A dilapidated warehouse with structural and foundation problems in the Melrose section of the Bronx isn’t the typical setting for an uplifting construction story. But the transformation of a 99-year-old building from dangerous eyesore to home of the LaGree Baptist Church—a modern, 31,000-sq-ft church, community hub and commercial tenant space—has become an inspirational journey. Repurposing the three-story wood-framed structure—an effort led by BDB Construction Enterprise as contractor and Body Lawson Associates Architects and Planners as architect—not only is relocating an active congregation from its Harlem base, but also providing Melrose with a new economic engine via four new tenant spaces for professional and retail businesses.
Creating a multiuse development out of a badly out-of-code building—most recently used for light manufacturing and a car repair outfit—required an extensive overhaul of structural systems, says Tallal Bhutta, CEO of BDB Construction.
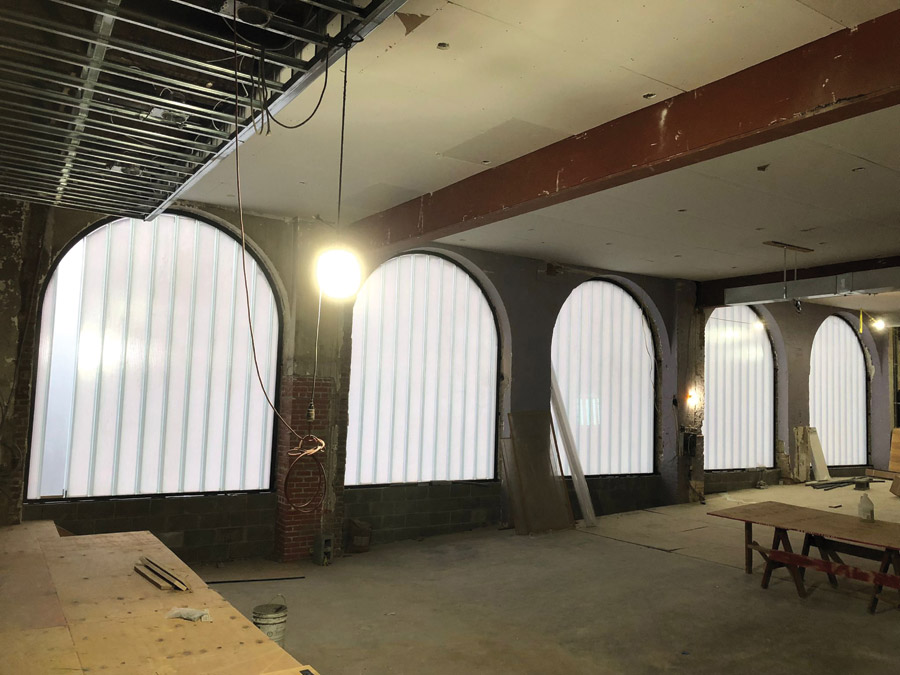
The project team installed Pilkington arched insulated glass panels along the street-facing wall of the sanctuary.
Photo courtesy BDB Construction
“The whole building had irregular construction, and many elements were not properly recorded,” he says.
The team had to address major deficiencies, including repairing and reinforcing existing columns for greater load capacity, shoring up a crumbling roof, bolstering floor decks to allow new cuts for stairs and elevators and repairing the foundation, Bhutta says.
Little of the structure was suitable for preservation, says Victor Body-Lawson, principal of Body Lawson Associates. “It was a gut renovation,” he says. “There was structural damage—the floors were not aligned, the roof was falling apart. We did a lot of structural surgery and intervention—a lot of steel, new wood—to [accommodate] the new church.”
But the project had to incorporate much of the skeleton and footprint, requiring careful demolition and adaptation of the existing structure, Body-Lawson says.
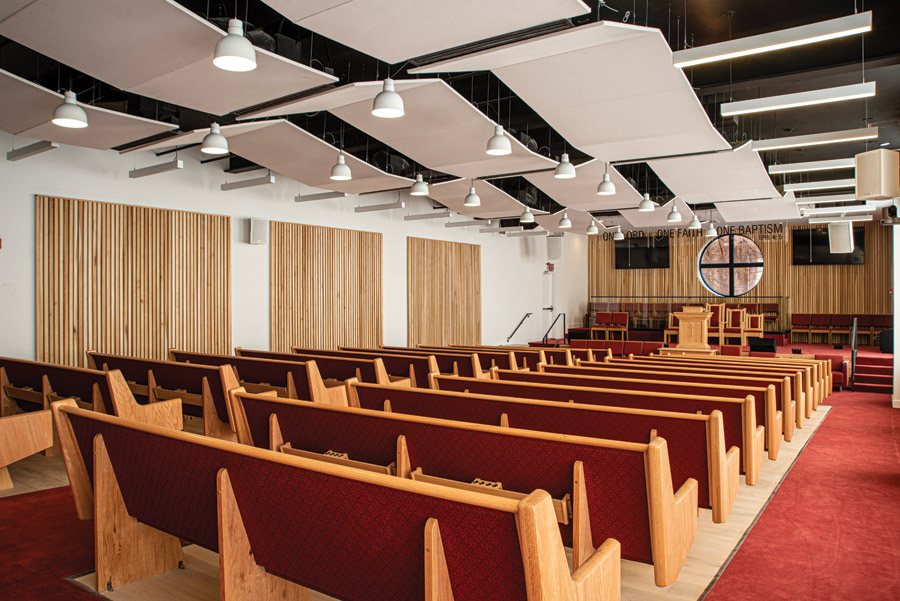
The team brought in sturdy new elements—steel beams to support the roof deck, reinforced columns and foundations, C-shaped steel joists and concrete for the floor decks to support new stair and elevator openings and structural steel for a sloped floor in the 2,140-sq-ft main sanctuary.
