As a historic center of American industry, Detroit is a city built on an assembly line production mentality. But to deliver a project that aims to be one of the most sustainable in Michigan, the project team for a new commercial campus had to let nature take its course. Design and construction of a 79,000-sq-ft, six-building project for Japan Solderless Terminals in Farmington Hills, Mich., outside Detroit, blends a reverence for nature with Japanese and American culture, seeking harmony between people and the ecosystem. Preservation of flora and fauna on the site are paramount, guiding not only the design, but how buildings are constructed.
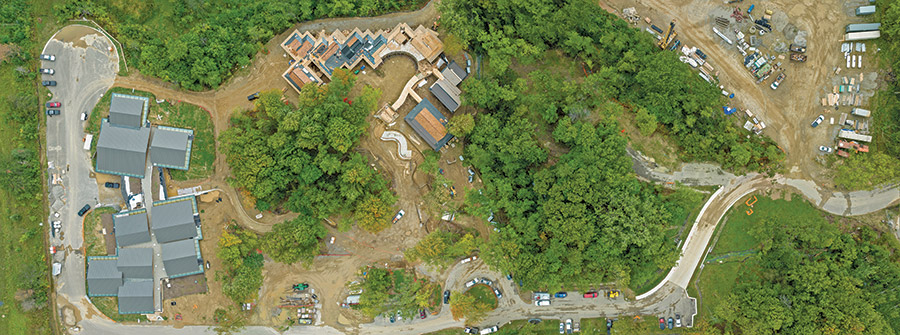
The first three of six buildings are underway on the 10-acre site of the new JST Detroit Engineering Center. The 79,000-sq-ft project aims to maximize preservation of existing flora and fauna.
Photo courtesy of Cunningham-Limp
Organic Approach
From early project planning—which began more than a decade ago—through construction—which began in 2019—construction manager Cunningham-Limp has had to rethink its processes and procedures to meet project goals.
“Southeast Michigan is known for production and our company is known for production,” says Samuel J. Ashley Jr., president of Cunningham-Limp. “So, taking that mindset and then putting together a project that is a true Craftsman style on a commercial scale takes a lot of encouragement of our staff, our subs and our suppliers to really change misconceptions.”
The project, dubbed the JST Detroit Engineering Center, will deliver six interconnected buildings dispersed within a forested 10-acre site. Designed for Japan-based JST by Japanese architect Ryuichi Ashizawa Architects and Associates, the team blended Japanese design aesthetics and sustainability concepts with American standards. Among its most critical goals, the team must preserve as many trees as possible on site and reuse any materials that are cut or excavated on the project site.
Approximately 87 trees were harvested, tagged and removed to clear space for the project. Those trees will be repurposed as structural and aesthetic elements in the buildings, ranging from columns to furniture. In some cases, harvested trees will be reused as close as possible to their original locations. Excavated soil will remain on site to be used as earth berms.
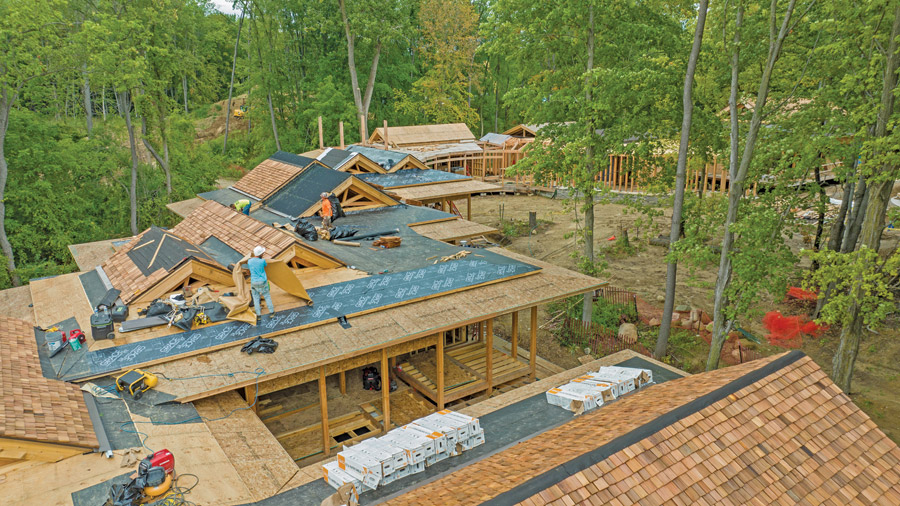
Crews must work around preserved trees on the tight site.
