In seismic zones, construction of concrete high-rises keeps getting easier, thanks to advances in high-strength reinforcing steel used for confinement of high-strength concrete.
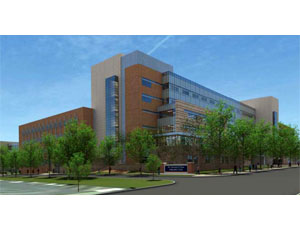
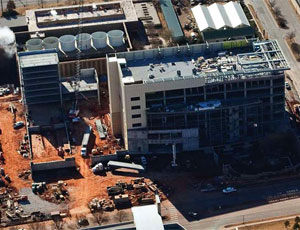
The first use of 100-ksi rebar, in a just-opening 31-story tower in Seattle, is getting high marks from the structural engineer and rebar fabricator, and the first use of a more price-competitive 90-ksi rebar in a project in nearby Bellevue, Wash., is getting even higher marks.
The advantage of using the material on both projects is reduced rebar congestion resulting from a reduction in horizontal rebar in columns and shear-wall boundary elements—by 40% for 100 ksi and 30% for 90 ksi, compared to standard 60-ksi steel. That means less field labor, less material that is lighter in weight, less hoisting, fewer problems threading things through the rebar and easier concrete casting. There also are fewer connections to 60-ksi rebar in beams and vertical rebar in columns and shear walls.
“The high-strength rebar prevented some real constructibility problems,” says Lyall Hadden, general manager for Harris Rebar Seattle Inc., Tacoma, which supplied rebar for both jobs—Escala in Seattle and Avalon Towers Bellevue, which topped out in early December.
Structural engineer Cary Kopczynski, of the Bellevue-based firm that bears his name, says, “Everything worked great at Avalon and Escala, but at Escala, the cost reductions...did not materialize to the extent we thought they would.”
That disappointment partly was caused by the high cost of the patented, 100-ksi rebar, made only by MMFX Technologies Corp., Irvine, Calif. The engineer expected the higher cost to be more than offset by rebar-placement savings. But any savings went to the rebar placer, Apex Steel, because its lump-sum contract was negotiated before the decision was made to use the 100-ksi rebar. The total installed cost for the 100-ksi steel was the same as for 60-ksi rebar.
Avalon’s developer-builder is enthusiastic about the 90-ksi experience, especially because it saved $100,000 on rebar compared to using 100-ksi steel, which was the original plan. The switch was made because of the lower materials cost and because of concerns about getting the 100-ksi steel in a timely fashion from MMFX, says Bill Jorge, senior director of construction in the Bellevue office of Avalon Bay Communities Inc.
The 90-ksi steel was produced by Nucor Steel Seattle Inc., which had heard about Escala and expressed interest to Kopczynski about competing in the high-strength-rebar market, says the engineer. “We came up with the idea” of using the standard steel specification and pushing the material up to a higher strength, he adds.
Nucor then figured out the process and tested the material. The resulting fabricated-material cost of the 90-ksi steel was about 25% less than the cost of the MMFX steel, even though there was 10% more material used. Use of both had to be approved by the local buildings department.
Nucor, which owns Harris, produced the rebar using conventional steelmaking methods, which kept its cost down. The steel optimizes a standard carbon/manganese chemistry and was micro-alloyed with Vanadium to get the higher strength level while maintaining ductility, says Winky Lai, Nucor’s plant metallurgist.
The push was made possible by changes in ASTM A615, the rebar specification, says Lai. Smaller rebar sizes were included in the Grade 75 specification for high-strength rebar. Also, 80-ksi minimum-yield-strength steel was added.
“Now, we have the competition we lacked with Escala, which is good for the marketplace,” says Kopczynski.
Not to be outdone, MMFX says it is introducing a more cost-effective, low-chrome 100-ksi product in the first quarter of 2010. The chrome was for corrosion resistance, which is not needed for high-rises. “This steel will be available in the marketplace at a modest price increase over conventional reinforcing steels and is expected to reduce steel content by 25% to 40%,” says Amy Van Amburgh, an MMFX vice president.
Future use of 100-ksi steel will be eased by the American Concrete Institute’s “Design Guide for the Use of ASTM A1035 Grade 100 Steel Bars for Structural Concrete,” on course for publication early next year.
As far as choosing 90-ksi or 100-ksi rebar for his next high-rise, Kopczynski says he will evaluate each project and let the bottom line make the determination. “The beauty of it is that we have another tool in our toolkit,” he says.
Key Players
Escala
Developer: Lexas Cos.
Architect: Thoryk Architecture; Mulvanny G2 Architecture
General Contractor: JE Dunn Construction
Structural Engineer: Cary Kopczynski & Co.
Avalon Towers
Owner: Avalon Bay Communities
Architect: Ankrom Moisan Associated Architects PC
General Contractor: Avalon Bay Communities
Structural Engineer: Cary Kopczynski & Co.