Digging Deeper | Airport/Transit
Building at Breakneck Pace To Keep Pilots Up to Speed

Turner devised a novel schedule to deliver two flight simulator bays to United in spring 2023. The second phase includes 10 more bays slated to become operational before the end of 2024.
Photo courtesy Turner Construction
The world’s largest training facility for full-motion flight simulators is growing even larger with the addition of Building H at the United Airlines Training Center in Denver.
The 157,777-sq-ft facility, located on a 23-acre site near the long-gone Stapleton International Airport, will bolster United’s plan to hire 10,000 pilots by 2030 with 12 new full-motion flight simulator bays to support training.
The four-story, $123-million project also includes offices, classrooms and a pedestrian bridge linking the new spaces to existing campus buildings.
Work started with a more modest vision before Turner Construction enlisted architecture firm BRPH to respond to an RFP for an expansion to United’s existing Building F in fall 2021.
“United made a pretty bold move during COVID; it didn’t get smaller, it didn’t lay off pilots and it started buying airplanes,” says Mark Adams, the airline’s director of planning, development and corporate real estate for the Rocky Mountain region. “As you buy aircraft, everything else has to get bigger. We needed more pilots, mechanics and hangars and more simulator training facilities.”
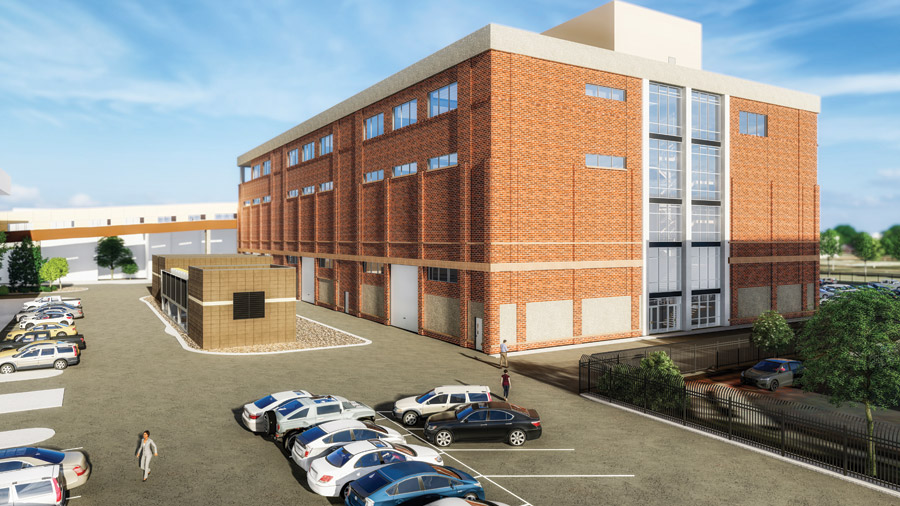
Upper floors feature offices and classrooms along with a fourth-story break area that offers sweeping views of the Rockies.
Image courtesy Turner Construction
Bag of Tricks
As other airlines were canceling orders for multimillion-dollar simulators from Montreal-based manufacturer CAE Inc., United was in buying mode.
“Even before we had the contractor and designer on board, we already knew when the first two simulators were coming in,” Adams says, with the airline initially issuing an RFP for a six-bay expansion.
United “was figuring out what it wanted to truly build out on the existing campus,” says Dan Wilder, Turner project executive in Denver. “We came to the final interview with 3D-printed models of about 10 different options” for the campus.
Jim Hillier, vice president and architectural national practice leader at BRPH, likened the session to playing dominoes. The first moves demonstrated that only four bays were feasible, not six.
“As you buy aircraft, everything else has to get bigger. We needed more pilots, mechanics, hangars and simulator training facilities.”
—Mark Adams, Director of Planning, Development and Corporate Real Estate for the Rocky Mountain Region, United Airlines
“At the same time, we showed [United] that it could add two additional 12-simulator bay buildings on campus,” he says. “We put together not only options to expand the campus, but also pricing for the review of what each option would mean to moving forward.”
The interview turned into an exploration of the possibilities, with an assist from the 3D models.
Team members “kept pulling pieces out of their little bag of tricks,” says Michelle Martin, president of Civil Innovations LLC and owner’s representative for United on the project. “They were moving the pieces around, and it really changed the way everybody saw that upcoming building.”
According to Wilder, “it became more of a working session rather than a formal interview for a new project.” He says, “We completely turned [the RFP] on its head,” telling the United managers that ‘We understand that’s what you’re asking for, but you’re going to run out of sim bays again months after we complete this project.’”
