In 2020, Intel’s Fab 42 began operations at its Ocotillo Campus in Chandler, Ariz. The 1.3-million-sq-ft semiconductor manufacturing plant was built by more than 4,000 workers with 120,000 cu yd of concrete and 12,000 tons of structural steel. Inside, it contains 1,300 tools weighing as much as 5 tons. It is the fourth semiconductor plant on the 700-acre campus.
Now Intel is building two more plants in tandem at the site, and they’re even bigger, expected to use 400,000 cu yd of concrete. The $20-billion project to build Fab 52 and Fab 62, with general contractor Hoffman Construction Co.—which has previously built other fabs at the campus—started in 2021. Fab 52 is expected to come online this year, followed by Fab 62 next year.
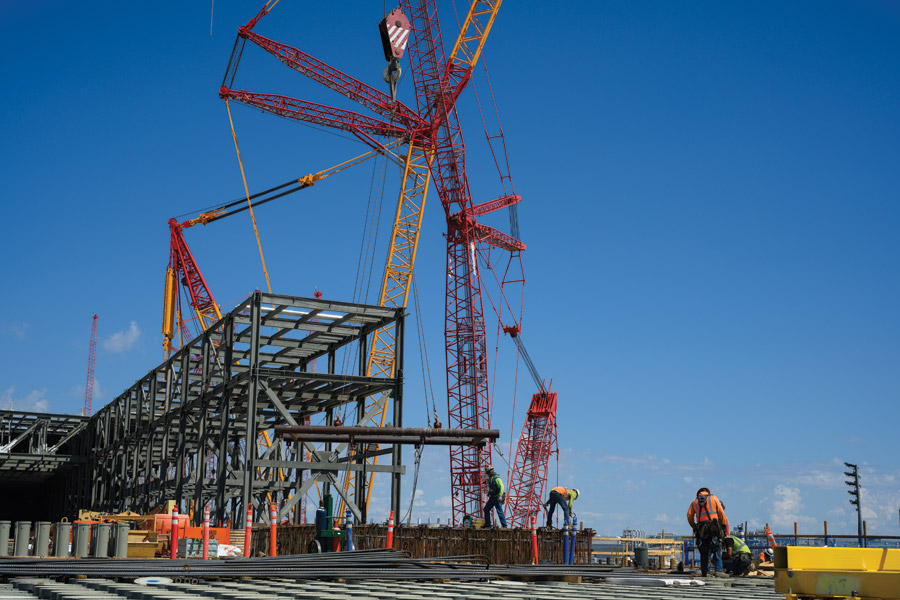
A crawler crane, the largest of its kind in the world, is shown at work in September 2023 lifting steel trusses into place.
Photo courtesy Intel Corp.
Each fab—short for semiconductor fabrication plant—is about 70 ft tall and includes four levels. One level is the clean room, where the actual production takes place and workers wear full-body “bunny suits” to keep hair, skin flakes and lint from becoming airborne particles that could disrupt the sensitive equipment. Above the clean room level is a fan deck with systems to maintain air quality, temperature and humidity in the manufacturing space. And below the clean room, is a level with the lateral pipes carrying different liquids and gases used in manufacturing and there is a utility level as well.
There are also various auxiliary buildings for systems like heating and cooling and a workforce of thousands in addition to the construction team. Dan Doron, vice president of manufacturing, supply and operations, and general manager of fab construction at Intel Electronics, compares the campus to “a small city” needed to produce leading-edge computer chips.
“As we go from project to project and we’re introducing new technology, the level of complexity is just getting higher and higher,” Doron says.
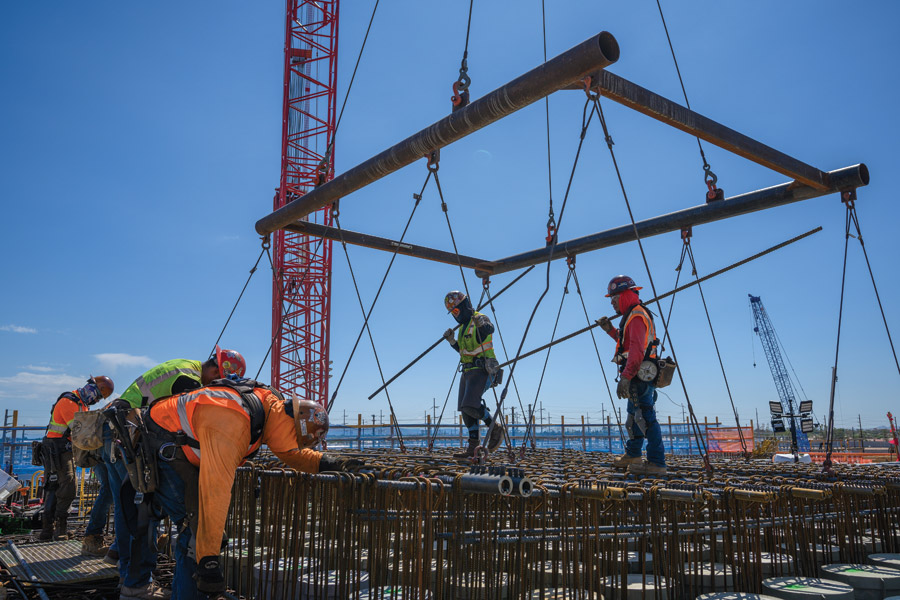
In September 2023, ironworkers lower a rebar cage to create the factory floor for one of the new fabs.
