Children's Hospital of Richmond at VCU
Richmond
BEST PROJECT, HEALTH CARE
Submitted By: DPR Construction
Owner: VCU Health
Lead Design Firm: HKS Inc.
General Contractor: DPR Construction
Civil Engineer: Draper Aden Associates
Structural Engineer: Dunbar, Milby, Williams, Pittman & Vaughan
Support of Excavation: Schnabel Geostructural Design & Construction
Construction Manager: JLL
Subcontractors: Atlantic Constructors Inc.; DPR Drywall; Pioneer Cladding & Glazing Systems Inc.; Prospect Steel; Liphart Steel, Mid Atlantic Steel Erectors; TK Elevator Corp.
Long before the challenges presented by the COVID-19 pandemic emerged, the project team on the Children’s Hospital of Richmond faced a daunting goal: design and construct a 600,000-sq-ft acute care hospital on an urban campus in about four years. Construction manager DPR Construction and design lead HKS were already two years into a validation study for a combined adult and children’s facility when VCU Health pivoted in late 2018 to developing a hospital focused on children and adolescents. The target was 2023.
In searching for sites, the team chose to create a 20-level addition to VCU's existing outpatient Children’s Pavilion with a five-level vertical expansion of the existing pavilion. Constrained within the boundaries of one city block, the design expanded the facility horizontally, vertically and on top of the pavilion, connecting each level to the existing structure. Ultimately, the plan would consolidate pediatric services from multiple buildings across campus into the expanded facility.

Children's Hospital of Richmond credits building a “fully kid-focused” hospital to teamwork and collaboration.
Photo by Garrett Rowland, courtesy DPR Construction
Facing an aggressive timeline with only a stacking diagram and square footages at that point, the team tapped integrated project delivery (IPD) methods to accelerate the project. Although DPR served as construction manager at-risk, the team agreed to work in an open-book, over-the-shoulder environment that allowed construction activities to move forward while designs were still underway.
“VCU Health Board made the decision to build a children’s hospital on Feb. 5, 2019, and in four years, we developed a program, validated it, designed it and built it, so that by April 30, 2023, they were seeing their first patients,” says Jason Maxwell, project director at DPR. “It allowed us to get to what really mattered, which was taking care of the kids in the shortest amount of time possible.”
The team developed a cost model in February 2019, and two months later, a guaranteed maximum price enabled it to break ground by demolishing an existing neighboring building. The team split the project into multiple design packages, starting with the demolition and support of the excavation package. Demolition and excavation proceeded while the building’s design was still in the early schematic phase.
Adopting IPD-Light
Matt Franklin, principal at HKS, says employing “IPD-light” methods and lean principles was critical for keeping the project on schedule. “It was a great partnership with DPR, where we really did a lot of pull-planning and confirmed when they needed the materials on site,” he says. “That then led to the different packages that we had to break out. We knew the overall master plan that [VCU Health] wanted to build. That helped guide us to the shell of the building, so that we knew the kind of the box that we then needed to fill.”
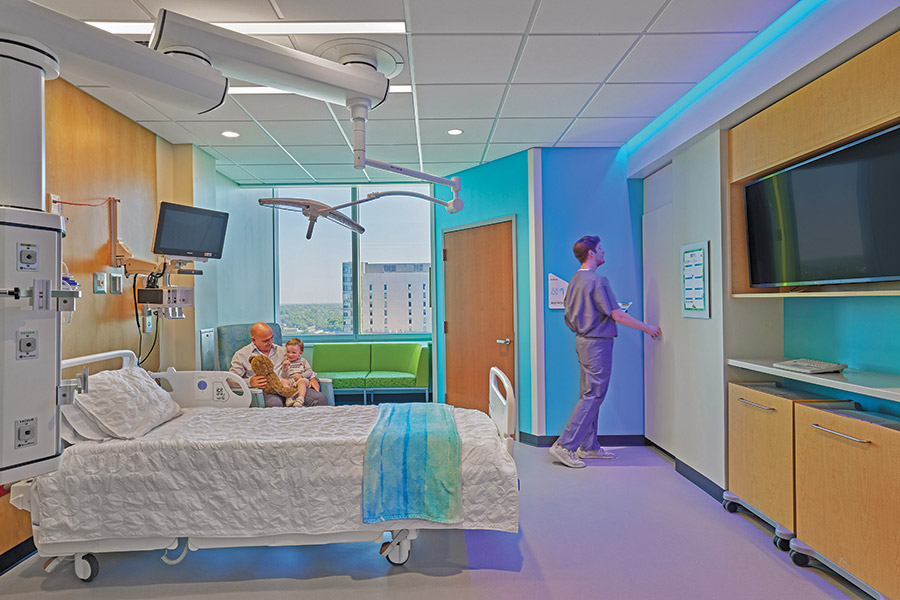
The project is pursuing LEED certification with elements including construction and waste recycling and management, energy performance optimization and enhanced indoor air quality strategies.
