Lafayette, Ind.’s $51-million public safety building will house the city’s police force and double the size of the department’s current space in the Lafayette City Hall.
The project, which will put the public safety department in its own space for the first time in 156 years, presented challenges for the construction team as a result of the building’s location on a single city block in downtown Lafayette and a tight budget for a 70,000-sq-ft, four-story building with an adjacent 468-space parking garage.
The city wanted to create a structure that would house not only the 152-member force, and meet their future needs, but engage the public.
“The design is really about the concept of community policing—the relationship between the officers and the community at large,” says architect Brandon Hoopingarner of Indianapolis-based American Structurepoint Inc., the architect-of-record. “It’s one of the reasons it is located in downtown Lafayette as opposed to being out at a distant location.”
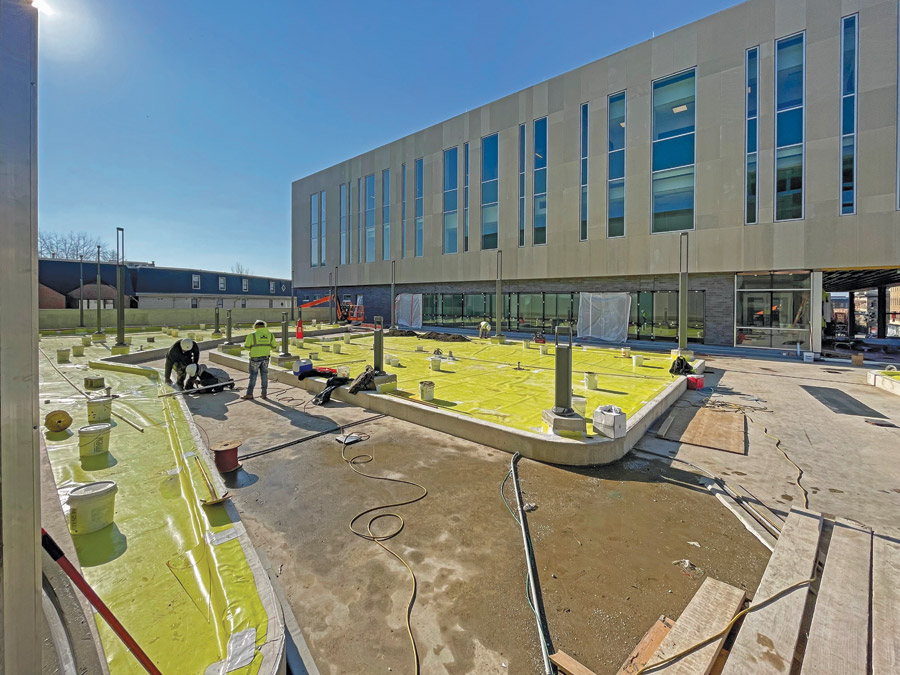
A city plaza that was added to the plans enabled work on the building and parking garage to proceed simultaneously.
Photo Courtesy of Kettelhut Construction Inc.
Optimizing Construction Management
A construction-manager-as-constructor (CMc) method was used in the project. In CMc, the construction manager acts as an advisor to the owner and manages both design and construction even though the project has a general contractor in addition to the construction manager. Kettelhut Construction Inc. of Lafayette acted as both general contractor and construction manager, hiring subcontractors, and providing a guaranteed maximum price. From the project's earliest stages, Kettelhut advised on design and construction and American Structurepoint designed the building.
Others involved in the project included Architects Design Group of Winter Park, Fla., which specializes in public safety; Applied Engineering Services for MEP engineering; MKSK for landscape design; and TLC for camera and security design.
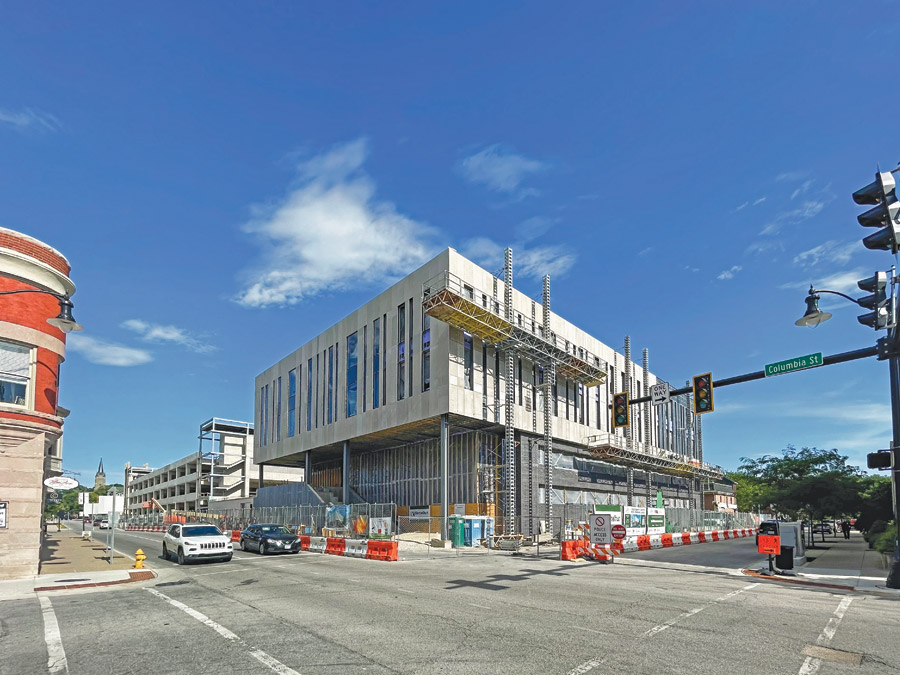
A cantilever extending from the third to fourth floors shields the first-floor public access door to the building.