Photo courtesy Intel Corp.
Repeatability
“As we go from project to project and we’re [using] new technology, the level of complexity is getting higher and higher.”
—Dan Doron, Vice President, Intel Electronics
Doron is responsible for managing a current construction portfolio of 15 sites and a budget of more than $14 billion per year. With so many projects in different stages in the U.S. and overseas, he says repeatability is a focus. Each plant is based on the previous one, but with improvements from lessons gained on the prior projects.
“What we learn on the first, we are going to implement on the second to start from a better position,” he says.
Mike Lindell, program superintendent at Hoffman Construction, says that mindset has carried over on the contractor side, too. While the large fab buildings appear plain on the outside, they are deceptively complex and densely packed inside. With thousands of workers and thousands of deliveries, knowing the sequence in which the equipment needs to be installed and turned on is a significant advantage.
“When you’re done with these, you can’t see the ceiling,” Lindell says. “You can barely see through the rooms, it’s so packed full of all the process and chemical distribution.”
To minimize the congestion, Lindell says the team is using preassembly and offsite manufacturing of some equipment going into the plants.
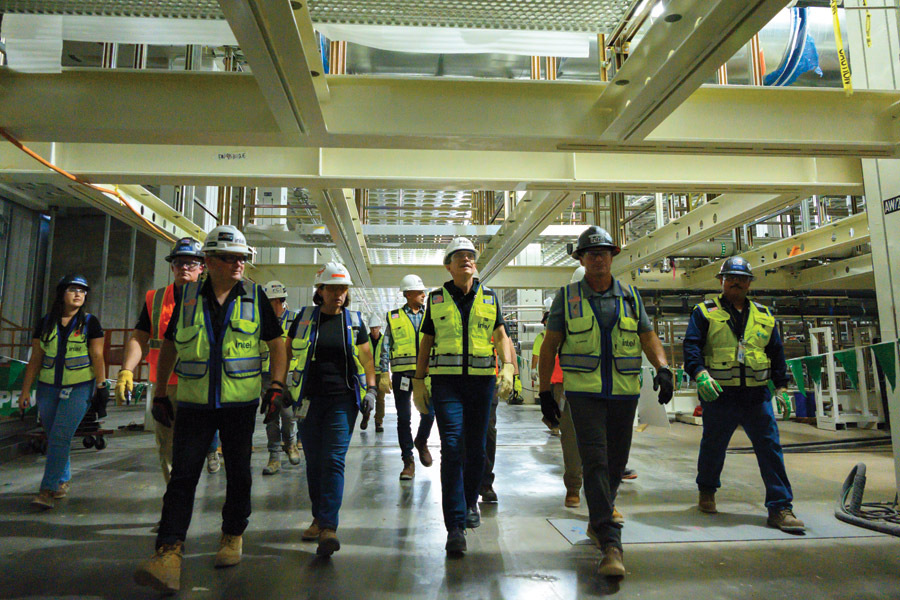
Intel Corp. CEO Pat Gelsinger (third from right) toured the site in October as the project marked a construction milestone.
Photo courtesy Intel Corp.
Skilled Workforce
Being able to retain skilled craftworkers is a big focus, and also a benefit, thanks to the labor shortages in construction and the boom of semiconductor fab projects in various stages of planning or construction across the country amid a national push to boost domestic chip manufacturing. Intel has been in Arizona for 44 years, and Doron says the company works to maintain good relationships with workers. More than 6,000 are involved in the Fab 52 and 62 projects.
“We make sure that no matter what happens, time after time the trades are going to choose us and the workers have a place they want to work,” Doron says.
