They were on vacation, walking the dog, relaxing at home, attending a graduation. It was a peaceful Sunday, June 11. Then the calls began coming in: A section of Interstate 95 in northeast Philadelphia was on fire.
An 8,500-gallon tanker truck delivering gas to a local Wawa fuel station overturned and exploded while trying to exit northbound I-95 onto westbound Cottman Avenue at 6:32 a.m. The northbound half of the 104-ft-long welded steel I-beam bridge collapsed within minutes. The National Transportation Safety Board is still investigating the cause of the crash that killed the driver, Nathan Moody.
Video by EarthCam
While the investigation will take time, the reaction of Pennyslvania Dept. of Transportation (PennDOT) officials; state, federal and local agencies; and contractors and suppliers was swift. Personnel anticipating a Sunday off would spend the next 12 days in non-stop action to get traffic back on the crucial national artery segment, which carries 160,000 daily vehicles.
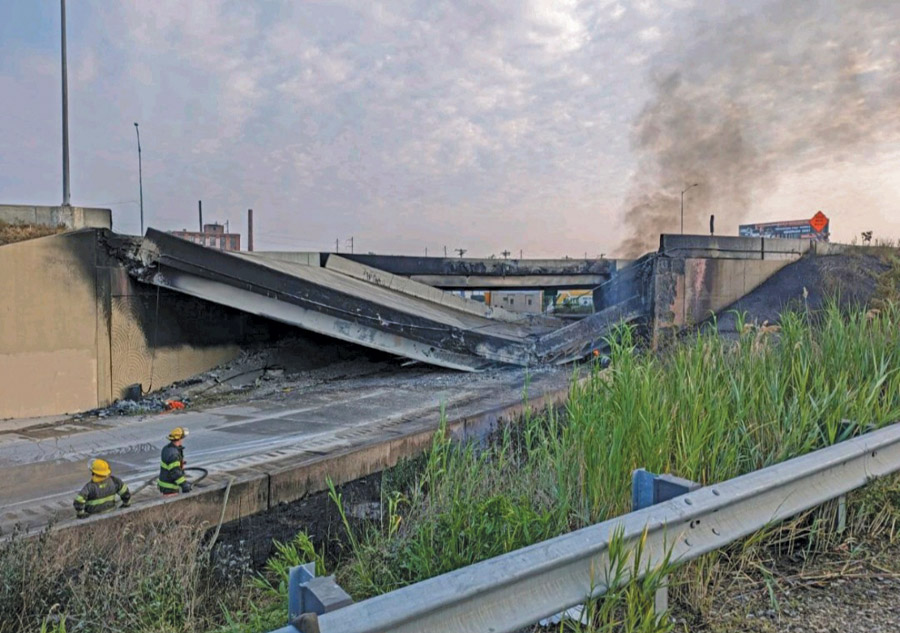
A tractor-trailer filled with gasoline lost control on June 11 and flipped on its side, setting an I-95 bridge afire and killing the driver.
Photo courtesy of Philadelphia Fire Dept. Twitter
Harold Windisch, PennDOT senior assistant construction engineer, recalls how numerous staff had to be called back “from wherever they were—from D.C. for a wedding, from New Jersey.” PennDOT secretary Mike Carroll activated his bridge inspection team.
Agency officials' first thought was whether the southbound lanes could be saved, says Windisch. Harry Laspee, vice president at engineering firm Pennoni, recalls that one option considered was to install temporary cribbing under the eight bridge girders. But by that afternoon, inspector AECOM determined that the girders had to be removed.
Din Abazi, PennDOT district bridge engineer, recalls waiting for the fire department to wash off the soot from the girders to take a closer look. In addition to the distortion, “I saw that in the northeast corner abutment the entire mat had expanded and popped the concrete face.” The heat had also damaged the elastomeric bearing pads.
