With a design that focuses on natural elements, Harwood No. 14, the newest office tower to rise in Dallas’ Harwood District, takes the approach of seeking harmony between the indoors and outdoors.
This 27-story building will reach an elevation of 388 ft and feature approximately 344,400 sq ft of office space, 17,000 sq ft of retail at the ground level and a 17,000-sq-ft rooftop sky garden.
“Harwood No. 14 will be the latest addition to the Harwood District’s master plan development,” says Oliver Barbier-Mueller, managing partner at Harwood International. “With 6 million square feet of future development in the pipeline, our focus is to populate the district with iconic buildings and street-level experiences to satisfy our existing and future tenants.”
The tower—Harwood’s tallest to date—was designed with a focus on utilizing natural elements and creating features such as sky gardens and green spaces, an approach that the developer utilizes on many of its projects.
In a video for Harwood International in 2020, architect Kengo Kuma said of Harwood No. 14’s design: “Through this design we have achieved a unique and thoughtful look among a diverse Dallas scenery. The feeling of the outside facade is not a solid one. Instead, it has holes and delicate curves that percolate sunshine.”
Kuma added: “The inside lobby presents soft steps that adjust with each different level. This creates harmony between the green outdoors and the inside lobby, and we have designed it so you are able to experience the greenery from inside the lobby.”
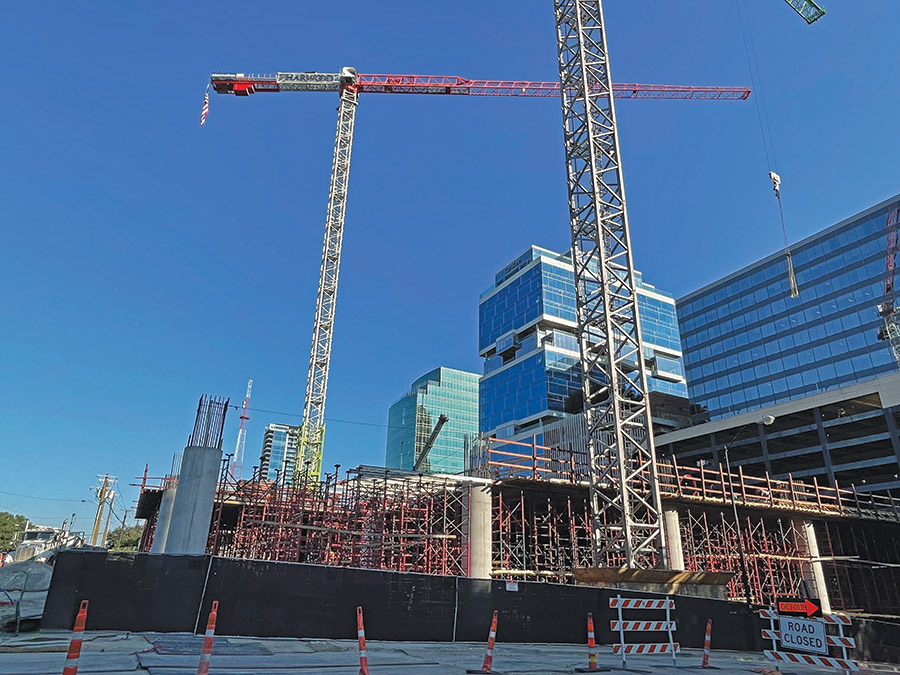
Harwood No. 14 is Harwood International’s tallest office tower to date. The Class AA office tower is centrally located in the 19-cityblock Harwood District in Dallas.
Photo courtesy of Manhattan Construction Co.
Team building
During the early stages of design, the owner was looking to build a project team “consisting of people that could work very closely to design, estimate and troubleshoot in a highly integrated fashion,” Barbier-Mueller says. “We had previously worked with Manhattan when we developed Frost Tower (Harwood No. 7), and we appreciated their team approach to design-build. Similarly, we had the opportunity previously to partner with Kengo Kuma and Associates on the Dallas Rolex building,” a project that garnered the Best Project award in the office category as part of ENR’s 2019 Global Best Projects competition.

Crews place concrete on site in late September. The elevated structure will consist of about 42,000 cu yd of concrete.
Photo courtesy of Manhattan Construction Co.
Manhattan Construction Co. serves as construction manager on the project, and the design team is comprised of Harwood Design Factory, Dallas, as architect of record; Kengo Kuma and Associates, Tokyo, design architect; and Corgan, Dallas, as associate architect. Additionally, L.A. Fuess Partners Inc., Dallas, serves as structural engineer; Halff & Associates, Dallas, as civil engineer; and BLUM Engineers, Dallas, as MEP/sustainable design engineer.
