Jacob K. Javits Convention Center Expansion Project
New York City
BEST PROJECT and PROJECT OF THE YEAR FINALIST
Submitted By: Jaros, Baum & Bolles
Owner: New York Convention Center Development Corp.: Empire State Development
Lead Design Firm: TVS
General Contractor: Lendlease Turner JV
Structural Engineer: Magnusson Klemencic Associates
Civil Engineer: Stantec
MEP Engineer: Jaros, Baum & Bolles
Owner’s Representatives: AECOM; Edison Advisors; LehrerCumming
Integrity Monitor: K2 Intelligence
Long before any big trade shows rolled into the expanded spaces of Jacob K. Javits Convention Center, major construction work was on full display along two blocks on Manhattan’s West Side. In 2016, a Lendlease and Turner Construction Co. joint venture embarked on the facility’s $1.5-billion design-build expansion. The New York Convention Center Development Corp. sought to expand the iconic space, originally constructed in the 1980s, to compete with other global convention centers while providing economic enhancement to New York City. Collaborating with designer TVS, the joint venture was able to optimize the indicative design, reduce costs and improve the schedule.
The project called for design and construction of a 1.2-million-sq-ft expansion that would house 90,000 sq ft of exposition space, 200,000 sq ft of pre-function and meeting room space, a 6,000-person special event space and a four-level truck marshaling and loading dock structure.

Photos by Albert Vecerka/Esto, courtesy of Jaros, Baum & Bolles
A 100-person team co-located on site to manage all project phases. Lean construction practices and technology were leveraged to further enhance communication, decision-making, accountability and execution.
Pat Murray, vice president and construction executive at Turner Construction, says the joint venture broke the project into teams— leveraging each other’s strengths while intentionally mixing their members. “We didn’t want to have any lines drawn among the team,” he says. “It was one team, one voice and one goal.”
One key component of the expansion was a new four-level truck marshaling building that solved long-standing problems created by tractor trailers lined up on the West Side Highway, waiting to unload and retrieve Javits center materials. The truck facility relocates more than 20,000 event-related trucks off nearby streets annually while reducing area congestion and pollution. The addition of 27 new loading docks also increases the efficiency of move-in and move-out periods for events.
The team says it evaluated approaches to the truck marshalling facility’s design, including changing the building’s structure from steel to concrete, which yielded significant savings and a more maintainable building.

