A $2.3-billion makeover for One Madison Avenue in Manhattan is transforming the stately 70-year-old structure into a sleek 27-floor, 1.4-million-sq-ft office tower companion to its adjacent Manhattan landmark—the 5 Madison clock tower. While work only began on the adaptive reuse effort in early 2020, the project team is set to finish ahead of schedule, with substantial completion later this year and an expected opening in early 2024.
Led by developer SL Green Realty Corp., with joint venture partners Hines and the National Pension Service of Korea, One Madison is reshaping the original 15-story Art Deco-era building with a new high-end design. This includes double-height feature floors at the level where the old limestone-facade base transitions into a new glass curtain wall tower above.
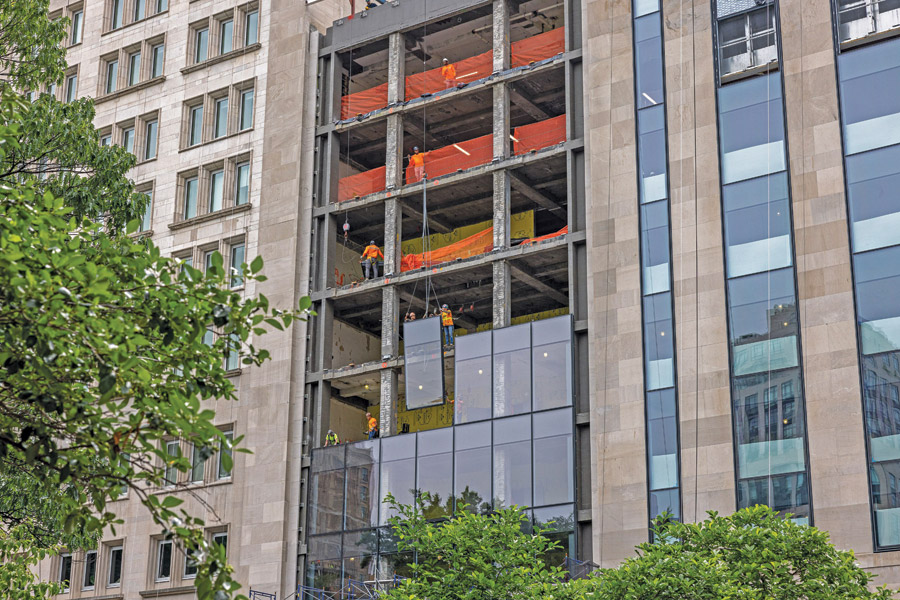
One Madison’s design blends some of the old structure’s classic limestone exterior with a new facade of glass with gunmetal-colored aluminum fins.
Photo by Max Touhey for AECOM Tishman
Along the way, the project team—with AECOM unit Tishman Construction as construction manager, Kohn Pedersen Fox as architect and Severud Associates as structural engineer—steered through the COVID-19 pandemic, supply chain crunch and deep coordination with key city agencies and community groups.
But one most impressive team feat won’t be visible in the final product: the mammoth demolition effort designed and executed to remove entire floors and tons of equipment and to carve out the building’s core—with excavators, bulldozers and backhoes chopping their way down to the foundation.
That took place on a building footprint spanning nearly a full city block, according to Dan Leiro, Tishman vice president of operations for architectural and structural trades.
“We gutted the whole building,” he says. “We demoed the top five floors. The overall height was 240 feet approximately, and we demoed 123 feet of it, so we almost took half the building height off.”
