Clock management is a critical football skill. Hard-fought games come down to decisions based on minutes left in the fourth quarter. But quarterbacks and coaches are never asked, midway through the game, to finish up a quarter early.
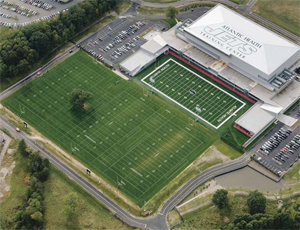
That’s essentially what the New York Jets asked their project team to do about a year into construction of the team’s new corporate home and training center in Florham Park, N.J. – finish nearly three months earlier than the original schedule in order to move in before the 2008 season. The team promised to deliver, evoking the spirit of Joe Namath, who famously guaranteed his underdog Jets would defeat the Colts in Super Bowl III three decades ago.
The project team, like the great quarterback, succeeded, and the Best of 2009 jury selected the $80 million effort for an award of merit. On Sept. 2, 2008, the team moved onto the 26-acre campus with features including a 217,561-sq-ft, two-story main building; a clearspan fieldhouse with an artificial turf practice field and 96 ft of headroom for kickoffs and punts; and three natural turf fields and another artificial one.
“Nine months into an 18-month construction schedule, we decided we couldn’t spend another year in our crumbling old training facility at Hofstra [University],” says Thad Sheely, the team’s executive v.p. for finance and stadium development. “This required a monumental level of acceleration and coordination to accomplish with zero room for error, and our construction team delivered flawlessly.”
The acceleration required many adjustments. Work had gone smoothly from the April 2007 groundbreaking through February 2008. But then the Jets issued their challenge to finish by September, says Robert Barbera, senior v.p. and New Jersey general manager for Hunter Roberts Construction Group. “Taking out two or three weeks off a schedule is a task, but taking out two or three months is a different story,” he says. “[T]he site didn’t look like it really could be done in seven or eight months.”
The biggest issue was that the building would not be enclosed in time for interiors trades to finish, Barbera says. So the team “basically shrink-wrapped” the shell, creating temporary enclosures to allow drywall, plumbing, and electrical work while others finished the exterior.
The multi-purpose facility has spaces for player training, on-field practice, lockers, physical therapy, hydrotherapy, lecture rooms, and audio-visual facilities, along with offices, conference rooms, laundry, dining, and other spaces for administration and operations. The design also aimed for what Sheely calls “a competitive advantage on Sunday” for players and coaches. That includes wrapping the building around the field to create a stadium-like enclosure and exactly matching the solar orientation of the home stadium in East Rutherford.
Barbera says Jets players and officials added a layer of game-time intensity by buying homes and relocating to the area during spring 2008. “It really was an immense amount of pressure to get that building done,” he says.
Key Players
Developer-Owner: New York Jets
General Contractor: Hunter Roberts Construction Group
Architect, Interiors Design: Skidmore, Owings & Merrill
Structural Engineer: Halcrow Yolles
Civil-Geotechnical Engineer: Langan Engineering
M-E-P Engineer: Flack + Kurtz
Landscape Architect: MKW +Associates
Specialty Consultant: Shen Milsom & Wilke
Post a comment to this article
Report Abusive Comment