As the water utility for more than 1.5 million people in Colorado’s largest metro area, Denver Water is responsible for 20 dams, what will soon be four treatment plants, 3,000 miles of distribution pipe and other infrastructure. Maintaining all that, replacing lead service pipes and meeting current and future needs for its customers is a significant undertaking, with more than $1 billion of work now under contract.
Robert Mahoney, Denver Water chief engineer, says the utility uses a 10-year infrastructure master plan to help prioritize projects. The utility also uses several different project delivery methods—design-bid-build, design-build, construction manager at-risk and construction manager/general contractor—depending on the complexity of work and how much the prime contractor will self-perform.
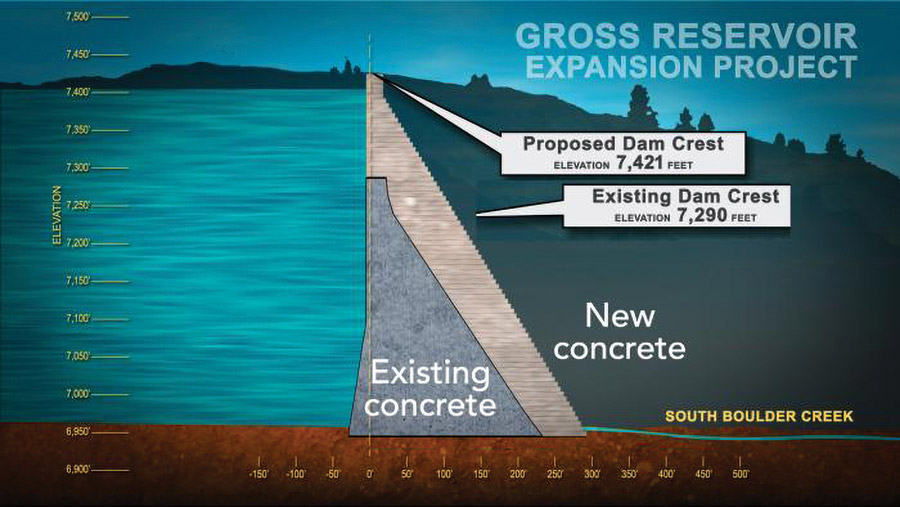
The Gross Dam had been designed with future expansion in mind, but the 131-ft height increase is even higher than the original engineers envisioned.
Denver Water has also found cost and time savings in design by publishing its engineering and capital projects construction standards online. The move has helped shrink design books, which included a lot of standardized material being redesigned unnecessarily. Knocking down plans and specifications to be project-specific saved 1 million sheets of paper in the first year, according to Mahoney. The utility’s standards have been used in 47 states and 23 countries, he adds.
“If you’re going to pour a thrust block on a pipe, you don’t have to redesign it every time,” he says.
Careful planning has helped Denver Water achieve a less-than-1% change order rate based on the contract value, Mahoney says, but that doesn’t mean contractors are being left to eat unexpected costs that arise during a project. The key is to “go ugly early” when a problem is discovered, he adds, by addressing any potential issues as soon as possible.
Mahoney emphasizes the importance of partnering with contractors. He maintains involvement with his projects—using what he calls a “half-minute meeting” to check on the scope, schedule and budget of each.
“When we negotiate contracts, we say, ‘This is where you’re going to make money on this markup. You’re not going to have individual profit centers, like marking up your trucks or whatever,’” Mahoney says. “So we say, ‘Let’s agree on where you’re going to make money and where you’re not.’”
The approach makes sure contractors “don’t have hidden profit centers and are not trying to pull one over on us,” he points out. “What we want to do is preserve the opportunity to make profit in a fair way.”
That attitude has helped advance projects such as Denver Water’s renewal of its north system, one of its two raw water sources and a key piece to ensure system resilience and provide for future demand.
