Top Contractors | Southwest Firm of the Year
Complex Projects Drive Growth at DPR

The Mayo Clinic West Expansion Project leveraged prefab exterior panels, headwalls and a 700-ft temporary bypass hallway module to shave five months off the schedule.
Image by Pete Pallagi
Founded in 1990 with a mission “to build great things,” DPR Construction operates from 29 offices around the country and internationally, employing approximately 9,000 professionals. Just over 700 of those are in Arizona, where a building boom that began at the height of the pandemic is taking the region by storm.
The contractor specializes in complex and sustainable projects for the life sciences, health care, higher education and commercial markets, and each of those sectors is experiencing unprecedented growth in the Southwest region. DPR recently expanded its Tucson office and built a dedicated prefabrication assembly facility to optimize labor and facilitate worker safety.
The firm’s regional revenue totaled $563 million last year.
Recent DPR projects across the region include the Meta Data Center, Banner Desert Women’s Tower Vertical Expansion and Arizona State University Media and Immersive eXperience (MIX) Center (all located in Mesa). Others include the Banner University Medical Center Tucson New Hospital Expansion, the University of Arizona Bioscience Research Laboratories in Tucson and the ASU Health Futures Center in Phoenix, a collaboration between ASU and the Mayo Clinic.
“There is so much energy coming to this region; the pace and scale of development with people and companies wanting to move here is something we’ve never seen,” says DPR project executive Joe Yeargan. “The megaprojects and the gravity of the country shifting to this region during the pandemic, it’s even more meaningful to be recognized as ENR Contractor of the Year in that climate.”
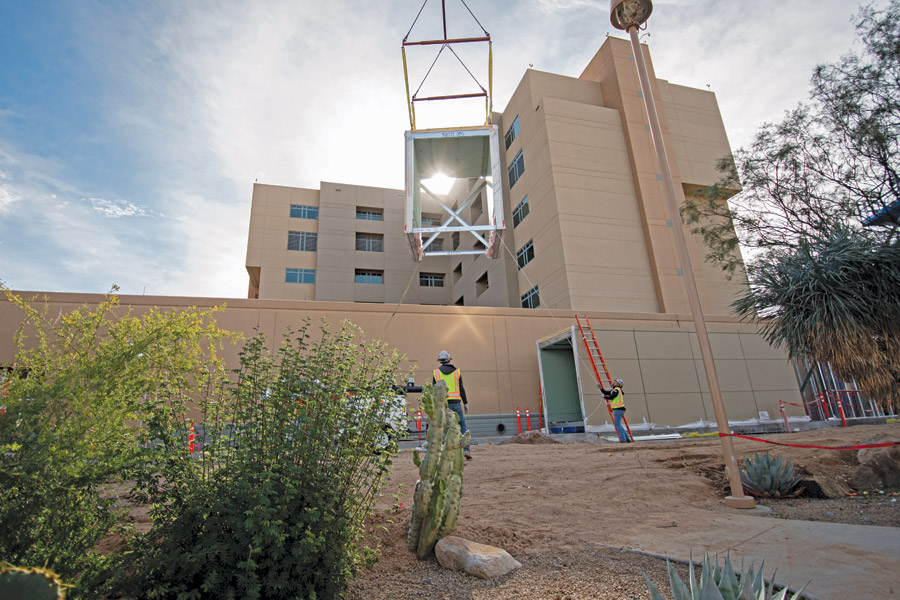
A prefabricated bypass hallway module is suspended via crane and guided into place at the Mayo Clinic West Expansion Tower.
Image by Matt Pranzo
Custom Fit
Health care, a core market for DPR, has felt the strain of the pandemic—from nursing shortages to the stress of canceling elective surgeries due to bed capacity concerns. “But the Arizona market continues to be growing with expansions to meet [those] needs [and with the] work to update facilities, do retrofits and keep up on the latest technologies,” says project executive Charlie Thompson.
“This project is an example of helping realize a facility that will take the client’s initiatives and mission to a new level of per-formance.”
— Matt Shock, Project Executive, DPR Construction
DPR’s Banner Desert and Mayo Clinic West Expansion projects are using prefabrication to deliver more predictable outcomes. “DPR was brought on board in lockstep with the design team in a heavy design-assist role for both projects,” Thompson says. The contractor installed 151 prefabricated factory-built bathroom pods on the Banner Desert project.
On the Mayo Clinic’s 650,00-sq-ft expansion project, DPR drilled a 250-ft-long tunnel under the existing lab and seven-story tower to connect it to the new space and built 155 headwalls on site. Tunnelling under an existing hospital required immense coordination and ingenuity, while the project’s prefab efforts shaved five months off the schedule.
