Duke Energy�s $2.88 billion coal degasification power plant under construction on 100 acres in Edwardsport, Ind., is a colossal endeavor with an endless number of firsts.
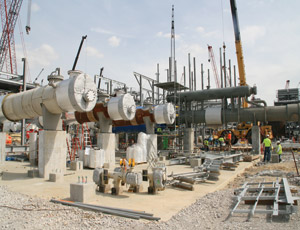
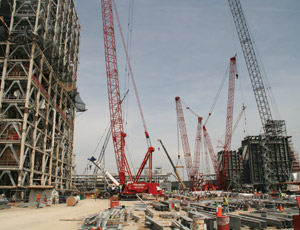
The unprecedented nature of the project has forced Duke to increase its original cost estimate by 48 percent for the 618-MW Integrated Gasification Combined Cycle (IGCC) plant. The original estimate pegged the plant at $1.95 billion.
When completed in September 2012, the IGCC facility will be one of the cleanest and most efficient coal-fired power plants in the world, according to Duke published materials. It will emit less sulfur dioxide, nitrogen oxide and mercury than the plant it replaces � while providing more than 10 times the power of the existing plant.
GE Energy is the owner of the new plant�s process technology, which will rely upon a coal gasification system to convert coal into a synthesis gas (syngas) and produce steam. The hot syngas is processed to remove sulfur compounds, mercury and particulate matter before it is used to fuel a combustion turbine generator, which produces electricity.
The heat in the exhaust gases from the combustion turbine is recovered to generate additional steam. This steam, along with that from the syngas process, then drives a steam turbine generator to produce additional electricity.
Mike Womack, Duke�s project manager and vice president - IGCC, says numerous changes during the detail design phase led to significant increases in material quantities.
�While there was no change in the overall process, there have been scope changes where we had to make a conscious decision to do something different,� Womack says. �The most conspicuous change, which resulted in an increase of almost $100 million, was due to a modification in the method of dispersing the wastewater.�
Originally, the contractor planned to inject wastewater into deep saline aquifers located about 4,000 to 8,000 ft below the surface, but the plan was based upon the initial understanding of the wastewater�s composition.
�GE determined that it was possible there would be more of certain elements that would change it to a hazardous wastewater classification,� Womack says.? �As a result, the wastewater disposal method was changed to zero liquid discharge.�
In addition, the required amount of above-ground pipe was originally estimated to be 350,000 linear ft, but following detail design the number ended up closer to 600,000 ft. Structural steel for the process area was expected to be approximately 11,000 tons, but reached nearly 20,000 following detail design.
Jeffery W. McNeely, Duke�s senior direct of project controls, says management of the project is performed by an integrated team consisting of both Duke and Bechtel employees. Heading construction management for Bechtel is Rich Marl.
While Bechtel�s Houston office performed design for the process areas, Sargent & Lundy LLC of Chicago designed the coal handling and water treatment systems, �the 2 biggest systems outside of the process area,� and Burns & McDonnell of Kansas City designed the wastewater disposal system and rail spur.
�At the peak of the process design as many as 460 Bechtel engineers were involved,� Womack says. �That would have been much higher if they�d also been responsible for the peripheral work.�
Womack says the project�s primary design challenge was its uniqueness.
�This is a first-of-its-kind design, so there�s no template to go by,� he adds. �If you told me, �I want to build a conventional 3-on-1 combined cycle plant,� I could easily find some existing designs.
Post a comment to this article
Report Abusive Comment