United subsequently pivoted to the concept of a new building with 12 simulator bays topped by two levels of offices and classrooms. The fourth floor features several fixed-base simulators and an outdoor break room with panoramic views of the Rocky Mountains.
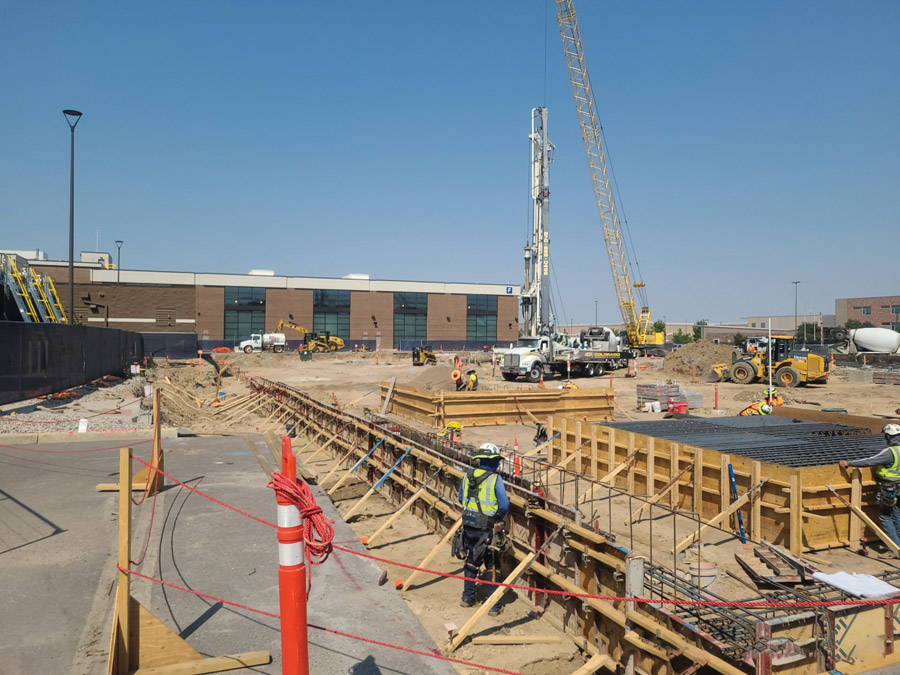
The project includes more than 6,000 cu yd of concrete and 300 tons of rebar.
Photo courtesy Turner Construction
Turbocharged Timetable
Turner and BRPH won the design-build job in December 2021, broke ground in July 2022 and topped out the structural steel in early 2023.
“Mark Adams told us, ‘You’re never going to hear a client say this again, but budget is actually secondary on this one. We have to hit the schedule,’’’ Wilder recalls. “The need was immediate. They needed more [simulation] bays and classroom and office space as soon as humanly possible.”
That was partly because the Federal Aviation Administration was already scheduled to certify the simulators before construction began. “If you miss that FAA certification date, you don’t get another date just around the corner,” Martin adds.
Shutting down the campus to accommodate construction was not an option. “It runs 24/7, and we only close it two days a year,” Adams says. “All of the 16,000 to 17,000 pilots we have right now are required to come through here at least two days a year every nine months.”
There were a number of other challenges associated with the tight timeline. Design and permitting required a breakneck pace, and labor was scarce. Earthwork also was no small task, with unmarked utilities and “veins of trash” from the site’s past uses as a Stapleton taxiway and landfill, Wilder says.
“Two and a half months to get enclosed after structural steel is somewhat unheard of. It allowed us to start all of the interior MEP work that much earlier.”
—Dan Wilder, Project Executive, Turner Construction
Contractor Elite Surface Infrastructure cleared the site while Turner self-performed the concrete work, which included a total of 6,500 cu yd of concrete and 315 tons of rebar. Turner further accelerated the schedule with a strategy of “breaking out foundations and superstructure from the balance of the building,” Adams says.
Working closely with the city of Denver and the Denver Fire Dept., the team was able to have the first two bays permitted separately and delivered under a phased occupancy permit so United could take beneficial use of them as of June 1, 2023.
“Those operating simulators, which are in use now, were behind rated partitions,” Wilder points out. “In January, we essentially revoked [United’s] occupancy of the building and removed those temporary rated partitions so that we could, in one short month’s time, tie all those systems and finishes into the rest of the building.”
A new certificate of occupancy was then issued for the building, which was reinspected and delivered back to the airline. “It was like a dual-occupancy delivery, but it absolutely suited exactly what United needed and asked for,” Wilder says.