Photo Courtesy of Kettelhut Construction Inc.
Teamwork
Hoopingarner says the CMc approach fostered teamwork and spurred new ideas for the building that contains spaces for administration, patrol, dispatch, investigations, information technology and evidence.
“It’s almost an RFP process to get the construction manager on board at the same time as the design team,” he says. “You develop the project with the construction professional as well as the architect professional and with the owner.”
Early plans for the building envisioned a three-story structure with an attached parking garage. But those plans changed as the team considered the various needs of the building.
“The original design of the facility had a larger footprint, but was a shorter building,” says Hoopingarner. “We ended up raising the building a floor taller [during design], which allowed us to separate the building from the parking garage. That is better from the viewpoint of safety planning.”
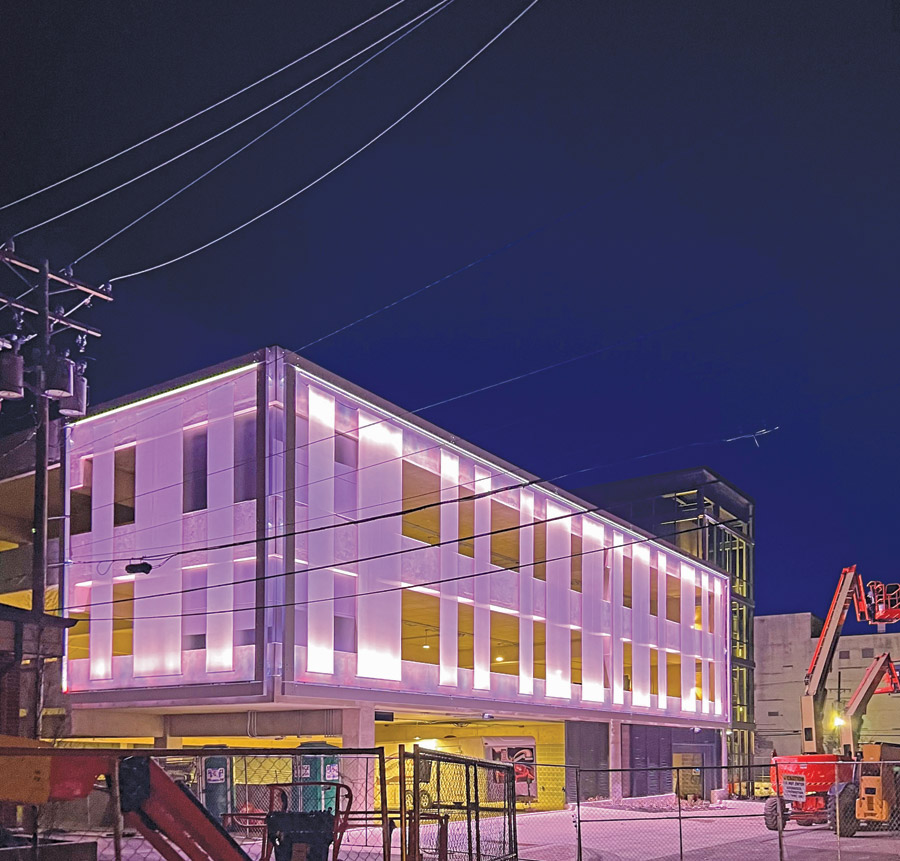
Adjustable LED lighting allows the city to light the safety center’s parking garage in any color.
Photo Courtesy of Kettelhut Construction Inc.
The solution to separating the two buildings came in the form of a cantilever on the third-to-fourth floors. The cantilever stretches over the interior of the first floor and an exterior public staircase that leads from the first to the second floor where an open air plaza was created between the public safety building and the parking garage.
