Chemical Phosphorus Removal and UV Disinfection Project
Englewood, Colo.
Best Project
Submitted by: PCL Construction
Owner: South Platte Renew
Lead Design Firm and Civil/Structural Engineer: Stantec
General Contractor: PCL Construction
MEP Engineer: BCER
The South Platte Renew Water Recovery Facility treats approximately 20 million gallons per day of residential and industrial wastewater from 300,000 residents in connecting communities. Treated effluent is discharged into the South Platte River. Since the river is host to numerous aquatic habitats and has water rights dedicated to several districts along its path, the Colorado Dept. of Public Health and Environment Water Quality Control Commission instituted new limitations on nitrogen and phosphorus levels.
This $12.2-million project focused on upgrades to the plant’s chemical feed system to facilitate compliance with these new phosphorus and nitrogen effluent limits. In addition to the chemical phosphorus and nitrogen removal system, scope included the conversion of the existing sodium hypochlorite disinfection system to ultraviolet (UV) disinfection.
Although the facility was meeting nitrogen requirements, the existing treatment process couldn’t meet required phosphorus levels. By converting the disinfection system to UV disinfection, the facility can drastically decrease chemical usage, have consistent and reliable control over the disinfection process and effectively meet all discharge permit requirements for disinfection.
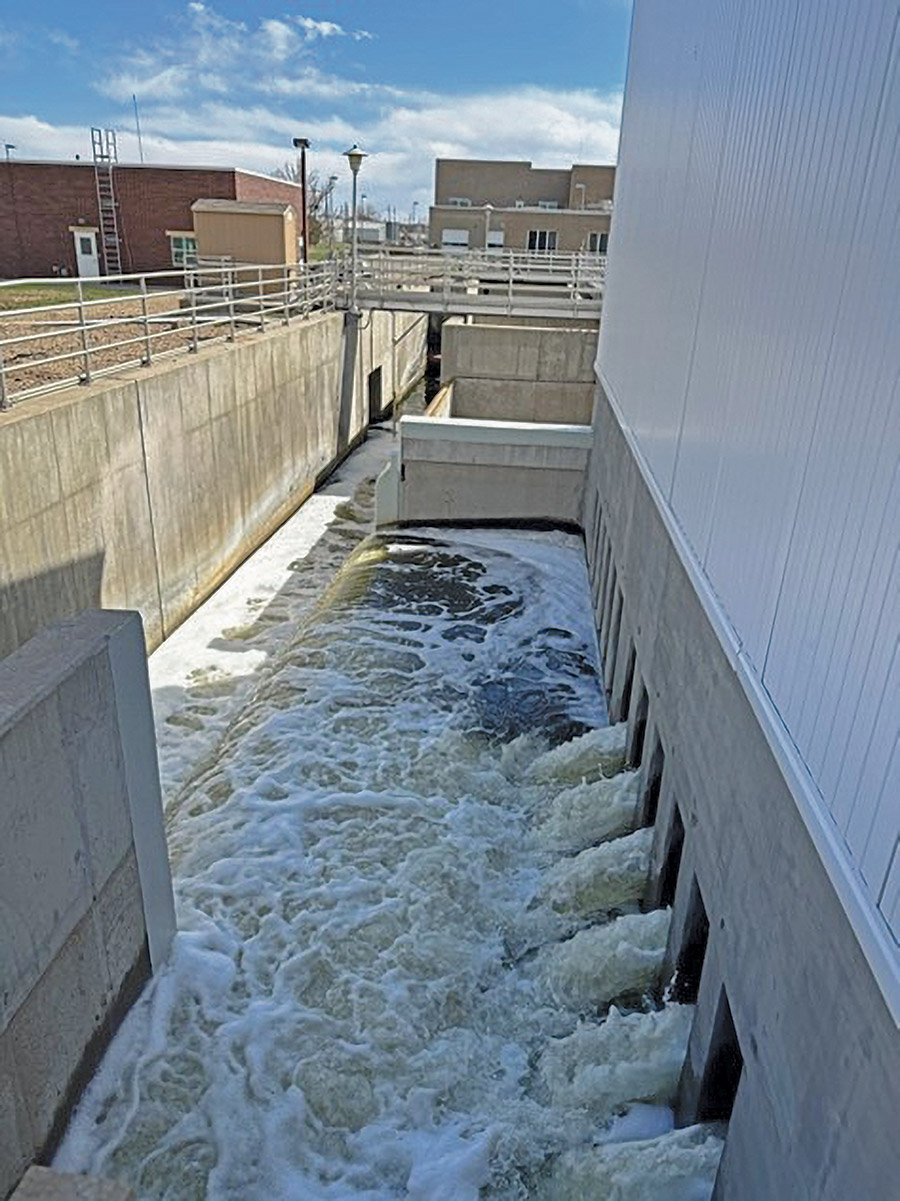
Photo courtesy PCL Construction
PCL worked with the city to establish a multiple GMP approach to accelerate process equipment and materials procurement to help insulate the project from high forecasted escalation costs. The contractor held a competitive bidding process between three UV manufacturers prior to the 30% design milestone, and the team evaluated unique UV system criteria, such as power consumption, number of lamps, ballast and cost of spares.
The addition’s initial design called for a masonry building with steel trusses to match the existing facility. Given long lead times and budget constraints, the design team proposed a preengineered metal building to meet the owner’s budget and lower operation and maintenance costs while meeting the client’s criteria for durability.
Crews completed work across three phases, all of which ended on time or early, leading to an on-budget and on-time completion in May 2023.
Post a comment to this article
Report Abusive Comment