A panelized exterior wall system manufactured by E&K Cos. helped Turner hit the target for the first two bays. It took about 10 weeks to proceed from topping out to full enclosure.
“We had the design concept, but they [E&K] really helped put meat on the bones,” Wilder adds. “Two and a half months to get enclosed after structural steel is somewhat unheard of. It allowed us to start all of the interior MEP work that much earlier.”
Adams credits the project’s more than 1,000 workers for hitting the targets set by Turner and BRPH. “All of the subcontractors, 100% of them, were from the Denver metro area,” he says.
“We had 124 subcontractors on the job, and we were able to do that all locally, which I thought was pretty huge,” he notes, adding that of those 124 firms, 37 were diverse contractors—minority- and women-owned businesses.
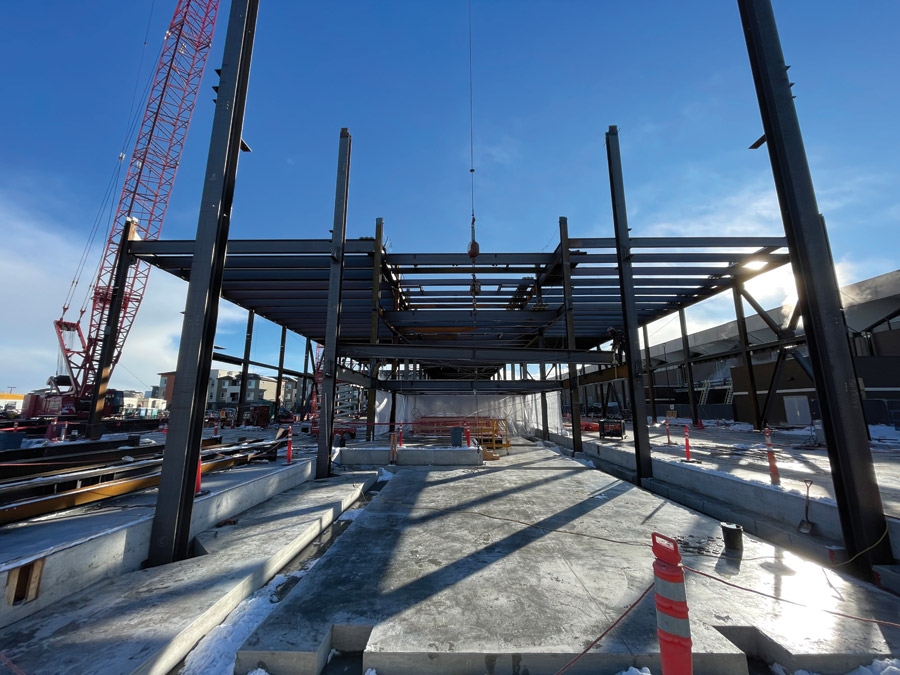
Structural steel topped out in early 2023, just about six months after groundbreaking.
Photo courtesy Turner Construction
Power Points
According to Wilder, “This is a very heavy MEP-intensive building with a lot of special systems.”
He adds that subcontractors Extreme Fire Protection, Encore Electric and Murphy Mechanical started their construction work before the building was enclosed. “Having those three firms on our team was hugely beneficial, he says. “We could not have done it without them.”
Hillier noted that the simulator’s power requirements required an evaluation of the campus’ electrical consumption.
“Some of the systems on the campus were underutilized by the actual power demands of the equipment,” he explains. “Once we went through that evaluation, that gave us a chance to make recommendations of what we could do with new equipment moving forward to try to take advantage of some of their existing systems.”
The effort was also guided by ambitious targets for energy efficiency and sustainable operations. United has “lofty goals about going carbon-neutral here in short order, and along with complying with new Energize Denver standards, a lot of the things and ideas and systems that were incorporated into the building are very new and forward-thinking,” Wilder says. This includes a Power over Ethernet lighting system, which studies have found can be 40% more efficient than AC-connected LED lighting, he adds.
Forward Thinking
With construction on Building H complete, the plan is to install and certify two simulators per month through the end of 2024. “At 40 [simulator bays], we were the biggest, and now we’re adding 12 more for 52, so we are definitely the world’s largest training facility for full-motion simulators,” Adams says.
United is already mapping out its next simulator facility on 114 acres the airline owns near Denver International Airport, with the airline expected to issue an RFP this spring.
“We have to be done by the end of 2027,” Adams says. “Once again, I’ve got the deadline before I’ve even started the project.”