Photo by Garrett Rowland, courtesy DPR Construction
To create the structural design package, the team referenced the existing building, which fortuitously had also been designed by HKS. The existing pavilion’s structure featured eight levels of concrete structure—including four levels below grade—topped with steel structure. Franklin says the structural system chosen for the pavilion was “purely based on schedule,” allowing concrete structural work to get underway while steel was being fabricated. As a result, the new hospital was able to see those same advantages. In addition, by matching the structural systems, the two buildings would be easily combined to create a single structure, rather than two structures connected with expansion joints.
Employing IPD methodologies, the team used target value delivery, starting with the risk and opportunity process to determine where the team could streamline the program, design elements and requirements. Five months into the project, the team refined the project’s costs. In addition to the structural system package, the team considered prefabrication options, crane placement and logistics and bid packages.
As part of that strategy, the team brought on key subcontractors early in design-assist roles, including mechanical and plumbing, electrical, concrete, structural steel and curtain wall.
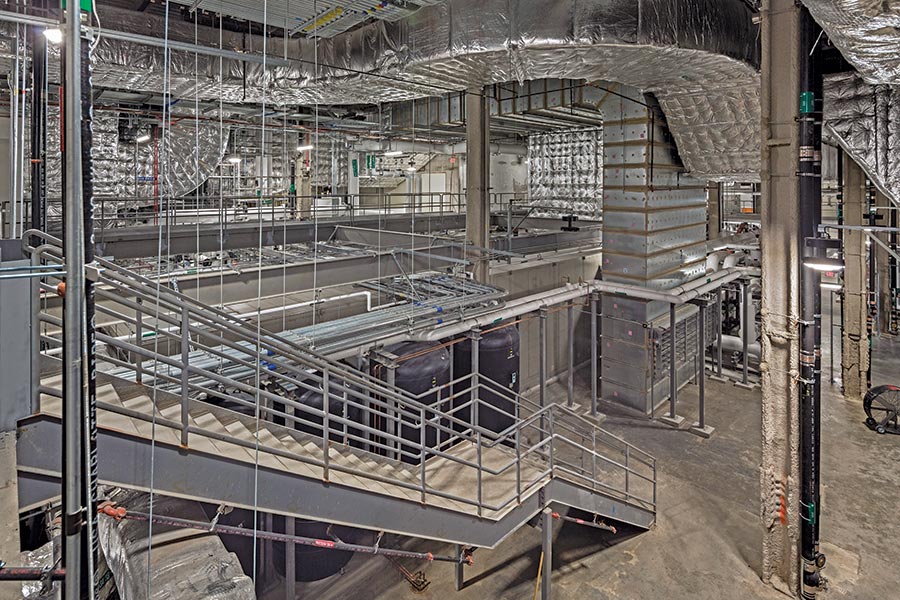
VDC coordination supported by design-assist partners allowed for repeatability of key components on most floors.
Photo by John Baer, Building Images Photography, courtesy DPR Construction
Just 601 days after inception, a final GMP was approved when $73 million of work had already been completed on the site. In all, the team delivered 26 estimates, nine design-assist packages and 70 bid packages through 10 cluster teams. Nearly $6.7 million of scope was added to the project, bringing the final cost within 2% of the final GMP. The team declined to disclose the total project value.
Throughout the project, the team employed a “big room” to intermingle the companies involved in different scopes of work, enabling them to better collaborate and address issues that challenged the budget. Early on, crane placement emerged as a critical concern on the urban site. Patient floors cantilevered on Levels 2 through 13, eliminating the ability to place tower cranes adjacent to the building. Cranes could not be situated on the sidewalk and the schedule could not accommodate placing them within a stair or elevator shaft. The only option was to put the cranes on the top of the existing building. The crane company, structural engineer, contractor and designers met and devised a solution to incorporate the tower cranes’ steel base structures into the final building steel. The strategy required upgrading columns and bracing beams on the floor below, extending 10 columns 25 ft above the existing roof and using horizontal I-beam bracing and diagonal tube steel bracing.
Acceleration Through Prefabrication
To speed up the schedule and overcome the site’s limited laydown and staging areas, multiple trades used prefabrication on significant scopes of work. With 70 identical patient rooms, the team designed and constructed the headwalls off site with framing, medical gas, electrical and wood blocking in a panelized wall system. The team then installed the headwalls and connected the overhead piping to the in-wall piping. With rooms back-to-back, one prefab wall accommodated two patient rooms.
The team was also able to spool sheet metal stud framing drawings to assist with layout, verification and quality control of penetrations for all through-wall items. The team worked with the door and hardware supplier to pre-install hardware on the doors before delivery.
A 275-ft-long structural steel pedestrian bridge that connects to the main hospital was also prefabricated off site in four sections for faster installation.