Photo by Erik Rank, courtesy BDB Construction
“A retrofit project always faces size constraints,” he says. “It’s not a tabula rasa.”
The team brought in sturdy new elements—steel beams to support the roof deck, reinforced columns and foundations, C-shaped steel joists and concrete for the floor decks to support new stair and elevator openings and structural steel for a sloped floor in the 2,140-sq-ft main sanctuary, Bhutta says. All of that took place on a tight 10,000-sq-ft site with no laydown area, he adds.
“It was a gut renovation.”
—Victor Body-Lawson, Principal, Body Lawson Associates
“We had to be very creative with a lot of equipment,” he says. “We had our boom trucks deliver the steel beams onto the site. Then we used lifters to manually install them in sequence, one by one. It was very meticulous.”
The LaGree Baptist Church purchased the South Bronx site in 2018, having already sold its former Harlem property and having moved into a rented space. But early on, church leaders sought to reduce their rent burden and asked the project team to carve out a temporary home in the Melrose building. That sparked an early redesign—making one of the first-floor commercial tenant spaces into a temporary sanctuary and office. The program shifted to that work in 2019, but still required weatherproofing to secure the building envelope and repair roof sections. That included constructing a reinforced concrete and rebar water retention tank in the cellar to collect stormwater drainage, Bhutta says.
The church moved into the temporary space just before the pandemic, Body-Lawson says.
“We built the project in two phases—first to get them into the temporary worship space, then to build the permanent space,” he says.
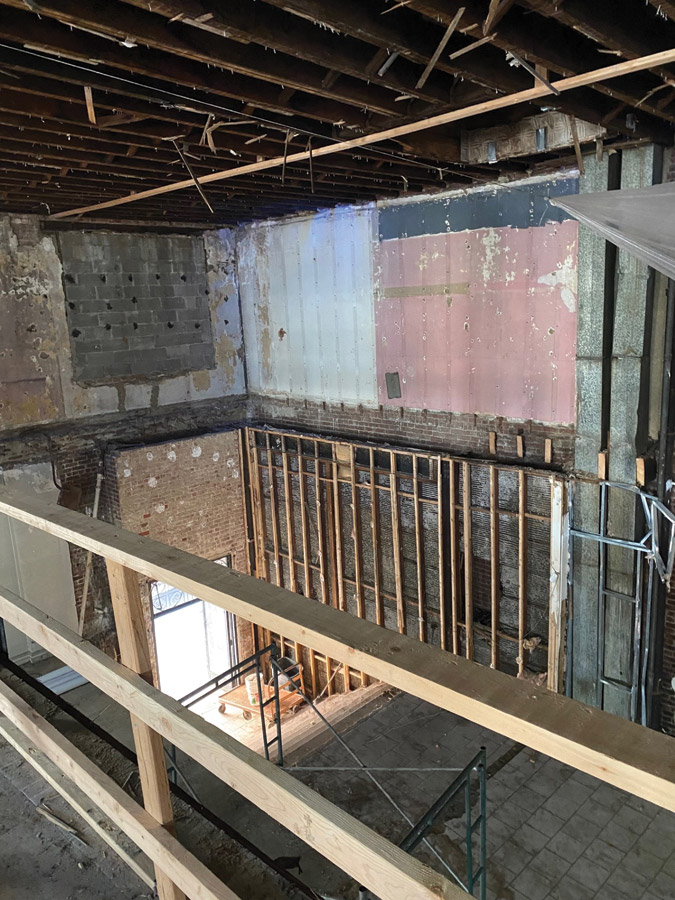
BDB Construction cut openings in the existing floor structures for the addition of new elevators and stairs.