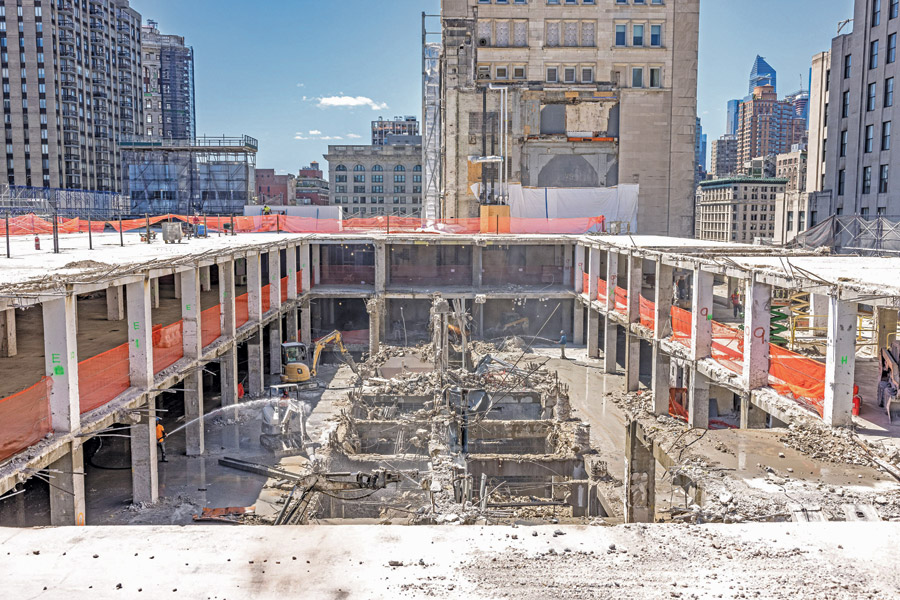
The complex adaptive reuse project started with demolition of the old building’s top five floors, gut renovation of remaining floors and construction of a new building core for the 27-story tower.
Photo by Max Touhey for AECOM Tishman
Removing the mountain of systems and old building core also were sizable tasks, says Rob Blackman, Tishman executive vice president.
“The mechanical penthouse had a tremendous amount of old, very large and very heavy pieces of equipment that all had to be demoed,” he says. “We basically demoed top-down—we ‘apple-cored’ the building down to grade, to the existing foundations.”
To handle the scope of demolition, the team strategically repurposed the building’s old elevator shafts into a giant debris chute, sending concrete and other materials to the basement and subcellar, Leiro says.
“We built a giant enclosure around these chutes— with massive reinforced wood doors—to speed up the process,” he says. “There were shoring jacks underneath—multiple layers of steel plates. Between the shoring and enclosures we built on every floor, it was pretty complex, but it was well worth it—a good strategy for demolition.”
The effort had an added layer of complexity because One Madison houses mechanical systems for the adjacent 700-ft-tall clock tower, which today is a luxury hotel. That created the need to build temporary systems for the hotel—and to orchestrate demolition around them, says Mike Goldberg, Tishman executive vice president and project executive.
“Until we had the temporary plant set up in early 2020, we could not do the hard demolition of the existing mechanical systems,” he explains. “Once we got the hard demo done, we were able to start the foundation work in the fall of 2021.”
Goldberg adds that from that point, “we are a little over two years ... to substantially completing the building.”
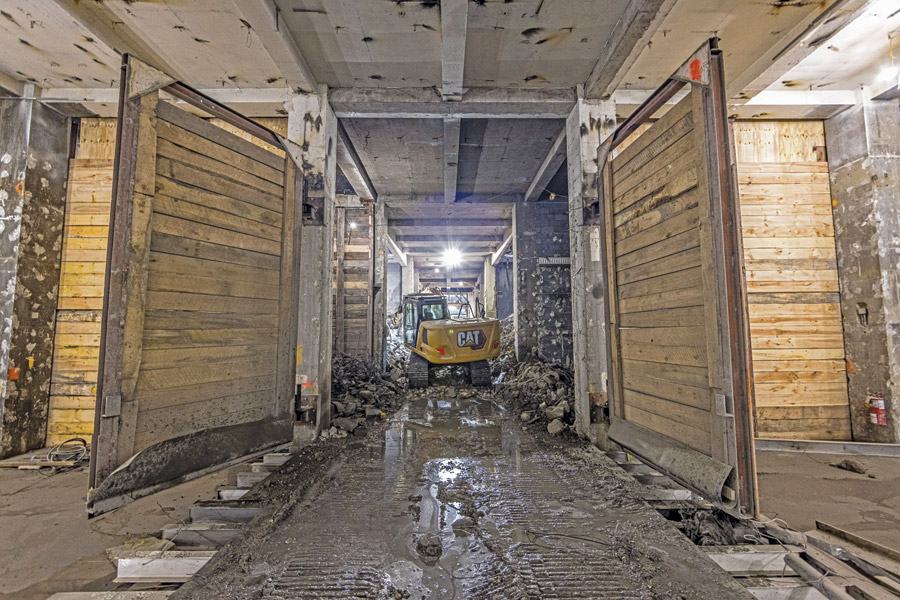
For One Madison's massive demolition effort, the project team converted the old structure's elevator shaft into a chute that shuttled debris down to a giant enclosure in the basement.
