Danisco, a food ingredients, enzyme and bio-based solutions company headquartered in Copenhagen, Denmark, commissioned the $7-million design-build construction of a walk-in storage freezer that is the coldest in the United States and the largest in the world.
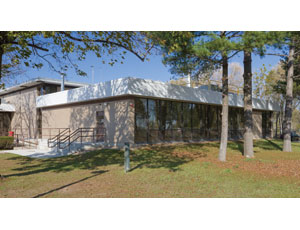
The facility in Madison, Wis., is used for the advancement of and research in dairy cultures to make cheese, yogurt and probiotics.
The project team took 10 months to design a 7,000-sq-ft walk-in freezer to operate at -76° Fahrenheit and a corresponding 11,000-sq-ft building addition to house this ultra-cold box.
Owner: Danisco USA, Madison, Wis.
General Contractor: Tri-North Builders Inc., Madison, Wis.
Design Firm: Strand Associates Inc., Madison, Wis.
Working with Strand and Dualtemps to ensure that the freezer could reliably operate at -76° was critical. Once the freezer went into service, Danisco could not afford to have it stop working, since there would be no alternative to storing the products in the freezer.
The team made sure the design, functionality and reliability met the continuous-operation requirement. In addition to designing the freezer, the team also had to design redundant monitoring to make sure that all systems remained operational.
Cleaning of shoes entering the clean areas was accomplished by depressing the slab, and installing a foam solution shot from each side of the door frame to eliminate contaminants. A person walks through the foam and then across mats before entering the clean room. The clean room outside of the super-cold freezer has to remain sterile at all times for the preservation of the cultures.
The ceiling panels are supported by threaded rod with plastic parts attached to the panels. The rods are heavily insulated up to the freezer structure. The plastic part of the connection is required because frost would build up on metal. The large round insulated PVC tubes around the threaded rods are necessary because the plastic parts will transmit cold to the metal rods and we need to prevent frost build-up on the rods. The build-up would have to be cleaned off regularly to prevent the possibility of it falling off and damaging the panels.
The freezer’s concrete slab was poured, cured and allowed to drop in temperature over eight weeks to control shrinkage. After the room and slab had reached -10°, the perimeter joints were caulked with a special compound that cures at that temperature. The room was then taken down to -76° over several weeks.
Air locks had to be installed to enter the super-cold freezer at -76°. They were created to go from ambient to 40°, 40° to -5° and -5° to -76°. This was necessary for the pressure issue and to control condensation or frost build-up in the units.
The 12-in.-thick freezer panels had to be fabricated in Europe, as no U.S. manufacturer would warrant panels for such extreme temperatures.
A lighting control reduces the amount of light, and related heat, generated by each bulb, allowing the freezer to cool to the proper temperature.
Wisconsin requires fire sprinklers and alarms throughout the building, but no sprinkler head or alarm will work at the temperatures found in this freezer. So the team designed and installed a system to trigger a fire alarm by detecting the change in air density that would occur if there were a fire in the ultra-cold box.
Post a comment to this article
Report Abusive Comment