Port of Alaska Petroleum and Cement Terminal Phase 2
Cook Inlet, Alaska
Best Project, Airport/Transit
Submitted by: Pacific Pile & Marine
Owner: Port of Alaska
Lead Design Firm: COWI
General Contractor: Pacific Pile & Marine
Civil Engineer: HDR
As the Port of Alaska’s primary petroleum dock and the state’s only bulk cement-handling dock, this facility is a key part of the port, which serves as the main intermodal transport hub for freight movement in the state. The Petroleum Oil Lubricants Terminal 1 was in critical condition leading up to this replacement effort, with corroded and splitting pipe piles and other damages exacerbated by a 2018 earthquake.
To achieve an early and under budget completion in October 2022, the project team tackled multiple challenges with careful planning and communication. The site’s extreme tidal variations, which can fluctuate up to 40 ft per cycle, impacted the available working height from barges and the velocity of the water during tide changes.
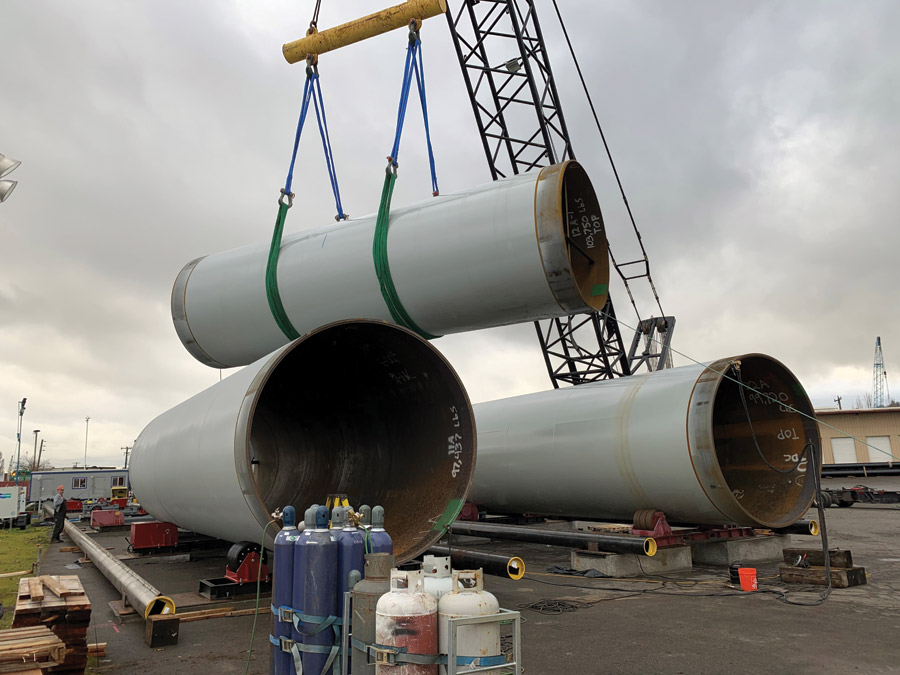
Photo by Zach Wallace
Adding to the complexities was the schedule, which was limited to ice-out and ice-in conditions. Since flat deck barges couldn’t be used during icy winter conditions, crews completed water side construction with a Pacific Lifter crane barge—the largest pile-driving crane on the West Coast. With its lift capacity and head room, the Pacific Lifter drove all nine 144-in. monopiles without the need to splice.
Throughout dredging, the project team had to navigate severe sediment shoaling within the dredge prism thanks to an influx of glacial sediments within Cook Inlet. During peak melt season, there was upward of 3,000 cu yd of infill shoaling within a single week. The port worked with the contractor to pay for additional dredging to hit the designated grade.
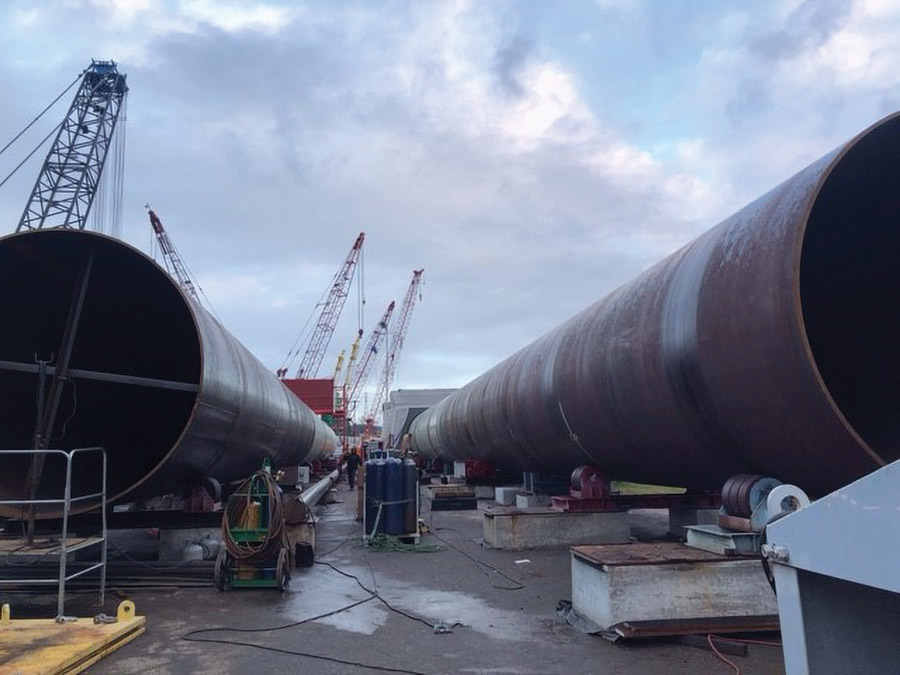
Photo by Zach Wallace
With multiple layers of varying soil conditions, piles were designed to reach a soil layer that could generate the required vertical load resistance, while the upper layers provided the necessary lateral resistance. Crews drove the piles deep through glacial sediment and into hard glacial till.
To limit impacts of pile-driving on the surrounding environment, the team used multiple stage steel-confined bubble curtains on both temporary 36-in. and 144-in. permanent piles. Each had a specific bubble ring layout based on site location and water depth from the top of the template elevation to limit potential injuries to local marine life.
Bubble curtains also served as a pile-driving template. Crews installed weldments with rubber D fenders at the top and bottom of the piles to guide them into vertical position, then the steel-confined bubble curtains were set in place, welded to the template top and used as a pile guide.
Post a comment to this article
Report Abusive Comment