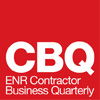
The current health care construction environment has created a heightened focus on cost reduction and efficiency. This is also a major concern of health care providers, along with improving patient well-being and comfort. According to a Mortenson survey conducted at the fall Healthcare Design Conference in Phoenix, many owners say that ongoing consolidation in the industry is a major challenge to managing growth and expanding their institutions. Here are some ways contractors can help meet this challenge.
Design matters: Design has a significant impact on the operational costs of a facility. By better understanding the life-cycle costs of design changes and enhancements, we can make dramatic improvements in facility performance. This becomes especially true when expanding or adding onto an existing medical campus. Centralized systems must be maximized to leverage their available capacity and redundancy while improving long-term maintenance.
It also can have a substantial impact on improving the patient experience, as noted by 56% of the health care providers in the survey. A strong majority also said that design contributes to important objectives such as patient outcomes and staff satisfaction.
Investment in best-practice tools and evidence- based design: Building information modeling and virtual design and construction (VDC) tools continue to evolve. Their use makes project teams more efficient during the delivery phase and allows facility managers better opportunities to improve operations and maintenance.
Advanced virtual reality technology such as computer automatic virtual environments (CAVE) allows designers, facility managers and nursing staffs to virtually test their facilities, making key design decisions and changes well before construction begins. We believe this technology will facilitate better designs at lower overall costs. Evidence-based design is another growing trend. The benchmarking of new facilities across the country—along with additional training and post-occupancy evaluation, combined with the adaptability of acuity-flexible rooms—allows improvement in care delivery with minimal capital and remodeling costs.
Process matters: Design-build and integrated project delivery (IPD) are enhancing collaboration by aligning project goals and involving parties early in the construction process. This is especially important because we are seeing bigger demands on construction schedules.
Compressed time frames are forcing design and construction teams to work together more efficiently and to take proven ideas and execute them in new ways. For instance, at the 830,000-sq-ft Exempla Saint Joseph Hospital under construction in Denver, the design team of ZGF/H+L Architecture/Davis Partnership (architects), Cator Ruma (MEP), Mortenson and its trade partners are taking prefabrication methods to a new level to meet the 35-month construction schedule.
The team made critical adjustments early in the design process before prefabrication took place, such as adjusting ceiling heights in the patient bathrooms. This was made possible by integrating into the VDC process fully prefabricated items (down to the toilet paper holders and shower rods), multi-trade racks, headwalls and exterior panels. VDC provides confidence that a rack built off site in a warehouse with HVAC components and other elements will work when it is installed in the field.
The survey respondents from the Healthcare Design Conference said they look to the AEC industry to provide a more integrated approach for delivering health care facilities. "Better processes" was ranked as the No. 1 change they'd like to see in facilities' design, and a majority of respondents share an optimistic outlook about improved processes.
Interest in IPD is growing in medical institutions. "We're looking at IPD to get more stakeholders involved earlier," said one respondent, while another noted, "IPD offers better collaboration, budget and schedule efficiencies." We believe IPD offers the best option for achieving integrated project goals.
Maja Rosenquist is vice president and general manager of the Denver Operating Group at Mortenson Construction.
Post a comment to this article
Report Abusive Comment