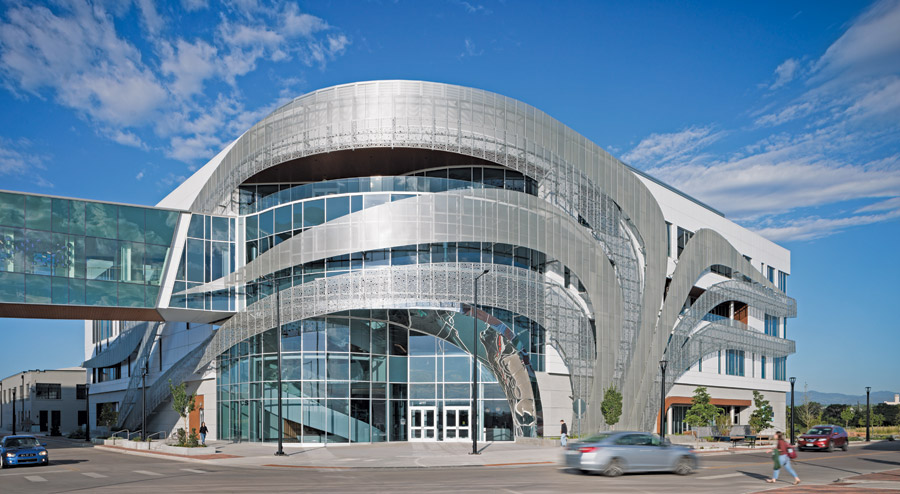
Denver Water collaborated with Colorado State University on the Hydro building at the Spur Campus. The structure houses a water quality laboratory.
Photo courtesy of Denver Water
Northwater Treatment Plant
The largest part of the north system renewal is construction of the $520-million Northwater treatment plant to largely replace a facility built in the 1930s, according to Peter McCormick, plant program manager. The new plant is due to come online this spring with planned capacity to treat 75 million gallons of water per day—close to 20% of Denver Water’s potable water consumption on an annual average basis, he says.
The plant includes its own hydroelectric power thanks to the nearby Ralston Reservoir, and it was designed to be off-grid, although Denver Water ultimately decided to connect to the grid, allowing it to be a net producer of power, Mahoney says. The HVAC and electrical loads are reduced by burying the buildings. The plant received Envision Gold certification.
Part of what’s unique—and fun—about Denver Water, he adds, is how it makes major decisions through the lens of current service agreement requirements while incorporating flexibility for future decision-makers. Northwater was designed to allow sustainability features to be added or expanded.
“We try to provide as much flexibility as we can for the decision-makers down the road.”
—Peter McCormick, Plant Program Manager, Denver Water
“We try to provide as much flexibility as we can for the decision-makers down the road,” McCormick says.
Geological conditions at the site provided some surprises for the project team. Bedrock in the area is tilted 90° in some places, and at one point an old coal mine in the planned project area was discovered, McCormick says. Those conditions were found early enough for the facility layout and location to be redesigned. The team has also faced long lead times for some equipment and continued work through the height of the COVID-19 pandemic without any outbreaks on site or delays. The project is under budget and on schedule.
Travis Baumgartner, treatment plant project director for construction manager at-risk Kiewit Corp., says that Mahoney “set the stage early that it was going to take a true partnership to make a job like this successful.” When dealing with obstacles, there was an unusually high level of collaboration.
“Working through those issues, as a partner, along with everybody else, really allowed us to get through them with minimal impact,” Baumgartner says.
McCormick attributes the project remaining on schedule to Mahoney’s leadership and the willingness of Denver Water contractors to partner for success.
“The goal is really to make sure that outside firms want to work with us,” he says. “The nature of the work they will do is generally one of a kind in terms of the infrastructure we own and its scale in the region.”