Overall, DPR estimates that prefabricated items removed 85% of onsite worker hours from those scopes of work. Use of exterior curtain wall panels on four stories of the new building reduced installation to 15 days from a baseline of 40 days. DPR also estimates that rework of MEP openings was reduced to less than 5%, from 20%.
As the project progressed through the early months of the pandemic, the team started to experience issues with labor and material availability, says Eric Rasmussen, project executive with DPR.
“By summer [2020], we’re starting to buy out final packages,” he recalls. “We hadn’t really hit major supply chain issues yet in the spring, but we were starting to hear about them a little bit. They really started challenging us through the summer of 2020 into the fall, which was the time we were finalizing our full GMP for the project with the owner.”
Rasmussen says that by splitting the project into packages and locking in pricing early saved the project from the worst of the supply chain issues that came in 2021. As part of the team’s plan to stay on budget, some planned spaces were initially shelled. But through target value delivery, some of those spaces were put back into the project. Since opening, some additional shelled spaces have been revived, thanks largely to donations, according to VCU.
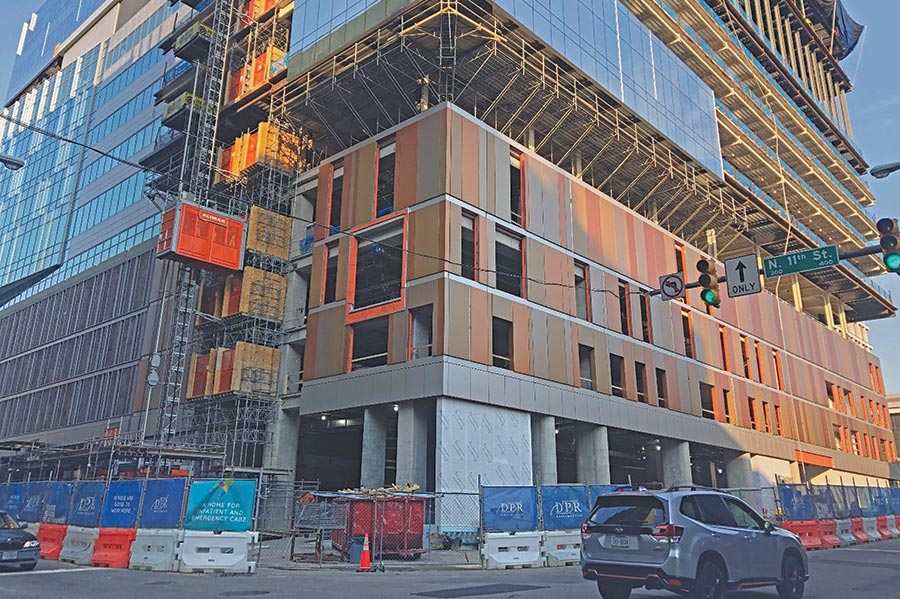
A large cantilever that extends over the sidewalk prevented the team from placing tower cranes adjacent to the new building. Instead, cranes were placed on top of the existing pavilion.
Photo courtesy DPR Construction
Achieving the Vision
Delivered on time and on budget in April 2023, the completed project creates a full-service, free-standing children’s hospital at the gateway to the VCUH’s medical campus. The new hospital consolidates existing pediatric clinics and inpatient and emergency department services into a pavilion capable of providing comprehensive health care for children and adolescents.
The hospital now features 72 pediatric inpatient beds; 24 pediatric ICU beds; 48 acute medical/surgical beds; shell space for future expansion of up to 120 beds; a pediatric emergency department; and an inpatient surgery department expansion. Other support spaces include a kitchen and dining area; a satellite laboratory; an inpatient pharmacy; and a rooftop helipad.
The vision for the patient tower design was to create an oasis for children and their families. The design draws inspiration from the James River and other natural elements, such as sky, water and forest themes.
Bright colors and imagery taken from local natural features, biophilia and native animals as well as local landmarks were used throughout the facility.
“We used color as a wayfinding theme,” Franklin says. “Pops of color are used at key moments on the floors to give the visitors and families a visual cue of important areas.”
As an expansion, the new addition builds on the design of the original pavilion to create a cohesive building. Its massing aims to break down the overall scale of the expanded structure, with the lowest zone honoring the neighborhood’s historic content.
One judge complimented the team on overall massing of the design. “There’s this gap that brings a level of levity, as if there is an element that is gravity defying,” the judge said. “For a children’s hospital, it’s quite important, because it looks like a place that is attractive that you might want to go to although you’re in pain, you’re scared. It’s difficult to get a program stack that requires the height to appear so light-hearted, thin and urban scape.”
Throughout the project, Maxwell says the concept of making the hospital available to the first pediatric patient helped drive the team to the finish.
“The entire team worked together to get to the first patient,” he recalls. “We repeated that constantly throughout the entire target value design process. Yes, we had a substantial completion date, but if we didn’t get to first patient [on schedule] that wouldn’t have been considered a success.”
Post a comment to this article
Report Abusive Comment