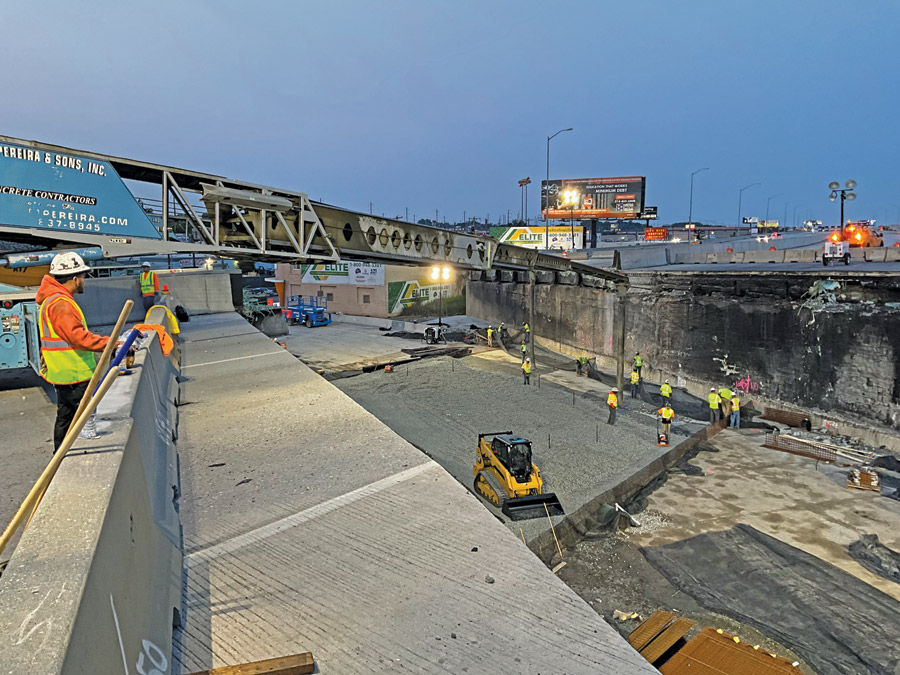
The team built a temporary road with wire walls and glass aggregate fill.
Image courtesy of PennDOT
The next step was to determine who would conduct emergency repairs. The answer: Buckley & Co., which PennDOT engineers knew had done repair work on its infrastructure after fires and floods. So the call was made to Robert Buckley, the Philadelphia-based firm's titular president. “We said, ‘Sorry to bother you, but this is an emergency. Please get down here,’” says Windisch.
Buckley, whose firm now is working on the permanent fix, is no stranger to emergency contracting jobs. But noting the wholesale engagement—from President Biden and the federal government to state Gov. Josh Shapiro (D) and his staff—he says “this is the first time I felt supported by everybody.”
The challenge was “working backward,” Buckley adds. “We had to find out what materials were available first, then design from there.”
Materials, it turned out, became available very quickly.
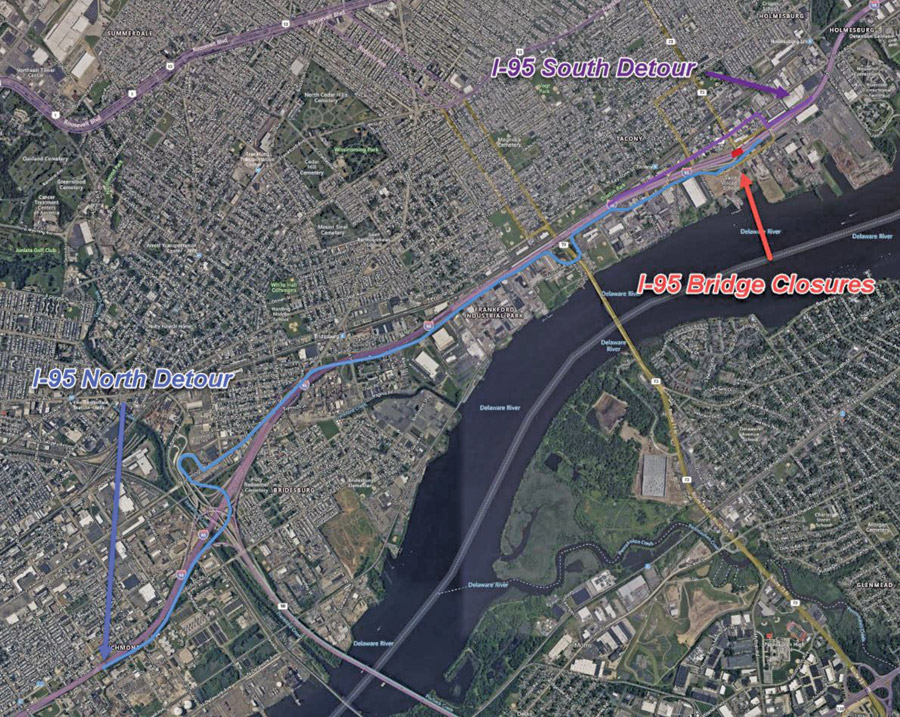
Carrying 160,000 cars per day, the damaged segment of one of the East Coast’s most congested arteries required detours around the crash site in the days following the fire.
Image courtesy of PennDOT
Clearing the Path
Peter Abbonizio, president of C. Abbonizio Contractors Inc., was watching TV when he got a phone call from one of his pump operators on a $60-million job to install a precast culvert sewer bypass some 40 ft deep for the city water department. The job includes rebuilding a ramp connecting I-95 and Cottman Avenue—right next to the bridge collapse.