Photo by Max Touhey for AECOM Tishman
Long Road
SL Green, which bills itself as Manhattan’s largest office landlord, acquired One Madison and 5 Madison—both formerly in the Metropolitan Life Insurance Co. campus bordering Madison Square Park—in 2005. For years, the company leased One Madison to blue-chip tenants such as Credit Suisse, but it sold the clock tower building, says Edward Piccinich, chief operating officer.
“[We] focused our efforts on the reimagination of One Madison,” he says.
SL Green moved ahead in 2018, soliciting bids for expanding One Madison. In 2020, it tapped Hines and the Korea pension service as partners, echoing the ownership of its One Vanderbilt tower near Grand Central Station in midtown. The developer also reconvened much of that structures’s project team, including Tishman, Kohn Pedersen Fox, Severud and Jaros, Baum & Bolles as mechanical engineer.
“We gutted the whole building. We demoed the top five floors.”
—Dan Leiro, Vice President of Operations for Architectural and Structural Trades, Tishman
SL Green ultimately selected a Kohn Pedersen Fox-Severud design after months of analyzing the project's main premise: using the old building’s bones but fortifying its superstructure to support a new tower, says Andrew Werner, senior associate principal and project manager at Kohn Pedersen Fox.
“The design continued through 2019 and 2020 during the pandemic,” he says.
The building already has signed IBM to lease 328,000 sq ft of lower floors in the revamped 10-story podium and asset manager Franklin Templeton Investments to lease 347,000 sq ft in the 18-story upper tower. Each anchor tenant takes one of the “garden” feature floors—IBM on the 10th, Franklin Templeton on the 11th.
Other tenants include Chelsea Piers Fitness that is occupying 56,000 sq ft and Michelin-starred chef Daniel Boulud, who will open a steakhouse and French open-air market style space.
Other building features include an 11,000-sq-ft roof deck, a 7,000-sq-ft tenant amenity space and other terraces and “sky gardens” providing an acre of outdoor space.
The developers have also partnered with the non-profit Madison Square Park Conservancy to support improvements to the park, drawing recognition from the area’s City Council representative Carlina Rivera, who lauded “the partnership of SL Green to reinvest in the neighborhood.”
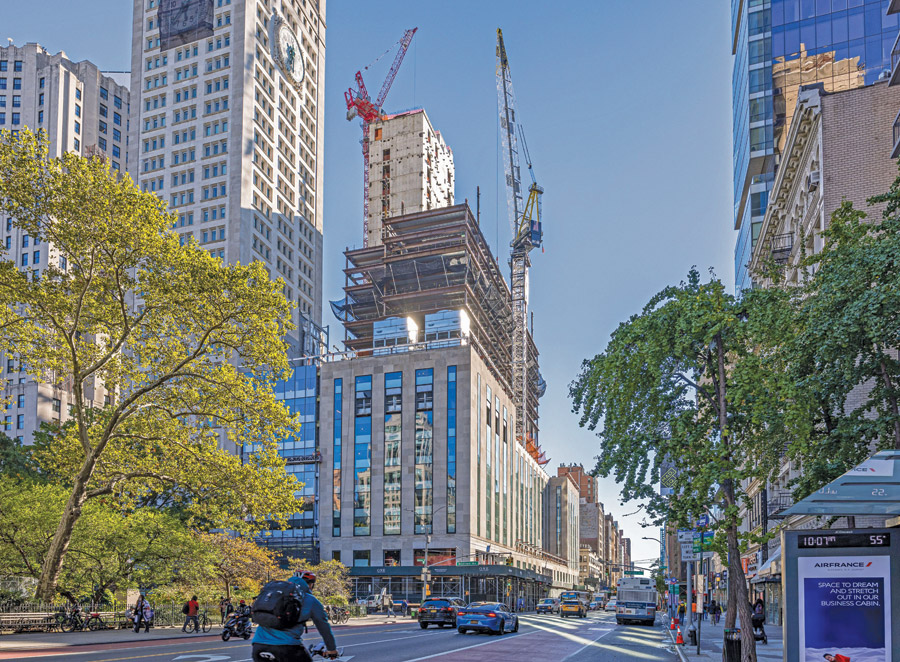
The project used multiple tower cranes, including an external climbing crane that did multiple vertical jumps to erect the upper floors.