“It was a negotiated project,” says Andrew Reese, senior project manager with Manhattan. “We provided preconstruction services and collaborated with the client and design team throughout the design. We worked hand in hand with the designers from early concept phase to provide cost feedback throughout the design process until we could get to a construction set of documents that were bid to the specialty subcontractor market.”
“Visually, the design looks like a flowing waterfall or fabric in the wind.”
—Andrew Reese, Senior Project Manager, Manhattan Construction Co.
The preconstruction effort and early engagement with the contractor enabled a speedy ramp up, Reese adds. “The real genesis to the Harwood No. 14 team came from collaborating on another project of theirs throughout 2019 and early 2020,” he says. “The already cohesive team moved seamlessly into the design, drawing and cost budgeting work to launch this project.”
Tech Forward
With a strict schedule and set commitment dates for tenants, Manhattan’s preconstruction team built the schedule using Fuzor’s 4D technology—a virtual design and construction (VDC) software.
“Using this 4D technology, we built the building virtually first and were able to show the Harwood team how each component of the construction goes in place in a time-lapse fashion in video form,” Reese explains. “It’s a powerful visual, but more importantly, it validates the schedule we devised and offers a deeper look into sequencing and constructibility. With that insight, we could make refinements to enhance the schedule before a shovel ever hit the ground.”
Other key technologies such as BIM, 3D imaging and renderings were also used to communicate between the client, design team and contractor. And with part of the design team being in Tokyo and the other part in Dallas, those tools proved critical, Reese adds.
As the team moved into construction in early 2021, BIM modeling and clash detection through Navisworks and Procore BIM was being used mostly for MEP coordination but also for architectural and structural features, Reese says.
“Among the building processes, what we are doing to enhance the speed of installation and ensure quality is the prefabrication of the rough-ins for the plumbing and electric on each floor,” he continues. “This includes in-slab rough-in with wire already pulled as well as prefabricated electrical boxes and wiring for in-wall and above ceiling rough-in.”
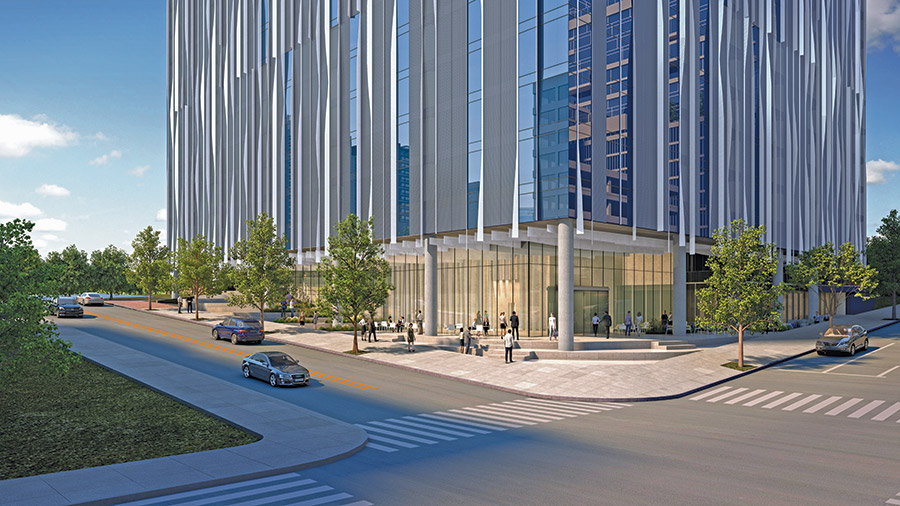
Harwood No. 14 builds on Harwood International’s design focus on natural elements.
Rendering courtesy of Corgan
Elaborate Exterior
Harwood No. 14’s modern design includes a distinctive feature in its exterior fins, which are part of the curtain wall system and will span 34,200 linear ft.
“Visually, the design looks like a flowing waterfall or fabric in the wind,” Reese says. The fins vary from 4 in. to 16 in. in depth and 15 ft to 45 ft in length and will be placed vertically on the structure.
“Due to the combination of the bedrock and the elevation change, there was minimal excavation compared to buildings of this size and nature in other locations.”
—Andrew Reese, Senior Project Manager, Manhattan Construction Co.
“Each fin is unique in its depth, orientation from the building or length,” Reese says.
To ensure precision, the construction team used 3D modeling and digital design files to detail and coordinate scope of work with designers and specialty contractors.
“We lab-tested the performance of the system using a mock-up of a 30-foot-high by 30-foot-wide section of the facade at an offsite facility to confirm wind effect and wind-driven rain on the fins and the curtain wall,” Reese says.
