Power giant Duke Energy is getting down and dirty as it spends more than $2 billion to upgrade its Cliffside Steam Station, in rural North Carolina, with advanced clean-coal technology. The builders attribute much of the job’s success to date to a collaborative team approach and a strategy that involves site preassembly of powerplant components.
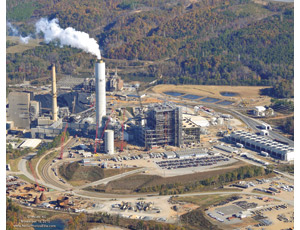
“The fabrication and preassembly performed onsite are a significant element of the project’s success,” says Bobby Smith, project director for The Shaw Group, the Baton Rouge, La.-based engineer and contractor.
Smith estimates 20% of total direct work hours were performed in a staged fabrication area. “This allowed the project to work many parallel activities in a safe and efficient manner, and ultimately reduced the project schedule risks,” he says, adding that Shaw had completed 10 million safe work hours as of January.
Construction of the $1.8-billion, 825-megawatt Unit 6 is taking place on a sloped site straddling Cleveland and Rutherford counties in North Carolina. The project has required blasting and excavation of an estimated two million cu yd of material, according to Shaw.
To complicate matters, truckers have had to haul loads of soil, rock and other deliveries across active rail tracks, timed between the plant’s coal deliveries. One of the rationales for site preassembly is to ease traffic flow in and around the project, says Smith. There are approximately 1,700 workers on site and all laydown space is located outside the rail loop.
For instance, crews preassembled ductwork, and three main girders that carry the weight of the boiler.
“The girders were shipped in multiple sections and required thousands of bolts and welding to ready them for placement,” Smith says. Other preassembled components included the front wall for the boiler furnace, portions of each baghouse and fiberglass flue sections.
Duke took steps to accelerate the project, too. To speed coal cars in and out of the plant, the company upgraded its unloading facilities from a system of rotary car dumpers to a faster bottom discharge system.
Duke and Shaw began their collaboration 15 months before construction got under way, in January 2008, when they developed an integrated team to address conceptual design, specifications, quantity estimates and open-book pricing, instead of using a fixed-price engineering, procurement and construction contract.
“It’s a fairly unconventional approach, but it has resulted in faster, more efficient problem resolution,” says Michael Pollack, Duke’s assistant project manager.
Shaw’s Smith adds that the process “reduces risk for both parties.”
The payoff for these efforts could be substantial. The work will double the plant’s generating capacity, and remove 99% of sulfur dioxide emissions, 90% of sulfuric acid mist, 90% of mercury, and 99.9% of hydrogen chloride and hydrogen fluoride.
The unit has been built to accommodate installation and operation of future carbon-control technologies, says Duke, which received $125 million in federal tax credits for the project. As a condition of its permit from the North Carolina Dept. of Environment and Natural Resources, Duke will retire four of its 1940s-vintage coal-fired units by 2011, as well as 800 MW of additional generation at other locations by 2018.
Increased Efficiency
Duke’s approach to clean coal at Cliffside boils down to building a more efficient—and agile—plant.
Unit 6, which will increase Cliffside’s output by 80%, from 760 to 1,360 MW, features a pulverized coal boiler unit with spiral water-wall technology. Tubing carrying water inside the boiler will run in a spiral design, instead of vertically, for more efficient heat transfer.
The plant’s new pulverizer, boiler, fans, ash handling and air-quality control system will allow Duke to burn coal with different burn characteristics without major modifications. To further enhance emissions performance, Duke installed a $380-million scrubber system on its existing Unit 5, a 562-MW, coal-fired generation unit. Unit 6 will share that equipment and chimney.
“The individual components are not unique,” says Pollack. “What is unique is the way we have integrated them into a single air-quality control system.”
This system also reuses scrubber wastewater in the spray drier absorber, “essentially eliminating wastewater discharge,” says Sam Alexander, Duke’s project manager. The wastewater is evaporated and particulate matter is captured in the fabric filter.
Another benefit comes from use of the existing river intake structure. New pumps will siphon water from the old facility for the plant’s water requirements. Duke says the amount required to cool the plant will ultimately decrease from 420 cu ft of water per second to 50 cu ft per second. “We saved a lot of cost and eliminated the need to go through another permitting process,” Pollack says.
Article toolbar
Post a comment to this article
Report Abusive Comment