Photo by Max Touhey for AECOM Tishman
Design Competition
SL Green’s 2018 design competition asked five architects for their visions of the site, Piccinich says. But the Kohn Pedersen Fox original concept largely held up.
“The development plan remained intact with respect to scope and scale,” he says.
The main thrust was adapting a 1950s building to today’s office tenants, Werner says. “We wanted to harvest what was efficient in the existing building and retain historic elements important to the neighborhood and to the character of the building,” he says. “We then infuse it with what today’s tenants need—access to light and air, [modern] elevator systems and life safety systems, power and data.”
The design avoids added structure to carry the new tower’s steel superstructure load, says Annie Savage, director and senior designer for the project at Kohn Pedersen Fox.
“The existing core was extremely inefficient. We saw the ability to start from scratch.”
—Andrew Werner, Senior Associate Principal and Project Manager, Kohn Pedersen Fox
“We came up with a scheme of megacolumns threaded through the building … to eliminate the need for additional horizontal structure,” she explains. “We were really able to maximize the floor-to-floor heights and create unique and desirable floors at the concrete podium and then [support] this new steel tower above.”
That support includes the structure’s new concrete shear wall, transfer trusses at the feature floors and the 13 megacolumns, which entailed fortifying nine existing columns and adding four new ones, Leiro explains.
“The existing building was not designed to take the load of a steel tower on top of it,” he notes. “To create the megacolumns, we enlarged the footing and then the column itself. The point loads from the truss under the new structure [will drive] down to these enlarged columns and … to the foundation.”
The structure’s design also called for a rebuilt core, Werner says. “The existing core was extremely inefficient,” he says. “We saw the ability to start from scratch.”
The structural plan also created wider and clearer floor spans, according to Savage.
“That really enabled some amazing views and a lot of daylight and a loft-like space,” she says.
The design also showcases some of the structural elements, with the truss visible on the interior, Piccinich says. “[It] can be seen at the connection between the old and new building and offers a unique architectural feature,” he says.
Encased by high-end architectural glass, the fiberglass-clad truss is a main focal point, according to Blackman. “There will be a lot of eyes on that,” he adds.
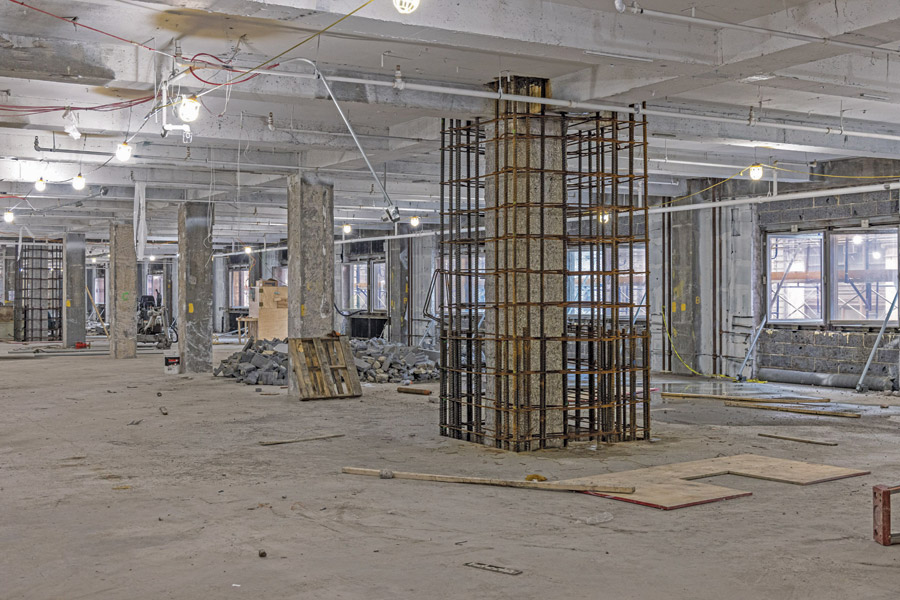
To support trusses carrying the new tower’s load, the design called for 13 megacolumns, including nine from the original structure that the project team enlarged and fortified.