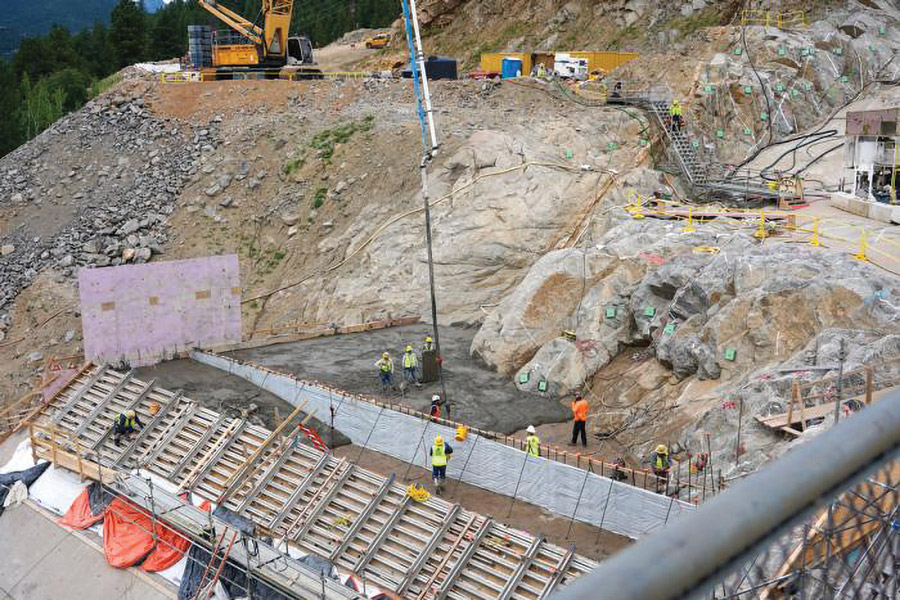
Crews excavated and strengthened areas where the elevated dam will sit.
Photo courtesy of Denver Water
Gross Reservoir Expansion
Kiewit is also working for Denver Water in a CM-GC joint venture with contractor Barnard on the $531-million Gross Reservoir expansion project. Chris Loeffler, Kiewit project director for that job, says Mahoney and the Denver Water team were serious about partnership from the start with honesty and transparency.
“I think they have done a very good job of aligning risk with client and contractor,” he says. “The spirit of this model is partnering.”
The project is elevating the height of the 1950s-era Gross Dam from 340 ft to 471 ft with a downstream buttress raise. It is the world’s largest dam raise to use roller-compacted concrete, about 725,000 cu yd, that would result in Colorado’s tallest dam.
Denver Water’s history of future-minded planning goes back far enough that the dam’s original engineers designed it in a way to allow for expansion, although the 131-ft raise is higher than they had envisioned.
The taller dam would nearly triple Gross Reservoir’s capacity to 119,000 acre-ft of water from 41,000 acre-ft. The project is important because Denver Water’s north system, of which the reservoir is part, accounts for just 10% of its storage capacity. Jeff Martin, Gross Reservoir expansion program manager, says the added capacity will help improve the system’s resilience in the face of climate change and future demand.
Felipe Garcia, senior principal at Stantec, the engineer-of-record on the project, says Denver Water used a “zipper plan” in which every design team member technical lead had a counterpart on the owner’s side.
“It really helped disseminate our engineering decisions deeper into the Denver Water organization,” he says. “Because they had the chance to digest it early on, as we were going through the analysis and design process, they were completely up to speed.”
Work started in 2022 and has focused so far on preparing the existing dam and surrounding area for the roller compacted concrete (RCC) structure to be placed downstream and on top of the current crest. Hydrodemolition was used to roughen the dam surface for better adherence to the new concrete. About 250,000 cu yd of rock was “surgically removed” with blasting within 30 to 40 ft of the dam and 500 ft up on cliffs for the future footprint, Martin says, adding that the foundation was grouted with a slurry of water and cement to make it less permeable, ensure no water seepage under the dam and reduce hydrostatic uplift pressure.
Martin says the team discovered some surprises in the rock along the way but planned ahead with different alternatives to use depending on conditions.
“Our team really strove to minimize any lost time or downtime by having a menu of choices,” he says.
The next stage of work is concrete placement. The team recently celebrated completion of the first stage. Mahoney says taking time to mark milestones in a project of this scale helps keep workers engaged for bigger challenges ahead.
“Now they’re reenergized,” he says. “Because it’s a 24-hour push that’s coming up.”
Starting in May, the plan is to begin 24/7 RCC work to raise the new section 300 ft this construction season. The team set up an on-site concrete batch plant along with a conveyor system to move the new concrete to the crest of the spillway.
Round-the-clock placement will be needed for quality. While “fast” and “quality” may not normally go together, Martin says that is the case when using RCC.
“The faster we place it, the higher quality we get,” he says.
Work will continue until some time in the fall when overnight temperatures get too low to work with concrete.
Post a comment to this article
Report Abusive Comment