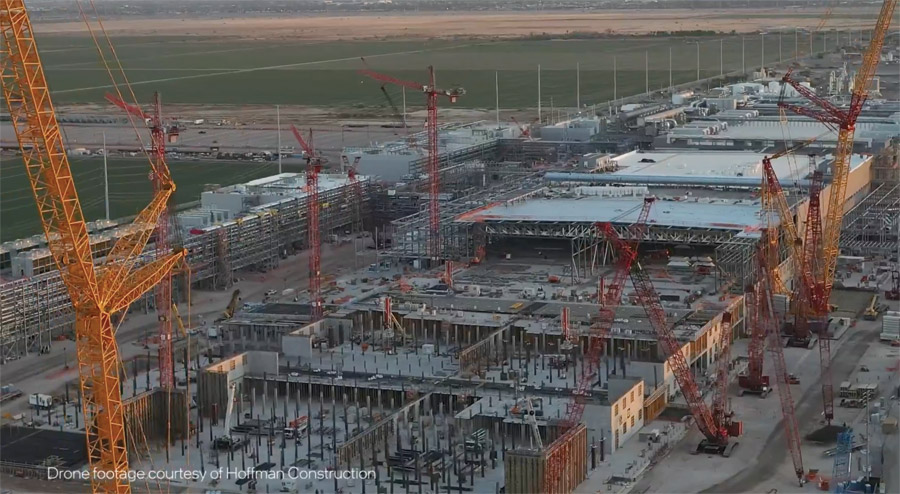
A view of the site in 2023 shows the project’s sprawling nature.
Photo courtesy Intel Corp.
Part of that is ensuring there are quality amenities and training for the workers. Another key part is having a safety culture that ensures they can keep coming back. Doron says Intel views safety as a value, not a task, and that comes from the top down.
“They care—not just about building a factory—they care about the people who are building it.”
—Mike Lindell, Program Superintendent, Hoffman Construction Co.
Intel’s safety culture goes beyond presentations at orientation. There are safety refreshers throughout the project and what Doron calls “pattern interruptions” where they surprise workers with an event or treat while reviewing safety options and recent events on the project. The team also makes “touch points” with workers, approaching them to talk about how they’re doing, ensuring they have all necessary skills and personal protective equipment they need for the job. Recognizing the stress that goes into construction and the impacts that can follow, the team also has experts available to speak with workers about their mental health.
“We’re putting the full person in the center and telling the person that they don’t just own execution of the job, they own the safety of their team,” Doron says.
Lindell, program superintendent with Hoffman, says Intel’s work on these projects and the earlier ones has shown that it wants to create an environment that allows people to work safely and efficiently.
“They care, not just about building a factory so that they can sell semiconductors, they really care about the people who are building it,” he says.
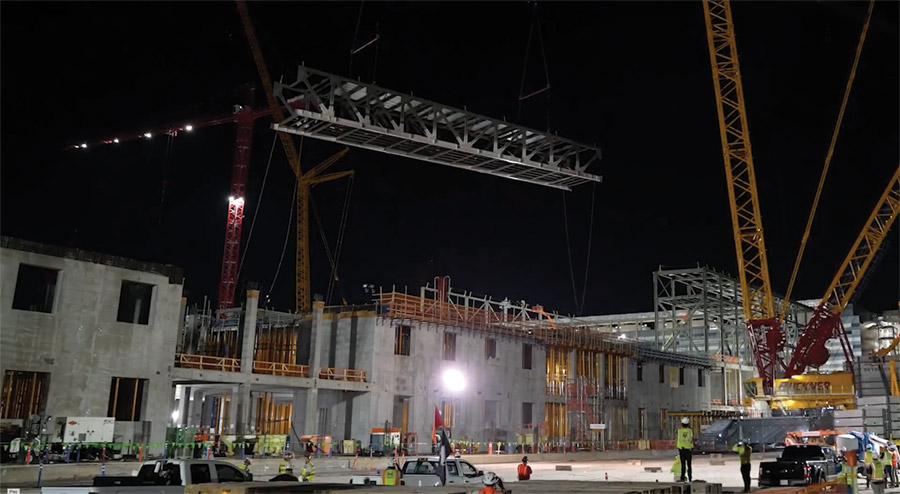
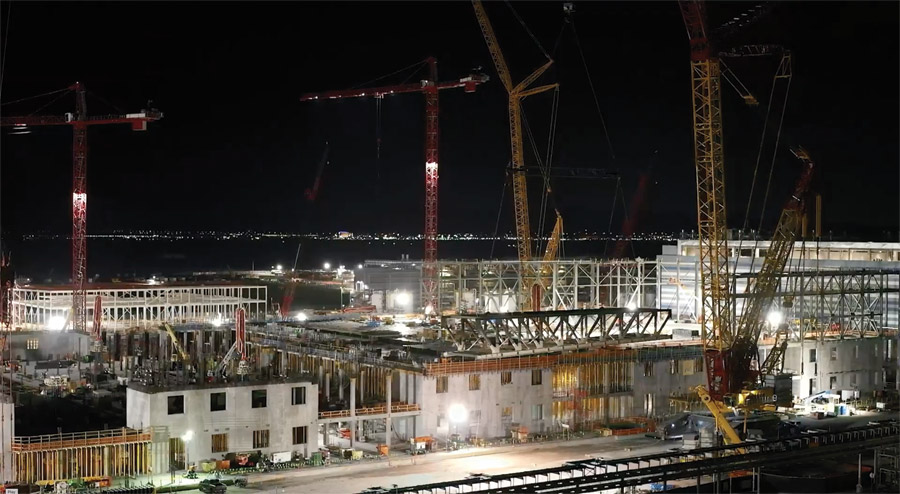
Construction continues during night hours, with placement of structural segments shown here.