Photo courtesy of Cunningham-Limp
Understanding The Ecosystem
Early in the 6.5-year planning and design process, the architect sent a team to study the site. In addition to discovering existing wetlands that would need to be preserved, the team also studied wildlife on the site.
“They had a series of trail cameras and were mapping out the natural animal pathways,” Ashley recalls. “What they found out is that deer, fox, coyotes, rabbits, squirrels and other animals all funneled down the same pathway to get down to the wetland area.”
“We want to establish harmony with nature to make it sustainable in real terms, rather than just as a certification.”
—Ashizawa Ryuichi, Principal Architect, Ryuichi Ashizawa Architects & Associates
That discovery led to a concept dubbed Animal Road, which would preserve that natural pathway. Honoring its commitment to promote the coexistence of humans and nature, buildings would need to be designed and oriented to maintain those natural pathways without deviation.
The team also discovered that the site had been previously occupied by the Native American Potawatomi tribe. The design team aimed to honor that heritage by incorporating Native American history into the project. For example, a future sales building is being designed using the concept of a Native American longhouse, including a large central fireplace.
Stormwater retention proved to be one of the project’s biggest early challenges, Ashley says. Because the team “surgically carved through the site, preserved topography and kept as many trees as possible,” he says it was impossible to find a location on site for stormwater. Part of the plan called for constructing 72 geothermal wells at depths of up to 450 ft, which eliminated the option of underground storage. Cunningham-Limp helped resolve the issue by working with an adjacent landowner to create a retention pond off site that would be shared by both landowners. The two parties also agreed to allow laydown and staging of construction materials on the adjacent property so that none of the JST site would be affected.
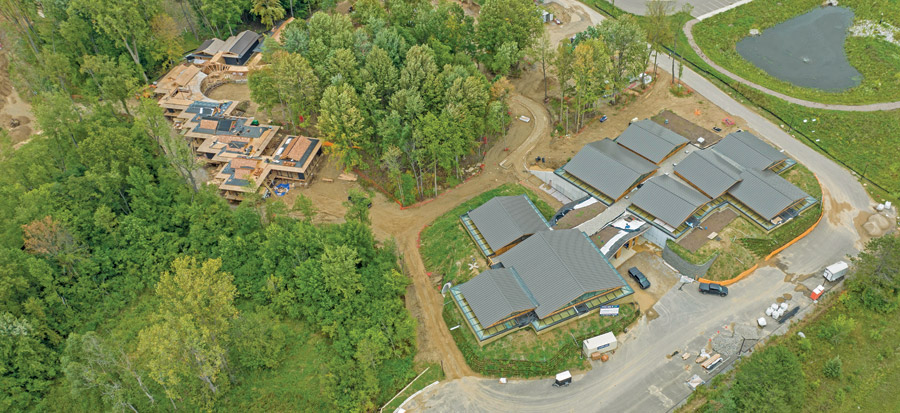
The engineering building, left, is tucked in the existing forest, while the test lab, right, will serve as a sound barrier at the edge of the site.
Photo courtesy of Cunningham-Limp
Among the Trees
Although the site will ultimately feature six buildings, designs of each building are being released over time rather than all delivered at once. The buildings will each provide different functions for owner JST, which is a manufacturer of electrical connectors.
Ashizawa Ryuichi, owner and principal architect at Ryuichi Ashizawa Architects & Associates, says he broke the campus into six components in order to find harmony with the ecosystem.
“The typical approach for this kind of development is to cut the trees, make it wide open, place the building in the middle and surround it with parking,” he says. “Instead, the approach was … how to minimize the disturbance to nature. So, instead of one building, it is multiple buildings, [split up] per function, and trying to avoid disturbing the forest as much as possible.”
He says the approach also honors Native American culture, with a central forested area that is surrounded by structures.
A test lab was the first to break ground and features the largest foundations by volume. As a result, the largest volume of dirt was excavated for that building, in part to accommodate a large cast-in-place concrete wall to support an area of earth massing. The building ultimately sits on a slab-on-grade system.
