Providing engineering services for the Houston Zoo’s Galápagos Islands exhibit was a challenge for two Walter P Moore engineers but a gratifying change of pace. “We were building [the exhibit] for the animals. We had to consider how they lived and their environment. There were so many things you don’t see in other designs,” says Ted Vuong, an infrastructure engineer and managing director of the firm’s civil engineering team in Houston.
Structural engineer and project manager Jessalyn Nelson describes working on the project as “really, really cool.” She continues, “We were always learning.… We had many conversations with the zoo staff who shared their knowledge about the animals and their habitat.” Many of those conversations required the engineers to think outside the box, they say.
From working in a 500-year floodplain to using materials deemed safe for animals, the engineering and design principles used in building retail space only applied partially to constructing a zoo exhibit.
The exhibit, which opened in early spring, highlights the delicate balance of an ecosystem. The Galápagos Islands, located off the coast of Ecuador, are part of an isolated archipelago home to various rare animals. According to the zoo, roughly 97% of reptiles and land mammals, 80% of the land birds and more than 30% of the plants found there are endemic. Most of the animals in the exhibit are closely related species.
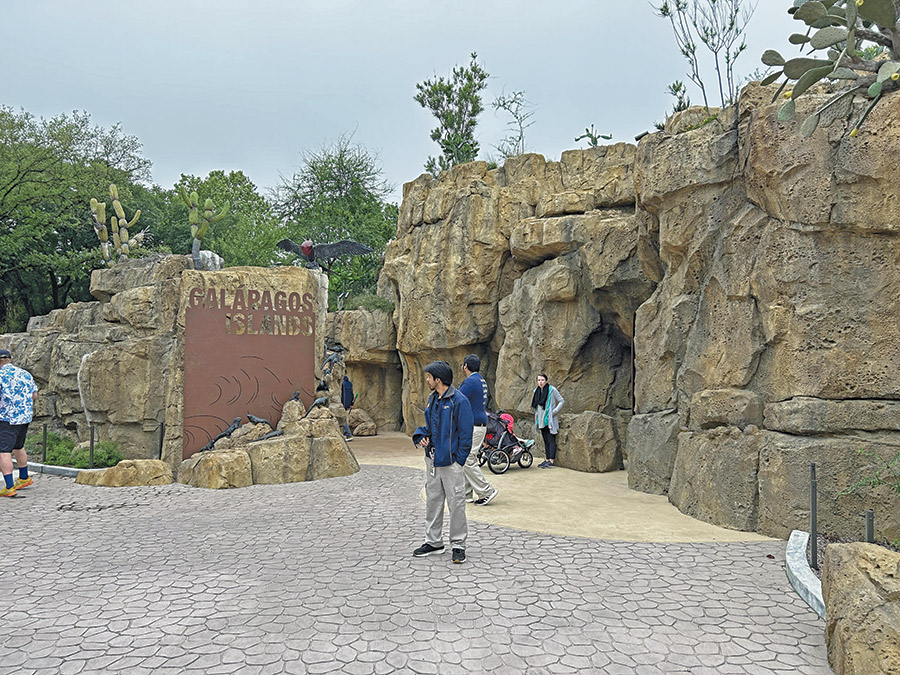
Image courtesy Walter P. Moore
Preserving the environment and surrounding conditions of the exhibit space was paramount to the zoo and the design team, says Vuong, adding that creative and outside-the-box thinking was necessary to overcome issues related to how to construct around 100-plus-year-old trees and ensure they not only survive but thrive as well as deciding how to create storage areas to accommodate detention in constrained and developed areas. The engineers used non-traditional stabilization strategies to construct pavement around the trees and incorporated low-impact design strategies throughout the zoo’s existing and new landscaped areas. These strategies reduced detention storage requirements and allowed traditional detention structures to be considerably smaller in size and cost, giving the zoo more programmatic options.
The state of the existing utilities also posed a major problem for the infrastructure engineering team. Vuong says many of the utilities were beyond their life, failing and undersized based on current codes. Much of the non-gravity utilities were installed in a spaghetti-like manner; over, under, shallow and with minimal clearance. Many areas had utilities that were difficult to locate and identify because they weren’t on any record drawings or as-builts.