The fins are comprised of an aluminum plate material that are laser cut into unique shapes. The structural components of the curtain wall system are also aluminum, Reese adds.
Kuma says “the outer design of this building is composed of extremely fine lines. These lines sway around as they connect the ground to the sky. With these curves and the different openings, we are able to control Dallas’ blinding sunlight and construct a relaxed interior.”
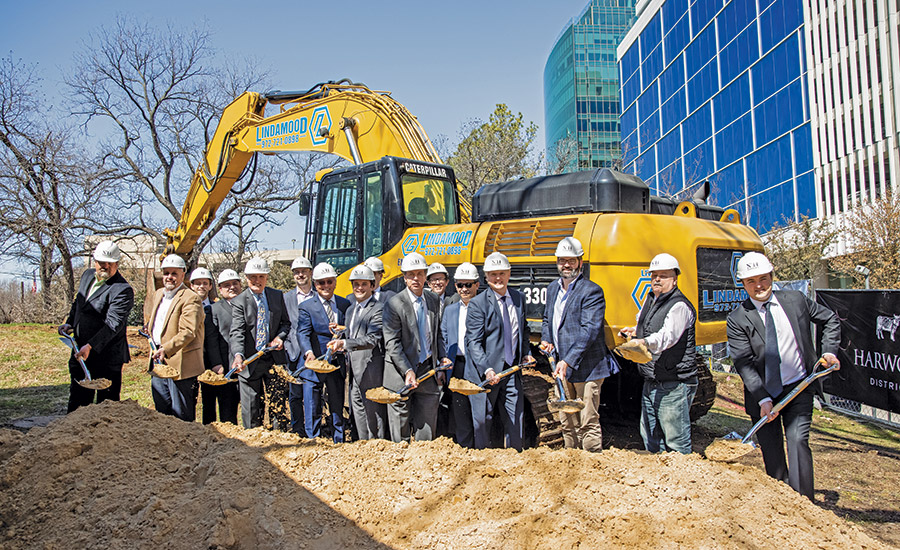
The project team and stakeholders celebrated the project’s groundbreaking in early 2021.
Photo by Rob Underwood
Groundwork
Given that the existing site was green space and surface parking, excavation was able to begin almost immediately, Reese says.
The interior ground floors of the building take advantage of a 25-ft elevation change from the west to east side of the site. As a result, the second floor’s ground floor is connected to the first floor’s ground floor by a monumental stone staircase surrounded by terraced stone steps and interior landscape beds to follow the shape of the natural terrain. The monumental staircase and terraced steps will be stone clad in white granite.
“This element, coupled with the low-iron structural glass and the stone-clad central core walls in the lobby, allows for the outside natural elements to come into the building in a grand way,” Reese says.
Kuma explains that “by introducing this incline to the inside of the building, we are able to construct a reverberating relation between the outside and the inside, and this incline also brings warmth and makes us feel like we’re back in nature.”
To support the elevated structure—which consists of about 42,000 cu yd of concrete, 560,000 lb of post-tension cables and 3,600 tons of supporting rebar—the team installed a total of 104 drilled piers, ranging from 36 in. to 84 in. in diameter and penetrating up to 30 ft into bedrock.
“Due to the combination of the bedrock and the elevation change, there was minimal excavation compared to buildings of this size and nature in other locations,” Reese explains. The project team excavated 20,000 cu yd of soil, and “the excavation material was mostly hauled off, but used as structural backfill where available. There was nothing unusual in the excavation findings except that this rock is extremely hard,” he adds.
While the slope across the site constricted the project team’s site access, “luckily we are able to occupy the property adjacent to the north for safe layback of the excavation and created a ramp down into the site,” Reese says.
But the location of the building on a tight site has presented access and space planning challenges. Luckily, all of the neighboring properties in the district are also owned by client Harwood.
To minimize the impact on existing buildings and tenants, the Manhattan team organized a lane closure and access plan to keep most construction traffic on the project’s west side, away from the district’s core.
Meanwhile, material was only hauled out through the adjacent property to the north. Because the other three sides of the property border city streets, the project team will take one lane of Harry Hines Boulevard for most deliveries and concrete pumping.
“We are abiding by the city of Dallas’ work hours due to the residential properties across Harry Hines Boulevard, so that means we can’t pour concrete or have any noisy work before 7 am,” Reese says.
