Although most mass timber projects are hybrids of a sort—boasting a steel or concrete lateral system—Cincinnati Public Radio’s (CPR) new $32-million headquarters in Evanston is something of an anomaly.
The 35,000-sq-ft structure’s lateral system is composed of cross-laminated timber (CLT) shear walls, creating a building with a superstructure almost entirely composed of mass timber, explains Dean Lewis, director of mass timber and prefabrication at Skanska, the project’s construction manager.
“The entire column and beam structure, second floor, roof structure and a selection of interior shear walls and exterior perimeter walls are made from mass timber,” he says.
Upon completion in early 2025, CPR’s new home for 88.5 WMUB, 90.9 WGUC and 91.7 WVXU will become the first two-story mass timber building in both Cincinnati and the Midwest region.
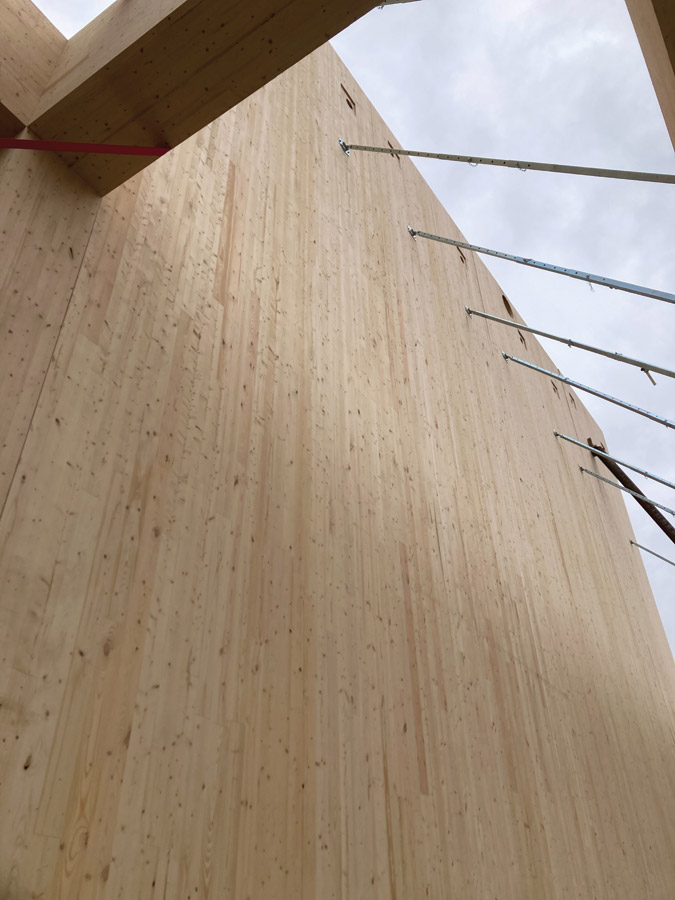
Nearly the entire project is comprised of mass timber, including some of the interior shear walls and exterior perimeter walls.
Photo courtesy of Skanska
In addition to serving as a sustainable resource, mass timber also leaned toward the owner’s desire for an iconic building that would be recognizable, welcoming and adaptable. However, given a mass timber system’s differences from the typical choices of concrete or steel, the design team worked carefully to find the optimal structural bay, explains Adam Luginbill, senior project architect at emersion DESIGN. This enabled the team to maximize the potential of the CLT panels and keep them at a reasonable thickness while also minimizing both the size and quantity of necessary beams.
Delivered under a CMAR with GMP contract, the 35,000-sq-ft facility features two on-air studios, two more for interviews and one for performances, along with 11,000 sq ft of office space. A free use podcast booth will allow anyone in the community to record their own content, while outdoor gathering and performance areas will provide a range of programming, such as concerts, educational programs and receptions.
Planning began in 2018, with emersion DESIGN and Skanska already on board, but the COVID-19 pandemic obstructed CPR’s fundraising efforts.
“As a nonprofit, CPR had to have the funds to construct the building, which is the biggest project in the history of their stations,” explains Richard Eiswerth, president, general manager and CEO of CPR. This effort also marks the first traditional capital campaign in CPR’s more than 60-year history.
Although the owner considered more than two dozen sites and the possibilities of both ground up construction or renovating an existing space, the station decided on a location in the diverse and growing Evanston neighborhood that CPR can invest in and give back to, Eiswerth says.
The site, which was formerly a parking lot, also borders Evanston Park, a public space where the station plans to host concerts and other events.