It took months to solve the utility issues, he says. In the end, engineers created a graphical information system (GIS) cataloging all the zoo’s utility infrastructure. They designed new infrastructure with maintenance and access a key consideration by creating utility corridors and routing them outside of hazardous areas and difficult-to-reach or work areas.
Houston code changes also created a challenge for the engineering team. During the project, city leaders decided to revise its floodplain requirements. That led to a race against the clock. The team raised buildings 2 ft above the 500-year floodplain just in time to beat the clock.
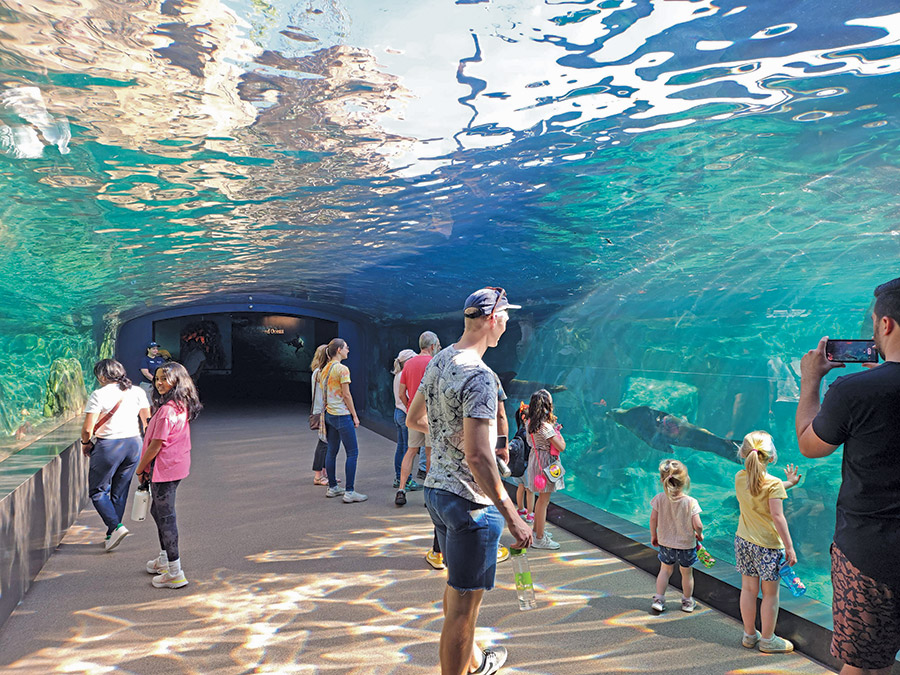
Image courtesy Walter P. Moore
“The Galápagos exhibit demonstrates how effective utility planning and phasing can successfully bring upgrades and modernize infrastructure that has been serving the zoo for decades. Simultaneous integration and implementation were critical to the zoo’s operations and their ability to serve the community,” Vuong says.
Nelson’s goal was to design a zoo that “didn’t consist of flat lines and straight plains all the time.… We had to come to each piece of the project with fresh eyes,” she says.
Since engineering a zoo isn’t an everyday project, her team was in forward-thinking mode; they continuously examined drawings, brainstormed and held in-depth conversations with the zoo’s staff.
A critical consideration was the zoo’s numerous aquarium tanks that contained fresh water, salt water and a mixture of both. Several different custom concrete mix designs were required for the different tanks. Careful material selection was important throughout the space to protect the animals from toxic exposure and avoid corrosion. This ranged from stainless steel precast connection elements to galvanized rebar and fiberglass-reinforced structural shapes.
“We built it how it needs to be built, not how we wanted to build it,” she says.
Nelson and Vuong’s part in the exhibit will remain a professional and personal career highlight. Nelson says it was a team build requiring close work with zoo staff and other engineers. The key to the project’s success “required a buy-in from all partners involved.”
The exhibit opened in the spring as part of the Houston Zoo’s $150-million Centennial Campaign. While the majority of the Galápagos Islands exhibit is complete, a few projects are still ongoing, the engineers say.
Post a comment to this article
Report Abusive Comment