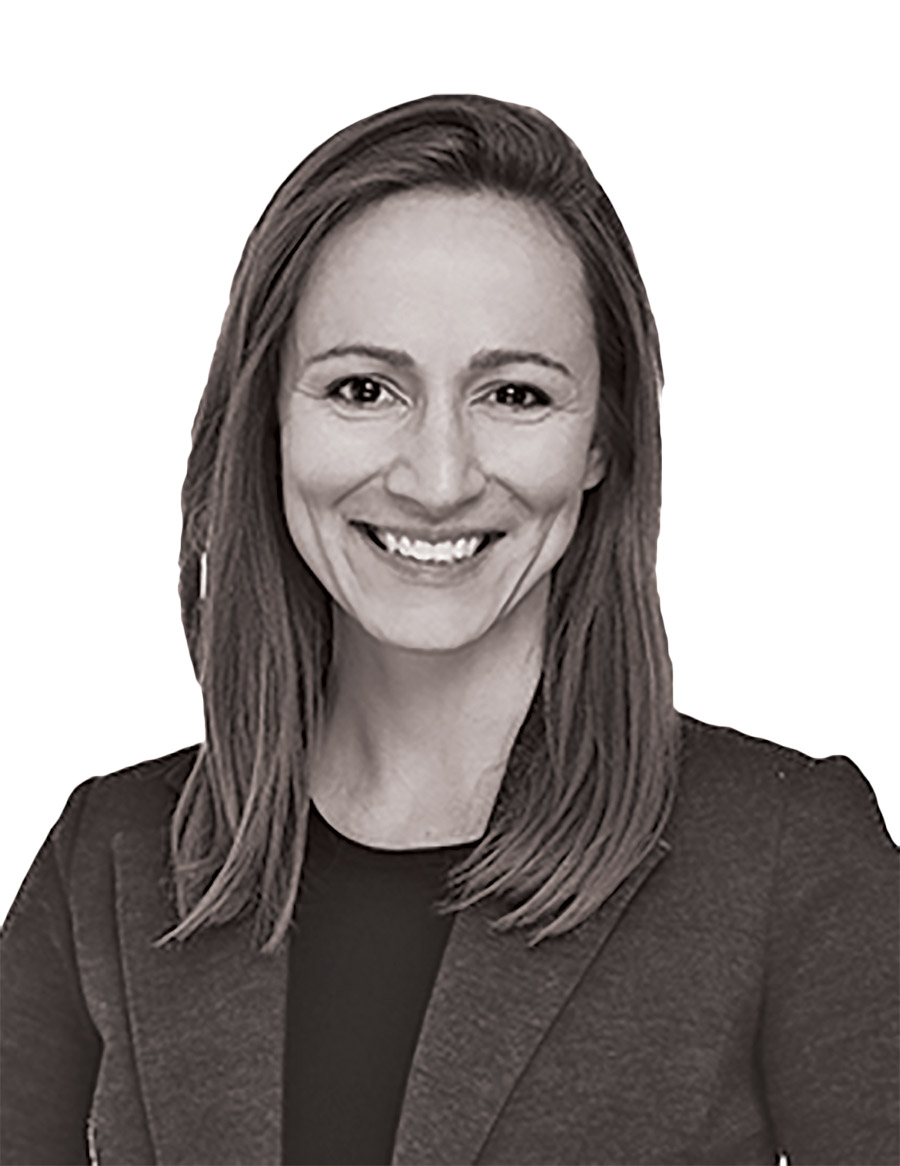
“In addition to professional training, we see our employees as ‘whole leaders’ and invest deeply in personal development.”
Emily Livorsi, VP of People, Catamount
“Along with supplying products, we also provide product customization and logistics, and can assist in strategic planning and specifications,” says Johnson.
On ENR’s Top 400 list, domestic and international contracting revenue totals rose 13.4% and 21.7%, respectively. The return of McDermott International to the list, ranked No. 9, heavily influenced its international revenue, adding $5.74 billion. Median international revenue fell 12.7%, to $58.9 million this year from $67.5 million last year. Less than half of the firms who filed both this year and last saw an increase in international revenue this year.
The numbers could reflect a business strategy among contractors to focus on the markets they know best to cultivate quality and control of resources, in place of rapid expansion, explains Moss CEO Scott Moss.
“With growth comes the challenge of scaling effectively while still maintaining the integrity of the values that have differentiated Moss from other contractors within the space,” he says. “Leadership has recognized the importance of maintaining these values and principles in perpetuity and has adopted several strategies that support this initiative as we continue to scale.”
Moss explains that its employees are the most important factor in achieving company goals. “Strategic hiring practices have been implemented to make sure we are welcoming people that are not only capable of doing the work but doing it in alignment with our core values,” he explains.
As Garney CEO David Burkhart notes, sometimes the most powerful solution is to focus on refining the industry’s core practices.
“In today’s labor market, investing in fundamental principles by returning to the basics is crucial to maintain competitiveness and ensure our workforce is well-equipped for future success,” says Burkhart. “While technological expertise is highly valuable, it’s important to maintain sight of the critical core experience required in our highly specialized industry.”
At Catamount Constructors, ranked No. 139, this strategy has also materialized in investments in employee well-being, says Emily Livorsi, vice president of people.
“In addition to professional training, we see our employees as ‘whole leaders’ and invest deeply in personal development including physical, financial and emotional well-being,” she says. “Our people have shared time and again that one of Catamount’s differentiators is the deep focus on development.”
As the industry onboards new employees, contractors must focus on evolving their skills, says Pepper Construction Executive Vice President Jay Ripsky. The firm is ranked No. 63.
“We want them to feel supported as they adapt to our culture and are able to become part of the family,” says Ripsky, as the Chicago-based contractor approaches its 100-year anniversary.
“Ironically, construction is the only industry that has become less productive over the past 50 years,” says Suffolk Construction CEO and Chairman John Fish. Noting that the Empire State Building was built in just under 14 months, “Today, it would take four years to build that same building because our industry is so fragmented and siloed,” with “contractors less willing to innovate or change the way it has always been done,” he adds. “We must innovate.”
Yet innovation must not be the construction industry’s sole purpose, says Turner Construction's Kuntz.
“In 50 years, as people reflect on our work building significant sustainable and resilient projects in our communities, I hope they will recognize that the most lasting, rewarding and life-changing work we have done is the progress we made in building a more just society.” he says.
A version of this article appears in the May 22 issue of ENR.