“The building is meant to feel integrated with and complement this public space,” says Nikki Goldstein, design architect at emersion DESIGN. “Visually, it is a simple pavilion with transparent exterior walls. But constructing a building that appears simple is often a complex endeavor. The execution of glass walls and exposed structure is critical to its success—there’s no place to hide imperfections in a simple structure.”
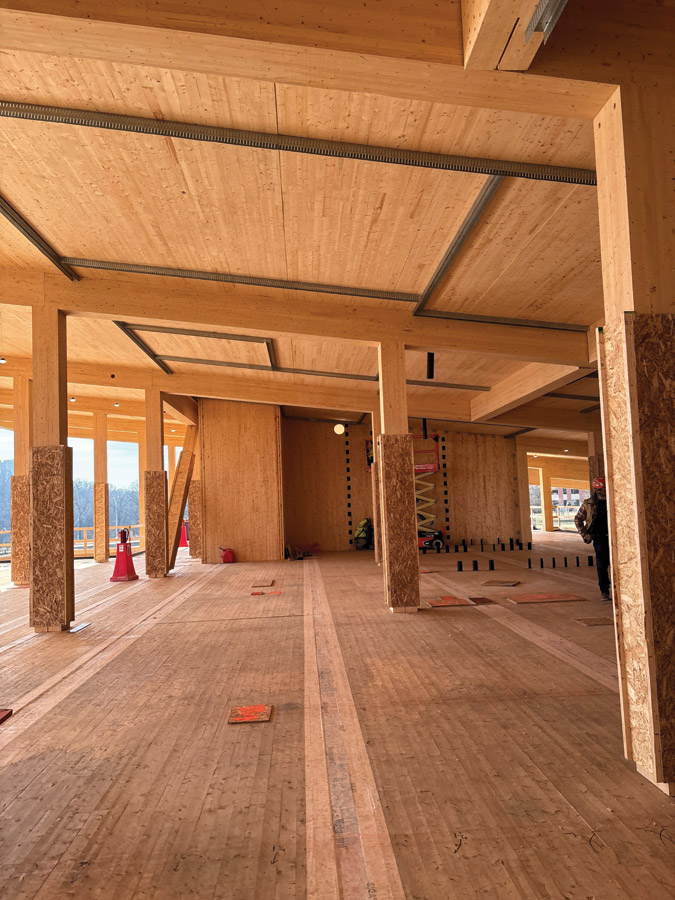
To safeguard interior mass timber elements, temporary protection was installed on all columns, from the slab up to 8 ft off the ground.
Photo courtesy of Skanska
Rapid Rise
From construction’s start in September 2023, work has quickly progressed. Building erection began in November and after just 34 working days, Skanska’s crews installed the 498 panels that comprise the shear walls, wall and floor panels, columns, beams and roof panels—the final roof panel was set on Dec. 22.
Since mass timber arrives ready to assemble—delivered with the help of 28 trucks—extensive coordination was vital before fabrication even began. Early engagement and a partnership with mass timber manufacturer Nordic Structures also helped ensure the CPR project had a production slot that aligned with its schedule, explains Jeff Smoker, project manager with Skanska.
“As a nonprofit, CPR had to have the funds to construct the building, which is the biggest project in the history of their stations.”
—Richard Eiswerth, President, General Manager & CEO, Cincinnati Public Radio
From there, BIM coordination served as a critical tool toward ensuring that both timber erection and system installation would proceed smoothly.
Although the structure has topped out, much of the building’s interior mass timber elements remain exposed, so preserving those structures while work progresses all around has proven challenging.
“Skanska rushed to install the roof and purchased a complete RWES [reusable weather enclosure system] for the exterior of the building in an effort to minimize the impact of moisture on the finished product,” says Dustin Hopkins, superintendent with Skanska. “The construction team has had to do a lot of tasks differently because of the finished wood. Tasks such as layout and material cutting stations all needed to be well coordinated so the wood is protected. Temporary protection was also installed on all columns from the slab to 8 feet off the ground.”
As an alternative to a traditional reinforced plastic wall system that would be thrown away at the end of a project, the RWES “installs quicker, performs better in high winds and rain, and can be folded up and sent to the next project,” he says. “The product can also be cut into custom sizes for sloped roof applications such as at CPR or to sequence with the install of exterior skin and curtain wall.”
