The Juno Project
Toledo, Ore.
Best Energy/Industrial
Submitted By: Greenberry Industrial LLC
Owner: Georgia Pacific/Juno
Lead Designer: John Zink Hamworthy
General Contractor: Greenberry Industrial LLC
MEP Engineer: Voith/Meri
Subcontractors: Olsson Industrial Electric; Pacific Excavation; Pence/Kelly
The Juno Project is a commercial scale demonstration plant for a new recycling technology. Utilizing a proprietary process, Juno captures paper, fiber, nutrient rich water and metals from incoming municipal solid waste. These recovered commodities are then diverted to established recycling avenues for reuse. Since commissioning, the facility has processed more than 10,000 tons of waste, lessening the burden felt by nearby landfills.
Construction of the foundation and the steel superstructure required the installation of more than 1,000 aggregate piers for dewatering and stability. After the completion of the piers, 2,800 cu yd of concrete was placed. Surrounding areas were paved with fiber reinforced concrete to ensure resilience. Once the civil team completed the primary foundations, the structural team started erecting structural members.
The main construction contract was awarded on 90% design drawings. As the team worked to achieve 100% IFC drawings, changes and scope gaps became abundant. Biweekly meetings were held to discuss ongoing changes and value engineering options. Through honest and open dialogue the team stayed on the same page to deliver a one-of-a-kind solid waste diversion facility.
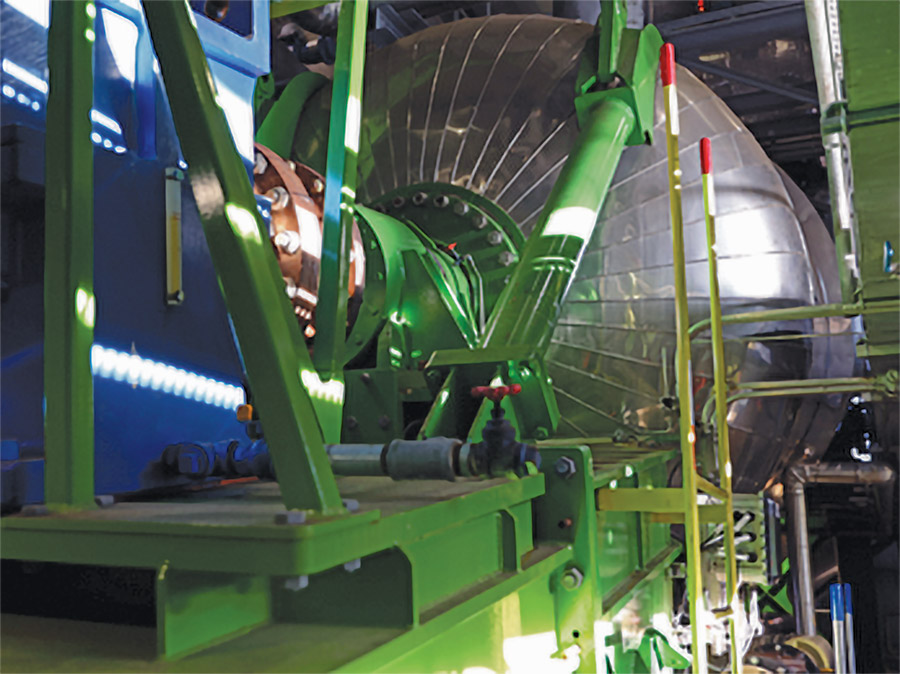
Photo by Franz Cosenza
By modeling the entire project within AutoCAD 3D and using plug-in applications, the project team was able to compress the overall site footprint and complete the facility in less than a calendar year.
Structural steel within a preengineered building also required innovation. Over multiple weeks, sub-coordination meetings proved effective to move the project forward. Priorities were mapped and transferred to Bluebeam markups that were handed out daily. These markups of photos and drawings depicted beams, columns, cable trays, purlins, etc. that were permitted to be installed.
The project team utilized just-in-time delivery. From civil to mechanical installations, all aspects were mapped and planned to allow expedited installations of equipment, including the 100-ton heart of the plant. The functionality of the new mill site required multiple utility connections. To achieve this goal, the construction team worked hand and hand with the client to coordinate tie-ins and install over one mile of conveyance piping.
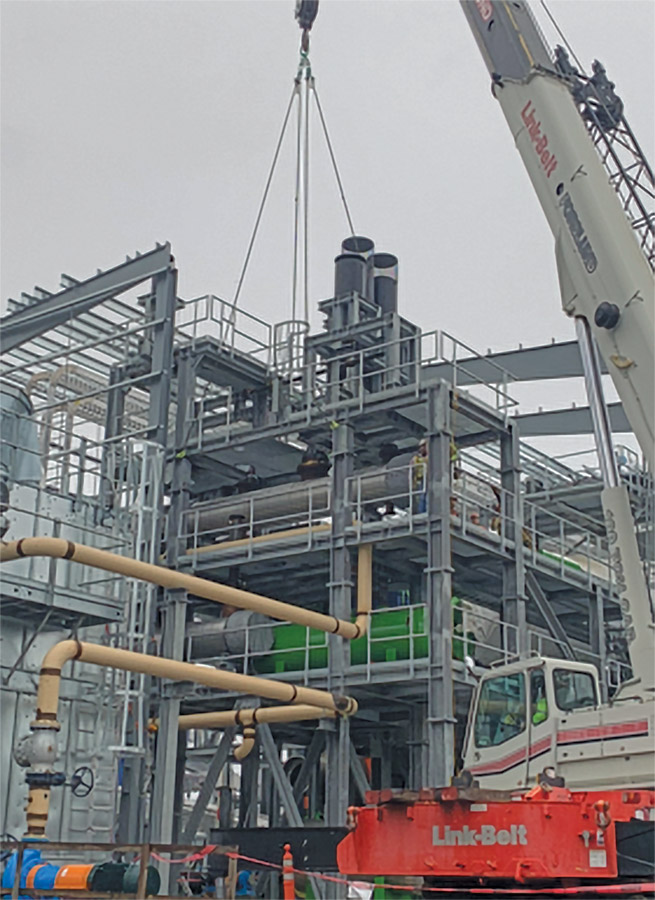
Photo by John Calhoun
Additionally, key equipment deliveries and standard material orders were held up due to labor shortages. This prompted the site management team to consistently adjust the schedule and pivot crews toward available work. PLC cabinets were installed while crews were waiting for electronics, and temporary pipe spools were installed to accommodate late inline instrumentation. Additional hurdles were faced when evaluating scope delineation.
Wildfire season was another challenge, with air around the project filled with soot and ash. Crews were limited to short work periods and were required to take frequent breaks. With a sustained air quality index of 400-600 ppm over two weeks, crews installed conveyors and placed area paving. While the team worked to maintain schedule, cost overruns became the next challenge.
Despite the difficulties of dealing with wildfire smoke, COVID-19 restrictions and supply chain issues, the project was delivered on time.