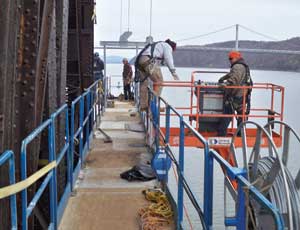
Once it became clear the bridge could be saved, the intention of reopening it with this year’s 400th anniversary of Henry Hudson’s maiden voyage called for fast-track work. A demolition contract to remove all existing steel rails, timber ties and abandoned utilities—plus contracts for steel repairs, materials and fabrication of precast deck panels—commenced within weeks of each other.
“We did modified design-build since design-build is not allowed in the state,” says Melewski. With public-private funding, railroads, various agencies and an invested community, “we had many masters to serve,” says Cooper. Stakeholders and potential contractors participated in brainstorming sessions from the beginning, adds Melewski.
After a prequalification process and mandatory site visit, Harrison and Burrowes Bridge Constructors, Glenmont, N.Y., won the general contract at the 90% design stage in 2008. Extensive negotiations with the engineer helped reduce the final contract bid by 20% to approximately $22 million, says Melewski.
The main challenge was in dealing with the strong winds over the river: “It is very difficult for our crane to swing panels, and we have men in baskets way out there,” says DiStefano. Other than that, “It is just a giant jigsaw puzzle,” he says.
The 973 puzzle pieces, as heavy as 18 tons but mostly 15 tons and 25 ft wide, were built by The Fort Miller Co., Schuylerville, N.Y. Using a custom formliner, “we cast each slab upside down to get better concrete on top,” says Scott Harrigan, Fort Miller’s managing engineer. “We wanted the bridge to be of monument-like quality...not an average concrete deck,” he says.
Fabricating crews built a steel form on a hinge to flip over each panel after casting, like a waffle maker. “That allows us to then break the bulkheads loose and flip it back over,” says Harrigan. “What was left is the nice surface cast against the formliner.” Precasting will be complete this month, he adds.
Panel placement commenced swiftly on the 1,034-ft-long west approach last fall, and ironworkers kept doing steel repairs through the cold winter, says Melewski. Panel placement started on the 2,640-ft-long east approach this spring, and work is slightly ahead of schedule. After celebrating the 400th anniversary this fall, officials will use stimulus funds to build a $2.4-million elevator up to the main deck, says Melewski.
This article originally appeared in Engineering News-Record
Using a 3D finite-element model to measure load capacity, “we found most of the losses we needed to repair are in the secondary members,” Cooper says.
Post a comment to this article
Report Abusive Comment