Photos by Albert Vecerka/Esto, courtesy of Jaros, Baum & Bolles
As part of the redesign, MEP engineering firm Jaros, Baum & Bolles suggested replacing 4-ft-deep horizontal ductwork with vertical risers, passive perimeter air and an active exhaust system. If carbon monoxide sensors detect high levels, the system can go into purge mode through the exhaust system, according to the team.
The project gained nearly 20 ft vertically by removing horizontal ductwork, which enabled the team to reduce excavation. “The whole strategy saved millions of dollars,” says Chris Prochner, a JB&B partner. “With a little bit of modeling up front and a little bit of ingenuity, [the team] came up with a concept that helped win this job.”
During the design process, project scope was expanded to include a 15,000-sq-ft rooftop pavilion above the truck marshaling building, an outdoor terrace and a 1-acre urban farm. The rooftop farm, operated by nonprofit Brooklyn Grange, is one of Manhattan’s largest. It consists of a meadow, shade garden and a 10,000-sq-ft orchard. Food sourced from the farm is served at Javits center events and in the employee cafeteria and offered as giveaways during twice-weekly farm tours and donated to community groups.
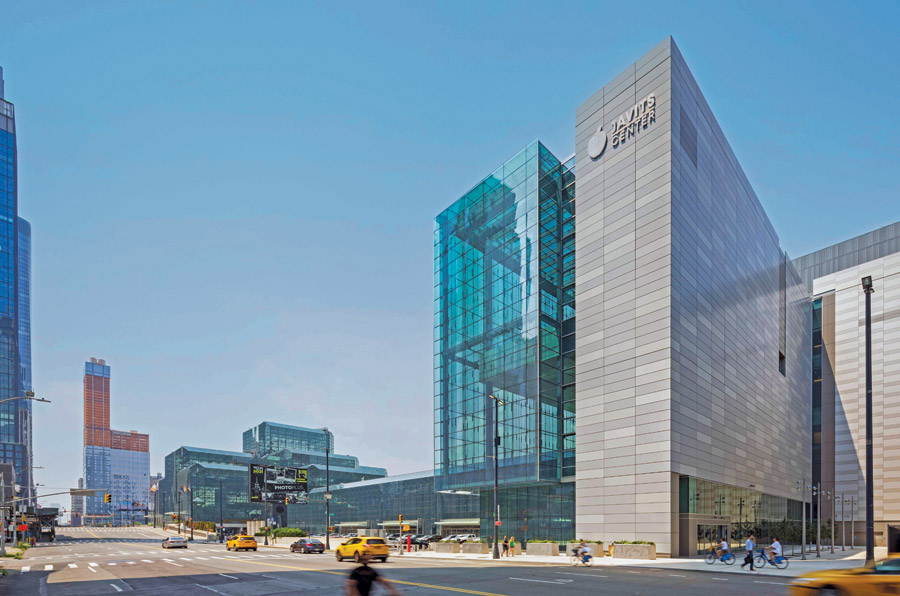
The 1.2-million-sq-ft Javits expansion is designed to house 90,000 sq ft of exposition space, 200,000 sq ft of pre-function and meeting rooms, a 6,000-person special event area and a four-level truck marshaling and loading dock building with a 15,000-sq-ft rooftop pavilion.
Photos by Albert Vecerka/Esto, courtesy of Jaros, Baum & Bolles
Adding to the construction challenge, the heavily used Lincoln Tunnel passes through the project site—sloping from just 6 ft below grade on one side of the site to 100 ft deep on the other. Use of long-span, cast-in-place concrete beams connecting to caissons and structural walls helped the project avoid any conflicts with the tunnel.
While the truck marshaling building was concrete, the remaining structure was steel. The team prefabricated portions of the super-truss structure, which helped improve functionality of the building with long spans for the exposition space.
“The vertical height of the main trusses are about 45 feet tall,” Murray says. “So we broke that truss down to a bottom cord that was 18.5 feet tall. We preassembled the lower cords on site and then we did tandem picks with the cranes. We set the bottom cords in one shot and then used those bottom cords without the need for shoring below. Then we built the rest of the superstructure above it.”
The facade uses a large-format unitized system, including some pieces that measured 10 ft by 25 ft. Panels were fabricated off site in Long Island and trucked to the site. JB&B was also able to reduce both the number of electrical substations and their parasitic HVAC loads by feeding rooftop HVAC from air-cooled outdoor rooftop substations. The strategy helped lower both operating and construction costs.
Theatrical rigging and state-of-the-art audiovisual and IT equipment were provided in the meeting rooms on the levels above the exposition space. The special event space, which accommodates up to 6,000 people, has automatic-shading equipment.

Atrium and lobby spaces feature multi-storied window walls and fritted glazing. Lobbies on the meeting room and ballroom levels have southern exposures overlooking the 6.75-acre green roof of the existing Javits center.
Photos by Albert Vecerka/Esto, courtesy of Jaros, Baum & Bolles
The meeting rooms and special event space are also finished with high-end materials, including acoustical wall treatments and acoustically rated folding partitions, says the team. Kitchens on two levels further support the function spaces.
Atrium and lobby spaces feature multistoried window walls and fritted glazing as well as elevators and escalators in an open space environment. The lobbies on the meeting room and ballroom levels have southern exposures overlooking the 6.75-acre green roof of the existing Javits center.
Schedule was a key driver of the project, which aimed for a mid-2021 opening. In March 2020, the state mandated a COVID-19 related shutdown of all construction for more than 30 days.
The project achieved the completion date by using overtime and accelerated schedules from trade contracts. Close collaboration between the project team and convention center staff was essential to avoid impacting ongoing event operations, according to the team submission. During the expansion project, there were no disruptions to event-related activities, including installation by the U.S. Army Corps of Engineers of a COVID-19 emergency vaccination facility in the existing Javits center.
“During the shutdown of the pandemic, we switched to a lot of web-based collaboration, but the intensity stayed there for all of us,” Murray says. “Everyone brought their skills in the room and left their egos outside the door. We were all about getting the project to a successful delivery.”