Both the plaza and the first floor have entries to the police department. Public parking is on the top three floors of the garage and is segregated from police parking on the first floor.
The plaza, which will have green space and a gazebo, also was designed so that movies can be screened on the side of the parking garage.
“It’s a good place for break areas for employees, and it allows one side of the building to get sunlight, which is very much appreciated by everyone in the building so they aren’t working in a cave,” says Hoopingarner. “Every office on the perimeter of the building has natural light coming in, which they didn’t have when the parking garage was against the building.”
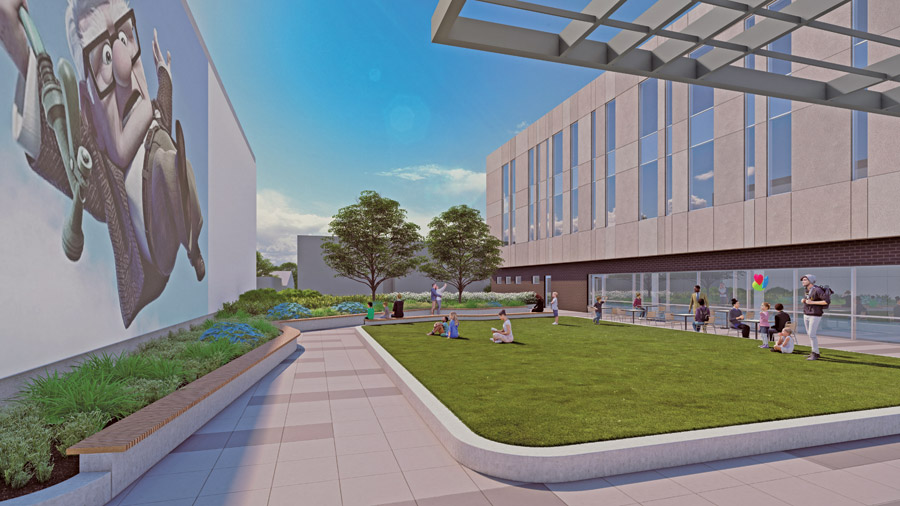
The public will be invited to enjoy movies or relax on the civic plaza that was created between the public safety building and parking garage.
Rendering courtesy of American Structurepoint
The building’s limestone exterior allows the building to blend in with a nearby historic district, which contains early 1900s-era townhouses and is separated from the public safety building by an alley.
One of the challenges was to protect the nearby historic district, particularly as the foundation was laid.
“As part of the foundation system we had to do ram aggregate piers,” says Alex Gonzalez, executive vice president for Kettelhut. “Those cause vibrations in the soil so we had to monitor that and we had to monitor the historic buildings next to us to make sure cracks weren’t worse than when we started or that there were any settlement issues there. Then we brought the public safety facility out of the ground with structural concrete.”
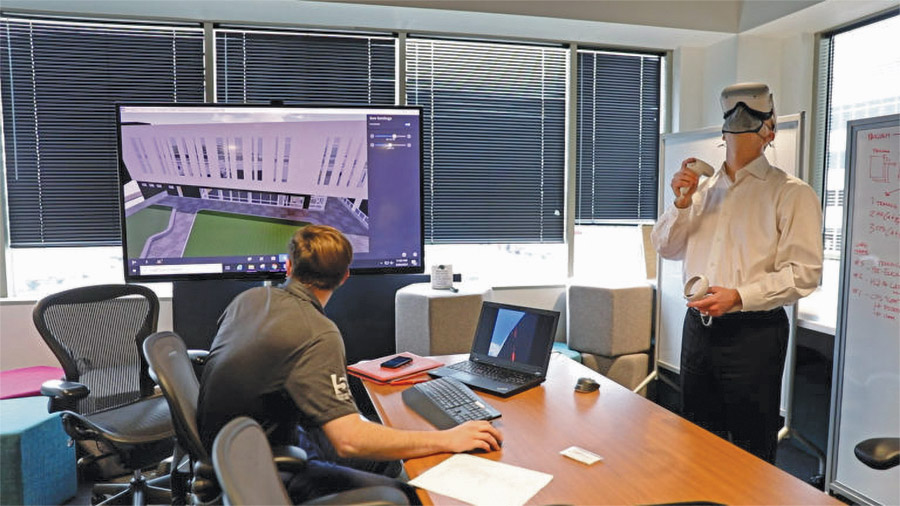
American Structurepoint provides city of Lafayette officials a virtual reality tour of the safety center during design.
Photo courtesy of American Structurepoint
Plaza Aids Construction
The plaza benefited contractors who used it as staging ground. It enabled construction of the two buildings to proceed simultaneously.
“The good part about it was that it gave us a break in between the buildings, which gave us additional laydown space,” says Gonzalez. “We could build the police station and the parking garage at the same time.”