Craning Up
A central construction theme of the project was maximizing the schedule, advancing it where work could take place even if it was just in portions.
After completing most of the demolition activity, foundation work began right away, with a large amount of rock excavation to dig new footings and elevator pits, Leiro explains. But the project team had already begun construction work on the superstructure as well.
“We said, ‘What can we do to accelerate the project?’” he says. “We decided to work on the megacolumns and the superstructure where we could because that was outside of the demolition zone. We actually passed each other—as demolition was coming down, we were building these megacolumns up.”
Fortifying and expanding the old columns entailed scarifying the concrete, applying a bonding agent, adding a rebar cage and then pouring new concrete, Leiro says.
Another effort used to speed work was tasking an ironworkers crew to embed plates—a bolted connection—into the concrete shear wall as it went up so this structure could later accept the steel floor framing beams without the need for additional welding, the Tishman executive explains.
“It was all very tightly scripted with military precision.”
—Rob Blackman, Executive Vice President, Tishman
The project team also maximized time in its crane selection and setup. While the existing podium could support the concrete tower crane, using shoring jacks tied back to the ground, the steel erection equipment—an exterior climbing crane that made jumps up the building as the superstructure rose—was too heavy, Leiro says.
The team decided to install the truss set to take loads from the tower and use it to support the crane, he says. That required two tight weekends of street outages, the first to complete the truss and a temporary “grillage” support tied to the shear wall and the second weekend to truck in and install the crane, Blackman says.
“This would be coming in on a Friday night, working through the weekend and taking it apart by Sunday night to be back to business as usual on Monday morning,” he says. “Bringing in all of the crane parts with permit loads that have to be timed to come across the [George Washington] Bridge at 2 or 3 in the morning—it was all very tightly scripted with military precision.”
Those strategies helped the building team top out last December, with work this year on the exterior—a process also streamlined by installing prewelded tabs on the steel frame as it rose to accept the glass and gunmetal-colored aluminum fin curtain wall pieces, Leiro says. The team also enlarged openings in the podium to install new full-height windows, he says.
Installing specialty glass to frame the truss on the feature floors was an added challenge, with the team renting a crane attachment with counterweights and a rotating cup from Germany to place the four-ply, 10-ft-wide, 18-ft-tall slabs of laminated glass, Leiro says.
“It’s really heavy glass,” he says. “It was a complicated installation.”
Mechanical Puzzle
Maintaining mechanical systems for the adjacent clock tower throughout the entire process—and mapping how to transfer over to new permanent systems—was another challenging project task, impacting each stage of construction, Blackman says.
The team first set up temporary systems in sections not slated for demolition—including a cooling tower on the 10th floor and MEP gear on the eighth floor—and then transferred capacity before demolishing the old equipment, Blackman says. The project team has maintained service as it builds out permanent mechanical systems for both One Madison and its neighbor.
Leiro says later this year “we’ll be setting up the hot cut, or the switchover to the permanent systems.”
A final touch will be cladding those sections—where the team still needs to complete final exterior and interior work after the switchover—with limestone from the same Alabama quarry that provided the facade for the original towers, Goldberg says.
The final product also will have a slate of sustainable features—including air filtration systems, monitors for volatile organic compound gases, maximized daylighting and outdoor spaces, as well as high-performance glass and MEP equipment, Werner says.
The project is aiming to obtain LEED Gold and WELL building certifications.
One of the most effective sustainable features is simply reusing the old structure. “They saved about 40% of emissions just by retaining that building,” Savage says.
Post a comment to this article
Report Abusive Comment