He received a call from Windisch. “I got there around 9 a.m. We stood around figuring out what we needed to do. Around 1 p.m., PennDOT told us to proceed with the demolition of the northbound lanes.”
With two excavators and a crane on hand, crews began demolition within three hours and worked around the clock. By the night of June 13, demolition began on the southbound lanes. “We used cranes to take the steel down and hammers to get the concrete off,” he says. “It took 20 hours a day to get the thing done.”
“This is the first job where we had to do something so fast.”
—Archie Filshill, CEO, Aero Aggregates
While demolition commenced, PennDOT and Buckley had to decide what the temporary fix would be. The decision to close that section of highway was easier than if it crossed over another highway, notes Louis Belmonte, PennDOT District 6 executive.
A temporary bridge would be difficult due to the 57% skew and aging water facilities located beneath the Cottman Avenue ramp, says Abazi. So PennDOT turned to lightweight glass aggregate fill.
Joseph Sirignano, vice president at Benesch, which had been involved in the design of that very section of I-95 less than 10 years ago, was at his daughter’s graduation that Sunday morning. “I got a text asking, ‘Is this one of our bridges?’”
Consulting with PennDOT and the contractors, “we all came to the same conclusion: a temporary road with wire walls and the glass aggregate fill, which I’ve used on two other projects.” The aggregate, provided by AeroAggregates, has been used in 23 states and at the Philadelphia airport.
CEO Archie Filshill got the first call from Laspee, giving him a heads-up that PennDOT might come calling. They did. “Then Rob Buckley called. They realized an embankment would be the fastest way to open up I-95. But the utilities were the immediate concern; 20 feet of traditional fill would have been too much weight.”
Filshill had previous experience with such a situation, where “they realized there was a sewer line and you can’t put weight on it. There was a design change, and in six weeks we were providing the foam glass aggregate. But this is the first job where we had to do something so fast.”
Pulling from inventory and a plant in Florida, AeroAggregates shipped 8,000 cu yd in 85 truckloads starting June 15, receiving a state police escort. The next day, the first day of installation, “there was a torrential downpour. Buckley built right through that,” Fishill says.
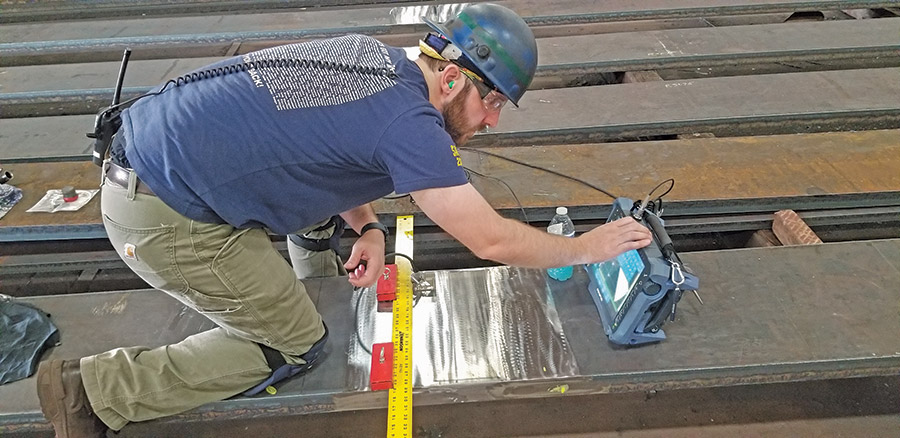
Permanent girders are being fabricated utilizing phased array ultrasonic testing.
Photo courtesy High Steel Structures
While Pennoni reassured the water department that its sewer lines were safe, AeroAggregates provided the design of the wall. “We had done a similar wall with Schnabel Engineering at JFK airport,” says Filshill. The dimensions were similar—20 ft high x 80 ft wide. “We used a high-strength polyester provided by Huesker,” he says. “Every 18 inches is reinforced. The facing is a temporary welded wire mesh.”
Earth Wall Products owns the design for the traffic barriers, or parapets, atop the wall. They have integrated moment slabs, eliminating the need to cast a separate moment slab. “We used 30 units, 15 in each direction,” says Austin Schollenberger, Northeast region sales engineer. “We had made traffic barrier units for a different PennDOT project. Since production is limited by the number of molds we have, our precast partner Atlantic American Precast will make units and store them at the yard.”
“We did scramble a bit,” recalls Mike Simmon, AAP operations manager. “We were producing barriers for another job. I got a text asking to reach out to Buckley.” The company shipped the thirty 8-ft-wide, 7.5-in.-tall, 13,000-lb. F-shaped sections diverted from the other job. “We loaded up five trucks for Monday morning and the second load by lunch,” Simmon adds, noting that they are the only moment slab-style barriers preapproved by the state.