Photos courtesy Intel Corp.
Water, Power and Materials
Intel also has several environmental goals, both globally and for its presence in Arizona. Liz Shipley, director of community relations and sustainable operations for Arizona and Costa Rica for Intel, says the company continually strives to improve its operations and minimize its impact on the environment.
Water is one of the most important ingredients in semiconductor manufacturing, and Intel has set a goal of achieving net positive water—returning more water to external restoration projects than it takes in—across all its sites by 2030. Shipley says they’re already net positive in the U.S., and have been since 2020. But Arizona is hot and dry—with the Phoenix area averaging 111 days per year with temperatures hitting 100 degrees or greater and a mean of 7.3 inches of precipitation, according to National Weather Service data.
“We're all about the community. How can we be an asset to our community, and how can we be a good neighbor? It’s important to us.”
—Liz Shipley, Director of Community Relations, Intel Corp.
Still, Intel has managed its water goal through reducing use and recycling and restoring water, even in Arizona, according to Shipley. The Ocotillo Campus has its own 12-acre onsite water reclamation facility with capacity for 9 million gallons per day. Intel also partnered with the city of Chandler on the Ocotillo Brine Reduction Facility, which treats water and removes salt so it can be reused at the manufacturing campus and elsewhere in the city.
Most of the water Intel takes in for the Ocotillo fabs is used again and again. For whatever is lost to consumption or evaporation, the company has also funded 20 water restoration projects benefiting Arizona, such as the Colorado Water Trust’s Upper Colorado River Flow Enhancement, which restored an estimated 533 million gallons in 2022, according to Intel.
Intel also set itself a goal of achieving 100% renewable electricity use by 2030. In Arizona, the company buys green power from a local utility, and the Ocotillo Campus also has onsite solar. The campus is already 100% on renewable power, says Shipley.
“Solar panels are great because there’s a lot of sun, so you can generate a lot of power off of them,” she says. “But they also make great covered parking structures, so our parking lots are filled with solar panels that our employees enjoy parking under to keep their cars in the shade in the hot Arizona summer.”
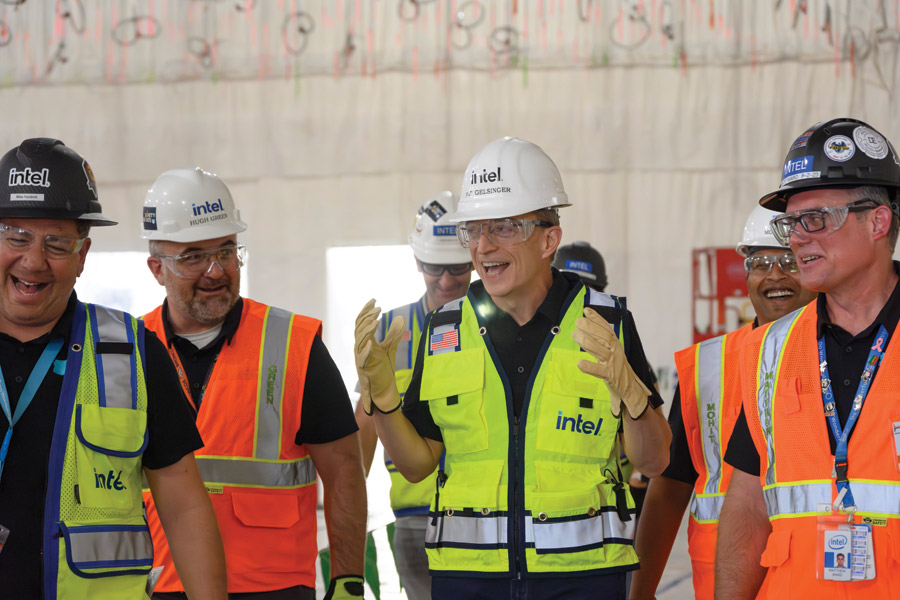
Pat Gelsinger, Intel Corp. CEO, shows his enthusiasm for the work being done at the project in October 2023.