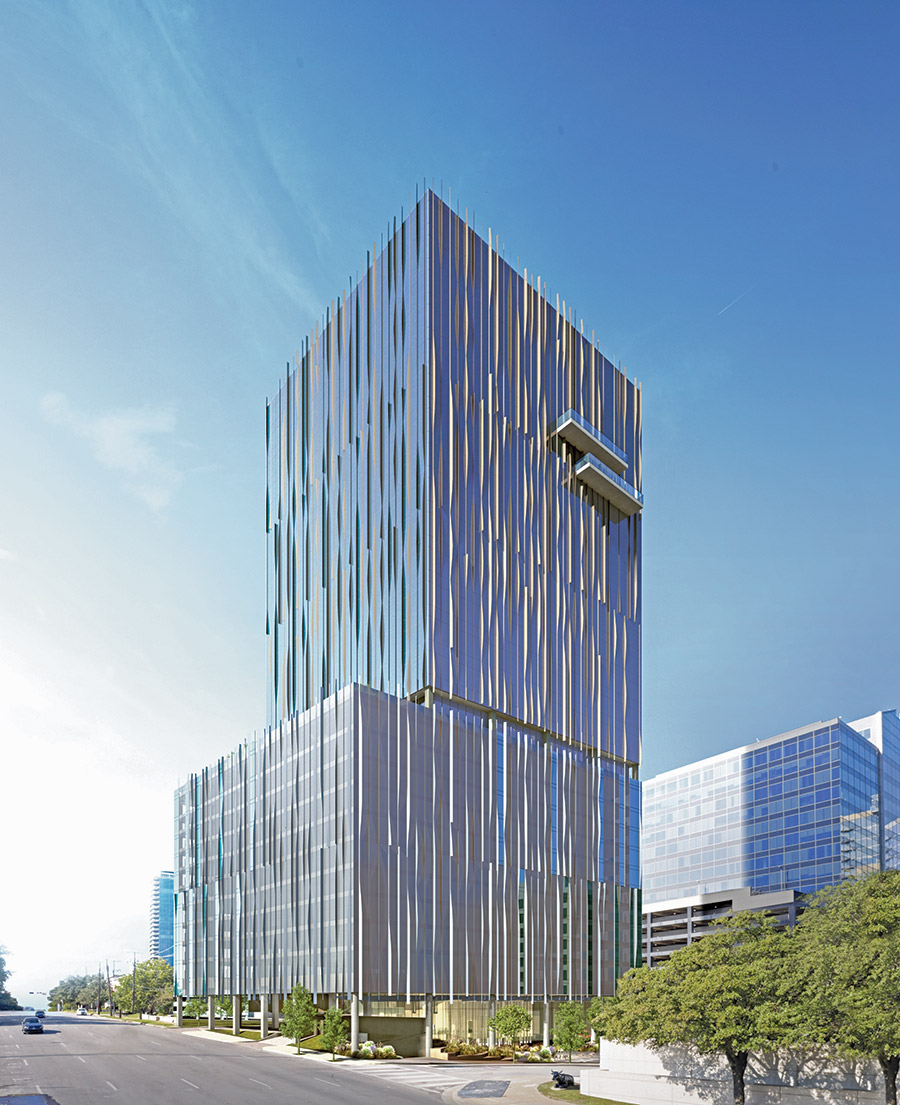
The building’s iconic exterior fins are part of the curtain wall system. Each fin varies from 4 in. to 16 in. in depth and 15 ft to 45 ft in length.
Rendering courtesy of Corgan
Staying on Course
One of the project’s major challenges so far has been navigating the pandemic market. During the early parts of the preconstruction process, Manhattan worked with the architectural team and Harwood to finalize and approve designs to gain authorization to secure and purchase key trades, including structure, MEP and the curtain wall facade, Reese explains.
“In turn, that gave the trades the ability to lock in commitments with downstream vendors and suppliers early. The timing of securing those contracts early made use of the eager specialty trade partner market and protected the project and client from material delays and supply chain issues,” he says.
Because of that early lock-in strategy as well as the project’s early ramp up, the team hasn’t encountered any major unforeseen issues with materials, Reese adds.
“Additionally, Manhattan has an internal team of people keeping an eye on the supply chains and anticipating potential impacts to downstream material availability and escalation to guide our clients through potential challenges,” he says.
Staffing the project has also been progressing smoothly so far. While a lack of trained workers still remains a general concern, “our specialty trade partners have been doing a great job keeping our project staffed with the right teams,” Reese says.
Although the project team is not pursuing any LEED certification, the city of Dallas has a comprehensive green building standard for new residential and commercial construction, which did require Harwood No. 14 to include some sustainable design and use elements, Reese says.
The project team has completed 90,703 work hours through August and is on track to remain within budget and complete work by summer 2023.