“We’re doing neat things, not cookie cutter. We continue to focus on unique approaches to project challenges and in advancing the industry forward with prefabrication,” Thompson says.
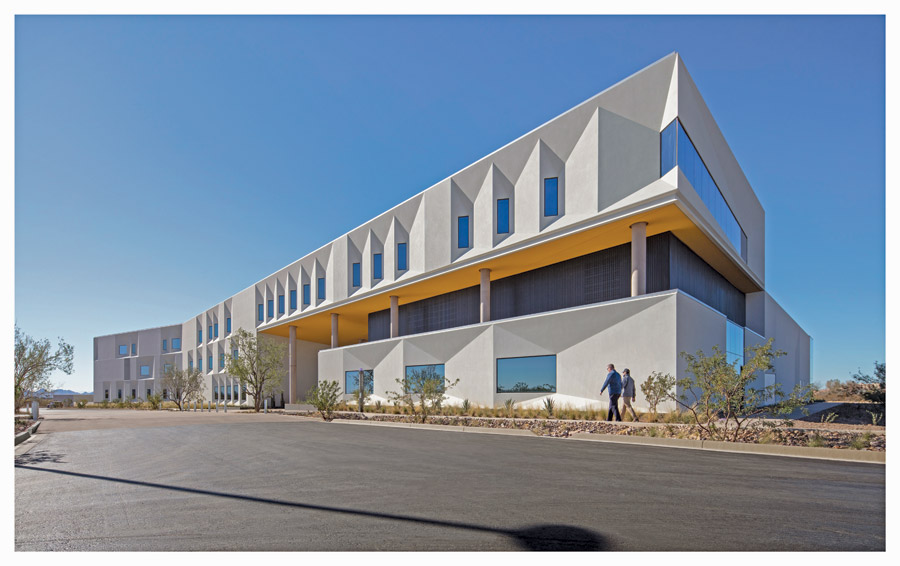
The ASU Health Futures Center houses leading-edge facilities for biomedical engineering and informatics research labs.
Image by Bill Timmerman
Collaboration
DPR recently completed the ASU MIX Center in Mesa. The 118,000-sq-ft facility features cutting-edge spaces that bring together researchers, designers and engineers with state-of-the-art production studios, a fabrication lab and screening theaters to support programs in digital and sensory technology, experiential design, gaming, media arts, film production and entrepreneurial development. A collaboration with the city of Mesa and ASU, the MIX project is a testament to DPR’s skill at facilitating the goals of two large public entities while also collaborating with two architectural partners and numerous faculty, staff and end users, says project executive Matt Shock.
“This project is an example of helping realize a facility that will take the client’s initiatives and mission to a new level of performance,” he adds. “We’re seeing more and more facilities focused on the interface of the real and virtual environment and understand how to construct these technically complex facilities.”
The project, which broke ground and was constructed at the height of COVID, features an intricate facade of terra-cotta panels from Germany. Supply chain challenges in addition to a lack of available shipping containers were an issue; however, DPR has dedicated national resources that deal with logistics and supply chain issues, and Shock says they provided the team with nuances into tracking those overseas materials and understanding what steps needed to be taken to ensure that the material arrived on site.
“It can be hard to admit to the client that there is a problem,” says Alex Kohnen, ASU vice president of facilities development and management, who worked closely with Shock and his team. “A million details went into this project and somehow they were able to constantly stay ahead of the issues and challenges before they became schedule impactors.”
Complex Environments
Mission critical work is another core technology for DPR, and the contractor is currently constructing an air traffic control tower for the Phoenix-Mesa Gateway Airport. The opportunity to build a ground-up air traffic control tower doesn’t come around very often and highlights DPR’s expertise as a technical builder working in complicated environments.
“We thrive on complex projects and seek out those challenges,” Yeargan says.
The Meta Mesa Data Center project features many of the key pieces DPR brings to its projects: prefabrication, virtual design and construction and self-performed work. “Anything happening cutting edge within DPR is happening with our Meta project,” he adds.
“We’re a builder not a broker, and we are eager to take on as much self-performed work as possible.”
— Joe Yeargan, Project Executive, DPR Construction
It’s DPR’s seventh greenfield development for Meta and “the client wants prefab in spades,” says Yeargan. “Prefabricating allows us to dictate when it’s built and stored; we don’t need as many people to build it; and it entails putting our people in a climate-controlled ergonomic environment with better conditions than a typical construction site.”
