Skanska USA was out to prove a point when it fit-out its new Manhattan offices. It wanted to show clients it could build a LEED Platinum office at a reasonable premium and produce long-term energy savings. And it managed to mark the feat in the landmark, 102-story Empire State Building.
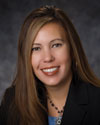
The $4.6 million effort cost $210,000 more than a typical Class A office fit-out, a premium of less than 5%. And since opening the 24,400-sq-ft 32nd-florr office last year, Skanska’s energy expenses dropped 46%, which, extrapolated over the 15-year lease, would produce savings topping $550,000. All of that complemented earning 44 points on the 57-point LEED scale – enough for the highest rating, Platinum CI.
Skanska served as its own construction manager, teaming with Cook + Fox as architect and Cosentini Associates as mechanical engineer.
The 78-year-old skyscraper was green-friendly, thanks to an original interiors design that maximized natural light and air ventilation, says Steve Pressler, executive v.p. and area general manager of Skanska New York. “We took advantage of all of those features and just continued on those design concepts,” he says. “Glass office fronts just help the daylight carry through even further.”
The team faced its share of tall tasks. It executed in a brisk 11 weeks, shaving a month off the normal schedule as Skanska tried to enjoy a rent-free bonus. A big contributor to that efficiency was utilizing the “racetrack” configuration around the building’s giant 67-bank elevator core to create a four-station sequencing of trades, staging, and materials circulation. The team used a circular progression, allowing early trades to complete tasks and move to the next station as other trades followed. The approach not only sped up construction but also simplified supervision, minimized trade conflicts, and enhanced safety.
And of course, the project had multiple sustainable features. Throughout the workspaces, training rooms, conference rooms, kitchen, and other spaces, the finished product has cork for flooring and paperstone for furniture; low-VOC paints and finishes; low-flow toilets and other water-saving plumbing; Forest Stewardship Council-approved wood-based materials; and a lighting system that uses 35% less energy than standard minimums, thanks to sensors within individual fixtures that monitor daylight and adjust bulb usage.
Perhaps the biggest contributor was a 10.5-inch raised floor air distribution system, which taps into four individual towers that can take in exterior air and operates more efficiently than a single large HVAC unit. It also allows for flexible placement of individual air diffusers so employees can control airflow within workspaces. And by removing overhead ductwork that blocked the top fifth of the building’s tall windows, the system allows daylight to reach 90% of the office.
Key Players
Developer/Construction Manager: Skanska USA Building Inc.
Architect: Cook + Fox Architects
Program Architect: Swanke Hayden Connell Architects
M-E-P Engineer: Cosentini Associates
LEED Charrette Consultant: Terrapin Bright Green
Lighting Design Consultant: Arup
Post a comment to this article
Report Abusive Comment