“You develop the project with the construction professional as well as the architect professional and with the owner.”
—Brandon Hoopingarner, Architect-of-Record, American Structurepoint Inc.
The difficulty arose when that space was no longer available.
“It was a timing question of when logistically to take that space away and build the amenity deck,” says Tom Morlan, senior project manager for Kettelhut. “Because, at some point, we had to take all of our equipment out of there.”
It became a just-in-time delivery jobsite for several months because everything was under construction and there was no extra space on the project site, Gonzalez says.
“We’d store materials off site and deliver them to the job as needed,” he says.
Building the two structures simultaneously saved money, which was a priority for city officials who timed construction for when they expected less competition.
“We kind of tried to time the bid at a time when we thought there would be a lot of interest,” says Lafayette Mayor Tony Roswarski. “It’s not the largest project in Indiana, but it’s a good-size project for central Indiana and we hit the timing just right.”
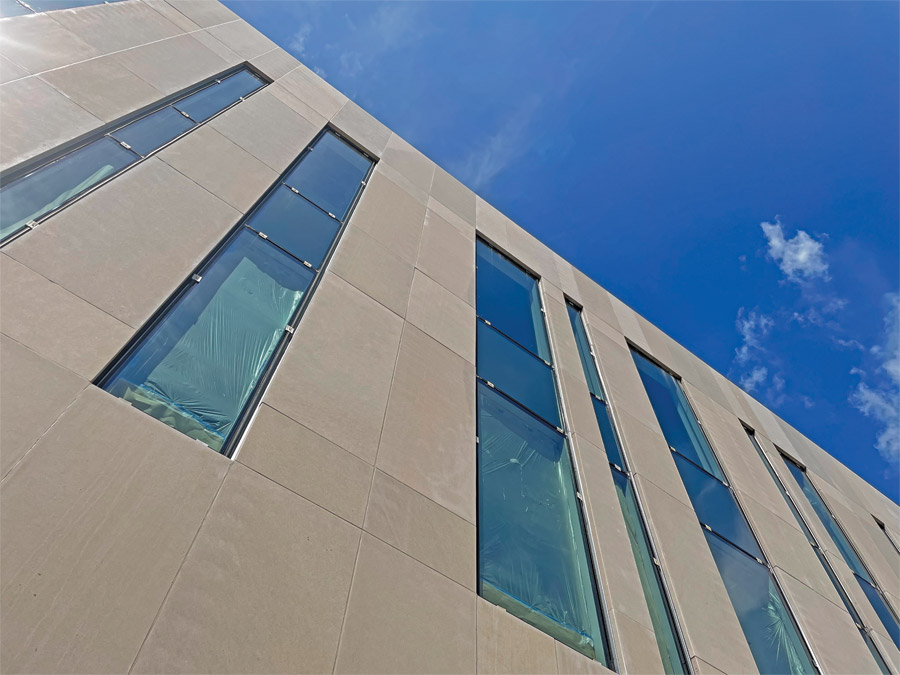
Limestone panels on the building’s exterior complement nearby historic buildings.
Photo courtesy of American Structurepoint
Saving a Historic Building
Another challenge was to preserve part of an early-1900s-era brick building with limestone accents that was already on the site and which the city plans to repurpose as a coffee shop or other use.
“The front 5 feet of the structure, including the main storefront, was carefully disassembled and preserved off site for over a year,” Hoopingarner says. “Then it was reassembled after the construction of the parking structure was completed.”
While that may sound simple, it was not.
“It was a timing question of when, logistically, to take that space away and build the amenity deck.”
—Tom Morlan, Senior Project Manager, Kettelhut Construction
“Some of the old bricks were warped and not square,” says Morlan. “We had to integrate them with new brick on the sides. Getting enough of the old brick and some new limestone to match the old limestone was also somewhat critical to making the shapes work.”
Recreating the building’s facade and storefront required “a lot of coordination between us, the masonry contractor [James Scharer Masonry] and the offsite storage facility where we stored all the old bricks. We had to look at all the bricks, count them and then integrate and mix them in by hand so they didn’t look too awkward when they were blended,” Gonzalez adds.
Old mortar also had to be sawed off. Thanks to these efforts, most of the original bricks were used in the facade—only 15 to 20 original bricks remained after construction.
When the project was nearly complete in May, Roswarski was pleased with the CMc process, which is also being used on construction of another project—the city’s $22-million public works department, which recently broke ground.
“It helped to have the construction people talking from the very beginning and sharing input, thoughts and ideas,” Roswarski says. “It helped us end up with a better project, both from a design and cost perspective. I think the architect and construction team worked well together.”
Post a comment to this article
Report Abusive Comment