Decontamination PAL Environmental Safety Corp., Long Island City, started remediation work on the site in November under a contract valued at $16.4 million.
Throughout the decontamination and deconstruction process, Airtek Environmental Corp., New York, provided air monitoring at eight sites around the building for contaminates such as organic compounds, asbestos, metals and mercury, says Benn Lewis, Airtek’s senior project manager.
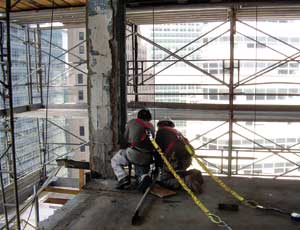
The entire remediation phase was conducted under negative air pressure containment zones within the building to prevent the release of contaminants. Each zone was wrapped in plastic and housed a negative air pressure system, which draws in air, filters it and then vents the air to the outside of the building, Lewis says. Negative air pressure zones were also created for stairwells and smaller rooms as required.
Within each zone, loose items such as desks, chairs or other materials were cleared. Ceiling tiles, walls and anything that was a fixed, such as ductwork and conduits, were also removed.
All materials, including the mechanical and HVAC equipment, were cut into pieces, wrapped in plastic and taken down in the elevators for disposal. Large equipment like the elevator motors, which could not be cut up, was wrapped in place for removal during the deconstruction phase.
Asbestos materials found in pipe insulations, floor tiles and waterproofing mastic on the interior surface of the façade walls were stripped. At the completion of this process, only the slab, walls and steel structure of the building remained.
The sequential cleanup operation started on the uppermost floors and progressed down the building in three-floor blocks. Each area was dusted, vacuumed and wiped down. The laborintensive process was primarily done by hand, although some hand tools with HEPA filters were used during the cleanup.
“We then called the regulators, the EPA, the Department of Labor and the NYC Department of Environmental Protection to do their own inspections,” Lewis says. If they agreed the area passed visual inspection for visual cleanliness, then air samples were collected to check for any remaining contaminants.
“The process was repeated for every containment area in the building, no matter how large or small,” Lewis adds.
Post a comment to this article
Report Abusive Comment