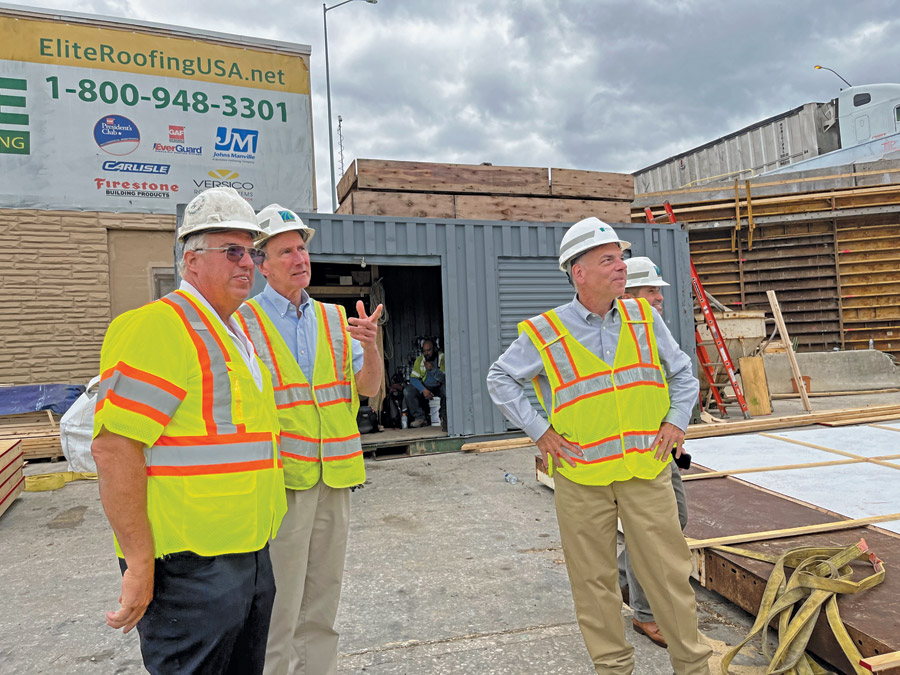
Buckley, Windisch and Belmonte survey construction progress.
Photo by Aileen Cho for ENR
Faddis Concrete Products provided bifurcated median barriers to account for gutter line grade differential between the northbound and soutbhound lanes, says president Austin Hess. On June 14, “specialty production molds were brought into the plant from storage and prepared for production,” says Hess. “Typical time for this type of barrier from initial request to final delivery would be 4-6 weeks for procurement, design and approval, fabrication and delivery.” The fifteen 12-ft-long, 5.3-ft tall, 2-ft-wide barriers were delivered in a week.
Nick Mercado, vice president of SJA Construction, was on vacation when he heard about the collapse. “I found out a couple days later that Buckley was considering us for the emergency paving work and concrete supply. Our biggest hurdle was determining when—we didn’t know how fast this was going to occur. Once the cameras were up and running, we had a better sense.” A crew began work that Wednesday night [June 14] until 4 a.m. They returned 11 a.m. Thursday. “Many workers barely got any rest, but every single one of them came back,” he says. The hot-mix asphalt paving completed that night, and lane striping could begin.
But with rain in the forecast, Carroll made a call to Poconos Raceway, asking to borrow a truck-mounted jet blower that a qualified driver could transport. With 3,000 lb of thrust, 16,000 rpm and blowing hot air at 1,400°F, “it keeps the asphalt dry enough to get the line striping done,” says Ricky Durst, Poconos Raceway senior director of marketing and analytics.
“Anyone I asked, they stepped up.”
—Rob Buckley, President, Buckley & Co.
High Steel Structures, working with steel mill Cleveland-Cliffs Inc., is fabricating the permanent steel girders, using phased array ultrasonic testing to test the welds. A fairly new technology, it cuts prodution time by about half and is safer than X-rays, says Ronnie Medlock, vice president of technical services.
“The governor gave PennDOT the authority to source the steel however they needed,” he notes. “It’s customary that shop drawings have to be approved by the owner’s engineer. We might wait up to eight weeks or more for drawings. But we got a day turnaround on these.”
Girders are anticipated to arrive on site by September. Crews will work from the outside edges toward the center, allowing three lanes of traffic to flow in both directions while the temporary fill is removed. Buckley anticipates completion by next spring.
“Anyone I asked, they stepped up,” he says. “Every one of those deals was on a handshake. We had no weak links, from the feds to the state to the police and fire department. I know all those guys, and I cashed in every favor I had.”
Post a comment to this article
Report Abusive Comment