With more than 2,000 skilled trade workers on site at its peak, the Meta (formerly Facebook) data center campus will include five buildings totaling more than 2.5 million sq ft. The site will be supported by 100% renewable energy and aims to achieve LEED Gold certification.
“We’re a builder not a broker, and we are eager to take on as much self-performed work as possible,” Yeargan says. “It gives us a deeper understanding of the health of the project when we have more people and craft in the field responsible for its delivery.”
As of May 2022, DPR had moved more than 1 million cu yd of dirt on the site, installed 175 miles of underground conduit for power and telecommunications and constructed more than 19 miles of stormwater, sewer and water underground piping.
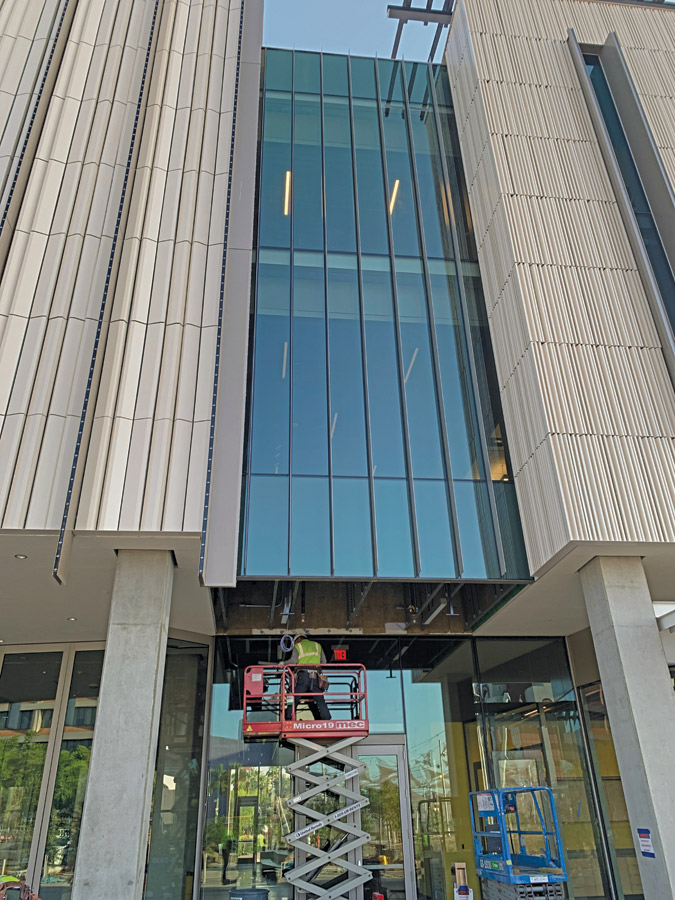
The three-story, 118,000-sq-ft MIX Center includes an enhanced immersion studio, four sound stages, a 280-seat screening theater and an 80-seat screening room.
Image by Charlie Leight/ASU News
Company Culture
Meta elevates the craftworker’s experience on their projects, with comfortable, safe amenities like climate-controlled break and meeting areas; wellness and medic services; and commuter relief programs for high fuel prices—key elements that align with DPR’s people-centric priorities.
“Our culture makes our employees want to take things to the next level, to build great things,” adds Thompson. “Everyone has a voice, and this comes through on our projects.”
“We grow and develop all our employees as individuals; our people are what make us special,” adds Gretchen Kinsella, DPR’s Arizona business unit leader. “We want them to enjoy coming to work and to go home as safe as they showed up.”
DPR brings its entire team together for “Culture Con,” where Con stands for conversation, an opportunity for craft and administration of each region to come together to ask questions, share feedback and learn about the company’s plans for the upcoming year.
“That intentional engagement with craft goes to the roots of our collaborative nature,” adds Shock. “Both craft and admin are equally important and highly valued for what everyone brings to table. We invest in that because we all feel strongly about providing that communication.”
Shock says DPR also is proud of its six-year partnership with New Pathways for Youth, a downtown Phoenix nonprofit that partners at-risk high school students with a DPR ally to learn interview and resume-building skills while taking a deep dive into the many paths available to them in the construction industry.
DPR also hires youth from underserved communities for paid summer internships.
“We will keep finding the best labor force and managing the supply chain impacts to the best of our abilities. We have to be on our toes and think creatively to protect our clients and their projects,” Kinsella says, adding that the sheer volume of jobs in the Arizona market will continue to present a challenge for contractors.
“I’ve never seen anything like it,” she adds. “I’m not sure if it’s the new normal, but we’re making the best of it while we can.”