Photo courtesy BDB Construction
The permanent features include the lobby and 211-person main sanctuary on the first floor along with church offices and an 1,890-sq-ft fellowship hall accommodating 152 people on the second floor. The hall has kitchen facilities and functions as an overflow space for worship services. The congregation also has access to a green rooftop deck for outdoor events, and there is a basement, which will house a youth ministry and storage space. The roof, cellar and fellowship hall can also be available for community events. The building also has three storefront retail spaces on the first floor as well as a 7,000-sq-ft commercial space on the third floor for a larger organization, such as a school or medical office, Body-Lawson says.
“These are uncertain times for churches, with attendance impacted by the pandemic,” he says. “With new designs, we try to get them other income sources that can make them more sustainable organizations over time.”
The construction phase brought challenges, including price hikes from the supply chain crisis and inflation. There was also a surprise: church leaders asking for a larger sanctuary stage after it was built. Original renderings did not give them a true sense of the stage’s size, Bhutta says.
The project team had already shifted columns and installed long-span beams to accommodate a 34-ft clear span for the sanctuary. To address the concern, members took a separate space for the baptismal font and incorporated it into the stage design to make it slightly larger. The work required replacing and adding joists as well as removing a wall, Bhutta says.
“With new designs, we try to get [churches] other income sources that can make them more sustainable organizations over time.”
— Victor Body-Lawson, Principal, Body Lawson Associates
While the bulk of construction took place in 2021, lower church attendance driven by the COVID-19 pandemic spawned delays in later stages across 2022 and 2023. Most work is now complete, with a temporary certificate of occupancy expected later this spring and final completion in summer. Work remains for the roof and outdoor parking area, including adding concrete pavers, railings and waterproofing. The building also got an injection of new systems and utilities, Bhutta says.
“There were no fire-life safety systems in the facility,” he says. “We had to bring in new waterlines for the sprinklers, bathrooms and domestic use [as well as] new standpipes.”
The team also installed a 2,500-amp electrical system and wiring, HVAC mini-splits, heat pump units, electric heaters and the two elevators, Bhutta says.
The team preserved original elements on the exterior, restoring Renaissance-Romanesque features such as large arched windows on the first floor, Body-Lawson says. Previous owners had closed them up, requiring extensive effort to unblock and reframe them and install channel glass, he adds.
The team also painted the facade, railings and other features red, Bhutta says. “We brought the building back to its past character,” he says.
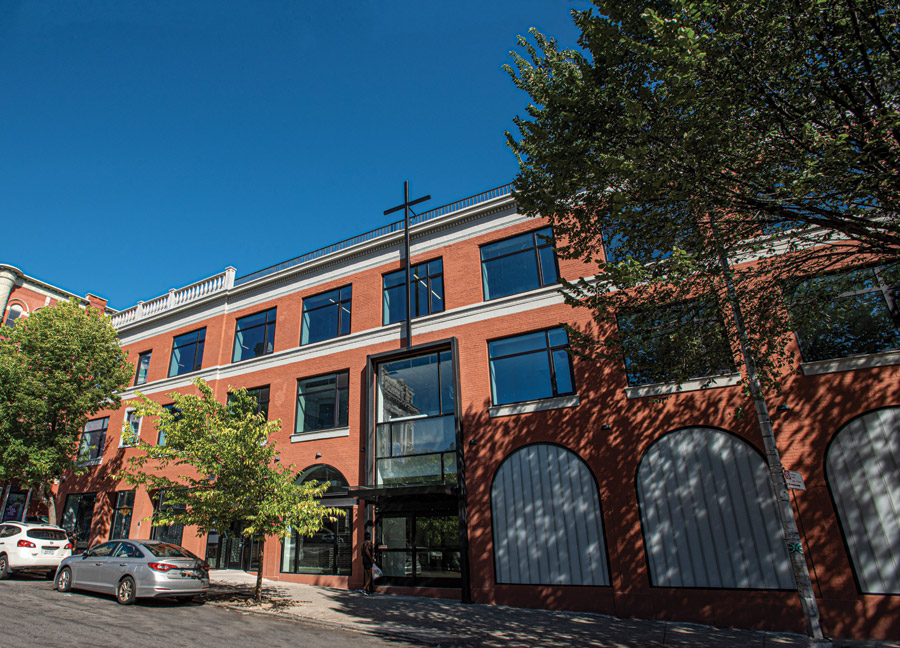
Most work is now complete, with a temporary certificate of occupancy expected later this spring and final completion in summer.
Photo by Erik Rank, courtesy BDB Construction
Another signature feature is the sanctuary’s industrial-style ceiling system, which has aesthetic and functional purposes, Body-Lawson says. The project team wanted to allow access to mechanical systems, leaving those elements partly exposed on the ceiling, but they camouflaged the ductwork and pipes, painting those items black and hanging white floating “cloud” panels below them.
The angled 4-ft by 8-ft panels offer not only an acoustic boost, combining with wall panels to bounce sound off the stage into the pews, but also a dash of visual flair, Body-Lawson says.
“They create this plane,” he adds. “All you see is the clouds.”