Photo courtesy Intel Corp.
The Arizona project team also aims to recycle at least 90% of its construction waste, and Doron says they’ve been hitting that goal, recycling 100,000 tons of material last year. Materials like concrete, metal and drywall are key parts of that effort, which requires separating materials on the site and also looking upstream on the engineering side and finding ways to reuse it.
“It’s an effort, but it’s worthwhile,” Doron says.
The new fabs also represent renewed growth of the U.S. semiconductor sector, which has been the focus of a federal push over the past few years. The White House has framed domestic computer chip production as an important issue for the economy because of the chips’ widespread use in various consumer goods, from small electronics to cars, which experienced supply chain disruptions from the COVID-19 pandemic. Federal officials also say it is an issue of national security, because the chips are used in telecommunications equipment and military vehicles.
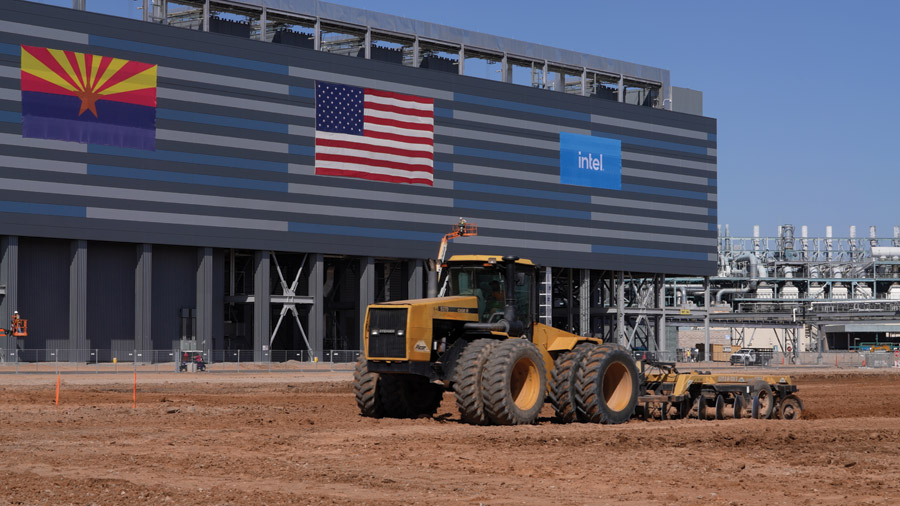
Intel states that the $20-billion project constitutes the largest private-sector investment in Arizona history.
Photo courtesy Intel Corp.
Local Impact
While it is hoped that the fabs will have a widespread impact, Intel is also focused on their local impact. The company sources items locally when it can, and Shipley says Intel spent $2.5 billion with Arizona-based companies last year.
In addition to the Ocotillo Campus, which is focused on manufacturing, Intel has a second site in Chandler, named the Chandler Campus, which it uses for advanced packaging, assembly testing, design, research, sales and marketing. The company has about 12,000 employees across the two sites.
Shipley says Intel has a “good neighbor” policy, and the company aims to proactively communicate plans and construction updates to nearby residents. The company also used the current project as an opportunity to redo landscaping along the fenceline with its neighbors. After taking their feedback, Shipley says the company recently completed construction of a one-mile-long wall and is planting 300 trees along it.
Intel also held a “name the crane” competition for local third graders to dedicate Buckner HeavyLift Cranes’ Liebherr Model LR 13000 crawler crane, which can be seen from the students’ school as it is put to work on the project. Shipley says they gave a laptop and hardhat to the child who suggested the winning name, “Skyreacher,” and held an ice cream party for their class.
“We’re all about the community,” Shipley says. “How can we be an asset to our community, and how can we be a good neighbor? It’s important to us.”
In recognition of the Intel project’s impact on the Arizona construction industry and state and local economy, and for its efforts to positively affect the surrounding communities, ENR Southwest is proud to recognize the company as its 2023 Southwest Owner of the Year.
Post a comment to this article
Report Abusive Comment