As with other buildings, the test lab will feature a timber framed structure, including trees harvested from the area where the lab is being built. For example, a 19-year-old, 20-in.-circumference pin oak tree and an 18-year-old, 18-in.-circumference black cherry tree were harvested, sent to Colorado to dry kiln in the high desert, certified for structural grade and returned to be placed in “almost the exact same spots” where they once grew, Ashley says.
The building is placed at the southern edge of the property and serves as a sound barrier for the rest of the site. It is on schedule to complete by the end of this year.
“Everything is considered on a very deep level, not just the superficiality of ‘Let's get this up so we can get operational as quickly as possible.’”
—Mark Rei, Executive Manager, JST Sales America
An engineering building on the west side of the site was designed in a zig-zag pattern, which Ryuichi says helps create more privacy and quiet spaces. Crews aim to close in the building by the winter and complete it next year.
Foundations are underway on the Center Circle building, which will serve as a gateway to the campus, with completion expected next year. The structure is designed in an ellipse shape, with the goal of “trying to absorb sounds from outside—the leaves, the wind and the animals—and trying to get those sounds into the space.”
Other buildings are still in design, including the sales center, an annex building and the Tree House. While all of the main buildings are scaled to remain tucked in the forest, the Tree House will rise above the tree line. It features a domed roof and timber frames wound tightly by instrumental strings, so that when the wind blows, musical sounds will echo throughout the property. When fully completed in 2025, the team expects approximately 4 acres of the 10-acre site will be used for buildings and infrastructure with the rest remaining undisturbed.
Although the project has taken a holistically sustainable approach, the team will not seek any sustainability certifications. “We don’t really care about sustainability checklists,” Ryuichi says. “For us, we want to establish harmony with nature to make it sustainable in real terms, rather than just as a certification.”
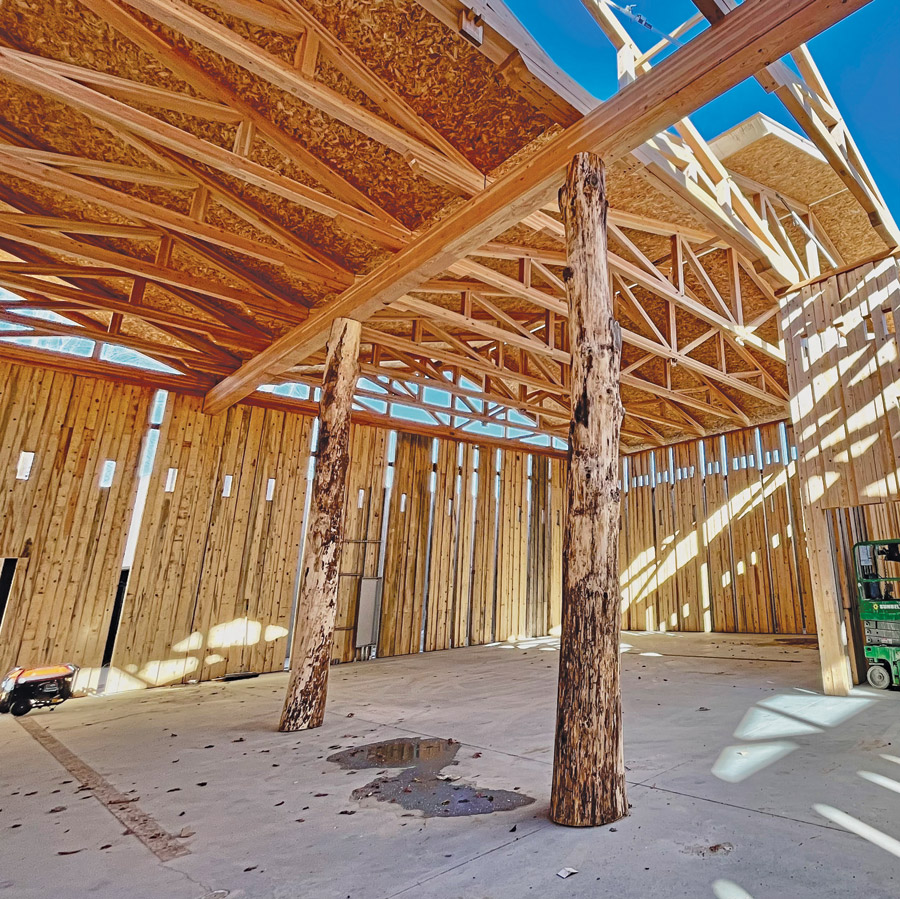
Trees harvested from the site were dry-kilned and used as structural members. They were placed in almost the exact location where they once grew.