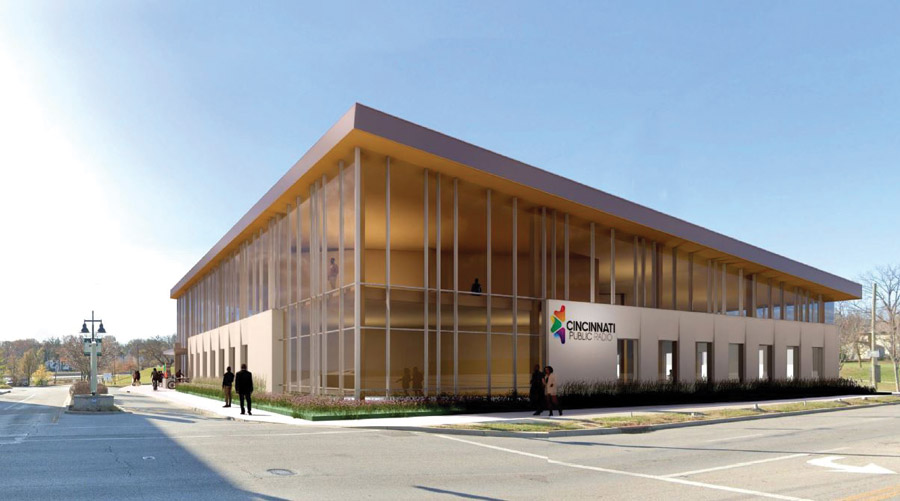
Although it will appear as a simple pavilion with transparent exterior walls, Cincinnati Public Radio’s headquarters will feature recording facilities housed within an environmentally friendly building.
Rendering courtesy of emersion DESIGN
Sound and Sustainable
Balancing the building’s function with an iconic design has been another challenge. It would have been “quite easy to make the acoustical aspects what they are and to lose the aesthetic of what the building could be,” Hopkins notes. “But we were able to make the final building both aesthetically pleasing while meeting the acoustical requirements that a studio needs.”
The facility’s studios were designed with solid CLT walls, and each one is acoustically isolated with a box-within-a-box design. Meanwhile, the floors feature a structural slab topped by a floating acoustical slab. Neither the framed walls nor ceilings touch the building structure and all penetrations were sealed as well.
“Where there are windows, in addition to the exterior glazing, there is a layer of 1-inch-thick laminated glass in the decoupled interior wall,” Luginbill says.
During design, architectural acoustic consultant WSDG actually recorded traffic noise from the site to simulate how it would sound in both the studios and boardroom that would sit next to the road, he says.
“The radiant heating and cooling meant that ductwork could be largely eliminated from the areas with exposed structure.”
—Adam Luginbill, Senior Project Architect, emersion DESIGN
Sustainability and occupant health were both owner-initiated priorities as well, with a LEED Gold target set early in the design process.
“In addition to specifying low-emitting materials, there will be indoor air-quality testing at the conclusion of construction. The use of natural materials, primarily the exposed mass timber, and daylighting are intended to improve occupants’ well-being,” Luginbill says.
In line with a design that aims to highlight the building’s very structure, the column grid is exposed. But anywhere there are partitions, they’re pulled back from the columns so the structure remains visible, Goldstein says. The stairs were also strategically located to display the CLT shear walls. Enclosed spaces were pulled away from the glass on the second floor, creating an open office environment.
However, integrating building systems within such limited closed space required careful management and a bit of creativity.
“The design team concentrated ductwork, plumbing and cable trays into the core of the building so that the areas around the perimeter, with exposed structure, would be as clear from visual obstructions as possible,” says Luginbill, adding that any systems within exposed areas were kept as unobtrusive as possible.
But these constraints were also inspiring, as was the case with the building’s HVAC system, which uses radiant heating and cooling, suggested by MEP engineer CMTA.
“Since the program demanded acoustical control, the design team recognized that this would mean a well-sealed envelope and that humidity within the building could be tightly controlled,” adds Luginbill. “The radiant heating and cooling meant that ductwork could be largely eliminated from the areas with exposed structure, and its energy efficiency contributed to the sustainability goals.”
In fact, the only ductwork anywhere in the building is solely for outdoor air supply and exhaust, which is hidden in the building’s core. This system also eliminates recirculated air, helping improve air quality for occupants, who will be able to take advantage of the facility’s recording spaces and outreach programs once the building reaches completion next year.
In the meantime, crews are approaching the project’s halfway point as of mid-March, having already logged 17,500 trade hours with zero recordables.