Photo courtesy of Cunningham-Limp
Producing Perfection
With designs rolling out over time, Jacob Gardner, senior project manager at Cunningham-Limp, says the greatest challenge is to keep production moving. “When a sub can make production and the project progresses forward rapidly, that’s usually what we push for,” he says. “But here, we’re really taking a step back and taking our time to do it perfect, and that has been the challenge.”
Acquiring qualified subcontractors and specialized materials has also been a significant challenge. A portion of the project will feature a thatched roof. “There’s only a couple of people in the country who can do thatched roof installations,” Ashley adds.
A Japanese craftsman was brought in to create an earth-formed plaster system that will be used in multiple buildings. Crews had to preserve specific clay material excavated from the site for use in the plaster. “It’s a mixture of natural clay, lime and straw that is mixed together and then hand formed into the wall,” Ashley explains. “When they use it for the floor, it’s more impressive because they take it, throw it on the ground, and then barefoot stomp it and form it to shape.”
The test lab will feature a reed ceiling. Designed in a traditional Japanese style, the reeds had to be imported from Japan. To honor the site, most materials were sourced locally to match the local ecosystem, including limestone and sandstone.
All subcontractors are also expected to respect the forested areas and leave them untouched. In many cases, Ashley says this has required use of smaller equipment than usual. There will also be no drywall, paint, carpet or other synthetic products used, and all finishes will remain raw. “We have to remind people not to wipe anything on an exposed material because it’s not being touched once it is installed,” Ashley adds.
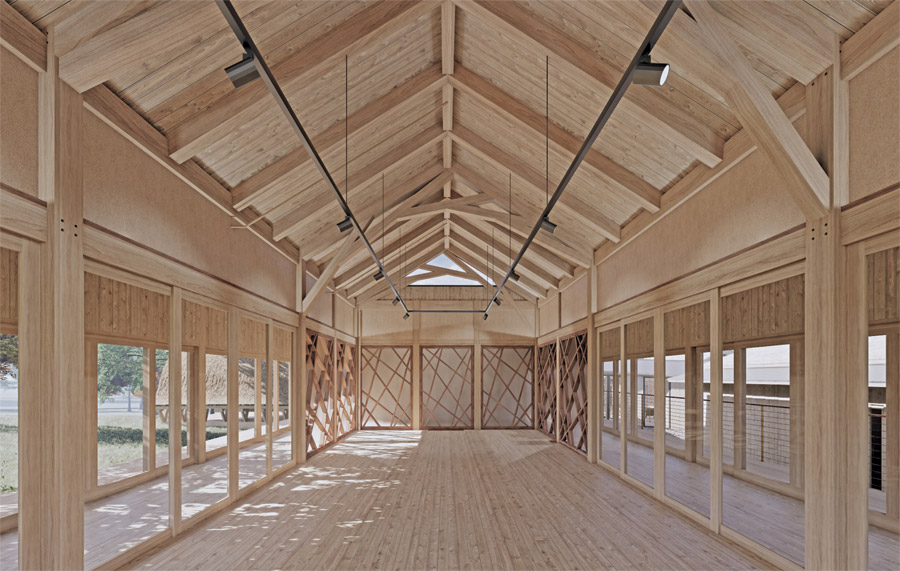
Interiors will emphasize natural materials and raw finishes while welcoming in natural light.
History in the Making
Although the project has been years in the making, JST sees that approach as one that will ultimately benefit the company and its employees.
“Everything is considered on a very deep level, not just the superficiality of ‘Let’s get this up so we can get operational as quickly as possible,’” says Mark Rei, executive manager of global sales and business development leader at JST Sales America.
Despite a myriad of design and construction challenges extending more than a decade, Ashley says he sees the project as a milestone for his company and the community.
“In our history, this is something that we can hold on to and be very proud of,” he says. “We explain to our employees, ‘This is history unfolding right in front of you.’”
Post a comment to this article
Report Abusive Comment